In this article
For protection in aggressive environments, choose a good coat
A good coat of a LOCTITE formulation with special fillers – designed for challenging conditions – will help you make large-scale repairs that last longer. Even in the toughest environments.
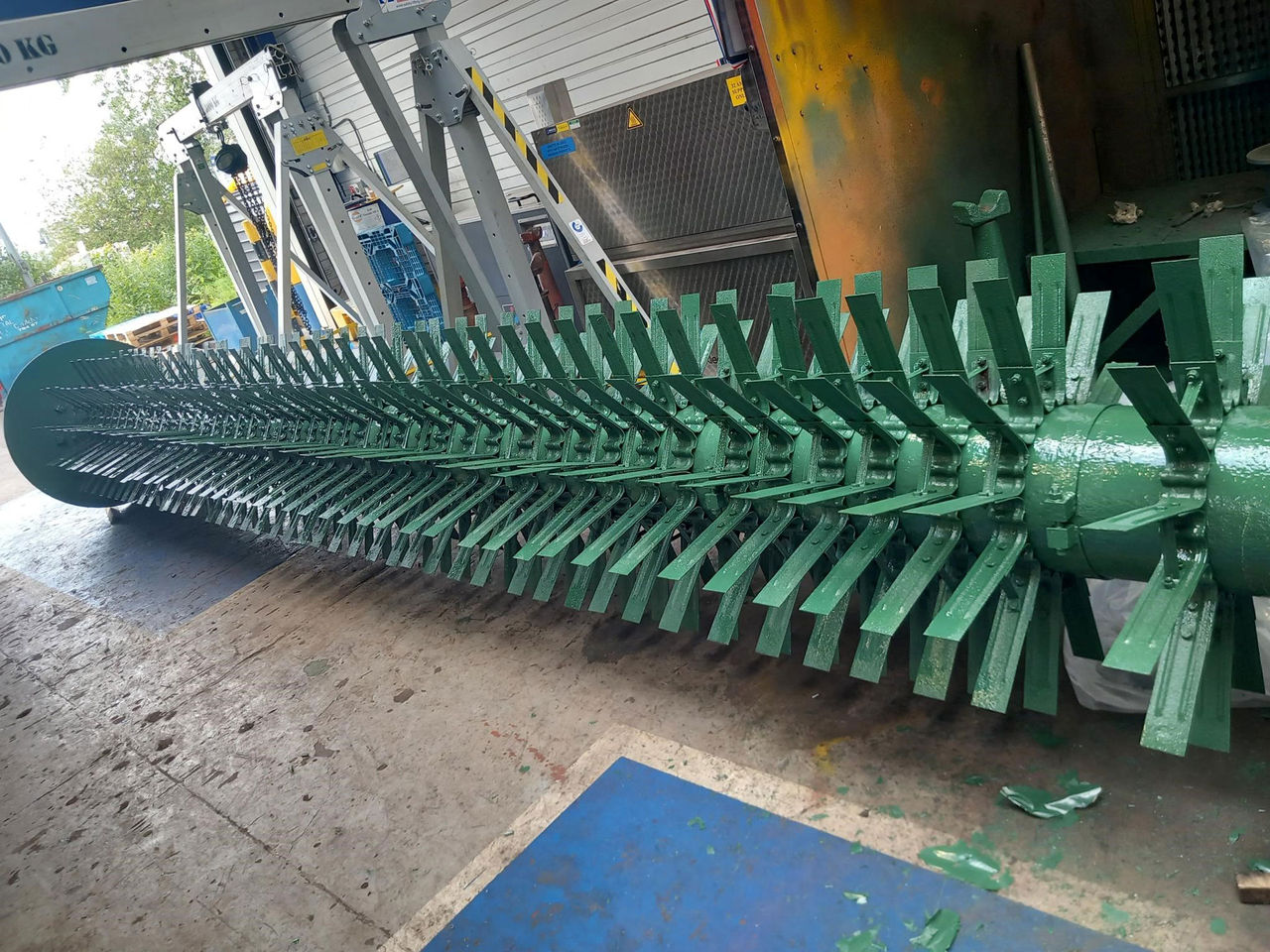
Whether it’s wear, abrasion, erosion, chemical attacks or corrosion, LOCTITE protective coatings and compounds are the maintenance solution you need. Filled with ceramic particles tailored to different service conditions, they provide superior adhesion, resist wear, protect against abrasion, and extend equipment service life.
And because they create a sacrificial, renewable working surface, they protect the original substrate too.
