In this article
ERIKS Complete Package Gets Ferry Back on Track
From enquiry to redesign through to commission
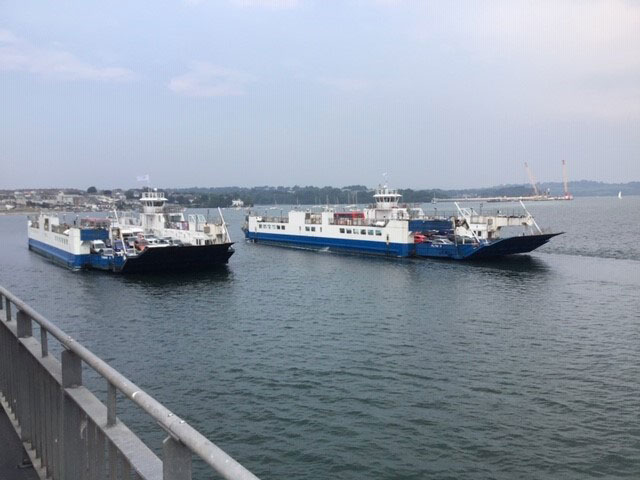
Industry Sector:
Transport
Application:
Ferry Port Gantry Sheaves
Actual Saving:
£2,239,440
Payback period:
7 Months
Product/Service:
- Power Transmission
- Re-Engineering
- CAD Design
Customer Benefits:
- Increased uptime
- Reductions in lost revenue
- Bespoke engineering
- Reduced lead time
- Improved health and safety
Picture the scene.
Your business is experiencing substantial revenue losses totalling hundreds of thousands, if not millions. Health and safety risks surround you. Your service is severely disrupting the community and other local businesses. And a media frenzy is attempting to damage your reputation.
Now throw in a global pandemic, posing more disruption to your supply chain, preventing you from getting your operation back to full service.
Sounds like your worst nightmare, right? Well, for one busy UK ferry terminal, the nightmare was real, and problems continued to mount.
Although an unfortunate sequence of events to tackle at any one time, to put it bluntly, this could happen to any of us at any given moment if we aren’t fully prepared for unexpected challenges.
So, having an emergency action plan in place, or access to the right expertise and strong supply routes, is essential to minimising, or even avoiding, disruption to your business and revenue streams.
Challenge
With one vessel (from three) already out of commission due to a scheduled 14-week overhaul, an inspection of the gantries at either end of the port reported some unexpected wear on a selection of the pulleys.
Having previously completed a guide chain tray sheave at the ferry terminal, ERIKS Power Transmission Product Business Unit were invited back to investigate the critical failures on the gantry sheaves that were causing severe disruption to service.
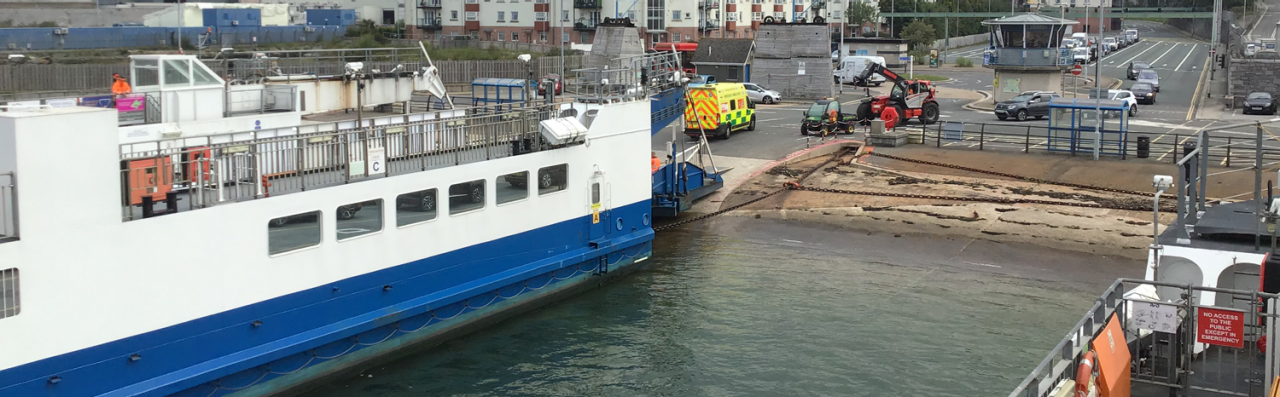
Following consultation and site visits with the customer, it was concluded that the pulleys required replacement to ensure that the ferry could be safely operated when docking into each terminal. As a public service, passenger safety is paramount and the main consideration whenever in operation, therefore highlighting the issue and devising the right plan of action was essential for protecting terminal staff and ferry users.
