In this article
Saving time, cutting costs and reducing electrical risks can be shockingly easy
Maintenance engineers have no time to waste. So an electrical safety testing solution which takes almost no time at all – and saves them hours – is too good to miss out on. If it also saves over £100,000 on the cost of maintenance, downtime and lost production, then ignoring it would be shocking. No wonder British Gypsum were quickly switched on to the solution.
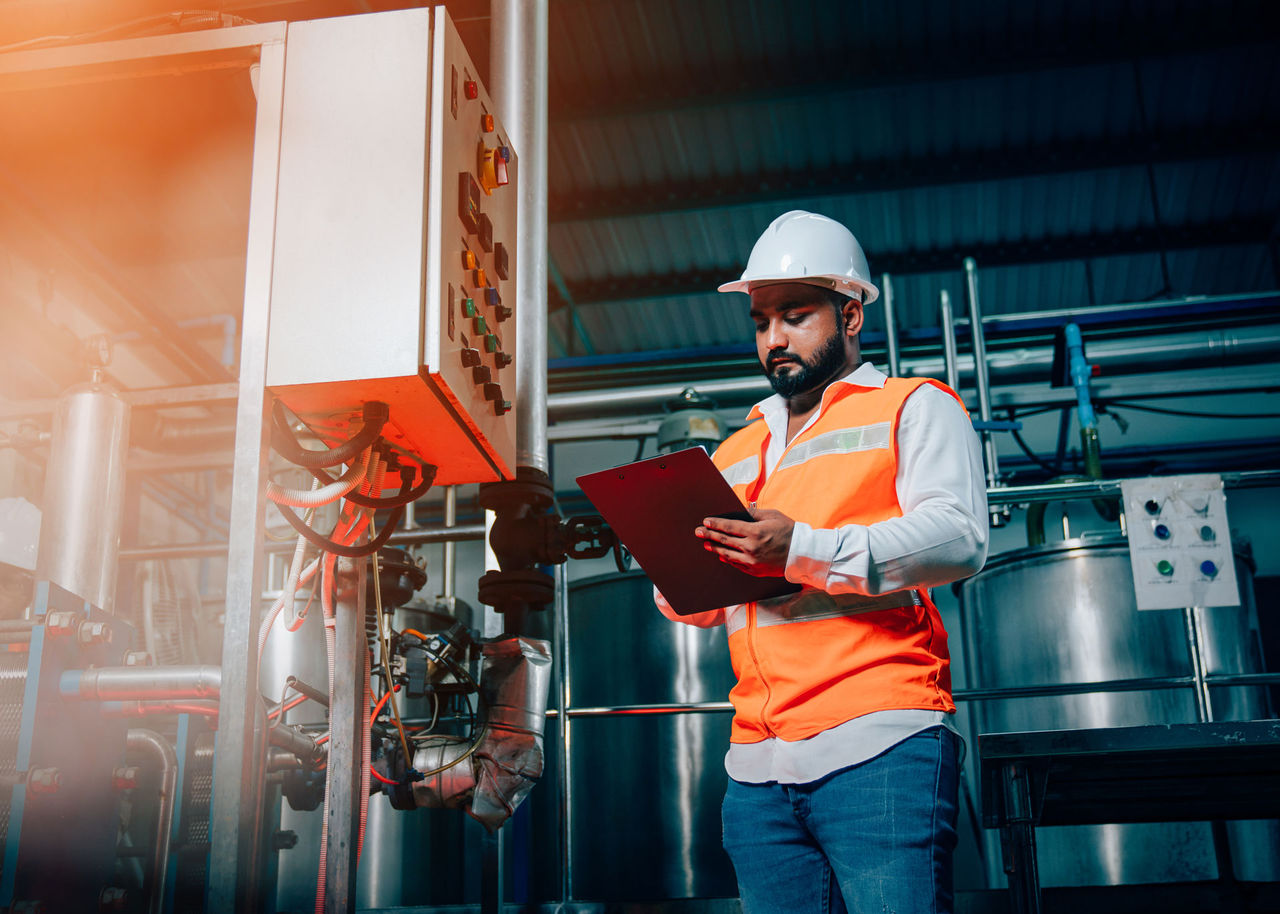
Regular and frequent predictive maintenance tests of electrical panels is the most effective way to maintain the efficiency of manufacturing equipment. But with dozens of panels across their sites in East Leake, Notts., and Robertsbridge, East Sussex, British Gypsum were experiencing excessive downtime for maintenance such as thermographic testing.
Before any maintenance can be carried out, the panels have to be disconnected from the power source, and have their absence of voltage verified. Disconnection is relatively quick and easy, but the traditional method of verifying absence of voltage is slow, complex, and open to error, complacency and risk.
Dressed to test
When using a portable, handheld, voltage test instrument, before an engineer can even start the verification process they have to don PPE – which takes time in itself. But even dressed appropriately, the risks are not completely removed.
