In this article
Inspection reveals exceptional service
Meeting nuclear industry standards as standard
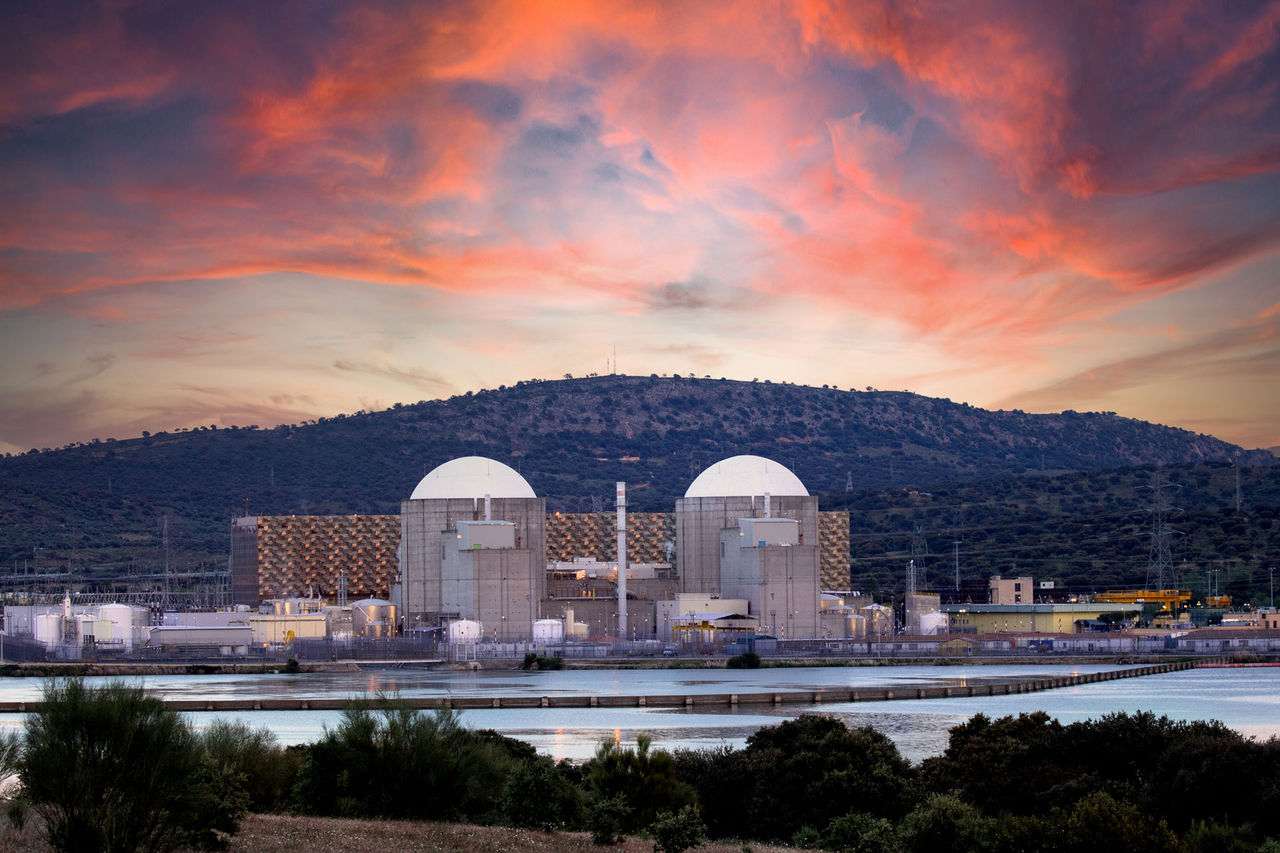
Industry Sector:
Nuclear
Application:
Cooling water pump motor
Actual Saving:
£25,000 / hour (cost avoidance)
Payback period:
n/a
Product/Service:
- Specialist Engineering
- HV Motor Repairs
- Compliance
Customer Benefits:
- Successful repair and refurbishment
- Extended motor life
- Tested, inspected and signed-off maintenance to nuclear industry standards
The engineering, maintenance, repair, testing and inspection standards for the nuclear sector are some of the highest in industry – for obvious reasons.
Even assets with only a indirect connection to the nuclear aspect of operations are rigorously third-party inspected during repair and refurbishment. This can identify failings in processes or – in ERIKS’ case – highlight the high standards which are already in operation as a matter of course.
Challenge
A UK nuclear power station operates an 11000V, 1580kW motor which drives a main cooling water pump. The motor is positioned on top of the pump, which pumps water around the power station.
Although this is not part of the reactor set-up or the nuclear operation, it is critical to the functioning of the power station, and its failure could negatively affect the station’s operation.
