In this article
Milking the Benefits from SIlver-Lube® Bearings
Reduced maintenance and downtime periods
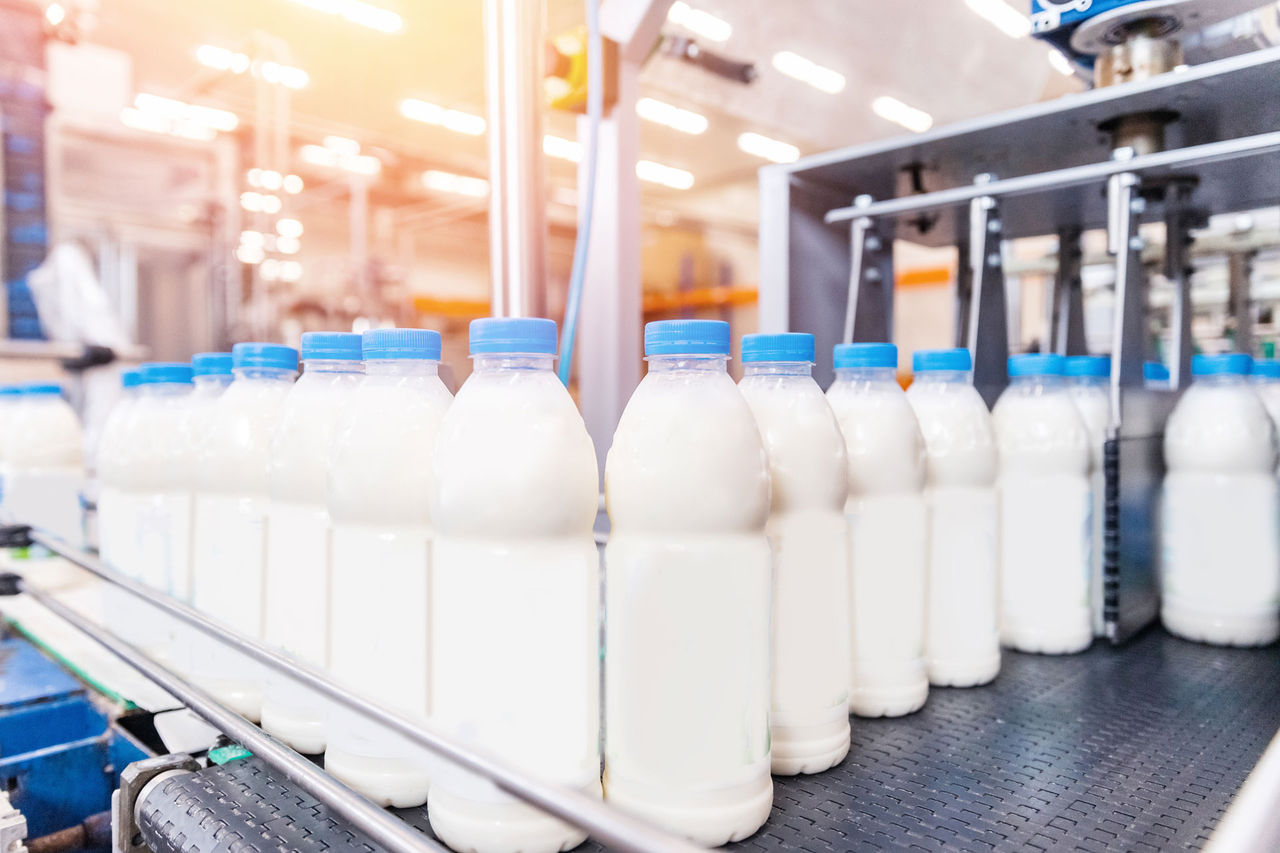
Industry Sector:
Food & Beverage
Application:
Conveyor
Actual Saving:
£32,700 over 5 years
Payback period:
7.5 months
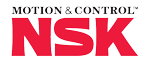
Product/Service:
- Bearing upgrade
- Application support
- AIP Value Added Programme
Customer Benefits:
- Improved reliability
- Reduced maintenance
- Increased production efficiency
- Improved site safety
Enduring repeated bearing failures on your critical assets will have a significant impact on your productivity as well as increasing the stress on your maintenance teams to get production up and running quickly. Recent research has shown that during breakdown periods your team are 9x more likely to have an accident than when undertaking scheduled maintenance. So when a UK based milk processing plant called in ERIKS and NSK, there was more than just downtime disruptions on their mind.
