In this article
Parts Conversion Project Reaps Significant Benefits
Reduced inventory, improved supplier network
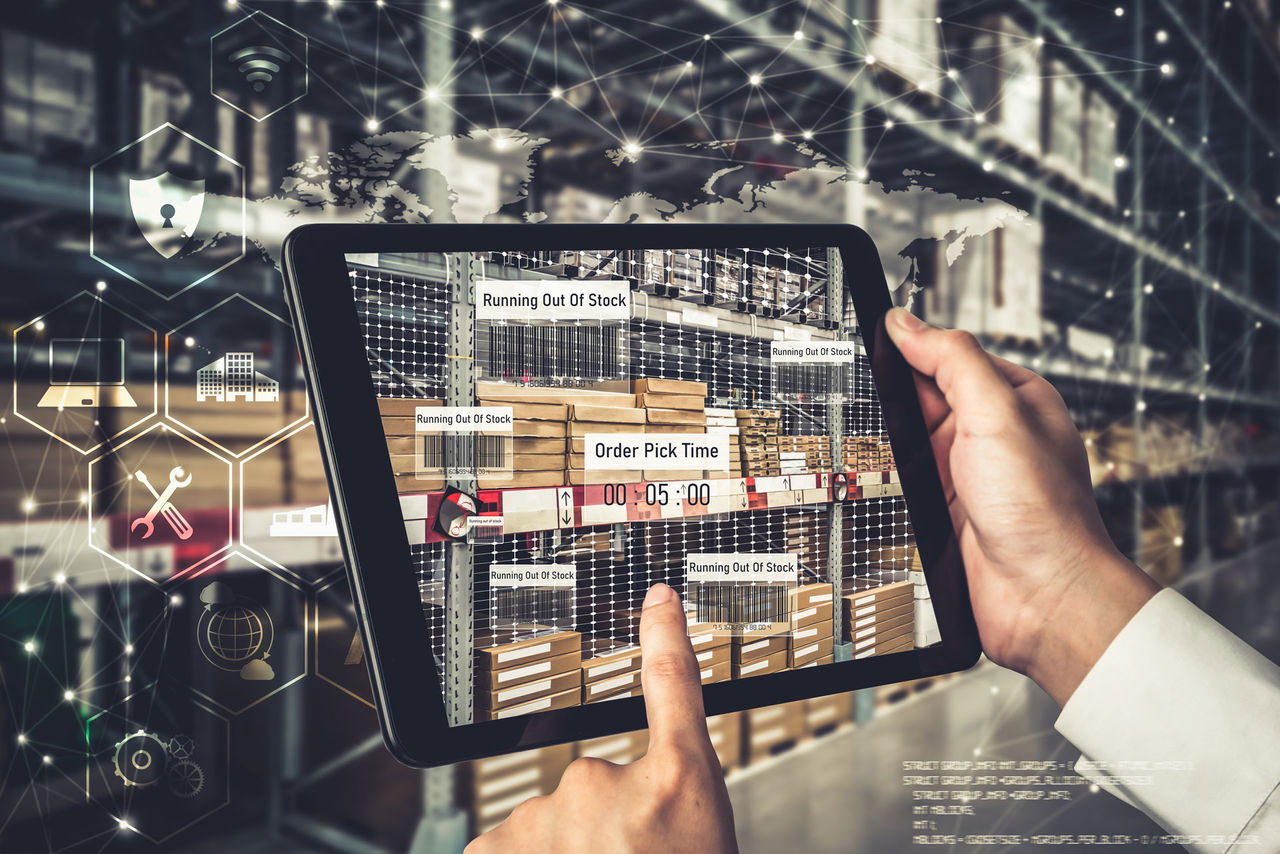
Industry Sector:
Pharmaceutical
Application:
OEM Parts Conversion & Spare Parts Management
Actual Saving:
€436,000
Payback period:
5 years (on going)
Product/Service:
- OEM Parts Conversion
- Spare Parts Management
- Stores Management
Customer Benefits:
- Increased cost savings
- Improved efficiency
- Reduced inventory
- Maintenance Reduction
- Lower Total Cost of Ownership
- Risk mitigaton
- Sustainability
With all industries focused on the bottom line, cost saving is a hot topic for most organisations. In the past five years, businesses have increasingly looked at their supply chain to see how they can reduce supply chain costs.
