In this article
When Two Experts are Better Than One
Close collaboration delivers customer success
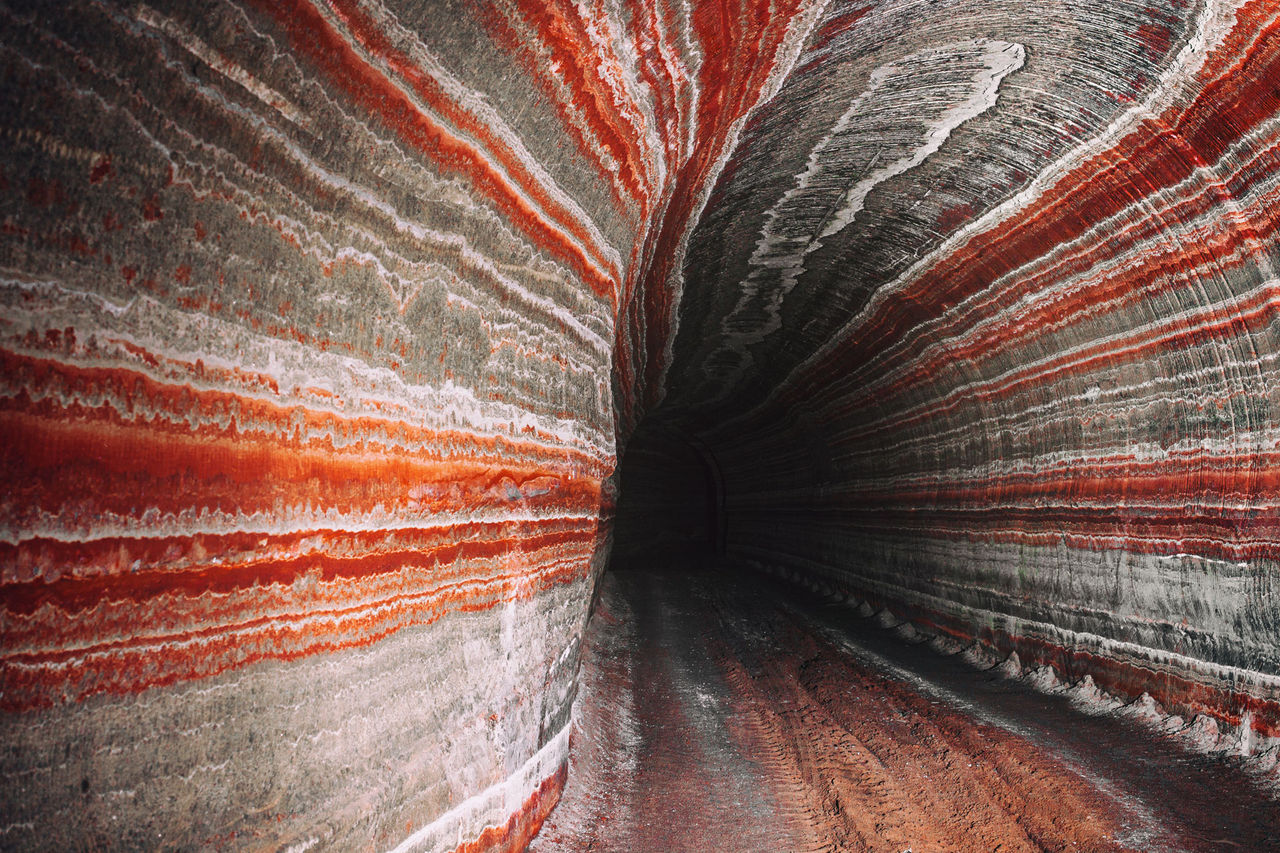
Industry Sector:
Building, Mining & Quarrying
Application:
Compacting Machines
Actual Saving:
£30,000
Payback period:
3 months
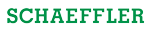
Product/Service:
- Bearing replacement
- On-site exoert installation
- Bearing reconditioning
Customer Benefits:
- Bearing failure averted
- Expert professional mounting of new bearings
- Maximised product lifestyle
- Reduced Total Cost of Ownership
There’s only one thing which serves customers better than ERIKS’ know-how. That’s ERIKS’ know-how plus additional highly specialist expertise, working seamlessly together to get results.
The operator of the UK’s deepest mine benefited from this kind of collaboration to optimise the life of their critical bearings, and save money and production downtime.
Challenge
The customer operates two compacting machines, from different manufacturers. The machines crush mined ore as one stage in a mining and refining process producing fertiliser and road de-icing salt. The machines’ compactor rolls have two rotor shafts, which rotate against each other to crush the mineral ore.
