In this article
Cutting energy costs with an air knife
ERIKS engineers have their fingers on the pulse valve
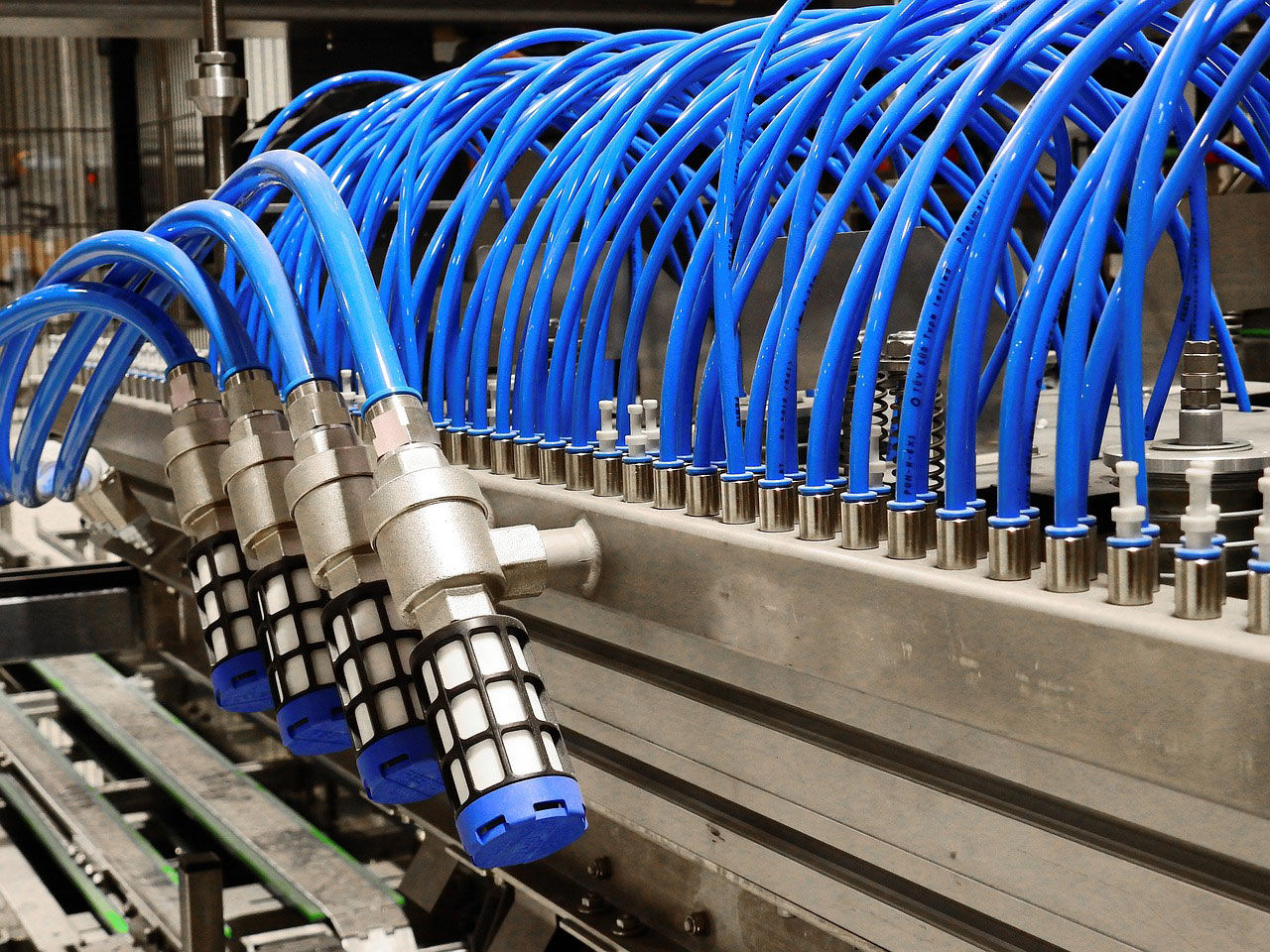
Industry Sector:
Food & Beverage
Application:
Carton erector
Actual Saving:
£49,000 p.a.
Payback period:
3 Weeks
Product/Service:
- Self-acting pulse valve
Customer Benefits:
- Reduced TCO
- Energy efficiency
- Environmental compliance
Because compressed air is invisible, its role in energy consumption is often overlooked. Yet compressed air systems are used to operate a huge variety of process and packaging equipment throughout a wide range of industry sectors. And the cost of generating the compressed air to supply them is high.
That was the reason for the ERIKS’ pneumatic products roadshow organised by the ERIKS On-Site Technical Benefits Team at a customer’s location. This team is tasked with finding savings for customers without affecting productivity – and ideally while improving it.
Using the roadshow to highlight energy-saving products to the customer’s engineering team, the intention was to stimulate new ideas to cut energy use and costs associated with compressed air.
Challenge
Following the roadshow, the customer identified an application in their packing process which had the potential for a reduction in energy consumption.
Compressed air-powered air knives are used to blow open flat boxes, prior to packing with product. The knives run continually and the compressed air is pumped directly into the environment during use. The compressors also run continually, so the wastage of compressed air – and the energy cost of its production – are both high.
To establish a baseline for cost savings, during a production shutdown ERIKS Value Delivery Team installed a flow meter on the packing line. When the line was restarted, compressed air usage was measured at 1116.6LPM (litres per minute), which equates to 1607.9m3 /24hrs, and an energy bill of £9,229 p.a.