If the instrument has a mechanical or electrical failure, or isn’t used correctly, it could give a false result. Even the testing procedure is a risk to the user if voltage is present. Then, once the test has finally been completed correctly and successfully, there’s more time wasted in taking off and storing the PPE.
Throughout the testing of the tester itself, the voltage checking and the retesting, the operator is potentially exposed to electrical hazards. And all this time, the asset is out of action. So the only thing it’s manufacturing is more costs.
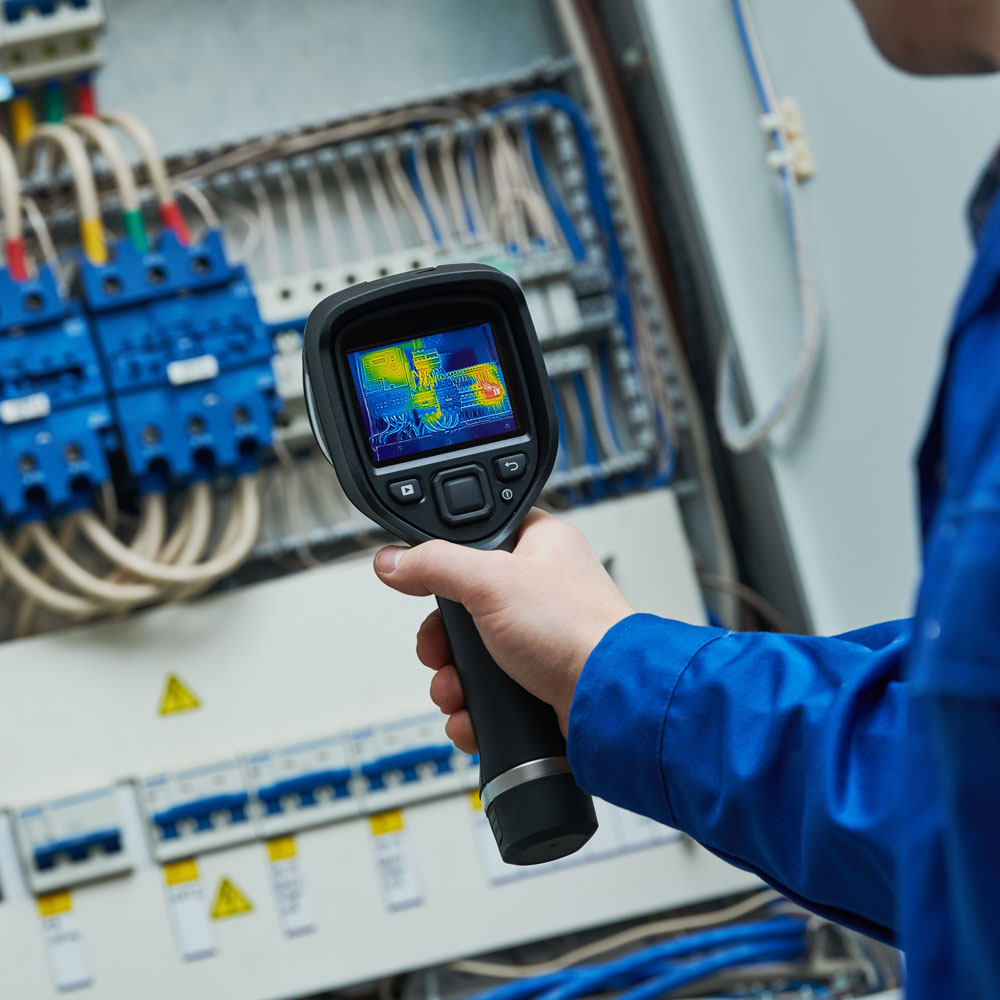
A solution in seconds
Of course the answer can never be to take shortcuts or risks. But it can be to do the same testing in less time, with more convenience and even greater safety.
British Gypsum did take a shortcut of sorts – because they knew that ERIKS had the know-how they needed. And when an ERIKS electrical safety expert suggested the automated Panduit VeriSafe™ Absence of Voltage Tester (AVT), they knew they had the answer they needed too.
The VeriSafe™ AVT is the first AVT tailored for electrical enclosures. By simplifying and automating the voltage verification process, it shortens the procedure to a matter of seconds, while maintaining absolute operator safety.
Using the VeriSafe™ AVT, all the engineer needs to do is activate the automated tester, note the indicator status and – if a green indicator is illuminated – open the enclosure to start work. There’s no direct exposure to electrical hazards. And the voltage status is established before equipment is accessed.
It takes just seconds, and puts safety first.
