In this article
Motor Overhaul Remains Right On Track
Reduced downtime, increased safety, lower costs
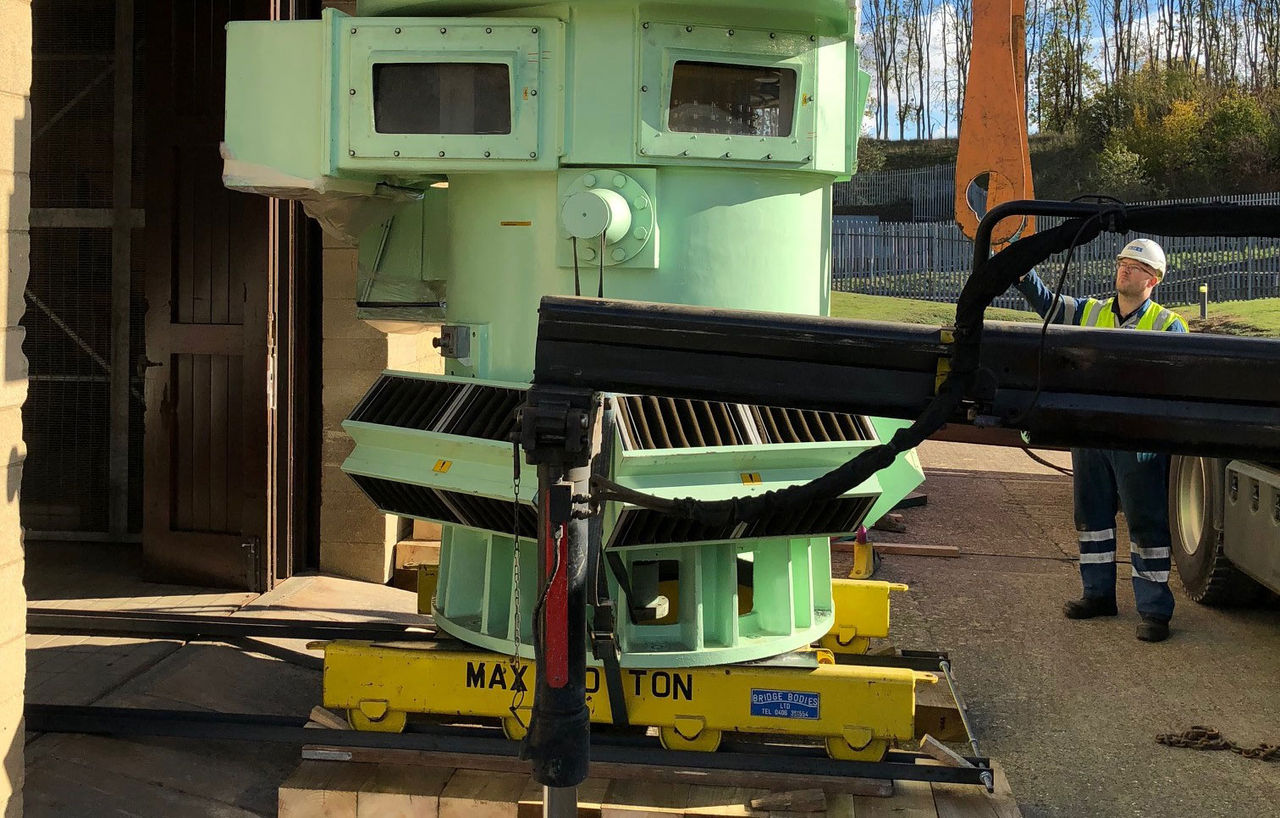
Industry Sector:
Water & Wastewater
Application:
High Voltage Motor Extraction
Actual Saving:
£20,000
Payback period:
Immediate
Product/Service:
- Power Transmission
- High Voltage Motor Repair
Customer Benefits:
- Reduced costs
- Increased operator safety
- Reduced downtime
- Maximised productivity
- Complete Motor Overhaul
- Reusable Bespoke Solution
Being responsible for supplying drinking water is something we as consumers take for granted, and any interruptions to the supply is a massive problem, the pressure on the water company is immense.
So, ensuring that all of your pump applications are in constant working order is essential, even more so when scheduled maintenance is on the horizon.
Challenge
One supplier of fresh drinking water had six booster pumps on site (three duty and three stand-by) and was looking to better their supply and avoid reduced asset availability at all costs. A planned maintenance schedule required a complete overhaul to be undertaken in a tight six-week timeframe.
The unmanned site posed a number of extraction issues due to the size and location of the motors, the mobile crane previously hired was no longer seen as safe solution under current health and safety standards. It was time for ERIKS to come up with a solution to keep the overhaul on track, literally.