Across the customer’s six packing lines, based on annual run times, the total cost of the air knife process was calculated at around £61,000 p.a.
This not only represents a significant portion of the factory’s energy budget, but also has an impact on the cost per kilo of the product being packed.
Solution
After reviewing the process, ERIKS’ engineers used their application know-how to identify a possible energy- and cost-saving solution.
Rather than allowing the air knives to use compressed air continually, by fitting selfacting pulse valves the flow of compressed air could be stopped and started at a rate of 3Hz. This would be indistinguishable from a continual flow of air at end use, but would significantly reduce compressed air consumption, and allow the compressors to run at a slower rate.
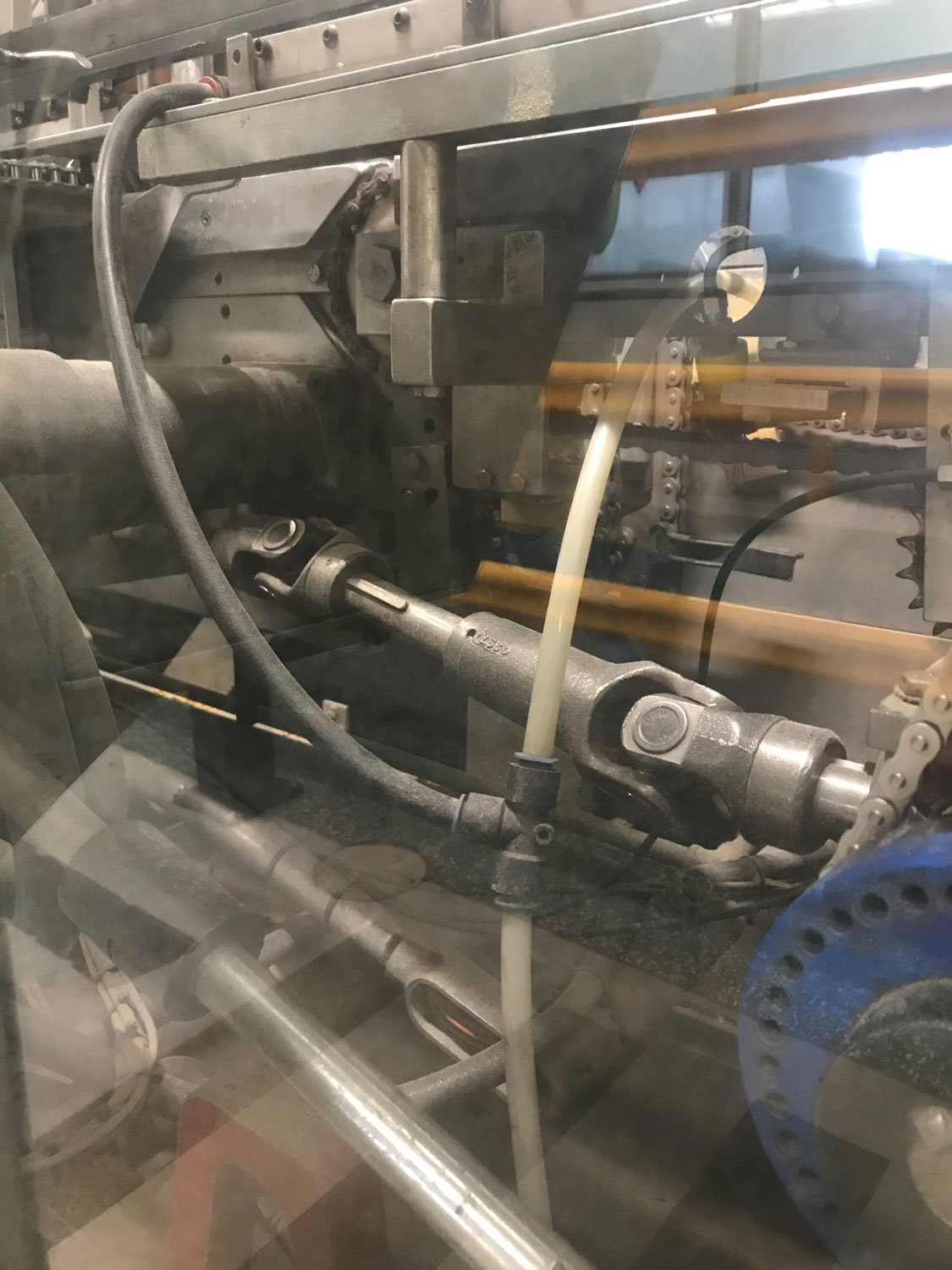
Application with Air Knife in-situ
Result
A trial installation of the pulse valve on the packing line with the flow meter already fitted, showed compressed air usage of just 215.1LPM, or 309.7m3 /24hrs. This would represent an annual energy bill of just £1,778p.a.
The reduction in energy use during the trial convinced the customer to extend the pulse valve solution to all six packing lines. This has reduced energy costs from £61,000 p.a. to £12,000 p.a. CO2 emissions have also been reduced, due to slower running of the compressors.
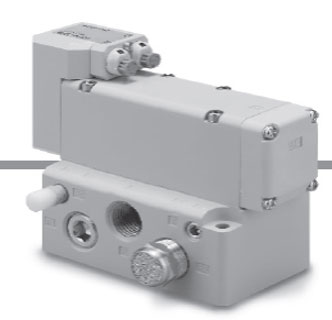
Air knife pulse valve
The simplicity and low cost of the pulse valve solution means that the payback period was just three weeks. If you want such sizeable savings, so quickly, you can trust ERIKS to pull them out of the air.