Challenge
It’s fairly common for a company to purchase 40-70% of spare or replacement machine parts directly from the OEM or a single supplier that is their only known source. A reliance on a proprietary source increases the risk of supply chain disruptions resulting from, for example, a worldwide pandemic or Brexit.
Spare parts management is about how spares handling must be systemised and structured to enable efficient inventory management that leads to improved availability and reduces the amount of capital expenditure.
Without spare parts, there is a risk of downtime, which may lower the quality of goods produced, cause environmentally hazardous emissions, and create a hazard for employees. This usually leads to the accumulation of an excessive number of spare parts, which will often result in large amounts of capital expenditure.
So, when one large Pharmaceutical company based in Dungarvan, Ireland, was looking to reduce their spares inventory, and ensure capital expenditure remained at a manageable level, they called upon ERIKS strong supply network to assist in an OEM parts conversion project with the aim of delivering significant, otherwise before unidentified, cost savings.
Solution
Due to the fantastic working relationship with the customer, our strong supply network, and the experience of the ERIKS Engineering team, we were able to work closely to identify the required spare parts and provide an alternative source, reduced prices and significant energy savings.
Initially, the ERIKS team had concerns regarding the basic nature of the current OEM part descriptions available and part number creation process, which saw the customer formulate their own part numbers, making it incredibly difficult to correctly identify the parts required.
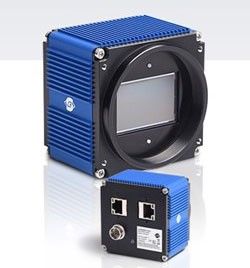
OEM camera system conversion totalling a saving of €70,226.50 saving (81%)
