In this article
It’s not easy being the big ‘Cheese’ in the industry!
A change in material increases longevity
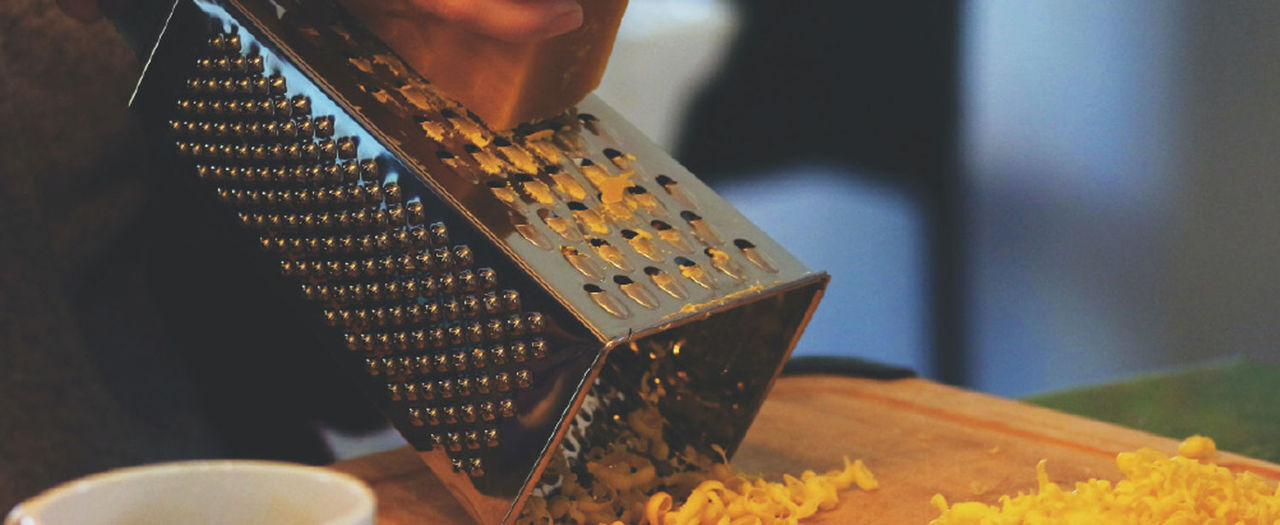
Industry Sector:
Food & Beverage
Application:
Curd Production Line Ball Valve
Actual Saving:
£36,000
Payback period:
Immediate
Product/Service:
- Re-Engineering
- Problem Solving
- Sealing and Polymer
Customer Benefits:
- Increased uptime
- Productivity Savings
- Maintenance Reduction
- Improved production quality
It’s often the smallest of things that can deliver the mightiest of issues. Leaving them unattended or remaining un-noticed they can offer catastrophic results. From a failing spark plug in an engine, finding a hole in the hull of a boat whilst in the middle of deep water or even a loose wheel nut when travelling down the motorway at speed.
Each one starts as a relatively small problem but can quickly escalate into an urgent issue. Take this onto a production line and the results can bring significant damages and incovenience. Losses in productivity, drops in efficiency and unplanned downtime all come at a cost and are never welcome during the process.
Challenge
A leading food manufacturer in the dairy industry was facing quality and contamination issues within their production line and process. It was identified that small particles of rubber had found their way into the food stream.
Traced back to a sanitary ball valve located on the curd line it became quickly apparent that rubber was in fact missing from this component. This occured due to the ‘O’ Ring swelling in tight proximity and as the ring exceeded it’s parameters it became pinched and trapped between the ball of the valve and the PTFE Seal, inevitably resulting in the cutting of the rubber leading to the overall contamination.