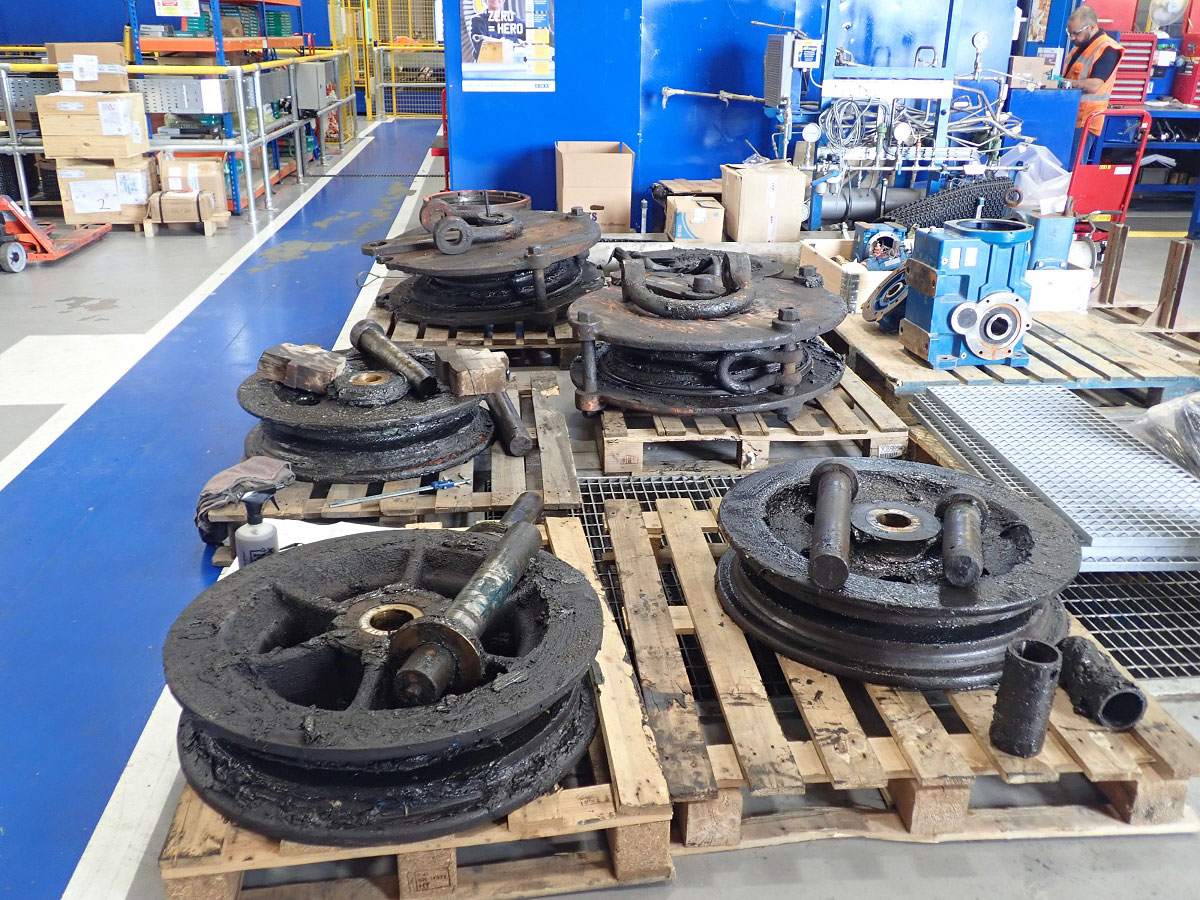
Worn pulleys at Plymouth Service Centre
Challenges arose from the get-go. There were no drawings of the current assembly available, and a redesign decades prior had updated the gantries to a chain format, which was no longer suitable for operation.
A total redesign was required, from scratch, with nothing but conversations with the terminal management team forming the basis for the new installation. ERIKS’ engineering know-how, best practice and expertise was about to be put to the test.
The Challenges kept on coming
But the challenges didn’t stop with the design aspect, continuing to mount with the COVID-19 pandemic causing further disruption to supply chains, and restrictions from the initial lockdown period making further site visits and face-to-face consultations difficult to facilitate.
Regular discussions were held virtually, abiding by strict government regulations on travel and social distancing, with site visits arranged only where essential.
Initial fears from the customer were that the project could take up to 12 months to completion, and given the high traffic turnover of the terminal, and community dependency so high, this timeframe needed to be shortened dramatically.
