In this article
Profiting from spending controls
Accuracy and performance in inventory management
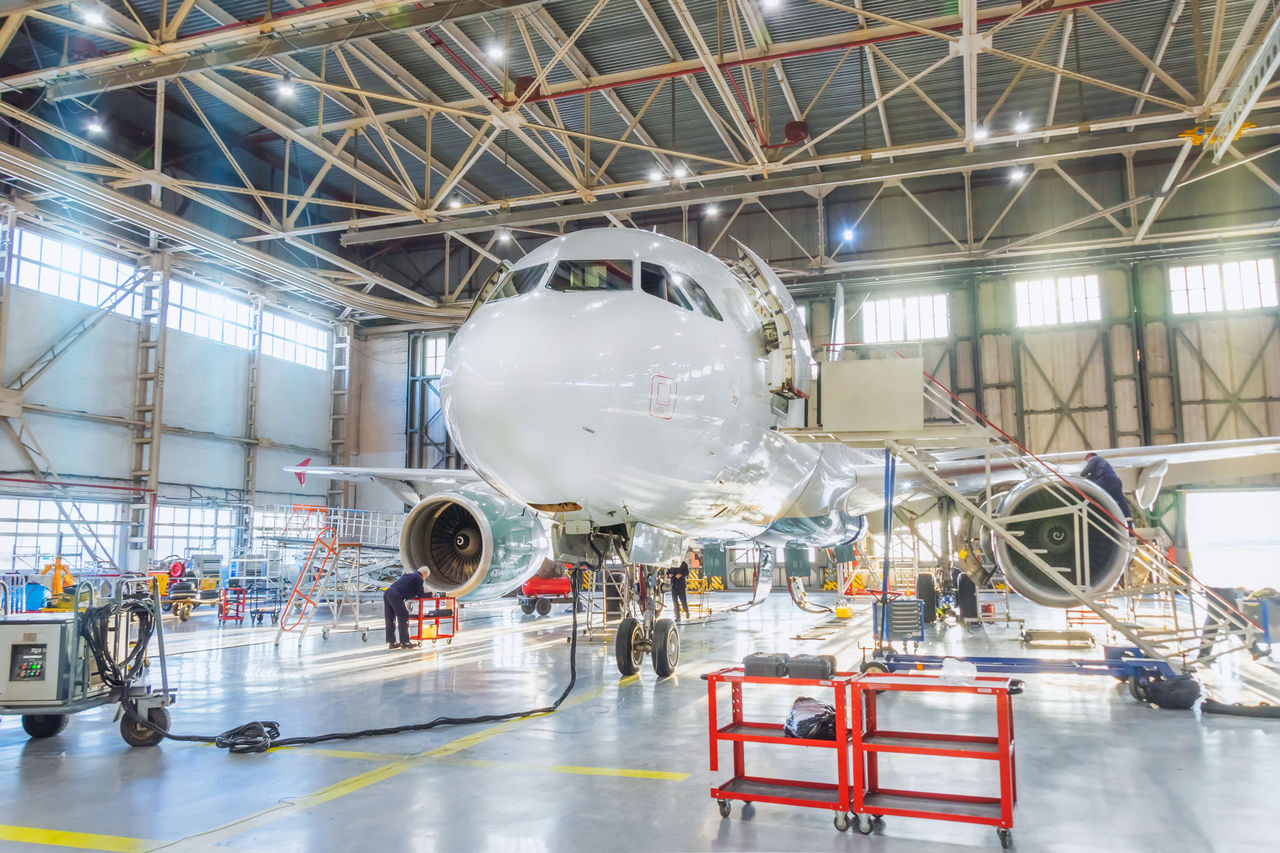
Industry Sector:
Aviation
Application:
Fully outsourced, stores and inventory management
Actual Saving:
£1,000,000 over 5 years
Payback period:
n/a
Product/Service:
- Stores & inventory management
- Fully-trained, dedicated staff
- In-house technical expertise
Customer Benefits:
- Experienced MRO resource
- Procurement expertise
- Efficient and accurate inventory management
- Technical support for engineers
We all understand the importance of budgeting and controlling your spending, and if not managed correctly, it quickly becomes like a leaky tap, steadily dripping money away. At first, it may seem inconsequential, but over time, those small drops accumulate into a steady stream, draining away your profitability as one customer began to realise.