Challenge
Frequent bearing failures on one of its principle conveyors was becoming increasingly problematic, the inaccessible positioning resulted in the inability to provide regular re-lubrication. As a result of this frustrating occurrence, the customer was required to change the bearings every 16 weeks across five conveyors.
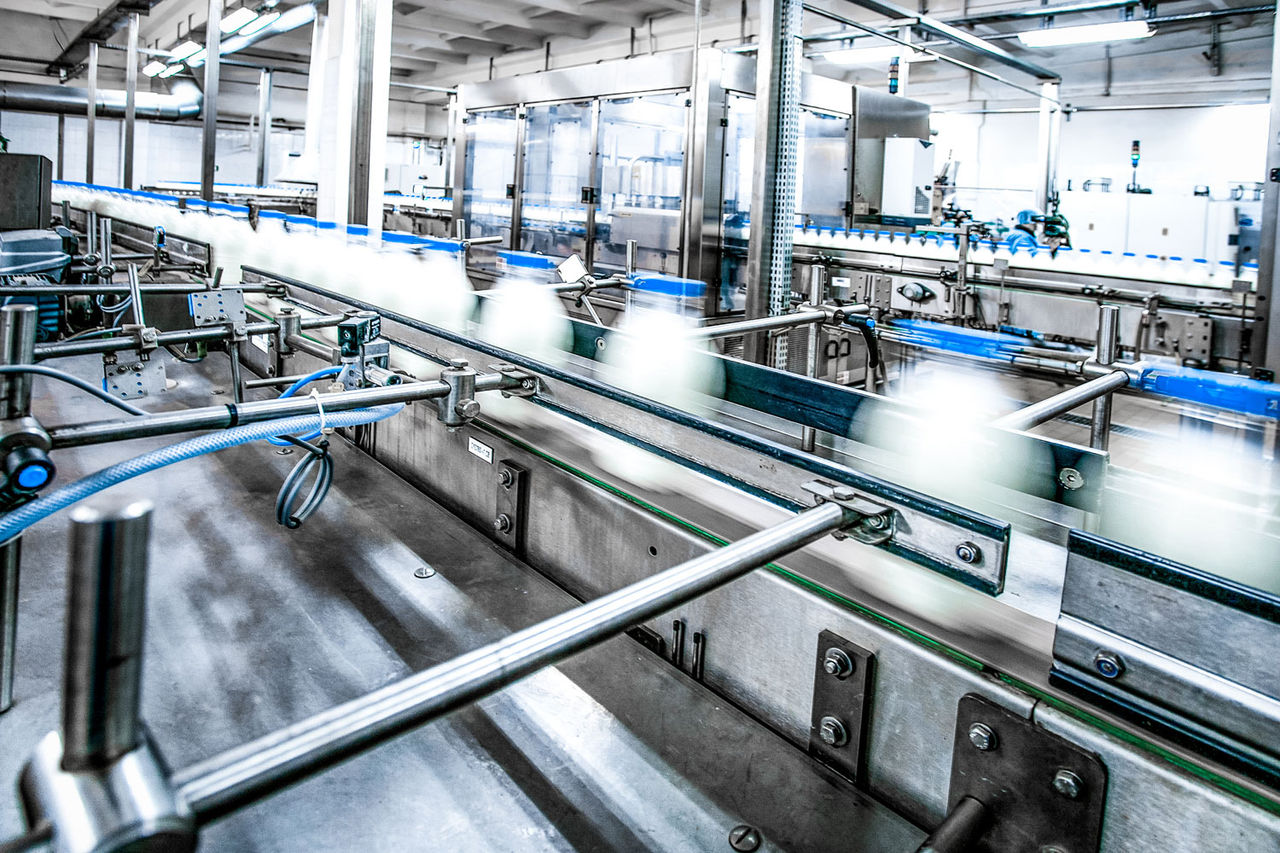
Milk bottling conveyor
Solution
Following an application review, undertaken as part of NSK’s AIP Value-Added Programme, it was discovered water ingress was the issue and causing bearing corrosion. As a result, NSK recommended the use of NSK Stainless Steel Silver-Lube® bearings to eliminate the problem.