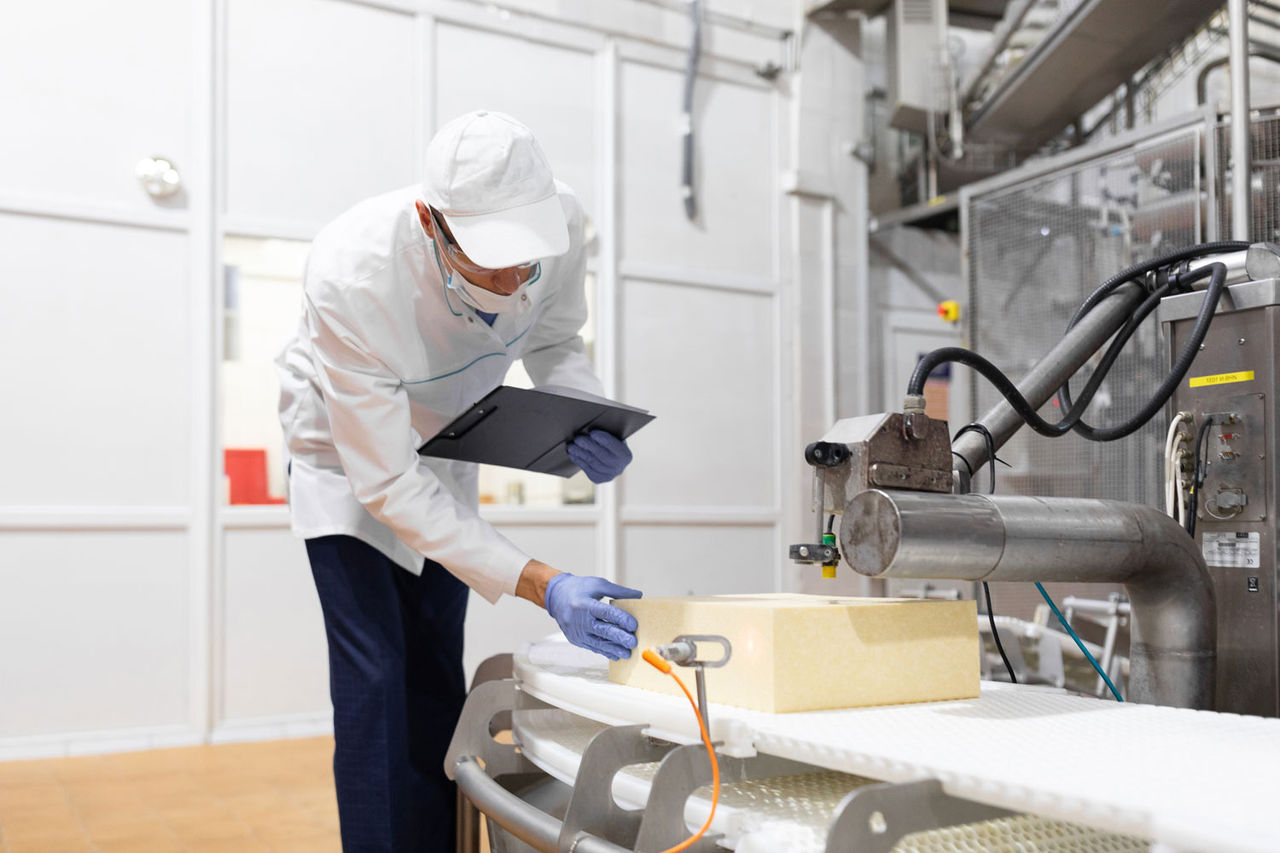
Production line inspection of goods
With the component failing after just 2-3 months from installation, it was imperative for the customer to seek a long-term solution, to eliminate both unnecessary cost and unplanned downtime. The ERIKS Team were contacted to aid in resolving the matter with their extensive know how and expertise, a solution could be identifiied and implemented.
Solution
With an on-site visit organised for ERIKS Sealing and Polymer Technical Specialists a complete review of the application was conducted. It was revealed that the O-Ring was manufactured from EPDM - (a form of synthetic rubber) supplied from the original equipment manufacturer (OEM). Which was found to be the root cause of the issue due to the material of the O-Ring unable to withstand the production line process.
Evaluating the overall operation of the line, the ERIKS Technical Specialists recommended that the manufacturer opt for an alternative O-Ring with a V-70-594 fluorocarbon (FKM) ring. This ring offers improve benefits such as heat resistance and a good compression set.
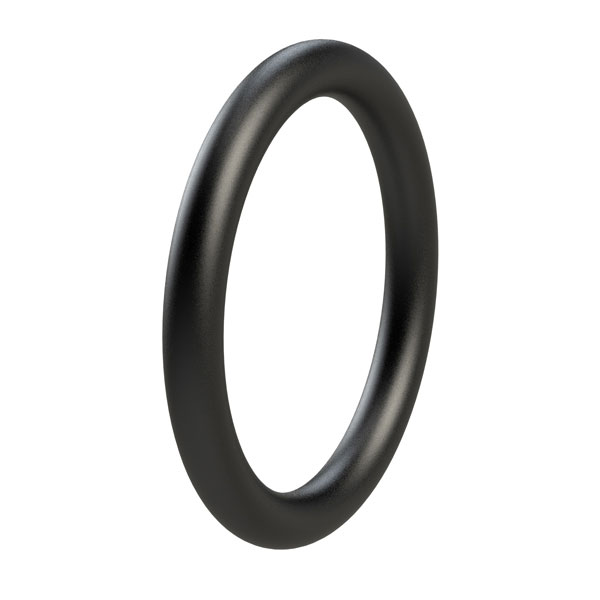
V-70-594 O-Ring produced from Fluorocarbon
Fluorocarbon as a material offers increased toughness and durability through its structure whilst remaining repellent of liquid - making it the ideal choice. Conforming to relevant compliance FDA 21 CAR 177.2600 for use with dry, aqueous and fatty foods, this O-Ring is also manufactured to be free from animal-derived ingredients (ADI) not only improving the process instantly but remaining friendly to todays demands and standards.
