In this article
Delivering significant savings on a tray
How one new pump washed problems away
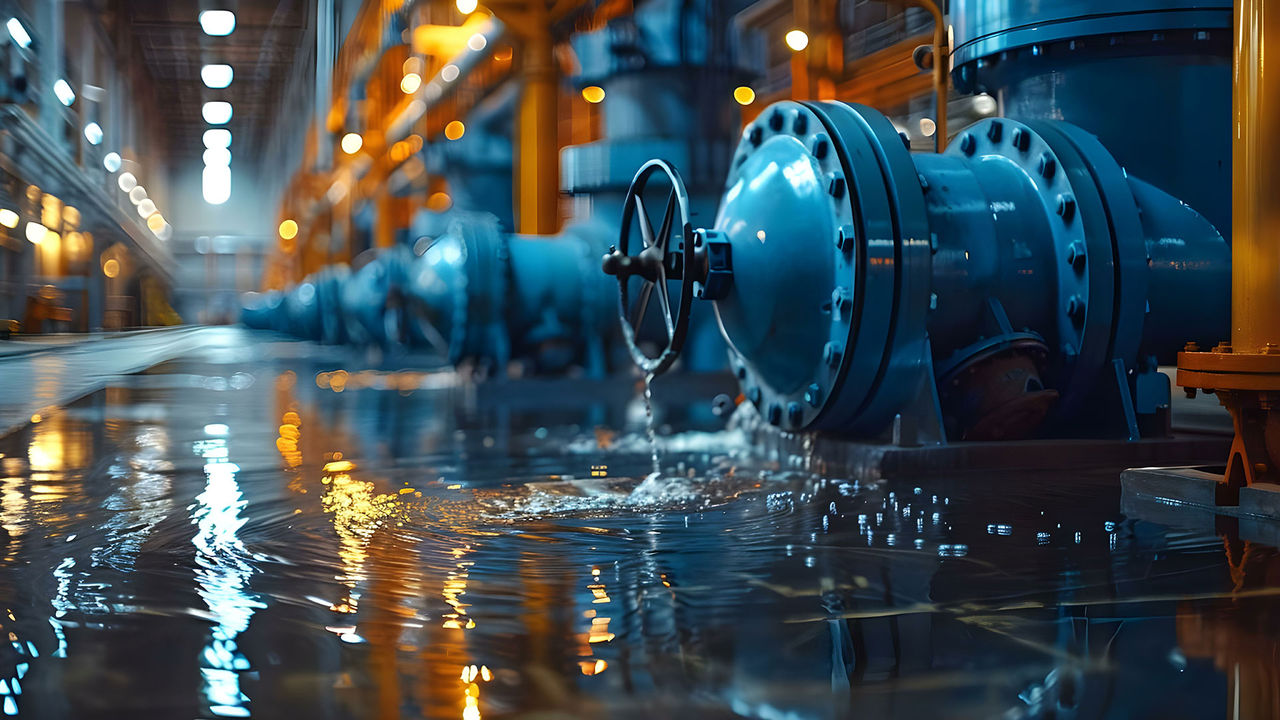
Industry Sector:
Food & Beverage
Application:
Tray Wash
Actual Saving:
£20,995
Payback period:
Immediate
Product/Service:
- Pumps
- Problem solving
Customer Benefits:
- Cost savings
- Reduced downtime
- Increased productivity
If a failure mode is repeated just once, it’s an issue. If it repeats itself eight times, it’s a major problem.
After replacing the same pump, for the same reason, eight times in a twelve-month period, a major meat processor realised it was time to ask ERIKS to get their teeth into the problem. It didn’t take long for an ERIKS Application Engineer to identify the cause of failure and propose a cost-effective solution.
Challenge
The repeatedly failing pump operated in the wet and messy environment of the meat processor's tray wash area. This is where trays used to transport meat are washed-down with chemicals to ensure they meet the required food hygiene standards before being returned to use.
In just one twelve-month period, the pump suffered no fewer than eight failures – and failed to the extent that it had to be replaced, rather than repaired. At a cost of £3,200 per pump, that was a lot of unnecessary expenditure for the customer to have on their plate.
It was down to ERIKS to find out not only what was causing the repeated pump failures, but also to propose a cost-effective solution to prevent them from continuing. The ERIKS Application Engineer quickly spotted a combination of related issues.
Firstly, the washdown chemicals were causing corrosion of the pump. Although it was covered, and protected from the worst of the washdown, the pump had not been specified to be resistant to the washdown chemicals, owing to the perceived cost.
In addition, the mounting position of the pump allowed it to flood if the sump wasn’t fully pumped out, leading to electrical failure. And lastly, air becoming trapped in the seal was causing the pump to run dry – also leading to pump failure.