The Silver-Lube® series is a range of corrosion-resistant bearing units specifically for use in industries where frequent, thorough washdowns are necessary and optimum hygiene standards are required. The units consist of bearing inserts with high grade stainless steel rings and balls, cage, flingers and set screws.
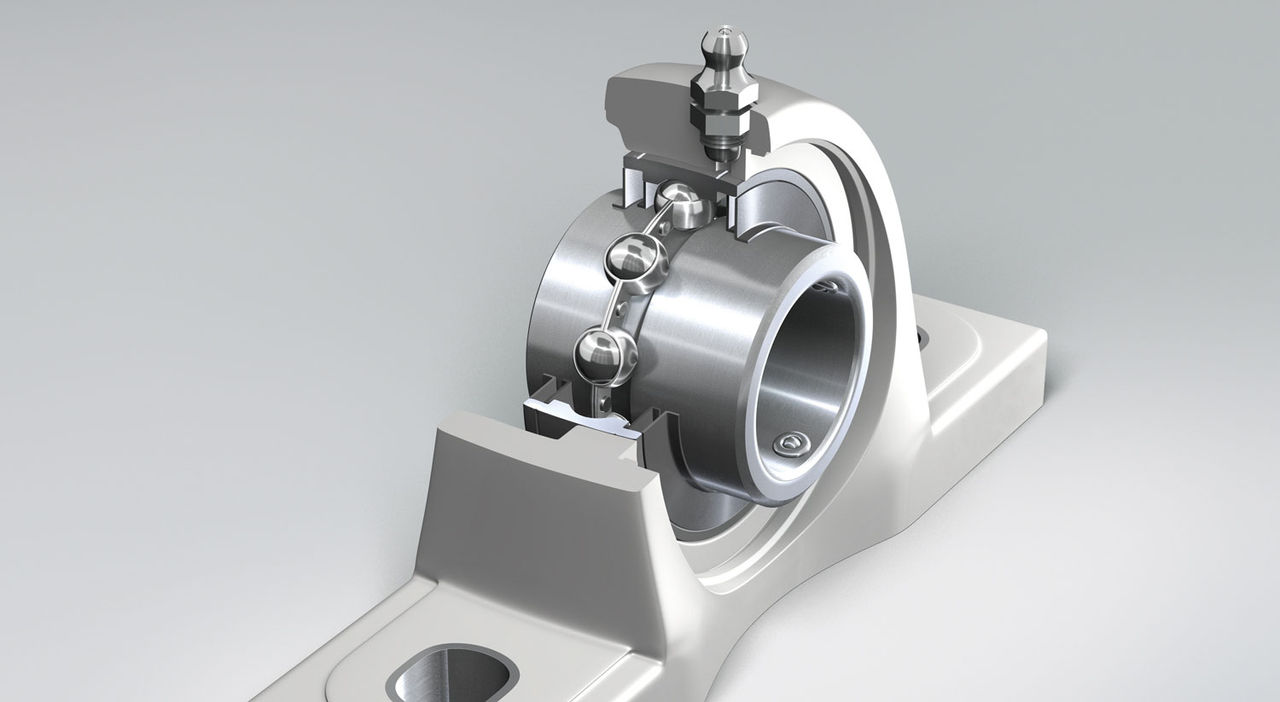
NSK Silver-Lube® bearings
They are further enhanced with durable, heat-resistant silicone rubber seals and are charged with an aluminium complex, high temperature approved food grade grease as standard.
Result
A trial was proposed and implemented on all five conveyor systems. This resulted in a reduction in machine downtime, maintenance costs and significant annual cost saving as bearing service life was extended to more than 5 years. This simple switch resulted in savings of £6,540 pa culminating in £32,700 across five-years trouble-free operation, not to mention improving site safety, after all less haste means more speed and safety.