In this article
Online monitoring service warns on imminent failure
Reduced downtime through increased insight
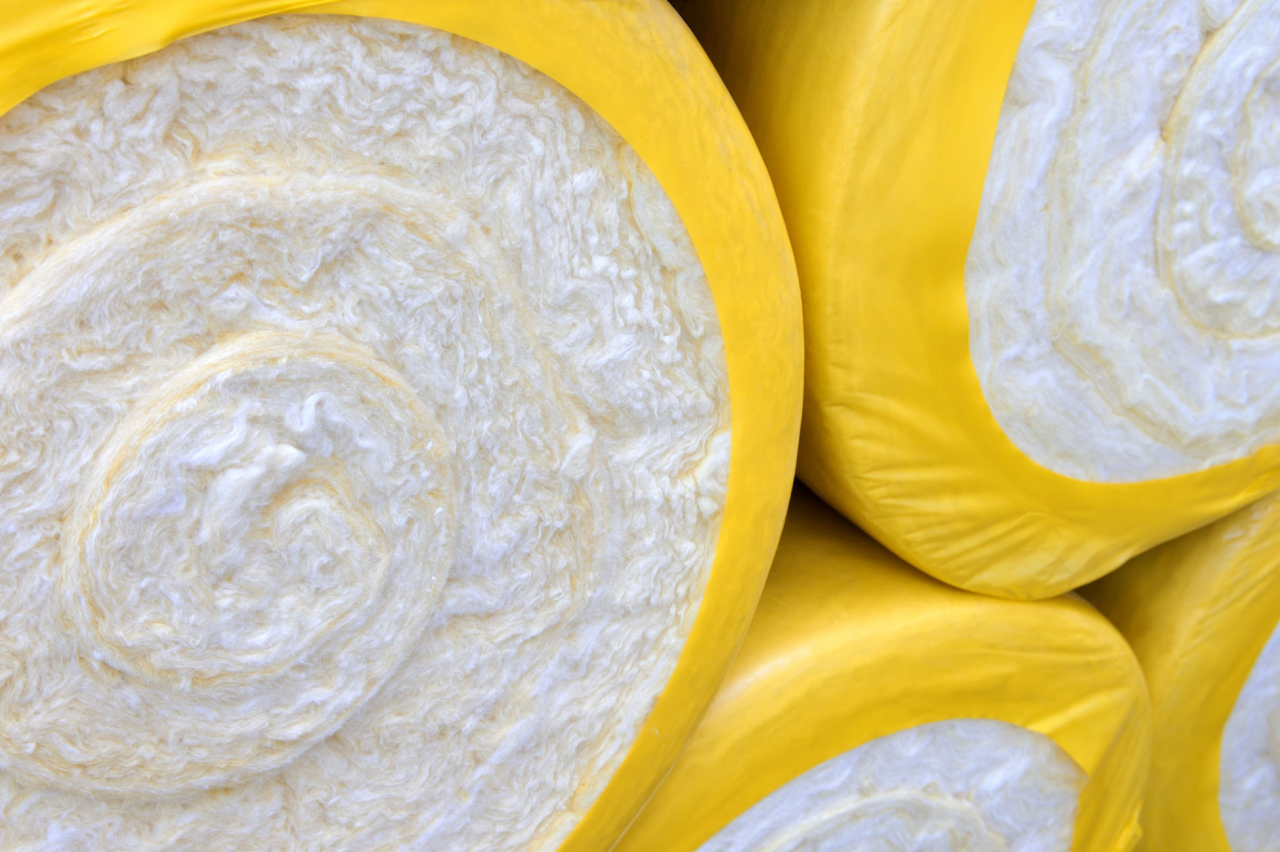
Industry Sector:
Construction/Insulation Manufacturing
Application:
White Wool Transport Fan Drive Motor
Actual Saving:
£56,000 (cost avoidance)
Payback period:
2 days
Product/Service:
- Digital Reliability Services
- Online & Reliability Monitoring
- Engineering Services
Customer Benefits:
- Future foresight and insight
- Reduced downtime
- Productivity savings
- Planned maintenance schedules
- Increased MTBF
For an engineer, what’s worse than an asset failure? Repeated failures of the same asset. But what’s even more frustrating, is repeated asset failures with no explanation all leading to increased downtime and production losses.
With the complexity of today’s machinery, the importance of having foresight into the condition of your assets is more important than ever. Just imagine the positive effects of foreseeing production issues before they become catastrophic.
For one independent insulation manufacturer, who was experiencing regular failures on a fan drive motor, investing in ERIKS Digital Reliability Services provided the answers to one of their long-standing problems.
Challenge
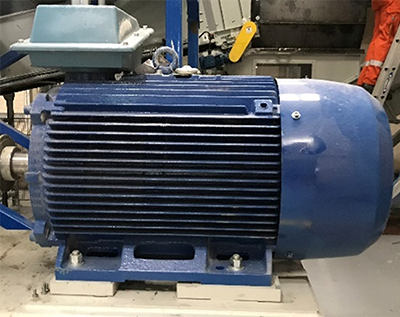
Non-drive end drive motor removed in-situ
The white wool transport fan drive motor in question had clearly experienced significant, undetected deterioration, and failure of the motor non-drive end bearing had been reported on three occasions over the previous 18-month period. That’s an average Mean Time Between Failure (MTBF) of a lowly six months. Troublesome to say to least.
Solution
Following the installation of ERIKS Digital Reliability Services online monitoring which includes tri-axis accelerometers logging velocity, acceleration and temperature, trend data over a five-month period highlighted that acceleration peak and rms amplitudes on the fand drive motor were steadily increasing and in breach of agreed warning thresholds.
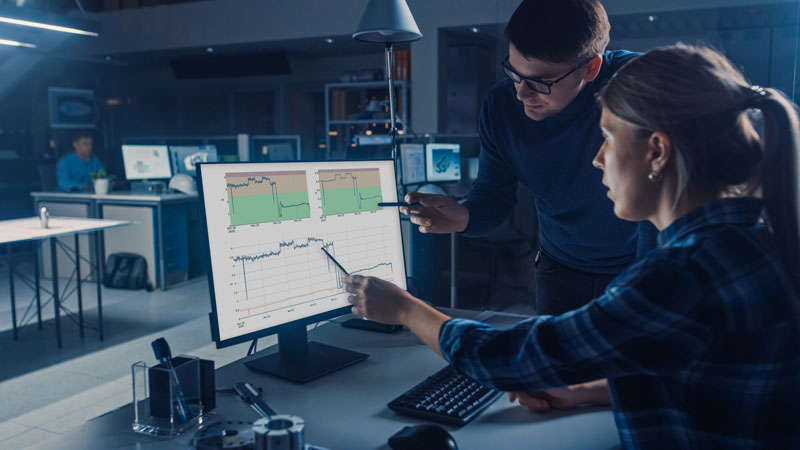
Digital Reliability Services dashboard analysis
It was estimated that the bearing would reach a critical level within just a matter of weeks. ERIKS Condition Monitoring specialists analysed the data, and following an extensive investigation, confirmed that the NDE bearing was the main reason for the deterioration, due to electrical fluting.
The early warning recieved from the ERIKS Digital Reliability Services dashboard enabled the customer to understand the recurring failure mode, and subsequently request additional engineering support from ERIKS to recifty the issue during a scheduled maintenenance window.
The customer has gained a better insight into the health of their critical assets, receiving alerts should pre-determined thresholds be triggered, while real-time data allows for in-depth trend analysis, assisting them in discovering any similar or recurring problems.