In this article
Scaleable "Plug and play" clarifier upgrade for the water industry
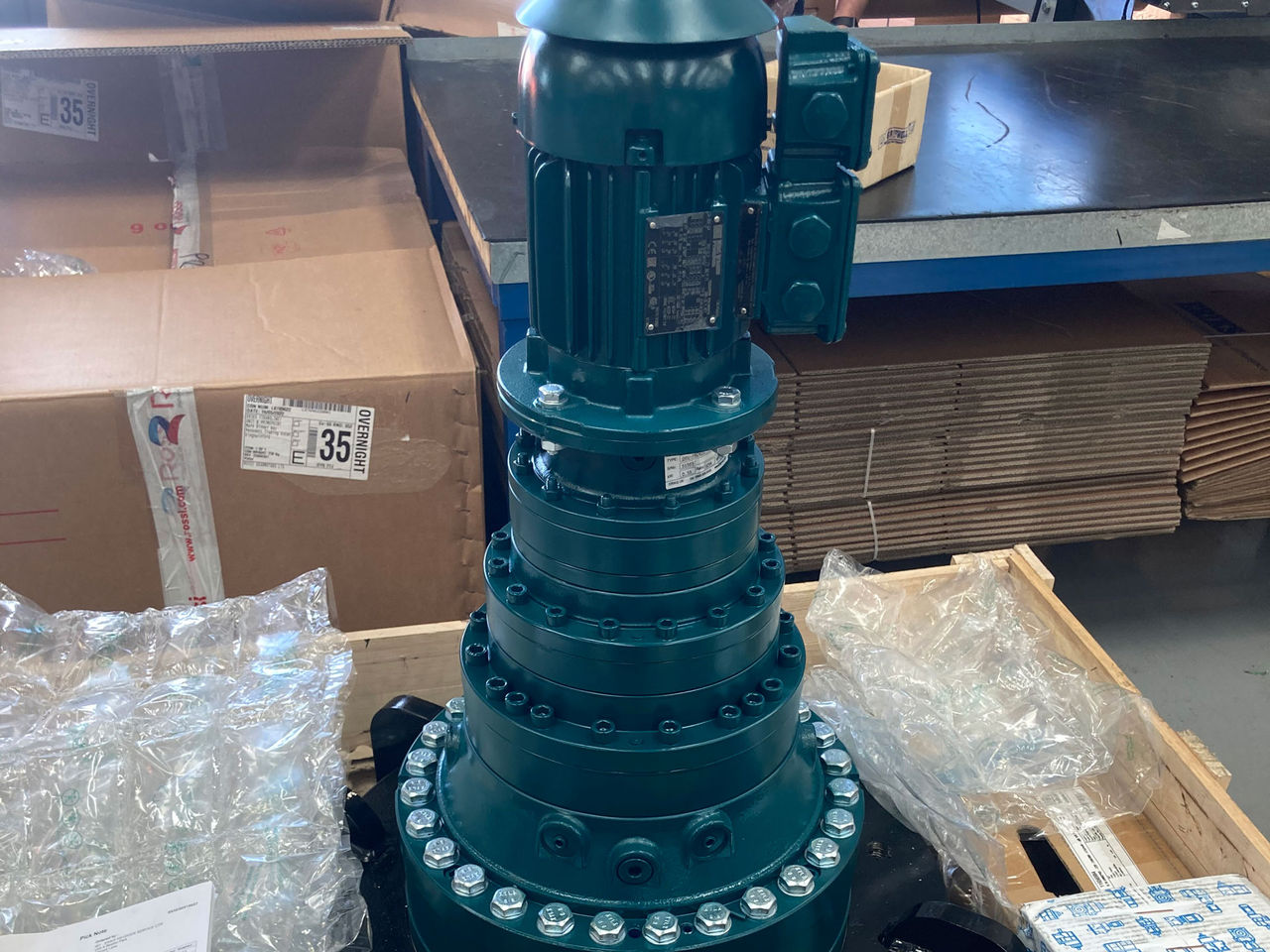
Industry Sector:
Water and Wastewater
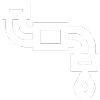
Application:
Clarifier drive systems
Problem
Ageing clarifier drive systems were putting process performance and reliability at serious risk for one northern wastewater company. Each clarifier tank relied on ultra-slow rotation - around one revolution every 90 minutes - to maintain flow consistency while settling out grit and heavier particles.
However, existing drives were made up of multiple ageing components: electric motors, torque limiters, belt or chain drives, and multi-stage gearboxes. With many systems over 30 years old, failures were becoming increasingly common. Water ingress, bearing collapse, worn belts, and poorly adjusted couplings led to frequent stoppages, excessive maintenance, and costly downtime.
Lack of standardisation across assets made it even harder to respond quickly - each tank often had bespoke parts and mounting arrangements, with no shared spares across sites.
Solution
ERIKS delivered a fully integrated planetary gearmotor system - designed to simplify the drivetrain, cut maintenance, and improve energy efficiency. The planetary unit, compact and highly efficient, combined high torque with smooth, ultra-low-speed output. The gearbox and motor were directly coupled, removing the need for belts, couplings, or secondary gearboxes.
A Variable Speed Drive (VSD) was also included to offer controlled acceleration, torque protection, and the flexibility to adjust tank rotation speed as required - ideal for coping with changing process loads. To ensure adaptability across multiple tank sizes, ERIKS developed a universal mounting and adaptor plate, allowing this standardised solution to be deployed across different clarifier designs.
The result? A scaleable ‘plug-and-play’ off-the-shelf drive system from ERIKS that can be installed in a day, serviced quickly - with minimal disruption.