In this article
When 'out of the tank' thinking solved the problem
Safe access to sensors saves money too
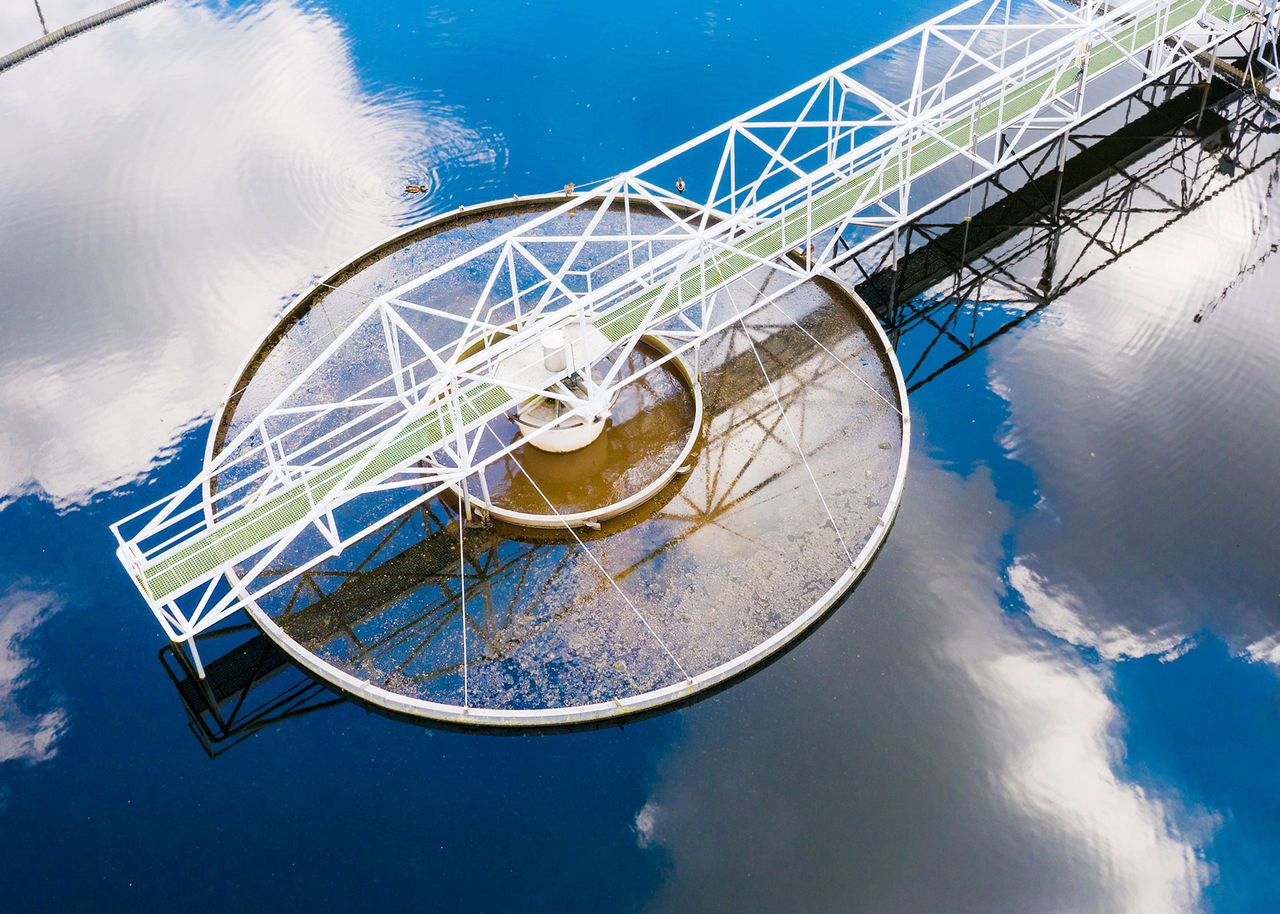
Industry Sector:
Food & Beverage
Application:
Wate water plant
Actual Saving:
£53,128
Payback period:
N/A
Product/Service:
- Volume Analyser Sensor
Customer Benefits:
- Reduced labour costs
- Enhanced employee safety
- Elimination of unpredicted failures
- Avoidance of shutdowns and lost production
The more you monitor, the more you know. Which gives you more chance of avoiding unexpected breakdowns and unplanned downtime. But more monitoring requires more sensors – which can mean more problems.
