In this article
Saving energy, cutting costs, avoiding disruption
Planning for the future delivers benefits today
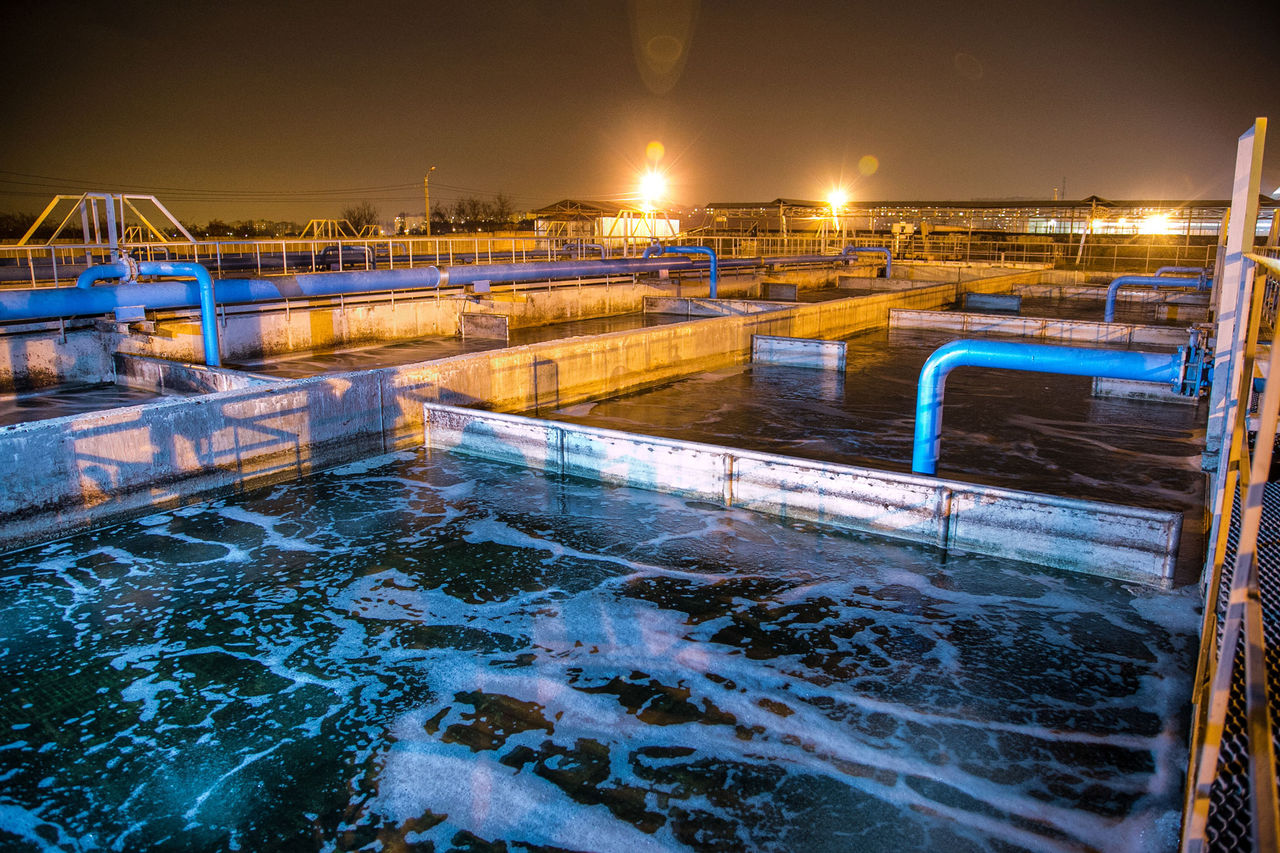
Industry Sector:
Water and Wastewater
Application:
Aerator paddle motor
Actual Saving:
£247,597.20 (lifetime energy savings)
790.35 tonnes CO² (ifetime reduction)
Payback period:
1 year 11 months
Product/Service:
- Energy Management
- Total Cost of Ownership
- Re-Engineering and Problem Solving
Customer Benefits:
- Lower TCO
- Increased energy efficency
- Reduced carbon footprint
- Increase Plant Reliability
- Meeting CSR KPI's
‘If it ain’t broke, don’t fix it’ is not a valid philosophy for any organisation concerned about its energy efficiency and carbon footprint. So even though a major utility had been running 11 electric motors for almost three decades with no significant downtime, they realised it was time to upgrade to more efficient assets.