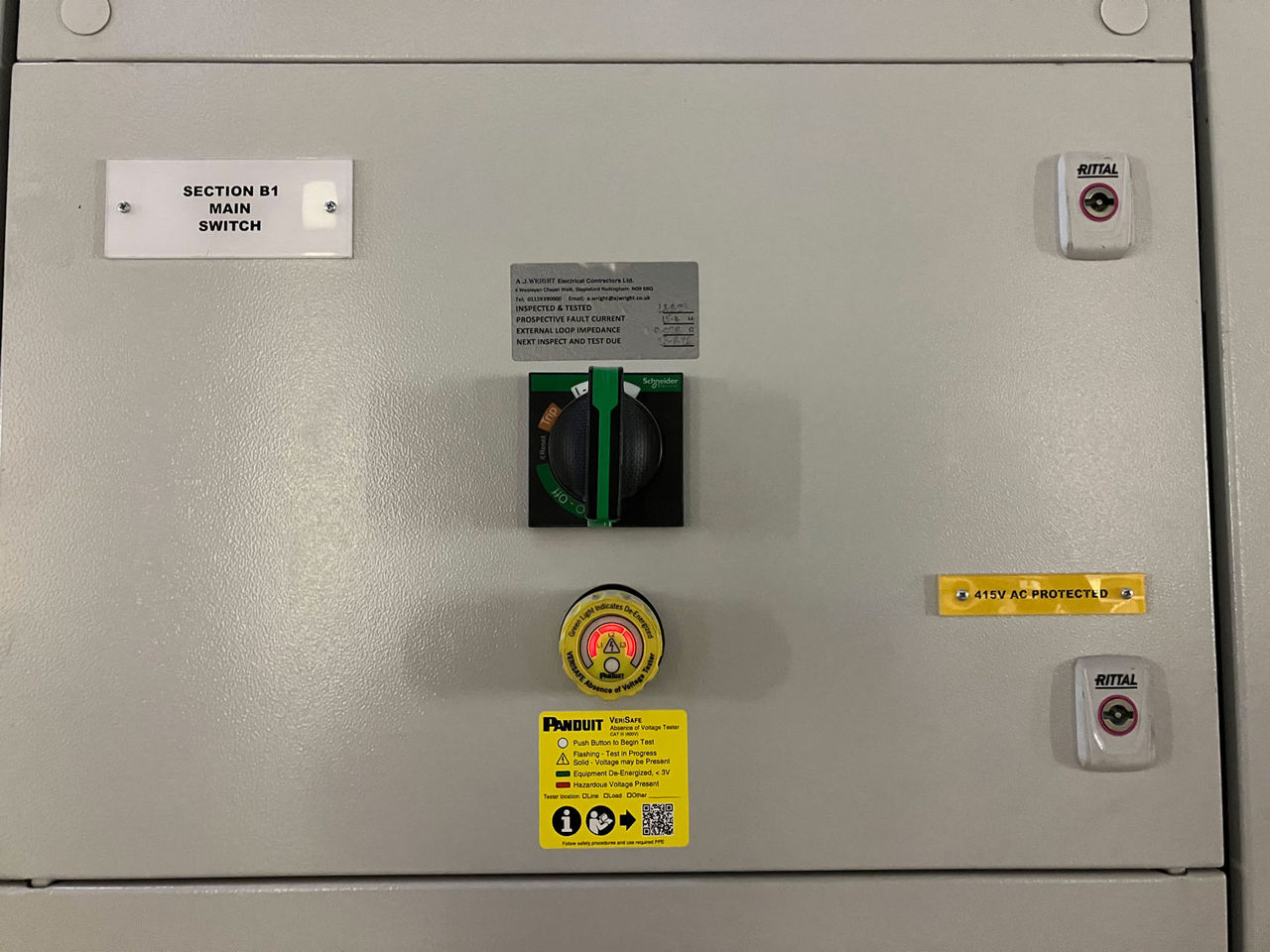
In fact the amount of time which the VeriSafe™ AVT could save them on testing was so great, British Gypsum couldn’t believe it. So ERIKS and Panduit not only provided an initial demonstration using a test rig, but followed it up with a VeriSafe™ installation on a number of electrical panels in a trial area at one of the customer’s sites.
Shocked – in a good way
Once the trial was completed, British Gypsum were completely convinced.
So convinced, that they have since installed over 103 Panduit VeriSafe™ AVTs at their Nottinghamshire site, 50 at their East Sussex site and another 20 at their site in Leeds. The resulting savings on maintenance time, downtime and lost production have been calculated by the customer as £121,298.
But it’s not only the financial savings that have shocked them. Their maintenance engineers are now spending around half as much time on voltage testing and Lock Out Tag Out safety procedures. Which means they have more time to spare for more productive maintenance tasks which can enhance operational efficiency and productivity.
It’s not often you can find a solution to a maintenance issue that’s very safe, very efficient and very cost-effective. But Panduit have one – and they’ve just called it VeriSafe™ for short.
For more information on Safety solutions, please contact your local ERIKS Service Centre, who will be happy to discuss your options.
#Panduit #ERIKS #LetsMakeIndustryWorkBetter #PanduitVerisafe #Verisafe #Voltage #VoltageSafety #VoltageVerifying #ElectricalSafety