In this article
The overlooked factors in hand protection
In the manufacturing sector, every facility adheres to and recognises strict safety protocols and standard operating procedures to minimise hazards, with PPE practices central to protecting employees. Yet, it’s essential to periodically reassess PPE, especially hand protection, to address overlooked factors that contribute to a safer, more productive workplace.
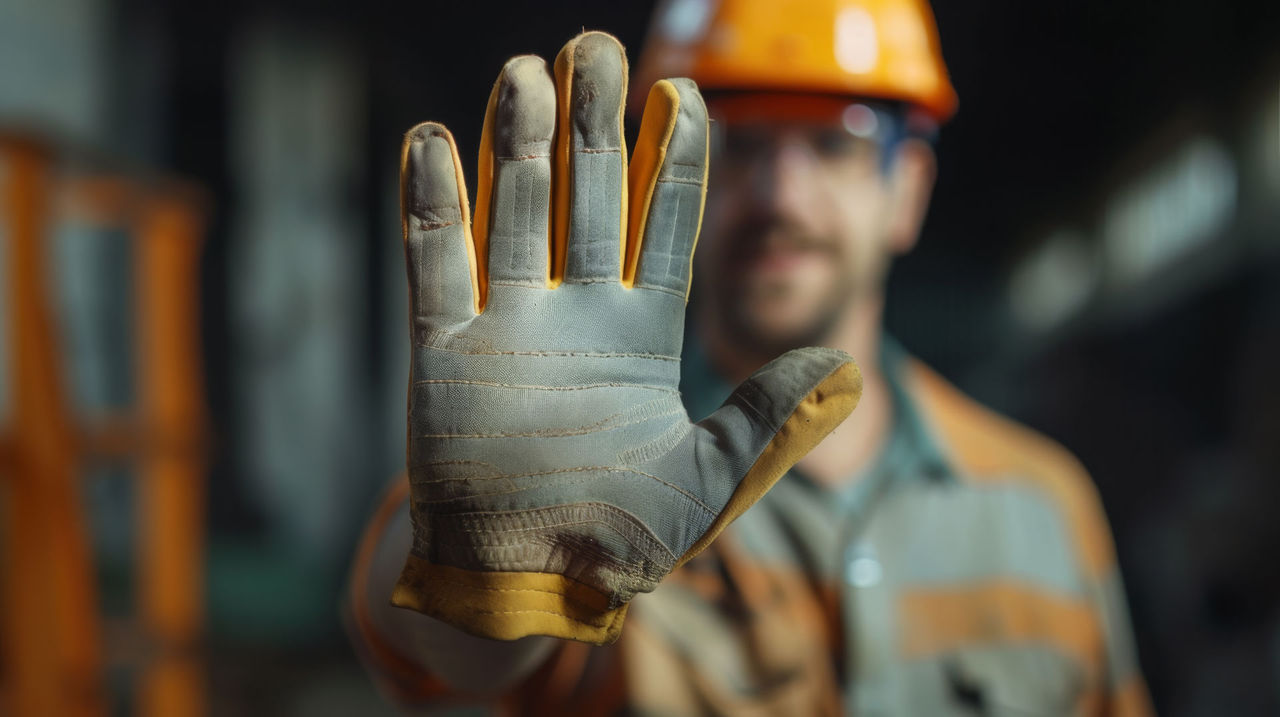
With the rapid evolution of manufacturing technology and regulatory requirements, industries face an ever changing landscape. This evolution includes heightened standards for both general safety and industry specific needs. However, secondary hazards are often neglected after addressing the primary risk, and mitigating these risks can play critical roles in injury prevention.
Hand Protection: Addressing Complex Hazards
Hands are a primary tool in manufacturing but remain highly vulnerable to injury. In the UK, hand and wrist injuries remain a significant concern in the workplace.
According to the most recent data from the Health and Safety Executive (HSE) for 2022-2023, there were 561,000 non-fatal injuries reported, covering all types of workplace injuries.
Within this figure, 60,645 injuries were reported by employers under the Reporting of Injuries, Diseases and Dangerous Occurrences Regulations (RIDDOR), highlighting more severe cases.
Common causes included slips, trips, and falls, along with handling or carrying injuries, which often affect the hands and wrists (HSE Nonfatal injuries at work in Great Britain).