With this discovery, both teams worked together to create a uniformed description and part number creation process that would aid the effectiveness of sourcing the correct parts at the optimal price.
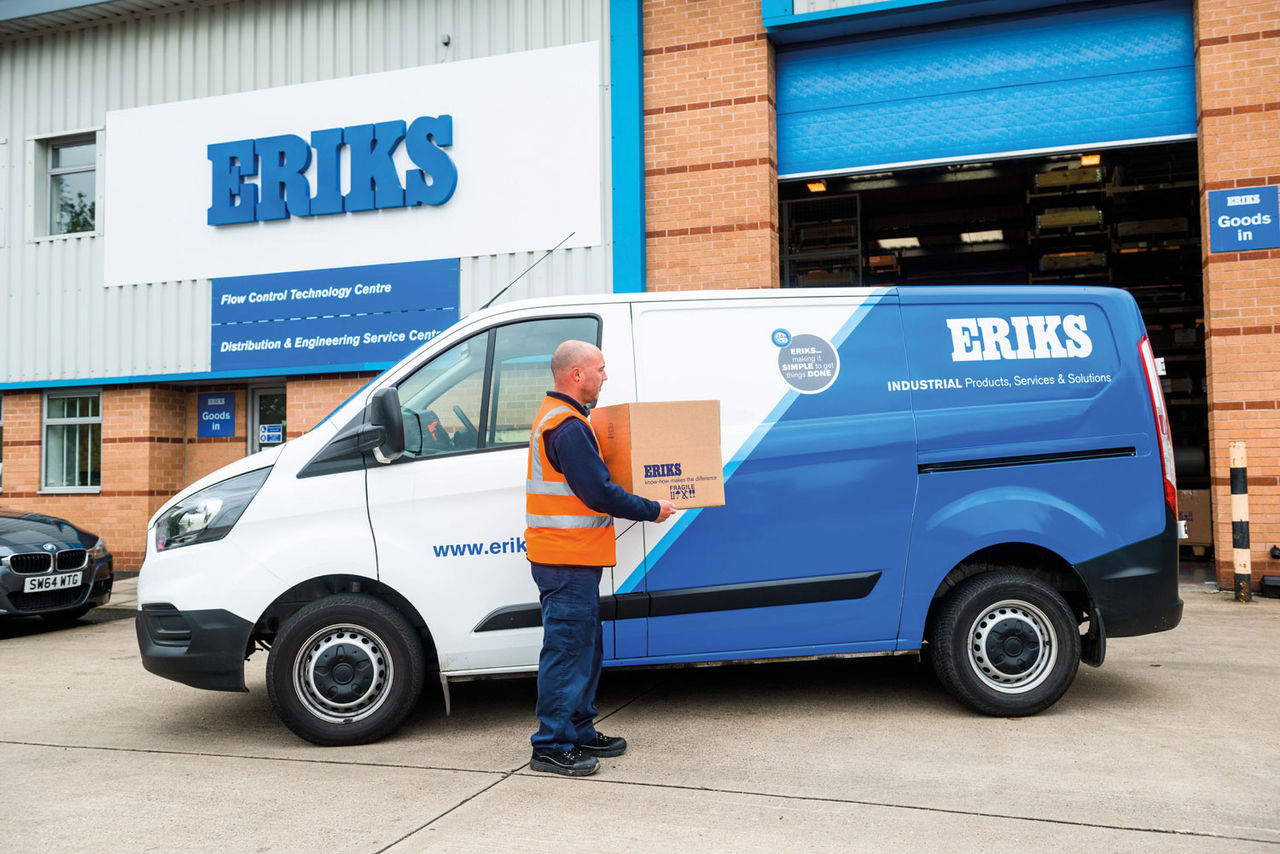
Switching from OEM supply alllows for parts to besupplied locally reducing lead times
Working in conjunction with the customer effortlessly facilitated the spare parts management process, whereby ERIKS has gone from supplying 17-line items as part of projects/new spares in 2016, to supplying 355-line items in 2020, and the trust continues to grow with ERIKS now receiving 1.5 million of orders which were previously being processed through the customers system.
Each of these has offered a significant saving to the customer and has assisted in keeping inventory value down and capital expenditure at the right level.
Result
Receiving the information at the earliest stage enabled us to identify the spares required and find an alternative source. Savings have been achieved through the accumulative work by the entire team, via the identification and conversion of OEM supplied items, both being sourced and delivered by ERIKS.
By working in tandem with the customer, the ERIKS team have been able to identify and provide savings totalling €436k to date, and the number of items continues to increase. This has extended to not only OEM conversions of existing lines, but also the inclusion of ERIKS teams on the onset of other major projects.
This improved management process has allowed for a more streamline supply chain, allowing the customer to oversee any challenges or areas that are resulting in profit loss – putting the power back in their hands.
It’s important to note that reducing costs is a huge operation and calls for focused and knowledgeable leadership that understands the end goal when considering supply chain management – an area that the ERIKS team has excelled in.
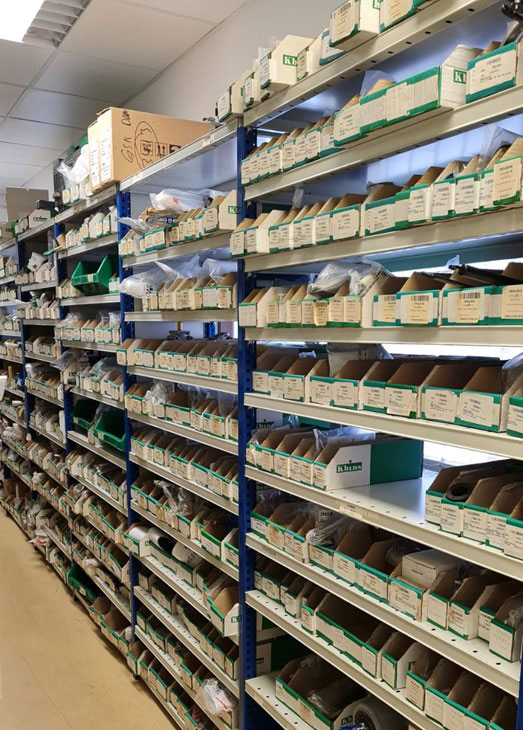