For a major dairy products manufacturer, gathering more data from more sensors meant not only more time and effort but also more potential Health and Safety risks. With motors and blowers located around circular waste water tanks at the 12 o’clock, 3 o’clock, 6 o’clock and 9 o’clock positions, the customer was finding that monitoring their performance could be risky, time-consuming and costly.
Asking ERIKS for a solution proved safe, quick and money-saving.
Challenge
Each of the customer’s five waste water tanks has four sets of motors and blowers positioned around the tank. Each of the motors – mounted at 45° – has a long shaft and impeller fitted, which agitates the tank’s contents. A hose attached to the blower extends to the bottom of the tank to aerate the solution.
Monitoring these assets means attaching fixed sensors at the drive and non-drive ends of the motors; attaching fixed sensors to the blowers; to enable taking regular manual readings; This task was very hazardous as not only the original task of fitting these to in-situ assets, but for the continued monitoring,
The customer wanted to regularly visit these sensors with a handheld monitor to take readings, at all sensor locations. So with four sensors for each motor/blower set, four sets per tank and five tanks across the site, that means repeating the operation 80 times. And this is would be highly risky and time consuming, also there was no guarantee that a good connection could be made each time and gain an accurate reading.
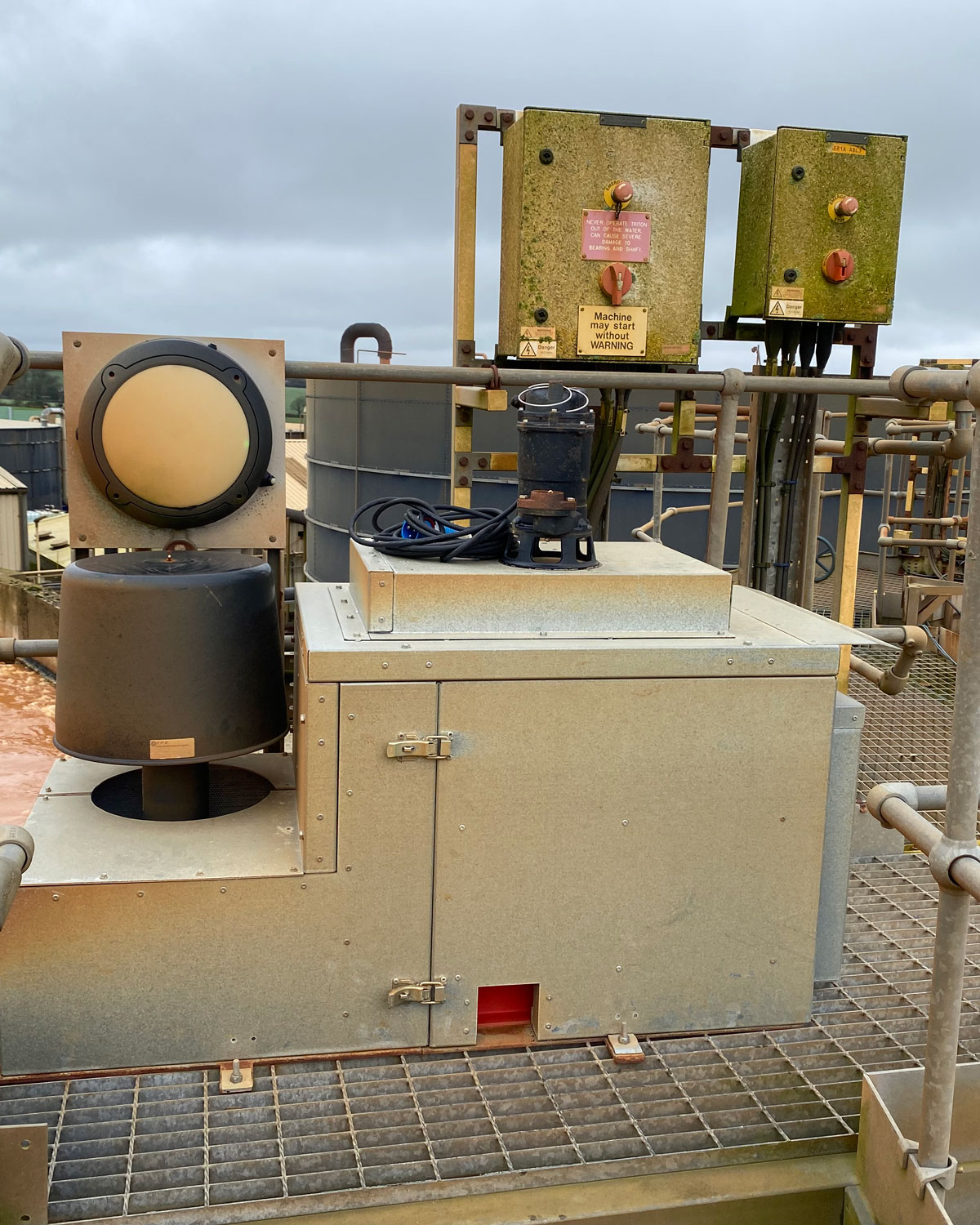
Blower unit on cat walkway
This would involve:
- Climbing a Cat (roof access) ladder to reach the platform
- Climbing onto the motor, or leaning out above the motor, and attaching a meter/monitoring device test leads to sensor to the top
- Taking the reading whilst still leaning out
- Moving to next sensor on asset
- Walking out on the gantry (not designed for access) above the solution-filled tank, to attach the test leads to a sensor to the bottom of the motor
- Taking the reading while still positioned on a potentially unsafe gantry above the tank
- Walking back to the platform
- Descending the ladder to the ground
Clearly the whole process would potentially breach several Health and Safety regulations, as well as putting the engineer at risk of a slip, a fall or – worse still – a fall into the solution-filled tank. In that instance, even wearing a safety harness, the engineer would sink because the solution is aerated. Throwing in a life ring would be the obvious emergency action to take, but the aerated solution would cause that to sink too.
And having someone on hand to throw in the ring means having two engineers carrying out the job together: slightly reducing the risk but doubling the labour cost.