Despite advancements in hand protection, each workplace presents unique hand related hazards that require solutions tailored to the specific environment and use. Choosing gloves based only on primary features, such as cut resistance, often compromises essential qualities like dexterity and grip, which can lead to secondary injuries.
In manufacturing environments, inadequate dexterity can contribute to dropped tools and missteps, increasing the risk of additional injuries.
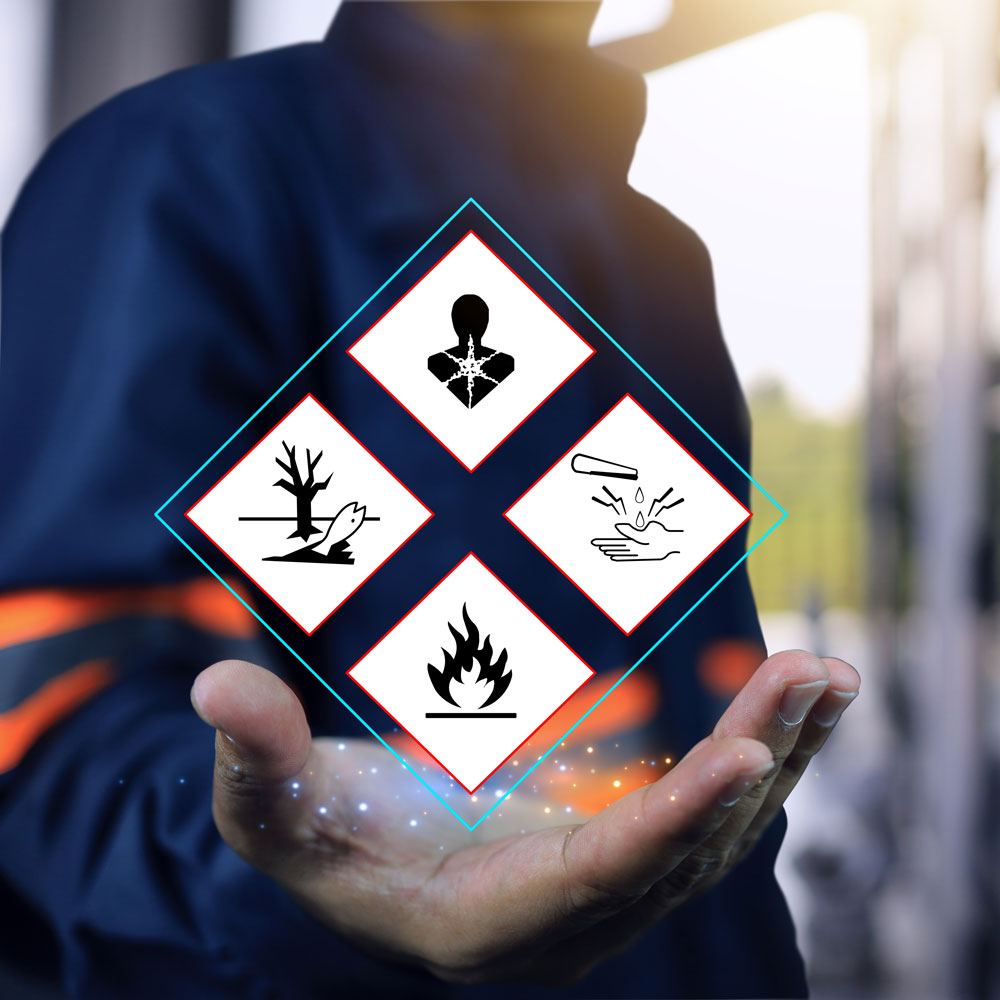
Importance of Dexterity and Grip
In settings where hand protection is vital, the need for a secure grip is often overlooked. Ambient conditions, tool surfaces, and the presence of moisture or grease can drastically impact grip, especially in high-risk areas. Enhanced dexterity and grip allow workers to maintain control, reducing incidents and/or over grip fatigue.
Shockingly, a significant proportion of hand injuries occur when workers are not wearing gloves. We believe the common reasons workers do not wear hand protection, includes gloves being too thick, uncomfortable, or not suited for environmental conditions. The challenge is selecting gloves that not only protects against hazards but protects without sacrificing comfort and usability.