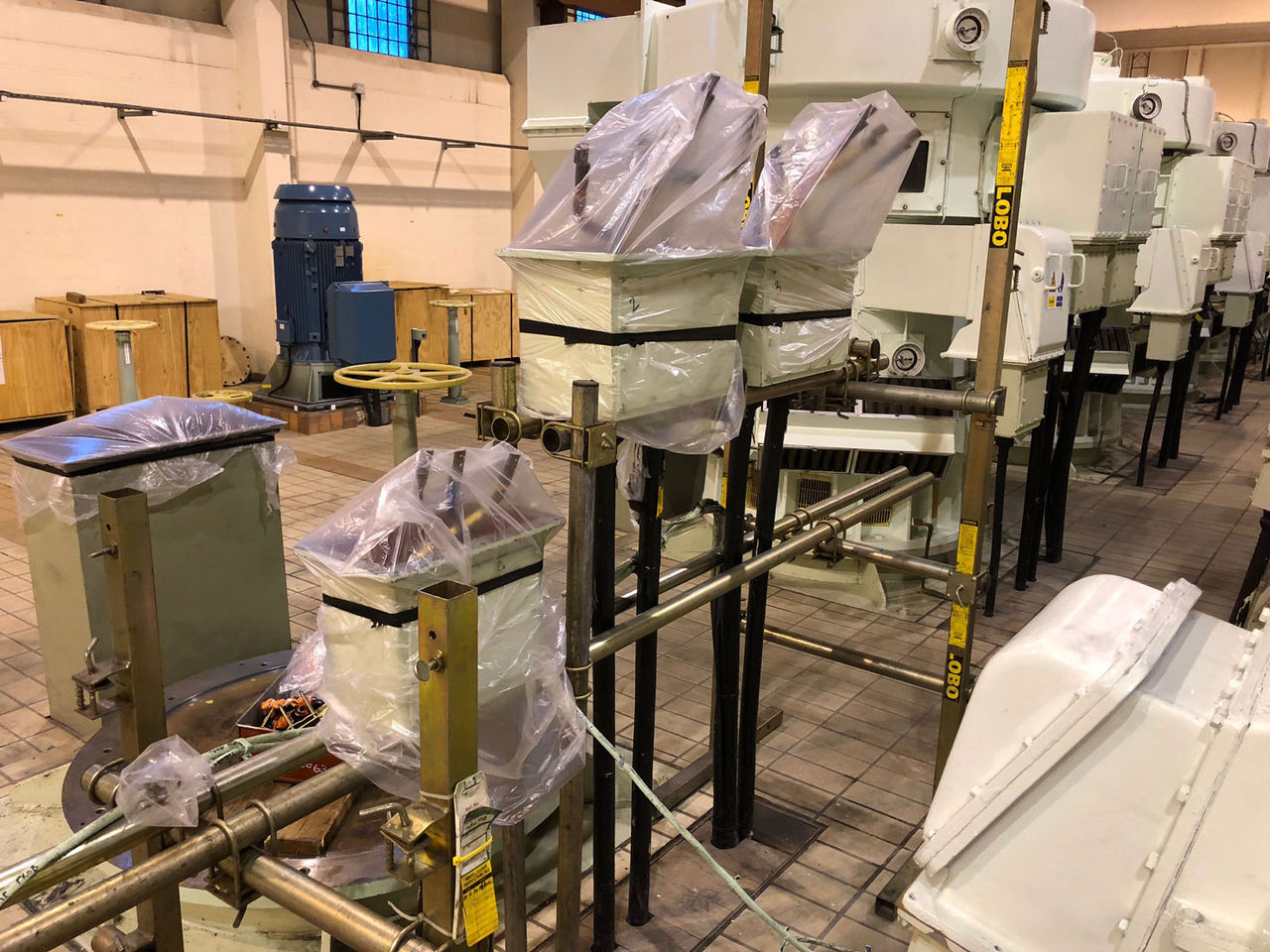
Pump application in-situ
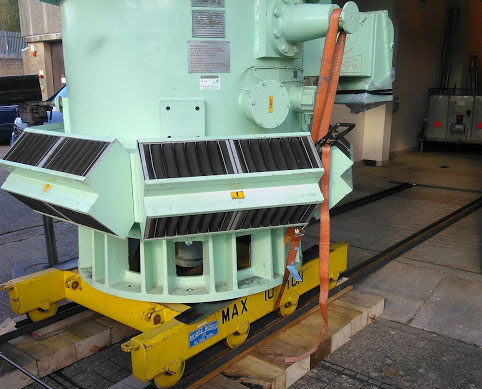
Pump and motor loaded onto bespoke track system
Solution
The ERIKS team devised an innovative track system that would enable the motor to be wheeled out of the plant room, the track could be extended to the loading area using additional railway sleepers, overcoming the issue of the small slope at the exit.
The track system was simple to install, meaning that the motor extraction was significantly quicker, easier, and safer than the previous crane and slings method.
Additionally, it can now be used at no extra cost for all future motor extractions on-site, enabling the customer to realise cost savings each and every time a unit is required to be removed from site.
Result
The bespoke solution meant that the extraction was quicker, saved the customer over £20,000 in third-party crane hire, and more importantly increased operator and site safety. The new extraction solution made routine maintenace easier to plan, maximising the time within the customers scheduled shutdown period for the ERIKS team to complete the overhaul of the motor, install and commission