Just to add some context to the scale and importance of the project, this particular ferry operation is the largest chain ferry service in the world, and the UK’s busiest inland waterway crossing, catering for the demands of 8,000 vehicles and 1,500 pedestrians every day, including emergency services, operating 24/7/365 regardless of conditions.
Solution
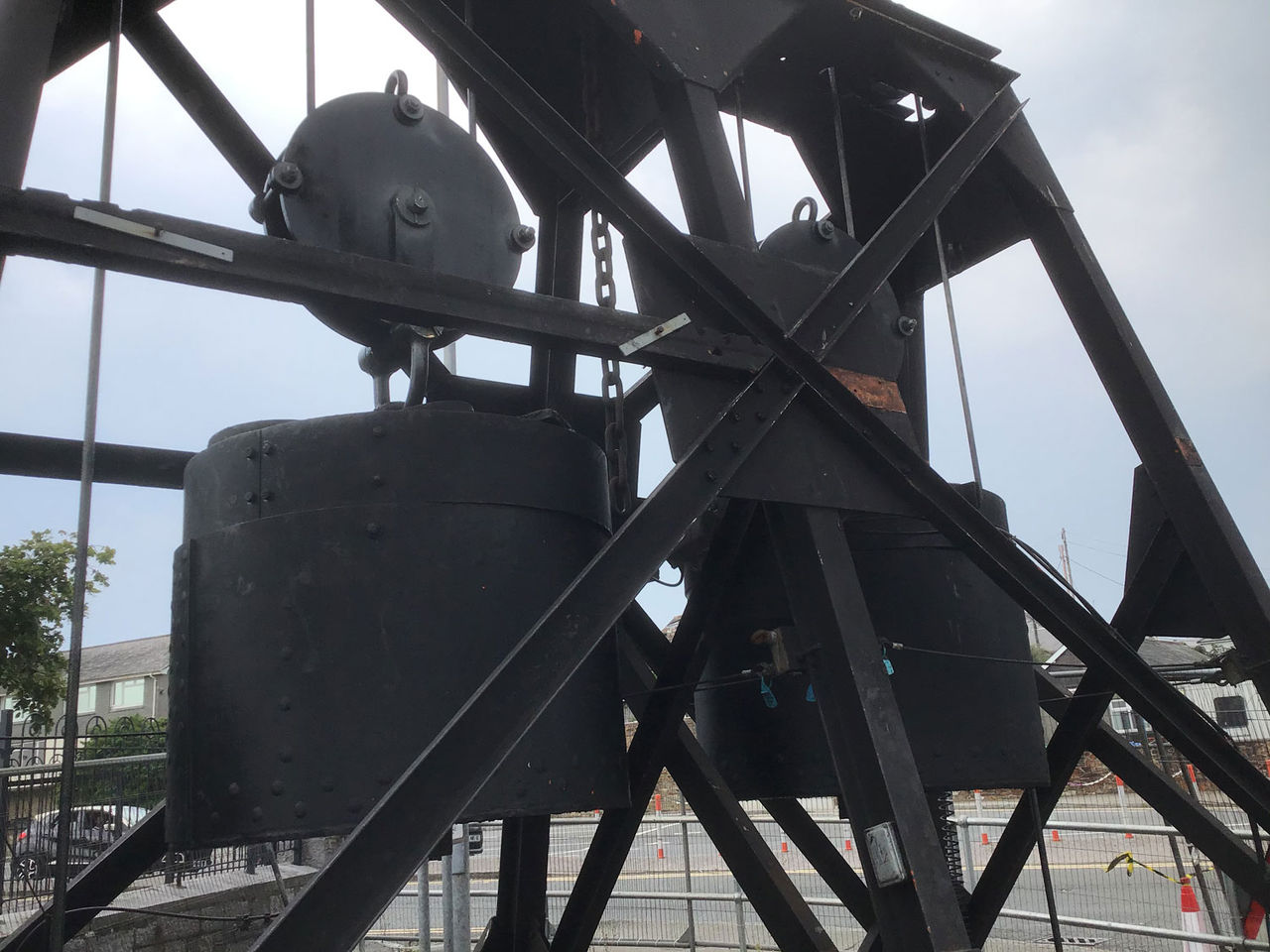
Gantry sheave in-situ
With an investigation complete, and the proposal agreed and signed-off by the customer, the Plymouth Service Centre and ERIKS Power Transmission Projects teams devised a corrective action plan that would see the redesign of the current blueprints.
With very little to go on, it was time to put our in-house engineering knowledge into action.