To address the need for sustainable, high-performance hand protection, Polyco Healthline introduces the enhanced Polyflex Ultra. Built to withstand challenging environments, this glove offers superior grip in wet and oily conditions and achieves a Level 4 abrasion resistance under EN 388:2016 + A1 2018. Its durable foamed nitrile coating ensures a secure grip and long lasting wear, making it ideal for a variety of manufacturing tasks.
Environmental Responsibility Meets Performance
Polyflex Ultra aligns with Polyco Healthline’s #phAMBITION, incorporating a liner made from 91% recycled nylon, which makes up 48% of the glove’s total weight.
This innovation reduces reliance on virgin materials, reflecting Polyco Healthline’s commitment to sustainability without compromising safety standards or product performance.
As industries advance, protecting the workforce requires attention to details beyond primary safety standards. Polyflex Ultra embodies this approach by addressing crucial aspects like grip, durability, and environmental responsibility, reinforcing safety and efficiency.
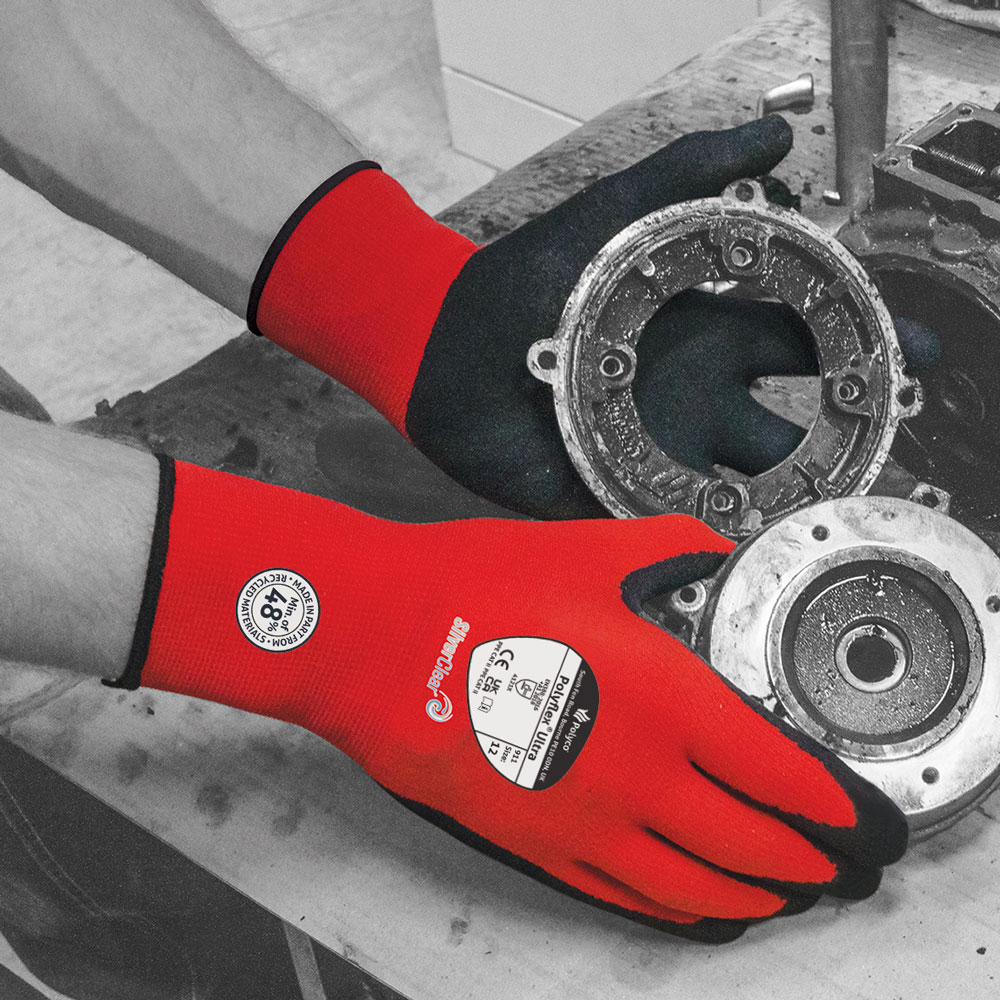
For more information on Safety Equipment, contact your local ERIKS Service Centre, who will be happy to discuss your options.
#PolycoHealthline #ERIKS #LetsMakeIndustryWorkBetter #PPE #HandProtection #Polyflex