The compactors operate 24/7 under extremely high loads and with very slow rotation. Each machine has two extremely large bearings per rotor, with an exterior diameter of 830m and weighing 700kg each.
As part of a regular planned maintenance schedule, the bearings are changed every 2-3 years during the site’s annual two-week shutdown.
The mounting of such large bearings demands specialist expertise and equipment. There is also the risk of significant costs if they are incorrectly mounted – resulting from additional component damage and production downtime.
The lead time on the bearing manufacture, and the limited availability of specialist fitters required to work with such large bearings, means planning for the bearing change has to begin at least 6 months before the shutdown.
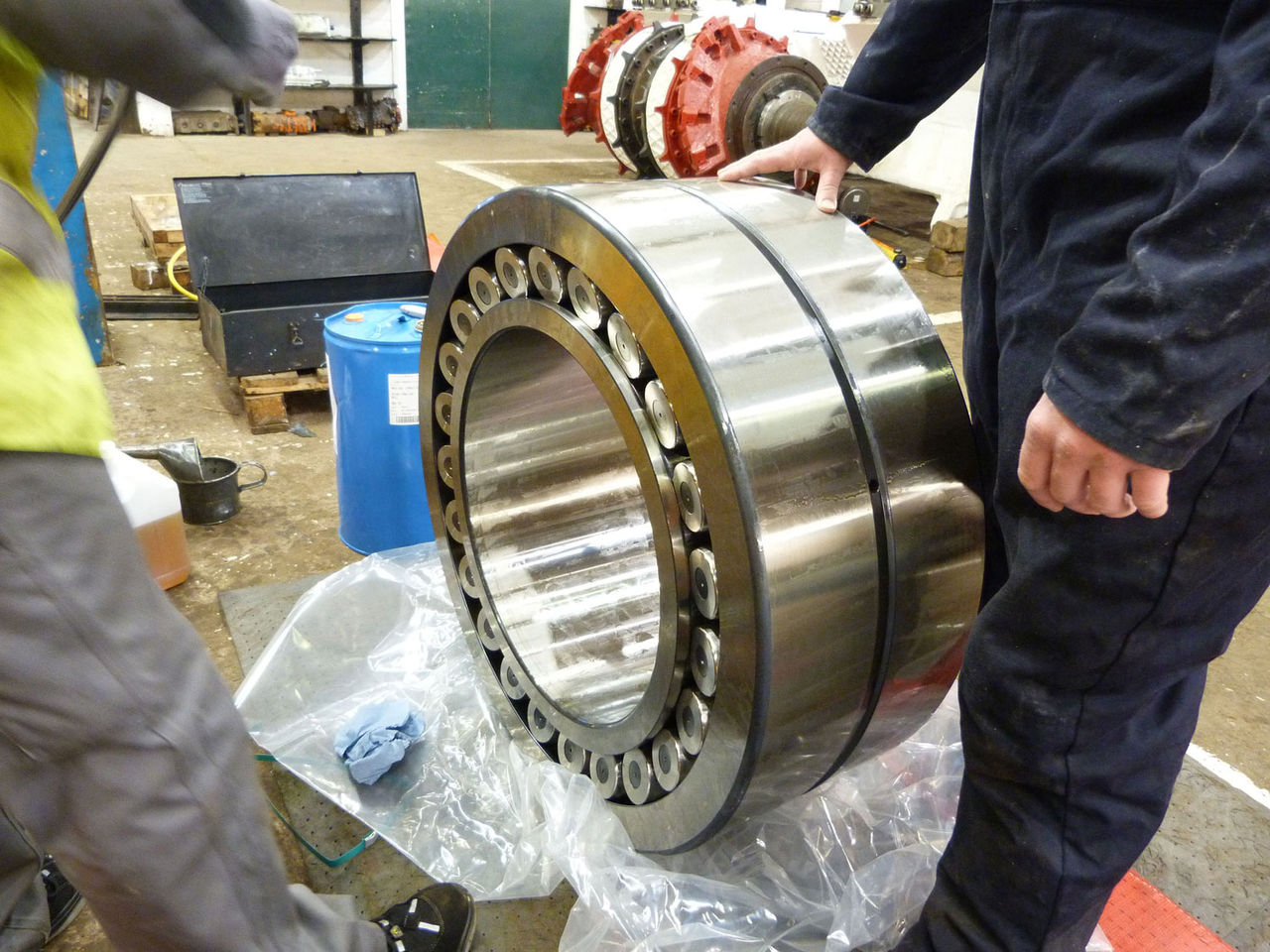
Inspecting the bearing for damage
Solution
ERIKS’ Teesside Service Centre in Stockton-on-Tees has a long-standing relationship with the mining company, and both ERIKS and the customer have experience of Schaeffler’s expertise in large and heavy bearings.