Utilising limited samples, with no formal load calculation or FEA (Finite Element Analysis) available, ERIKS CAD Specialists entered into deeper consultations with the customers engineers, creating a new set of design blueprints that would see the original rope design format reinstated, while remaining fit-for-purpose with the current infrastructure. Once complete, these were quickly approved and signed-off by the customer.
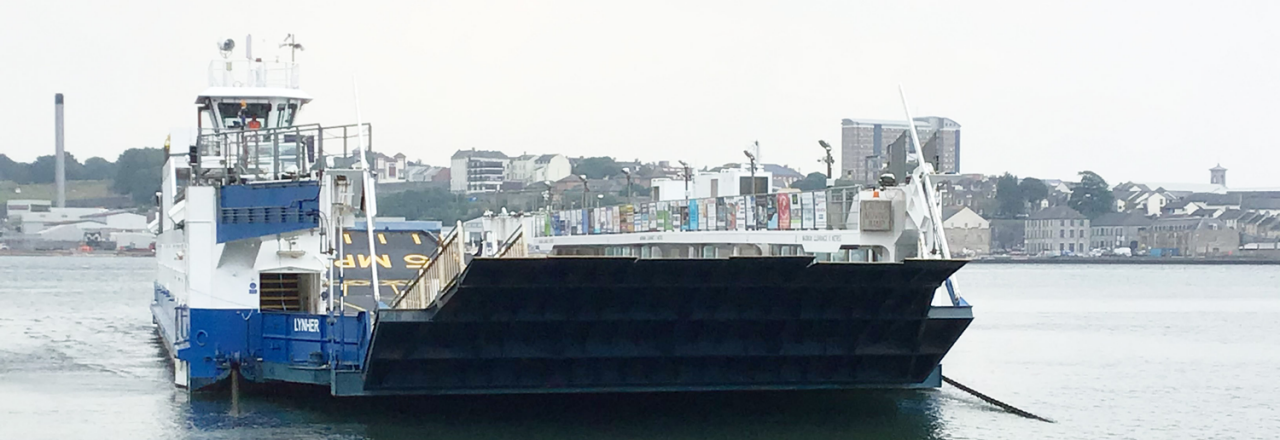
With an off-the-shelf solution not an option, the team compiled a list of essential components required to begin the complex rebuild of each gantry sheave, before designing, configuring, manufacturing and supplying all the listed parts, many from scratch, drawing upon ERIKS’ strong supply network and engineering skills to deliver the components in a short timescale.
All relevant risk assessments were then completed, before the sheaves were removed, collected, checked, and transported to the ERIKS Plymouth Service Centre, where strip-down and inspection commenced, along with measurements taken and recorded.
The engineering work got underway, with the detailed scope of the project including: in total 12—off various sheave assemblies designed, drawn and manufactured, comprising of shafts, SAE phosphor bronze bushes and thrust plates, shrouds, pivot arms, and HD bolts. In addition, special heavy-duty Dee and Bow shackles were designed and manufactured, which would all work together as one fluid mechanism to provide complete control and balance of the vessel as it glides across the water.
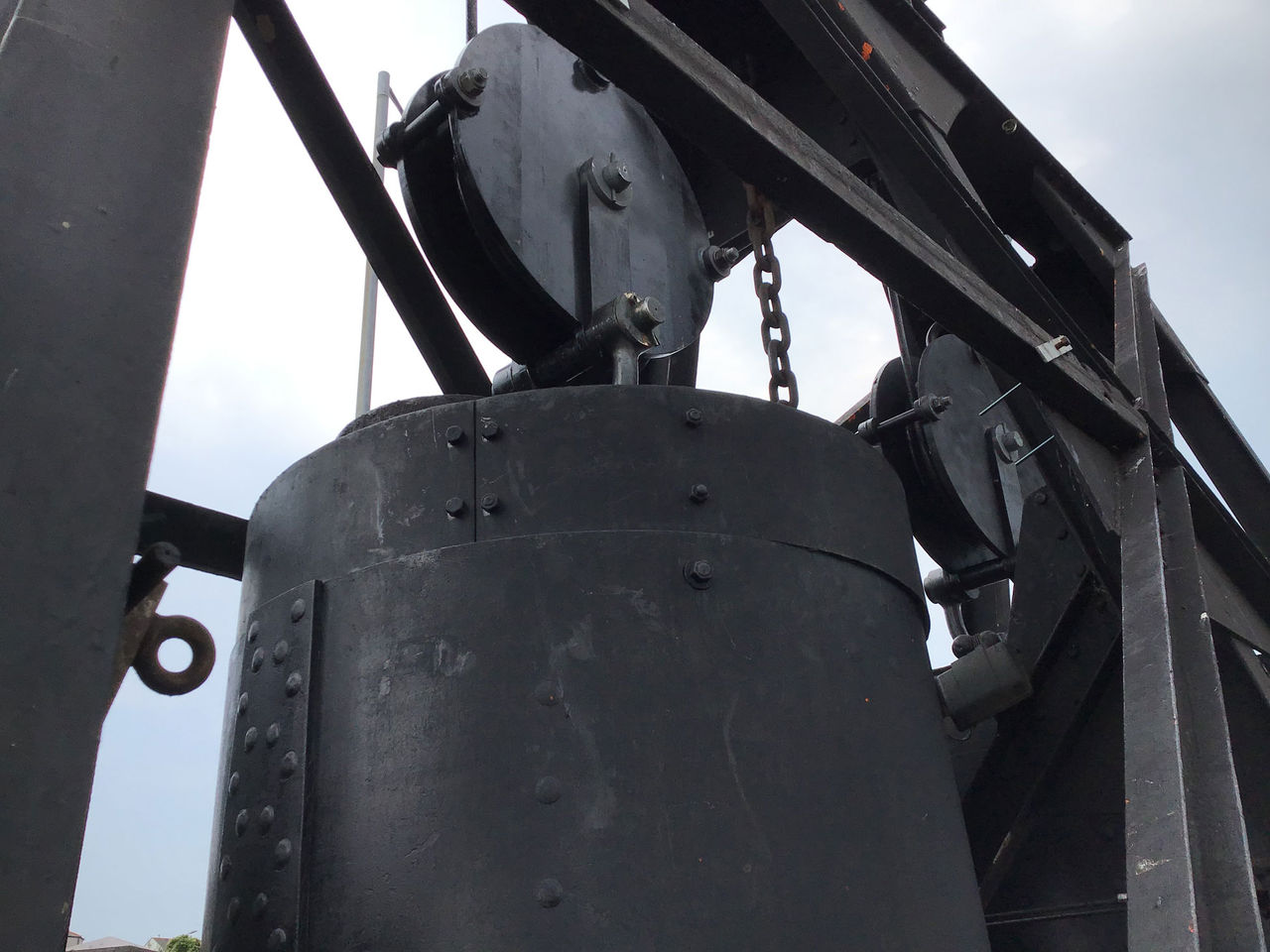
Imagine a zip line, connected to either end of the crossing, which runs directly through the boat, keeping it on course by tensioning at each end. This new installation design would ensure that the vessel does not deviate from its running course, which is essential given that tides changes dependent on weather conditions, and as previously pointed out, this service was in constant operation throughout the entire year, from the nicest summers to the coldest, wettest winters.
