In this article
New belt shows its grit against gravel
Longer life, greater efficiency - and less costly too
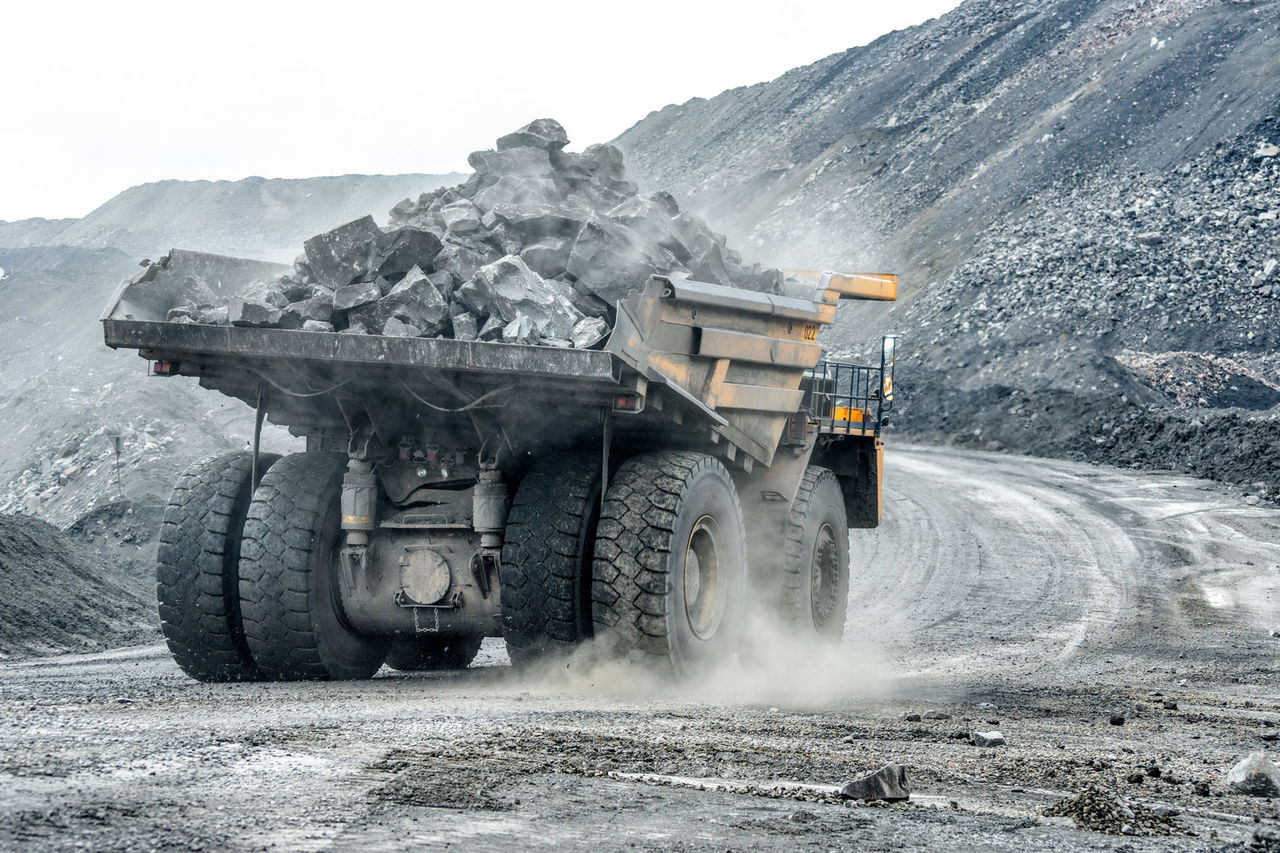
Industry Sector:
Primary Industries
Application:
Vibratory Screens
Actual Saving:
£919.16 p.a.
Payback period:
N/A
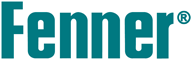
Product/Service:
- Transmission Belts
Customer Benefits:
- Cost savings
- Reduced maintenance
There are few tougher operating environments than a granite quarry. And for transmission belts, it’s not just the rocks and the explosions that make life hard, but the dust too.
Repeated belt failures on their vibratory screen applications were costing a quarry operator money for replacements, as well as taking up their maintenance engineers’ valuable time. After seeing photos of the belts, ERIKS Application Engineer for Rotating Equipment made a site visit to get to the root of the problem.
Challenge
The customer’s vibratory screens – used to sort granite gravel into different sizes – rely on transmission V-belts for their operation. Despite trying belts from several different manufacturers, the issue was always the same: belt failure after six months on average.
The images sent to ERIKS by the customer showed the failed and snapped belts, but didn’t reveal the cause. A site visit was clearly required.
The operating noise level of the vibratory screens is so high that they only run during the quarry’s daytime shift. So to avoid production downtime, the ERIKS engineer’s site visit took place during the night shift.
