In this article
Keeping production flowing freely
Monitoring & maintaining an often overlooked asset
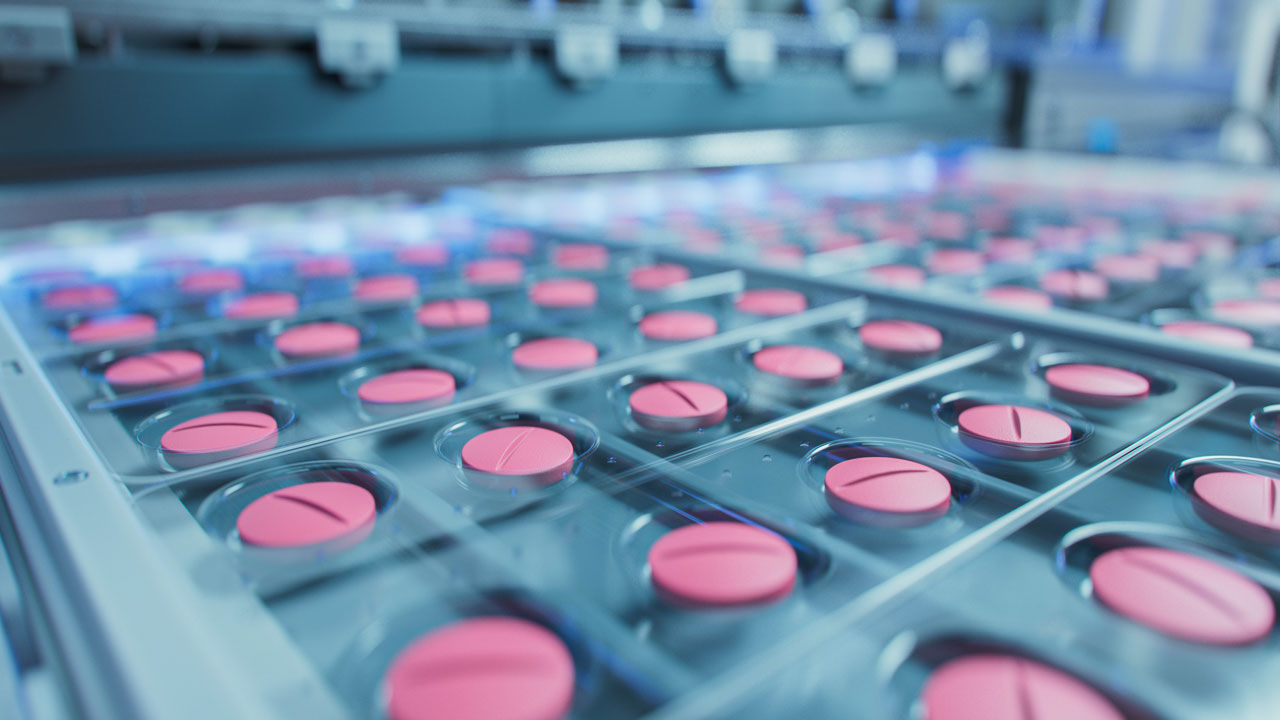
Industry Sector:
Pharmaceutical
Application:
General industry & specialist
Actual Saving:
£25,000
Payback period:
Immediate
Product/Service:
- Hose Management System
Customer Benefits:
- Increased safety
- Reduced downtime
- Reduced stoppages
- Regulatory compliance
- Reduced process breakdowns
If 15% of your site’s motors were at risk of failure, you would take pretty swift action to address the issue. 15% of its gearboxes or pumps? That would have maintenance engineers working overtime until they were fixed. But one ERIKS’ customer was completely unaware that 15% of their hoses were either leaking, overdue for replacement, or otherwise at risk of failure.
For an ATEX and COMAH Tier 1-rated site, that wasn’t just a worry. It was a serious risk of process breakdowns or stoppages, a health and safety incident, or even a major accident.
ERIKS hose experts not only identified the problem, but also put in place a Hose Management System to ensure it never happened again.