Frequent rewinds had reduced efficiency, and developments in electric motor design had left the motors looking extremely costly to run and unsustainable from an environmental viewpoint.
Challenge
Each motor drives a single aerator, which operates in its own water treatment lane. The failure of even one motor would significantly disrupt water treatment operations and reduce capacity, by requiring the closure of an entire lane.
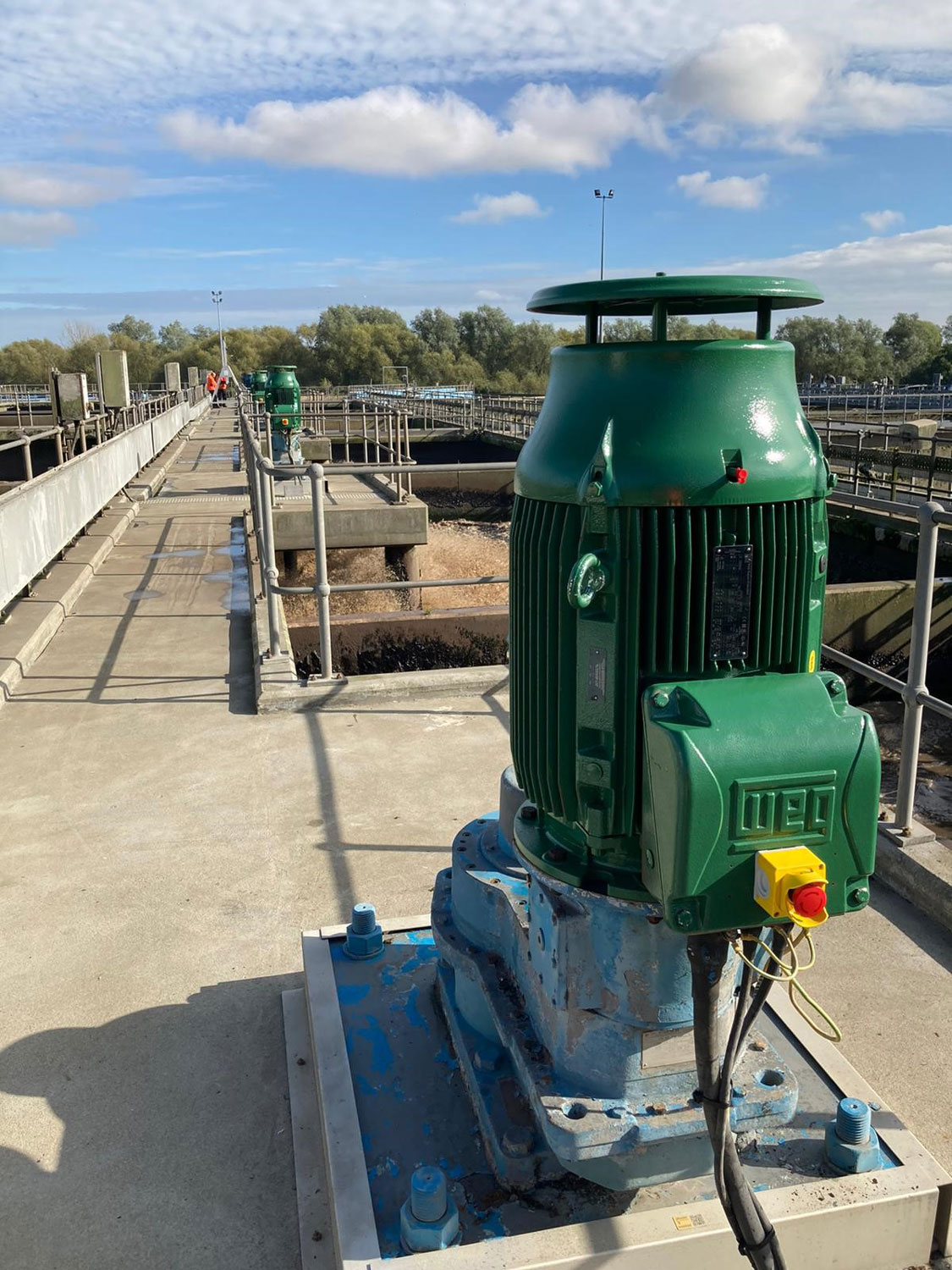
Newly installed IE4 aerator paddle motors
The age of the motors meant that there were no spares available, and no record of the number of rewinds they had undergone. Grease nipples were damaged beyond repair making lubrication difficult, and there was no lubrication service contract in place. Some motors were showing signs of potential imminent bearing failure.