But the Health and Safety implications – enormous as they are – are not the only risks. There’s also the danger that after all that, the readings will be worthless. Because if the test leads don’t make a clean connection then the readings would be inaccurate possibly (perhaps a different engineer is doing the job), then continuity levels could be disrupted and therefore the readings will be invalidated.
So rather than train their engineers in acrobatics, the customer contacted ERIKS.
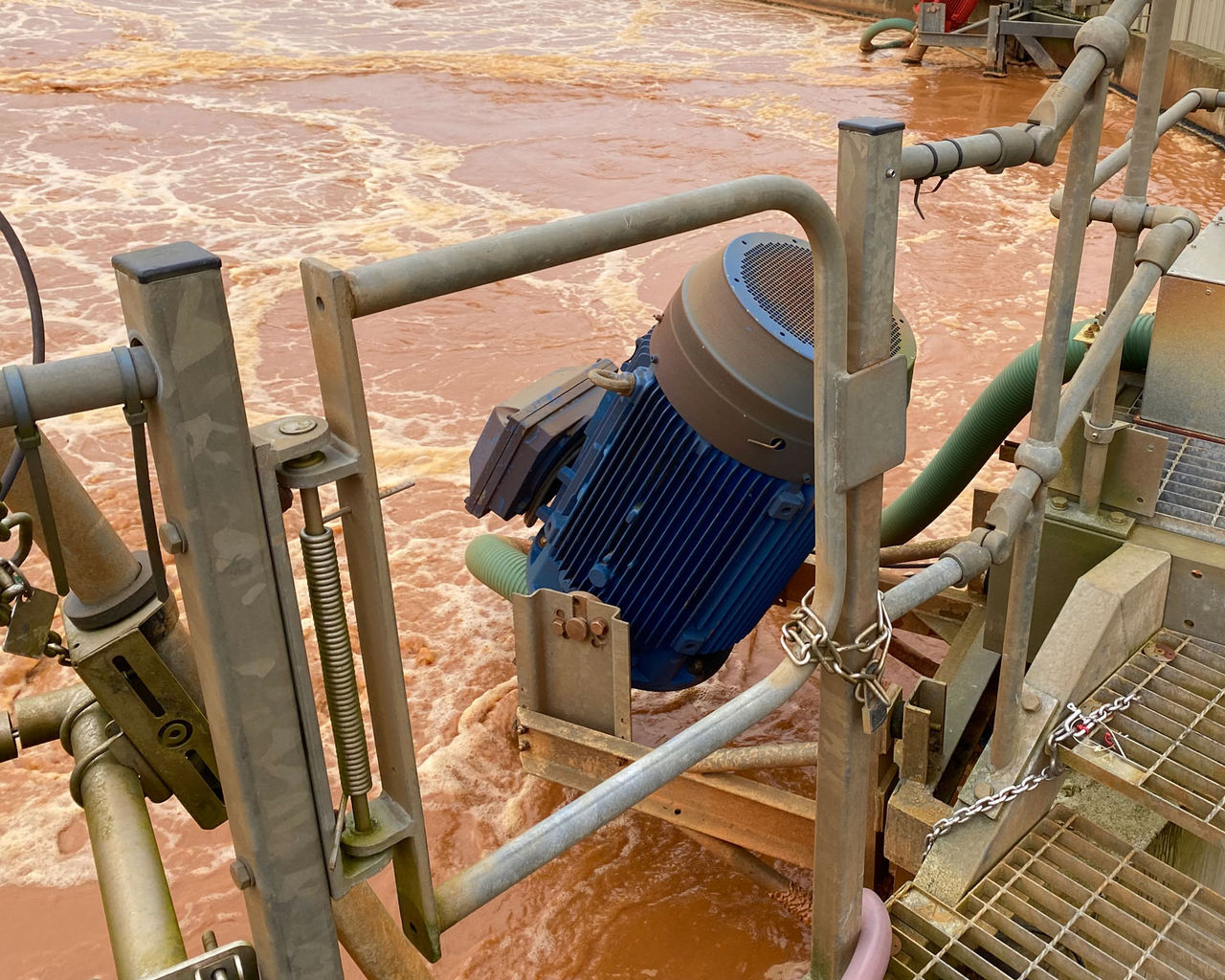
Large motor mounted at 45° fitted with a long shaft and impeller to agitate the contents of the tank
Solution
Clearly the challenge was to eliminate the Health and Safety risks, while maintaining the capability for repeated and accurate monitoring. If at the same time the number of engineers required and labour hours needed to carry out the task could be reduced, that would be a bonus.
ERIKS’ solution was simple – if you know how.
Rather than relying on manually using test leads to get good readings from 80 sensors, ERIKS’ engineers recommended the installation of fixed, hard-wired sensors in all the necessary monitoring positions: two on the agitator motor and two on the blower unit. This meant a once-only requirement to access the positions via the ladders and gantires, to attach to assets.