To ensure minimum interruption to operations in the event of a motor failure, the operator maintains a spare motor. A duty motor is replaced every 12 months with the overhauled spare, and then the ex-duty motor is inspected and overhauled to then become the spare, and this cycle is repeated yearly across all the motors.
If the inspection reveals maintenance and repairs are required, these are carried out and the work is subsequently inspected by a third-party rotating equipment expert.
The work is carried out to a pre agreed and approved quality plan specifically developed for these motors which is in accordance with the customers nuclear reference specification for HV motor overhaul.
All work must be signed-off by the inspector before the next stage can progress.
Solution
The dismantling, cleaning, inspection and testing procedure has been agreed in advance, and ERIKS Chesterfield has been undertaking the motor maintenance for many years.
The amount of repair or refurbishment required can vary year-to-year, but the most recent inspection is a good example of the procedure and its extent, and of the inspection regime.
Stator
- Winding washed, dried and inspected. Condition: good.
- IR stator tests carried out after cleaning and drying. Polarisation Index: 11.1.
- Surge comparison test. No fault indications.
- Tan Delta tests carried out to 11kV. Results indicate insulation condition is good.
- Partial Discharge (PD) tests carried out from each phase end up to line voltage
The PD test levels were higher than expected in some phases. Inspection revealed the star point connection cables had been rubbing on the corner of the steel stator frame, which could lead to fretting damage. This was further investigated with a PD retest with the leads removed and insulated from the frame. Results proved the leads were the cause of the anomaly. Extra over-insulation was installed, and a clean-up, remake and re-insulation of the star point was carried out.
- Core flux test. No abnormalities, problems or hot spots.
Stator auxiliaries
- All tested okay except 1 of the 6 RTDs, which is earthed. Only 3 are normally in use and 5 remain available.
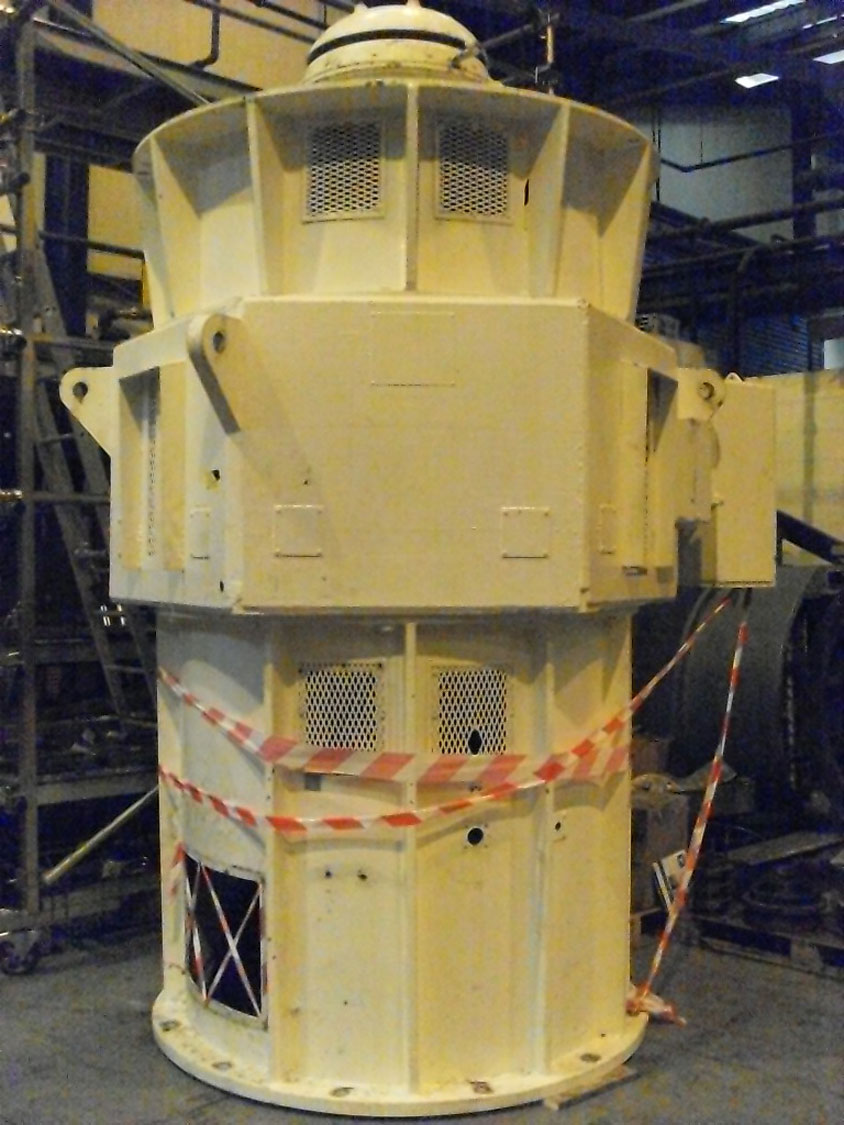
Cooling water pump motor in Chesterfield workshop
Result
ERIKS operates an open and transparent maintenance and repair service as a matter of course – not just for the nuclear industry – and always works to the highest standards. So a third-party inspection is never a problem.