At 28 years old, the motors were assumed to be equivalent to what is now EFF2 efficiency rating. This was resulting in high energy consumption and a large carbon footprint.
The customer was planning to run the motors to failure but their age meant that, in the meantime, running costs were unnecessarily high. Inevitable eventual catastrophic failure would result in significant disruption and further costs.
Solution
1% of the Total Cost of Ownership of an electric motor is acquisition. 2% is maintenance. The remaining 97% is the energy cost. So ERIKS proposed an upgrade to new energy efficient 45kW IE4 electric motors. This would benefit the customer not only in terms of reduced energy costs and consumption, but also with a smaller carbon footprint and a far smaller risk of breakdown, downtime and associated disruption.
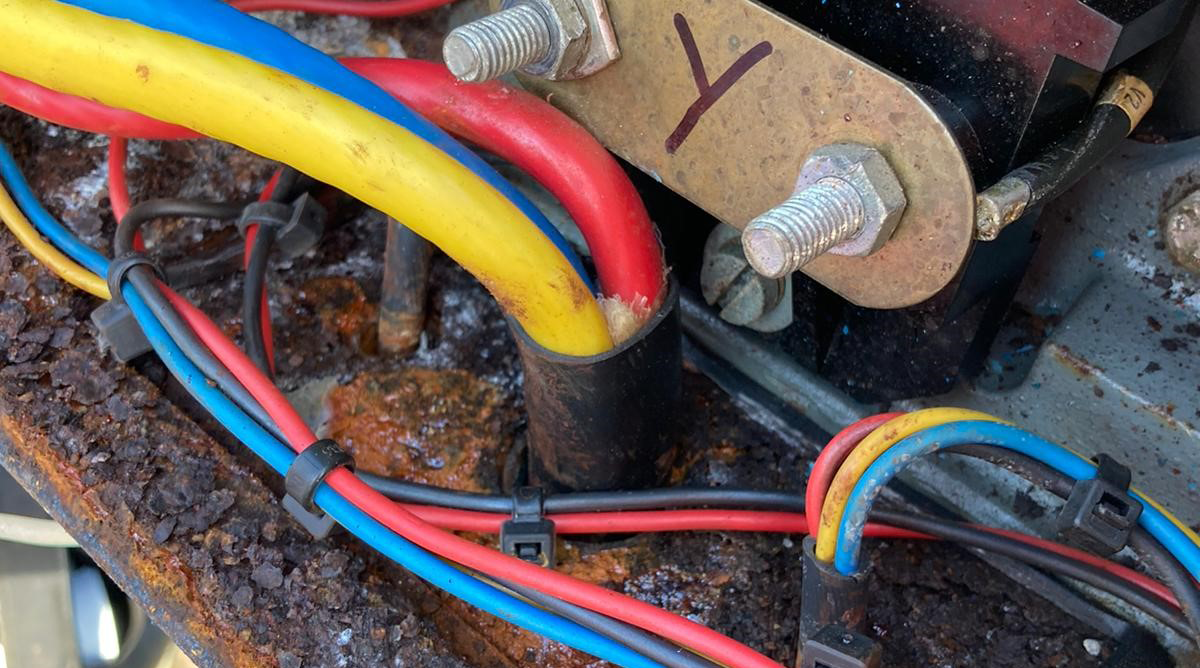
Corroded terminals boxes from water ingress
Because the motors could not be out of action for more than a day each, ERIKS undertook to replace all 11 individually, taking a maximum of one day each. This included removing the existing asset, installing, testing and commissioning the new motor, and cleaning down the site.
An additional problem arose when the terminal boxes were discovered to have suffered water ingress. Each box was full of water and the terminal glands had seized onto the boxes. ERIKS’ engineers not only devised a bespoke adaptation to the terminal boxes to fit the new motors, but also had each one engineered and fitted within the tight one-day timescale to avoid any production losses.