When an asset needed to be removed for maintenance the cable to sensor could be disconnected at a close by terminal box and the asset could be safely removed, once in the workshop the asset could be repaired and a new sensor and cable could be fitted and once the asset was reinstalled the cable could be reconnected to the junction box to provide permanent monitoring.
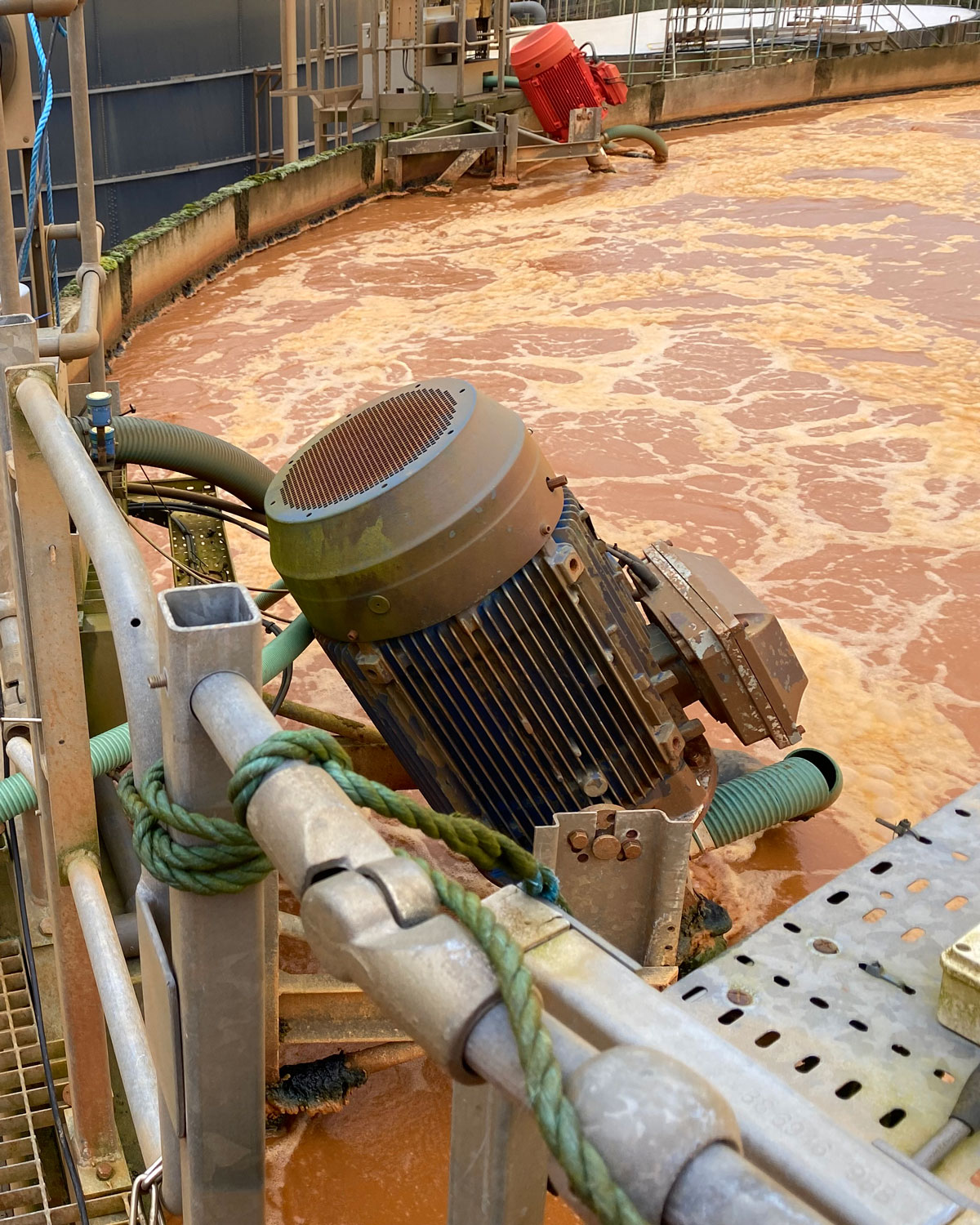
Another angle of two large motors mounted at 45° fitted with a long shaft and impeller to agitate the contents of the tank
The sensors have cables attached which are long enough to reach down to the ground from the motors and blowers above the tanks. At ground level, each cable is terminated in a switch box. With two switch boxes per tank, one box accommodates the cables from the motors and blowers at the 12 o’clock and 3 o’clock positions, and the other the cables from the assets at the 6 o’clock and 9 o’clock positions.
Taking the sensor readings is then a simple matter of opening the switch boxes on the ground. No ladder climbing. No gantry negotiating. No Health and Safety risk. And no need for two people to do the job.
Monthly readings can be taken in a matter of minutes, and the fixed sensors help to ensure that the reading is more accurate. If a result suggests closer monitoring is required, a daily reading is just as easy to take.