Result
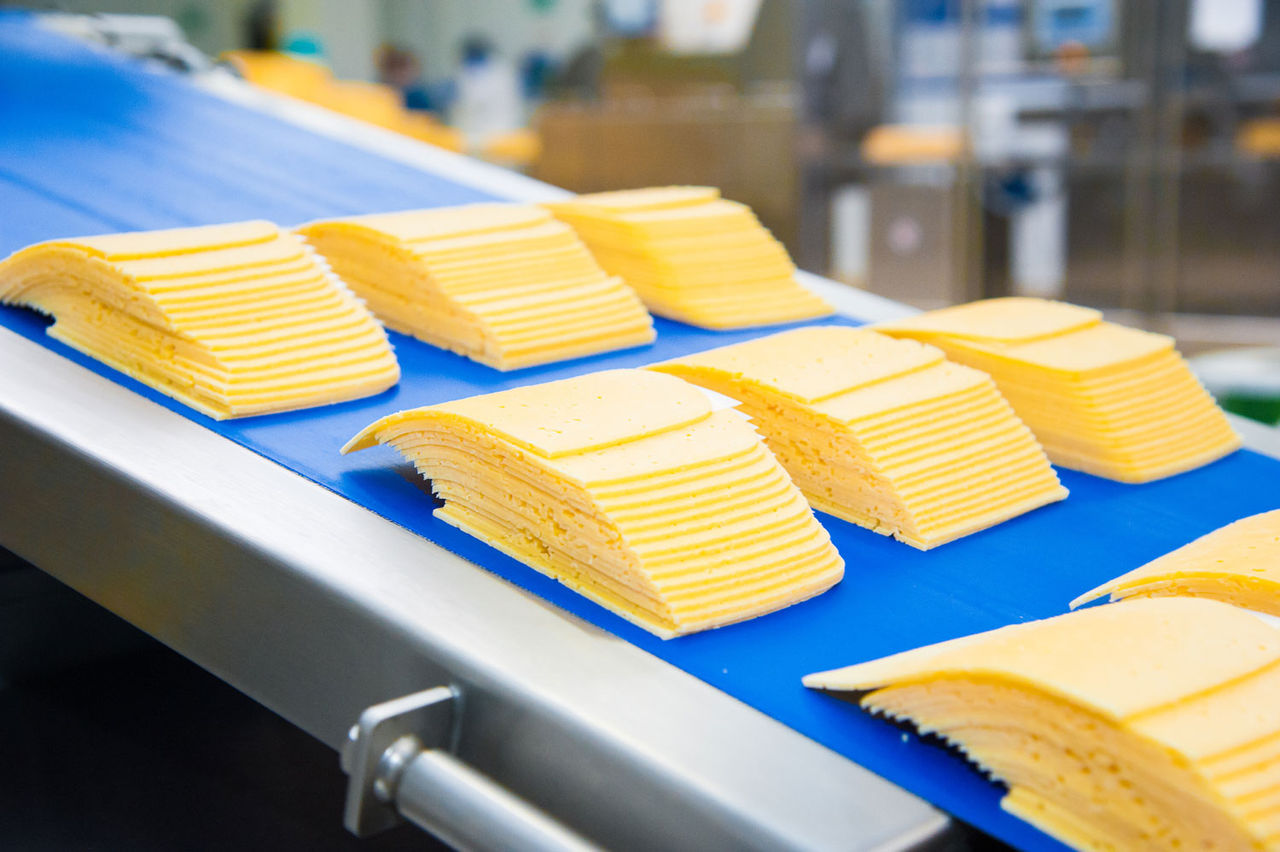
Conveyor belt transporting goods
After the specialist teams extensive and in-depth evalutation the relevant feedback was given to the customer advising the suggested change in O-Ring, the customer has since implemented and have reported a significantly improved production time. With no premature failures to date over a recorded period, and no reports of noticeable degradation in material performance.
This simple change in O-Ring and material on the production line has given the customer an overall saving of £36,000 delivering benefits such as reduction in maintenance, improved production quality and reliability.
Further eliminating immediate possibilities of unplanned downtime and unnecessary costs. Overall, helping an industry leader to remain on top of the competition and delivering the very finest ‘cheddar’ worldwide.