In this case, the motor parts were inspected and signed-off before the rotor was rethreaded for rebuild. Once reassembled, the motor was set up in the ERIKS test bed, and the bearings filled with oil for a low voltage, no-load test run to full speed. This was witnessed by the third-party inspector.
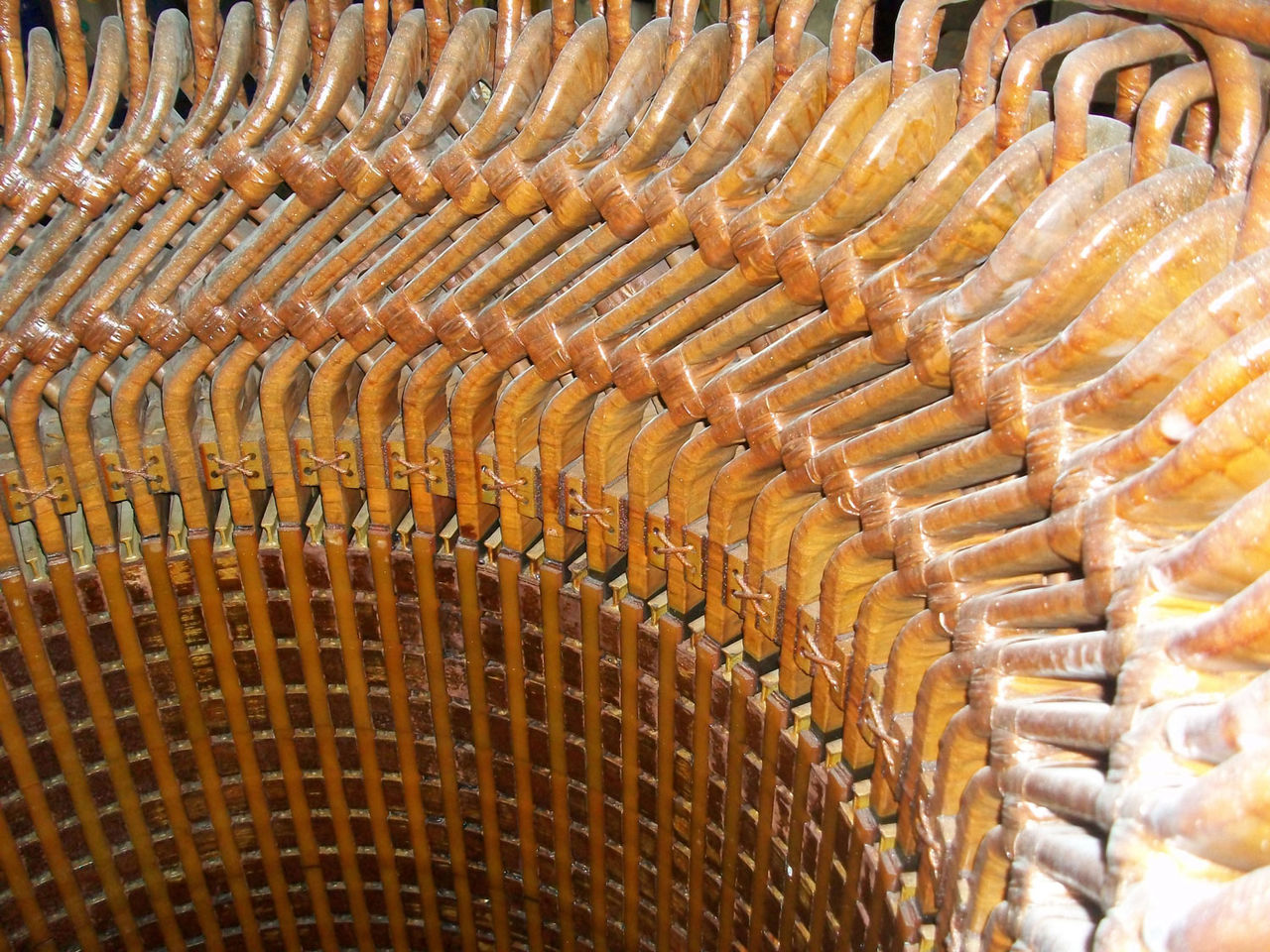
Stator windings inspection
The final third-party inspection – before painting, and the pre-dispatch Insulation, Resistance and Polarisation Index tests – was a check of a sample of bearing housing bolts for tightness.
As always, ERIKS’ engineering know-how ensured the motor passed with flying colours.