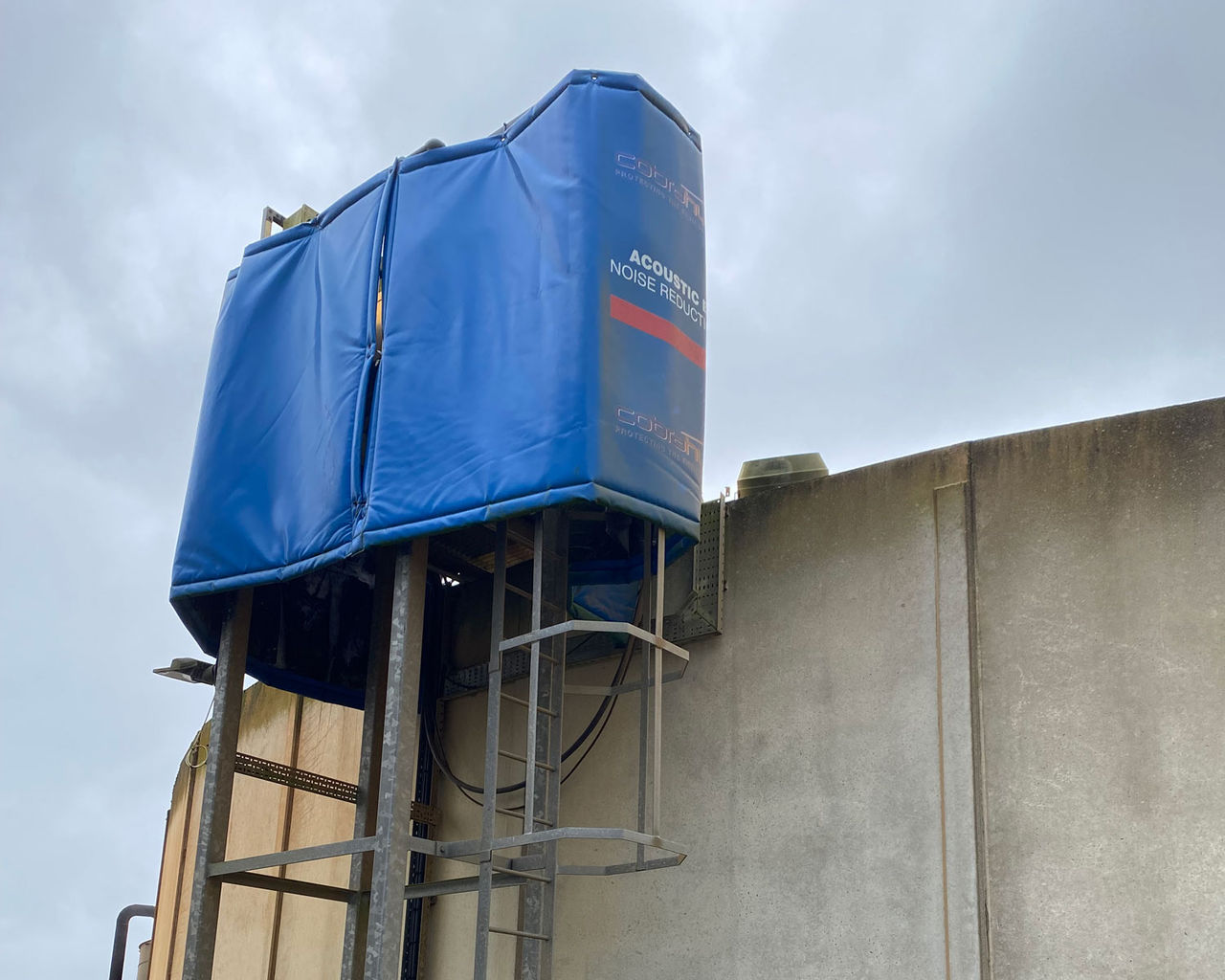
Access platform located at the side of each tank
Result
For Health and Safety reasons, the previous method of fixing and removing sensors for each reading could not be carried out by a lone engineer. So even a conservative estimate of 20 minutes for the entire operation at each motor position has to be doubled to 40 labour minutes.