This on-site inspection first considered the three most likely causes of belt failure: the belt is incorrectly tensioned; the pulleys are misaligned; the pulleys are worn. Assessment – including the use of a laser alignment tool – revealed that the alignment and tension were satisfactory, but that new belts were being fitted to worn pulleys, and some of these belts were of insufficient quality.
These two factors combined with the ingress of dust from the environment, leading to excessive heat. This was causing the belts to undergo a secondary cure during use – making them unstable and more likely to snap.
Although the customer had installed dust guards to try to prevent dust ingress, this was insufficient to keep the belts dust-free.
Solution
Completely eliminating dust from a quarry is clearly impossible. So the solution to the customer’s problem had to lie in the transmission belt itself.
ERIKS’ know-how led the engineer to propose the Fenner® Quattro PLUS CRE heavy-duty V-belt, manufactured from synthetic rubber EPDM. This belt not only has an extended operating temperature range of -40°C to +130°, but also has an enhanced tooth profile.
This is designed to improve belt flexibility and reduce bending resistance, but has the added benefit of helping to dissipate heat build-up.
The belt has a reduced weight compared with other Quattro belts, as well as transmitting 20% more power and providing a 15% longer life.
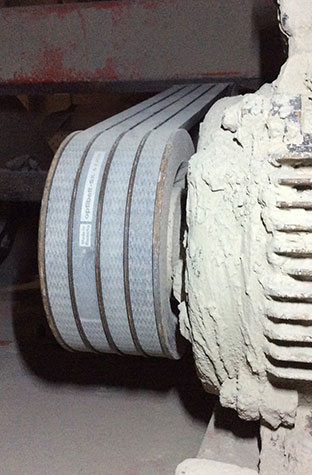
Close-up of original setup
Result
New Fenner® Quattro PLUS CRE belts were fitted to all the customer’s vibratory screens, and ERIKS monitored their lifespan.
The monitoring revealed that the Fenner belts were lasting twelve months at least. All of the alternative belts previously fitted had lasted no more than six months on average before failing.
The labour cost savings from fitting fewer replacement belts amounted to £1321.20 over a two-year period. In addition, the Fenner® Quattro PLUS CRE belt is less expensive than the belts previously used – saving another £258.56p.a. And with less time spent replacing failed belts, the customer’s engineers had more time for other maintenance tasks, to help keep the quarry running more smoothly and operating more efficiently.
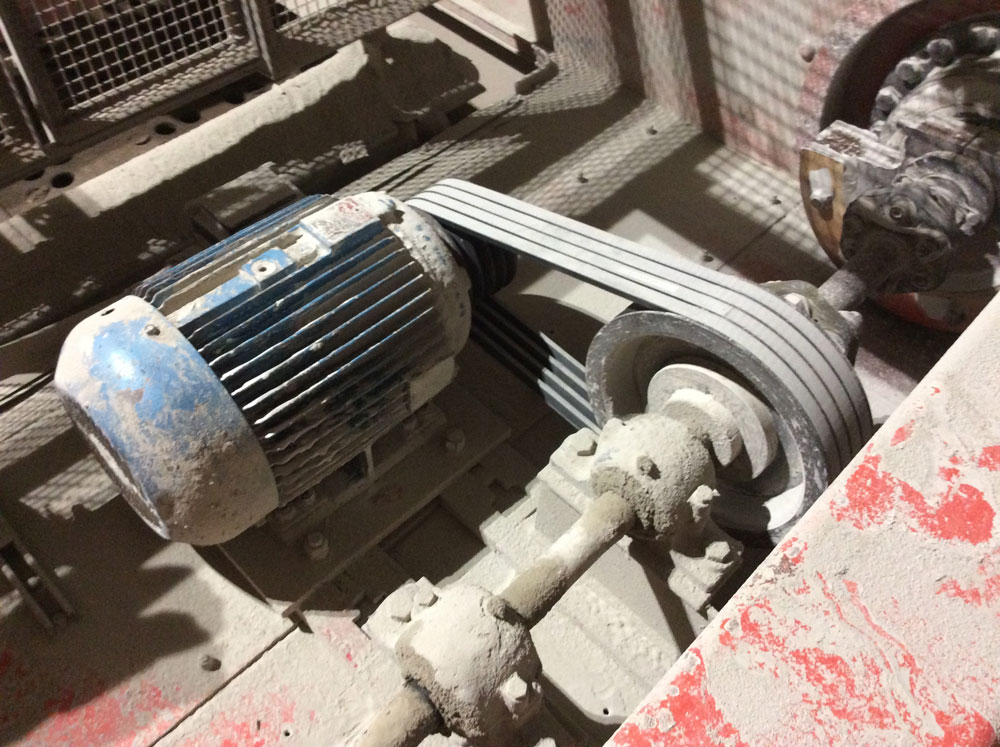