Challenge
The customer is a major pharmaceutical manufacturer, with a number of sites. The site assessed by ERIKS’ hose experts comes under the scope of two important regulations. Firstly, it is a workplace with a potentially explosive atmosphere under ATEX. And secondly, it is COMAH Tier-1 rated, for the presence of dangerous substances which can result in a major accident, and cause serious damage or harm to people and/or the environment.
With 825 hoses on the site – ranging from high-end PTFE to general industrial hoses, and specialist hoses for transporting various chemicals – the potential for leaks, bursts, wear and corrosion is high. The large number of hoses, plus the lack of priority for hose maintenance, also meant that five-yearly replacement (in line with British Fluid Power Association guidelines) had rarely been achieved.
The customer not only required a full survey of existing hose assets, but also a more reliable and efficient method of recording and monitoring those assets – to enable future timely inspections, planned maintenance, and scheduled replacements.
Solution
ERIKS hose experts carried out a visual inspection of all the customer’s hoses on the site. The inspection looked for leaking or corroded hoses or connections, and signs of age. Out of a total of 825 hoses of various types, no fewer than 130 were found to be either leaking, overdue for replacement, or otherwise at risk of failure. That represents 15% of hose assets with the potential to cause stoppages, process breakdowns, health and safety incidents or major, catastrophic accidents.
Having identified and replaced the failing hoses and connections, the experts introduced the ERIKS Hose Management System (HMS) to the customer’s site.
As part of the initial survey, every hose was physically tagged after inspection, with a unique number and barcode or QR code. A full written report was also presented to the customer, detailing hose condition, recommendations for upgrades, and proposals for alternative fittings or specific enhancements for individual applications. This detailed information was entered into the HMS database, cross-referenced with the codes on the tags.
The logged information also includes the hose type, size, availability (in stock on-site, or to order), dates of manufacture and modification, certificates of conformity, inspection dates and OEM technical drawings.
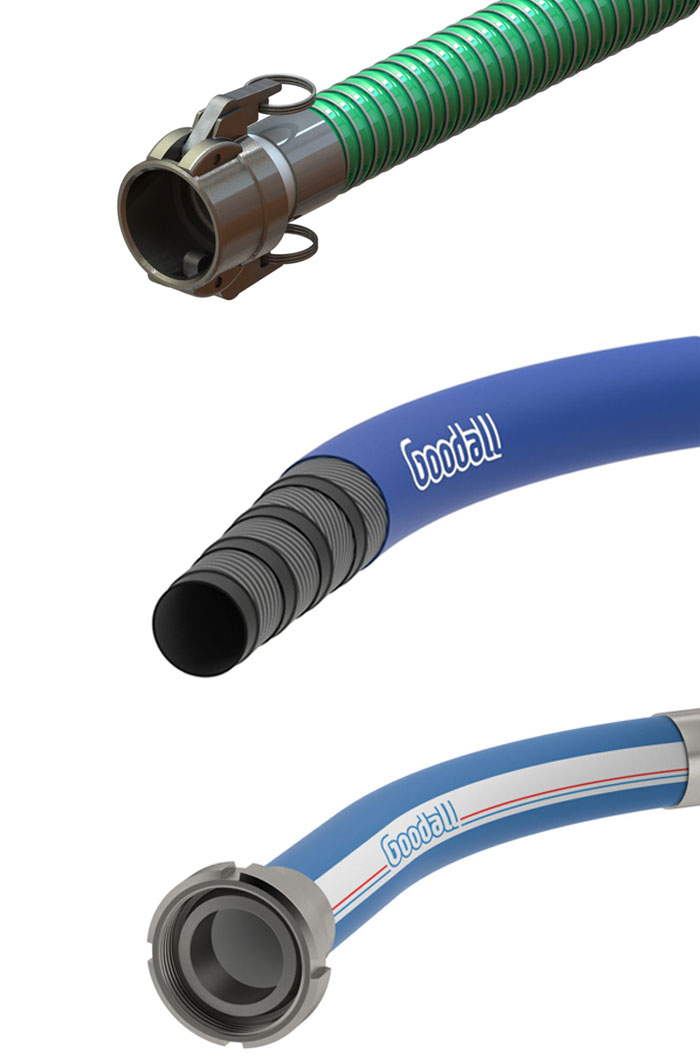
Range of Goodall hoses
With the HMS in place, the system automatically monitors the age of each hose, and provides ‘Valid’, ‘Almost Expired’ (three months in advance of the BFPA 5-yearly replacement deadline) and ‘Failed’ warnings.