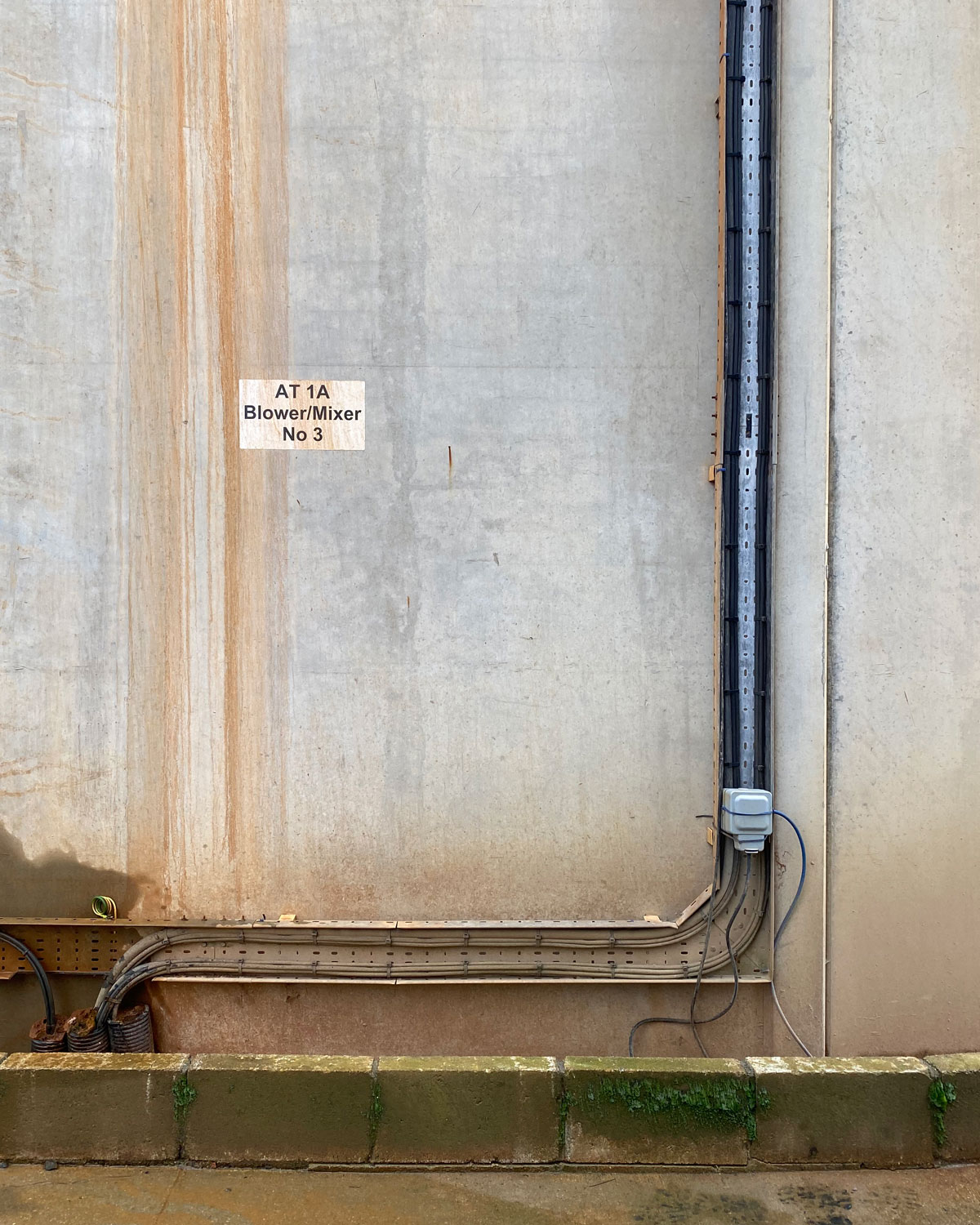
Electrical shut-off switch located at ground level
With 4 positions per tank, and 5 tanks to be checked, that equates to:
- 20 operations per month
- 800 minutes of engineers time
- 12 monthly checks @ 800 minutes p.m. = 9,600 minutes per annum
- 9,600 minutes = 160 hours
- 160 hours at £30/hr for Condition Monitoring engineer
- Annual labour costs of one engineer = £4,800
Developing robust reporting and improvement initiatives across equality, diversity and inclusion TOTAL: £9,600 p.a.
However, eliminating those labour costs is not the only saving. There are also savings of:
- £5,180 from reduced data acquisition time
- £7,200 from early diagnosis of potential blower faults
- £18,000 from early detection of potential motor faults
- £1,650 from reduction in crane use for alignment of planned jobs
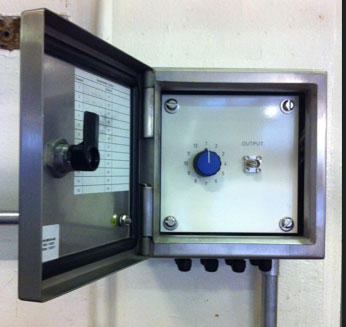
Switch Box controlling each motor at 12, 3, 6 and 9 o'clock
So, taking cost avoidance savings and parts and labour savings into account, the customer will save £53,128 with ERIKS condition monitoring solution. And if there’s a move to round the clock 24/7 monitoring, the solution is future-proofed to enable the change with no further installation costs.