The configuration and support of the sheave mechanism also had a number of components in a confined space location, permanently located and fitted on-site, which required on-site machining to be organised and conducted, as well as the use of specialist mobile machining equipment, all facilitated by the ERIKS Power Transmission Projects team.
Result
With all engineering work completed, to the joys of the terminal management team and local community, the new sheaves and pulleys were transported back to site before being re-installed and commissioned. Service had been returned to full capacity, significantly reducing the current delays.
Following the re-installation of the gantries, a representative of the terminal management team commented: “Now we have completed the commissioning and installation of the gantries, we have achieved what I thought was impossible during lockdown."
“I wish to express my gratitude for the service that ERIKS has provided during a very challenging time throughout the COVID-19 outbreak and lockdown. The ERIKS team played an integral part in providing total support and technical advice, with guidance and on-site support which was second-to-none.”
From enquiry to back-in-service took approximately five and a half months, which was a great achievement given the initial fears that the terminal would be decommissioned for up to a full year.
Given the scale of the project, coupled with unforeseen and ever-changing implications of the COVID-19 pandemic, this was an excellent result for the customer, who saw their revenue losses cut by a monumental £2,239,440.
It just goes to show that having access to the right people, the right skill sets, and the right supply connections, that anything is possible, regardless of what challenges are pushed in your path.
In Summary:
With severe commuter delays and distruption to the local community, a complex sheave redesign, from scratch, was required to recommission a public ferry terminal.
By utilising ERIKS’ engineering expertise, CAD design capabilties, and strong supply network, the customer cut their forecasted revenue losses by 7 months, totalling £2,239,440.
- £2,239,440 in potential lost revenue recovered
- Project completed seven months earlier than forecasted
- Normal service resumed with severe disruptions eliminated
- Public safety ensured with efficient, bespoke design