Solution
As a distributor rather than a manufacturer, ERIKS has a neutral repair/replace approach. So the ERIKS Application Engineer was able to propose the most effective solution for the job, rather than look for a quick or easy sale.
Addressing the chemical corrosion first, the engineer recommended a pump manufactured from 316 stainless steel for the volute casing, impeller and shaft. To prevent air becoming trapped in the seal - which was causing the pump to run dry - a flexible bellows mechanical seal, incorporating silicon EPDM elastomers, was specified. This seal also features vent pipes to allow air to be released before priming.
And lastly, in a simple but effective fix, the choice of a vertically-mounted pump model - the Apex TC 50- 200 15/2 - was advised, to ensure it wouldn’t flood even if the sump wasn’t drained.
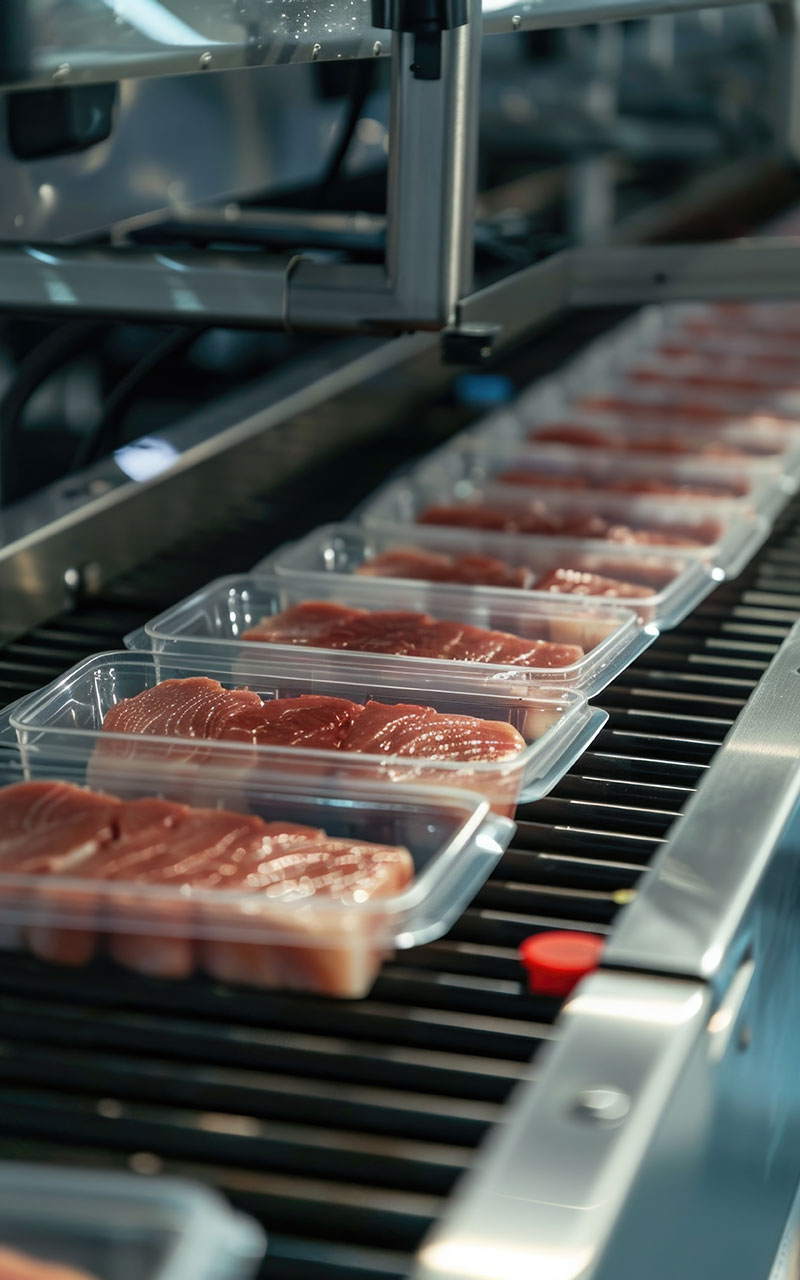
Meat being transported along conveyor belt
Result
Once approved by the customer, the newly-specified pump was duly installed. Although the new pump cost £4,645 more than the one it has replaced, it has now been running for ten months with no issues and no failures.
So by avoiding the replacement costs of eight pumps, the customer has already saved no less than £20,995 – on top of the downtime and labour cost savings from avoiding repeated pump failures.
Not surprisingly, the meat processing customer has no beef with ERIKS’ solution.