Challenge
The customer was suffering from uncontrolled spending due to unorganised, multi-located stores across a vast site, and understanding they needed help, they approached a logistics contracting partner who took ownership of procurement and stores management.
This relationship quickly deteriorated due to a lack of expertise across international and local supply routes, technical knowledge and expertise in key product areas. In addition, stock inaccuracies, poor communication channels, unclear communication from site management, and no obvious working escalation pathway compounded the problems. Often resulting in production downtime and productivity losses.
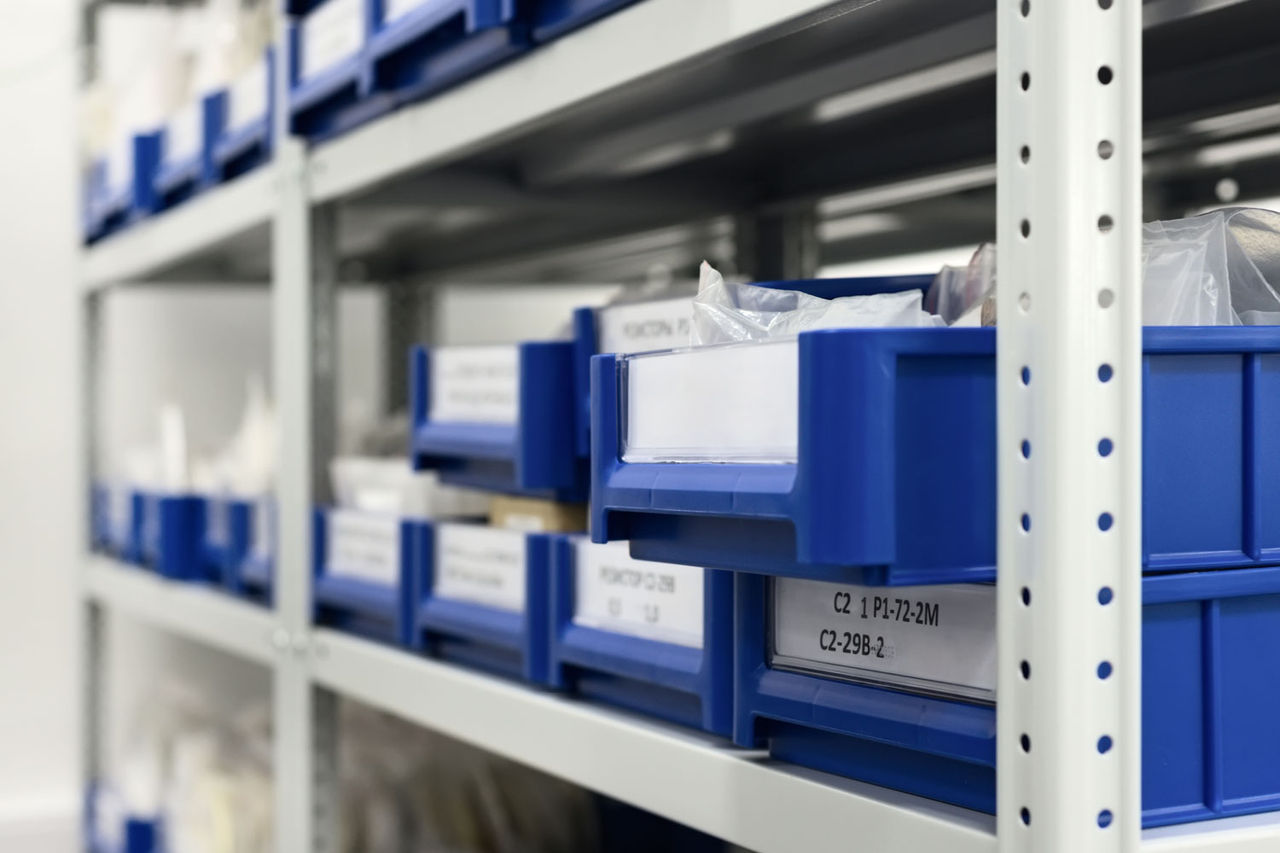
Storeroom performance improvements
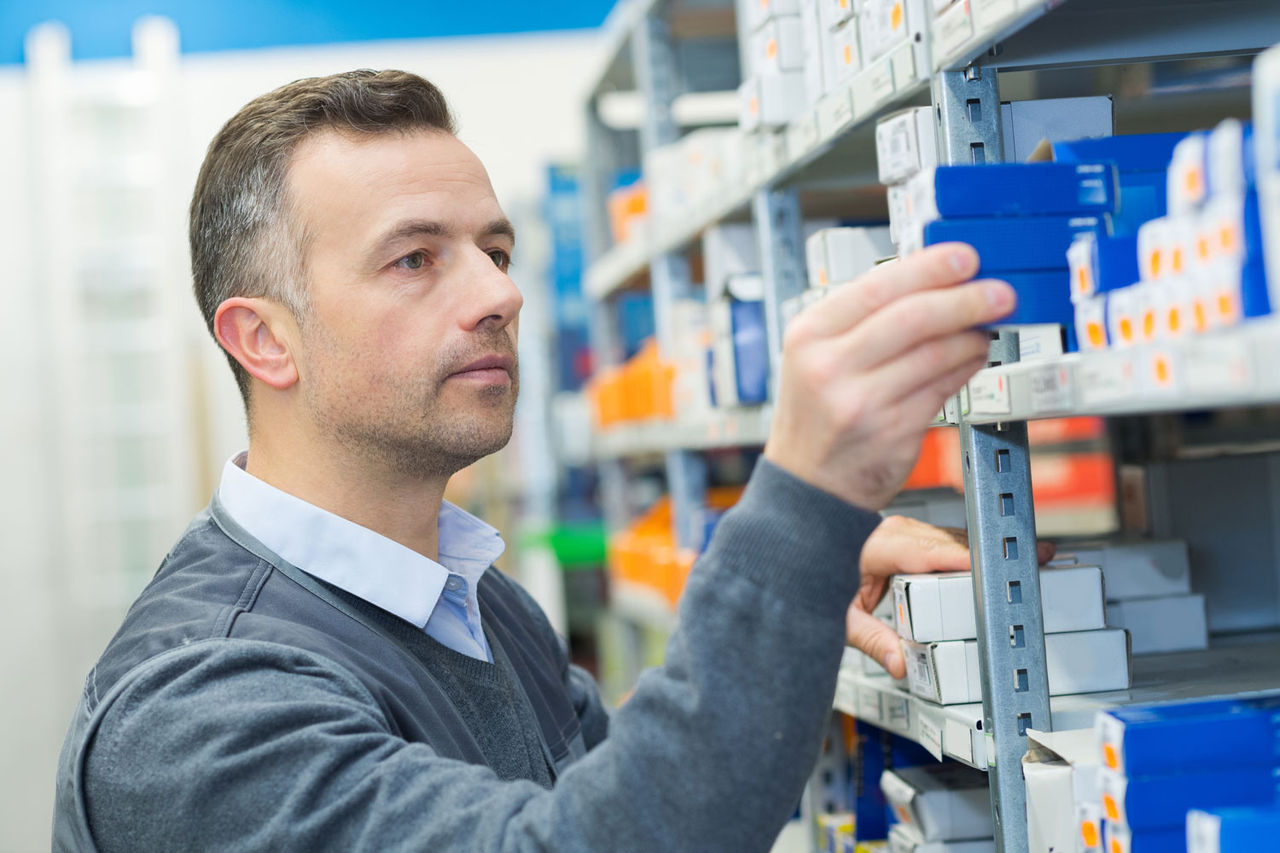
Parts stores build for increased accuracy
Solution
A competitive tender process ensued, with ERIKS chosen due to our proven and unrivalled track record of over 25+ years of experience in inventory management
Following a successful go-live, we began a 12-month storeroom review to improve accuracy and performance and introduce new technologies to help achieve these goals. This included logging, verifying, barcoding and organisation of over 20,000 SKUs, along with a parts stores build within the main stores.
The ERIKS OnSite teams now attend all crucial production and procurement meetings so that our highly trained and skilled team responds to the pulse of change immediately, communicating effectively, allowing a smooth flow of information to the right people at the right time.
Along with focused technical support and procurement specialism, ERIKS has successfully met and exceeded contractual savings obligations by working in collaboration with key customer Engineering and Procurement stakeholders to deliver results.
In the past five years, ERIKS has saved the customer over £1 million on agreed KPIs. Thanks to ERIKS stores management expertise, that leaky tap was maintained, fixed and is no longer a financial drain to the customer.