As soon as ERIKS were contacted by the customer, they began working together with Schaeffler to plan ahead for replacement of the bearings at the next annual shutdown.
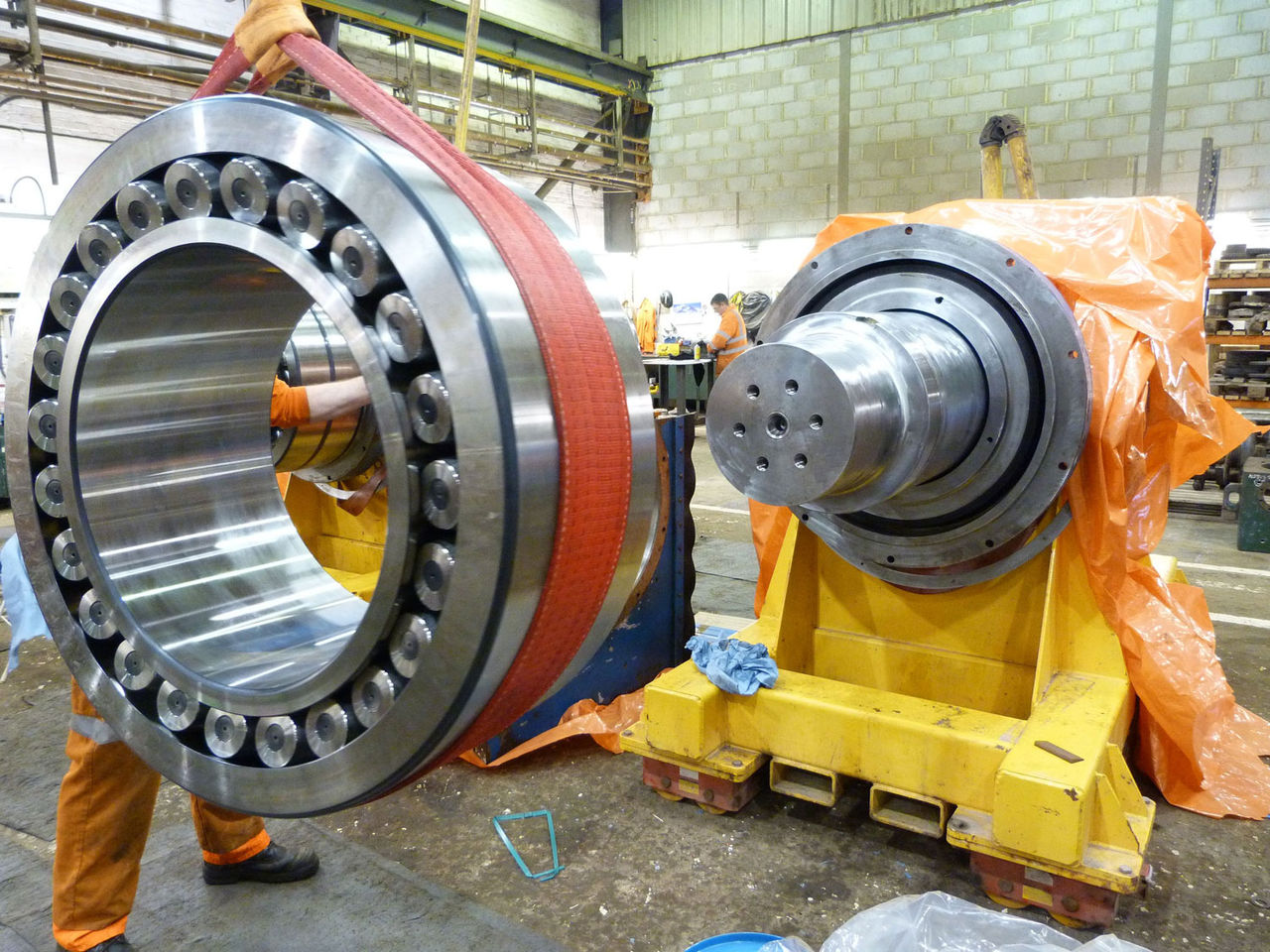
Mounting the bearing onto the shaft
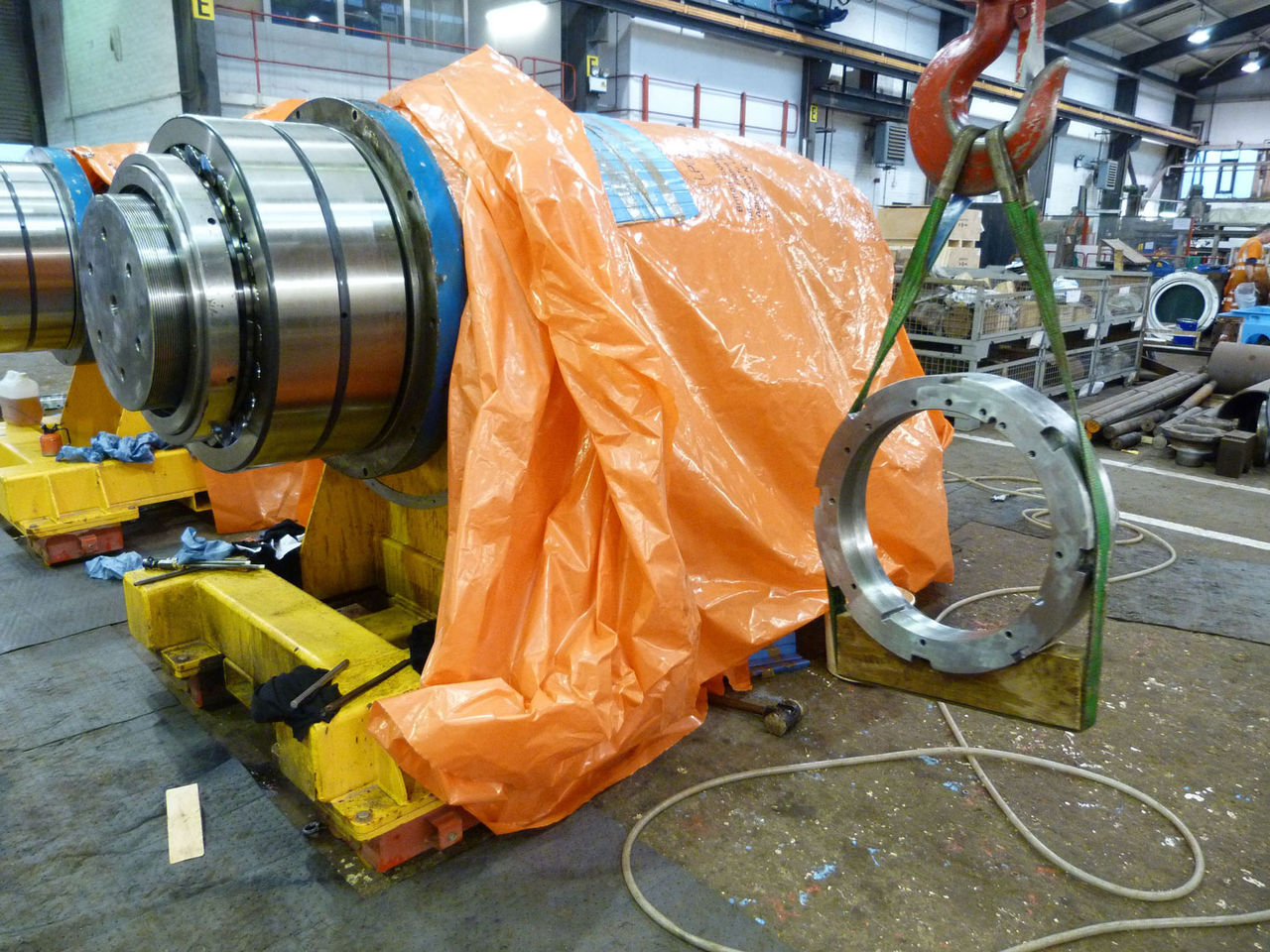
Mounting the hydraulic nut onto the shaft
The long manufacturing lead time for such large bearings is not the only reason for making plans so far ahead. The highly specialist engineers required to ensure the bearings are correctly fitted are in short supply and very busy. ERIKS and Schaeffler liaised closely to make sure the expertise would be available when required, including co-ordinating flying-in a fitter from Germany, and bringing-in an additional engineer from Birmingham, to work together on-site in the UK for 3 days.
Schaeffler also prepared a detailed method statement, specifying the tools, lifting and other equipment which would need to be ready and waiting at the customer’s location.
With the bearings weighing 700kg each, manoeuvring them into position and mounting them correctly is not a standard procedure.
It requires not only a specially-built rig to be made for the bearing shaft to sit in, but also the use of a high-powered hydraulic annular piston press, to push the adaptor sleeves into each bearing during the mounting process.
This remounting of the bearing was carried out under the supervision of the specialist engineers, who then measured and checked the critical radial clearances, and ensured the locking nuts were tightened to the correct torque.
Result
As part of the service to the customer, the replaced bearings were examined on-site, to provide an initial assessment of their suitability for reconditioning. Suitable bearings are then shipped back to Schaeffler for a full inspection, report and refurbishment.
With up to 12 months’ lead-time on new bearings, having a refurbished bearing back in stock within 3 months, not only improves availability but also reduces the total cost of ownership and improves sustainability.