As part of the HMS service, ERIKS now also provide the customer with monthly meetings and annual hose inspections and also consult with the customers project management team on new & refurbishment projects on assets that utilise hoses adding value through industry specific experience and product recommendations.
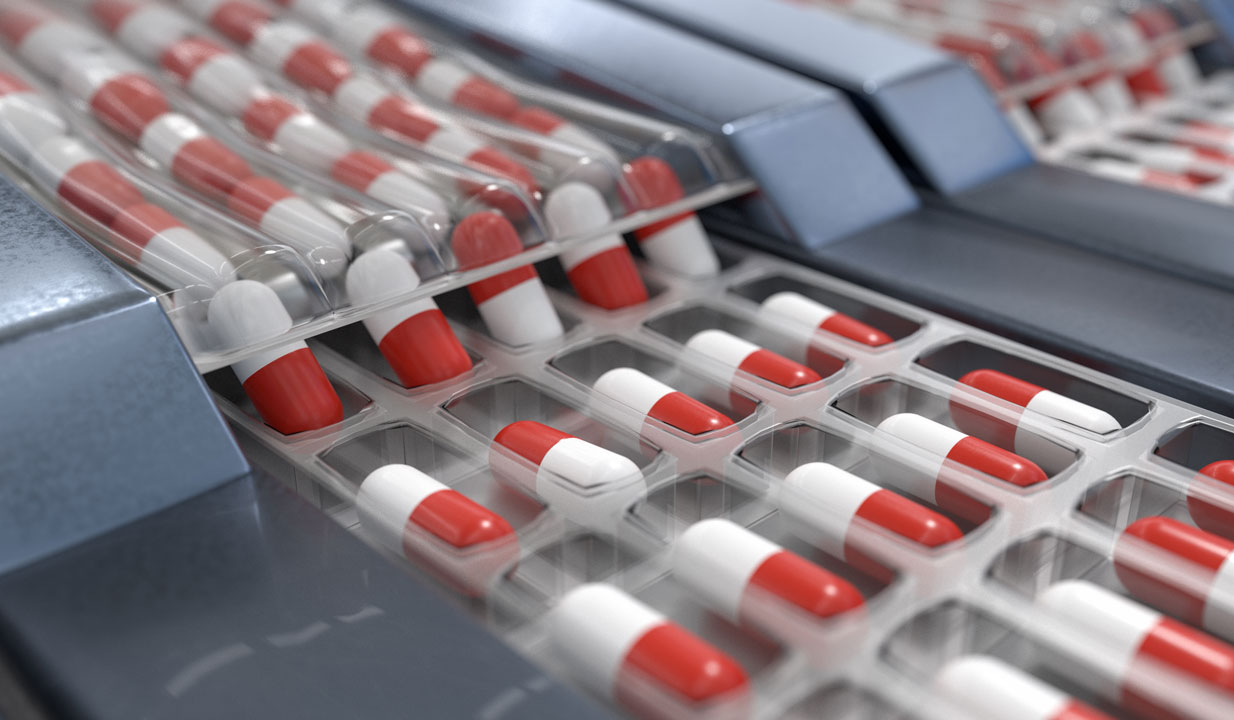
Result
With no real insight into hose condition, a spreadsheet of hose assets is essentially just an inventory rather than a management system. By providing the customer with a digital dashboard recording their hose assets, the ERIKS Hose Management System offers a significant improvement.
Previously, hoses were replaced only when they visibly failed. Now, with monitoring via the HMS, they can be replaced in line with BFPA guidelines – helping to avoid any accusations of negligence or non-compliance under HSE, ATEX or COMAH regulations.
Timely replacement – together with regular inspections by ERIKS – also helps to reduce the risk of hose or connection failure, and associated stoppages, breakdowns, incidents and loss of production. And by removing the burden and responsibility of hose management and maintenance from the internal engineering services team, ERIKS HMS allows them to focus on even more production-critical tasks.