Making life smoother
LOCTITE’s protective coatings can be trowelled, brushed or sprayed on, to create an exceptionally smooth surface.
One that helps key components – air ducts, pumps, heat exchangers, centrifuges, impellers, pipes, tanks and more – to last longer and operate more efficiently.
The coatings are easy to apply even on large surfaces, where traditional hard metal welding or flame spraying can be expensive and difficult. So corrosion protection can be achieved with no heat stress during application.
Their special epoxy matrix enables the coatings and compounds to resist most types of chemical aggression – from fresh water to sea water, and ammonium sulphate to sodium hydroxide. Even stronger chemicals like sulphuric acid and urea are no problem for some LOCTITE products.
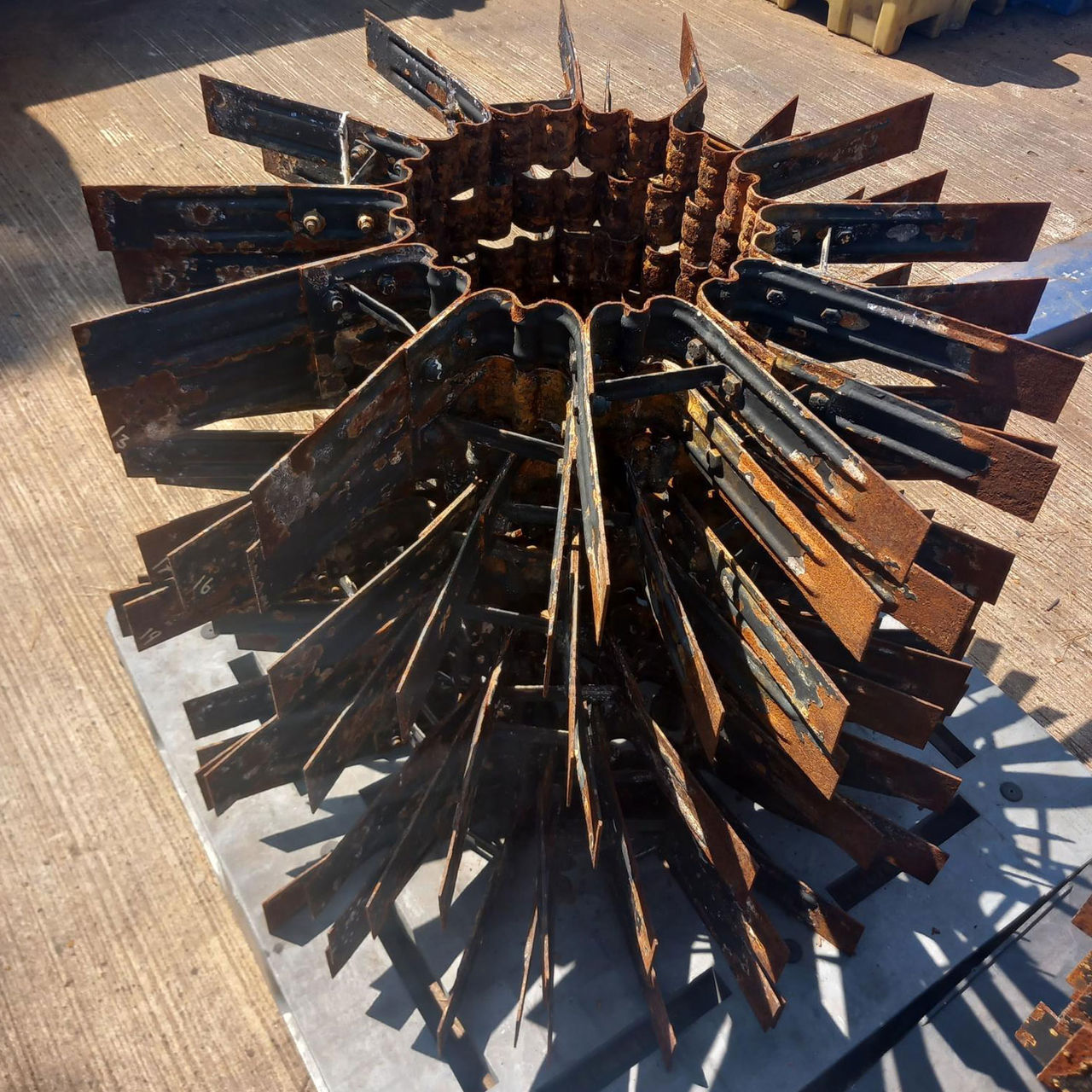
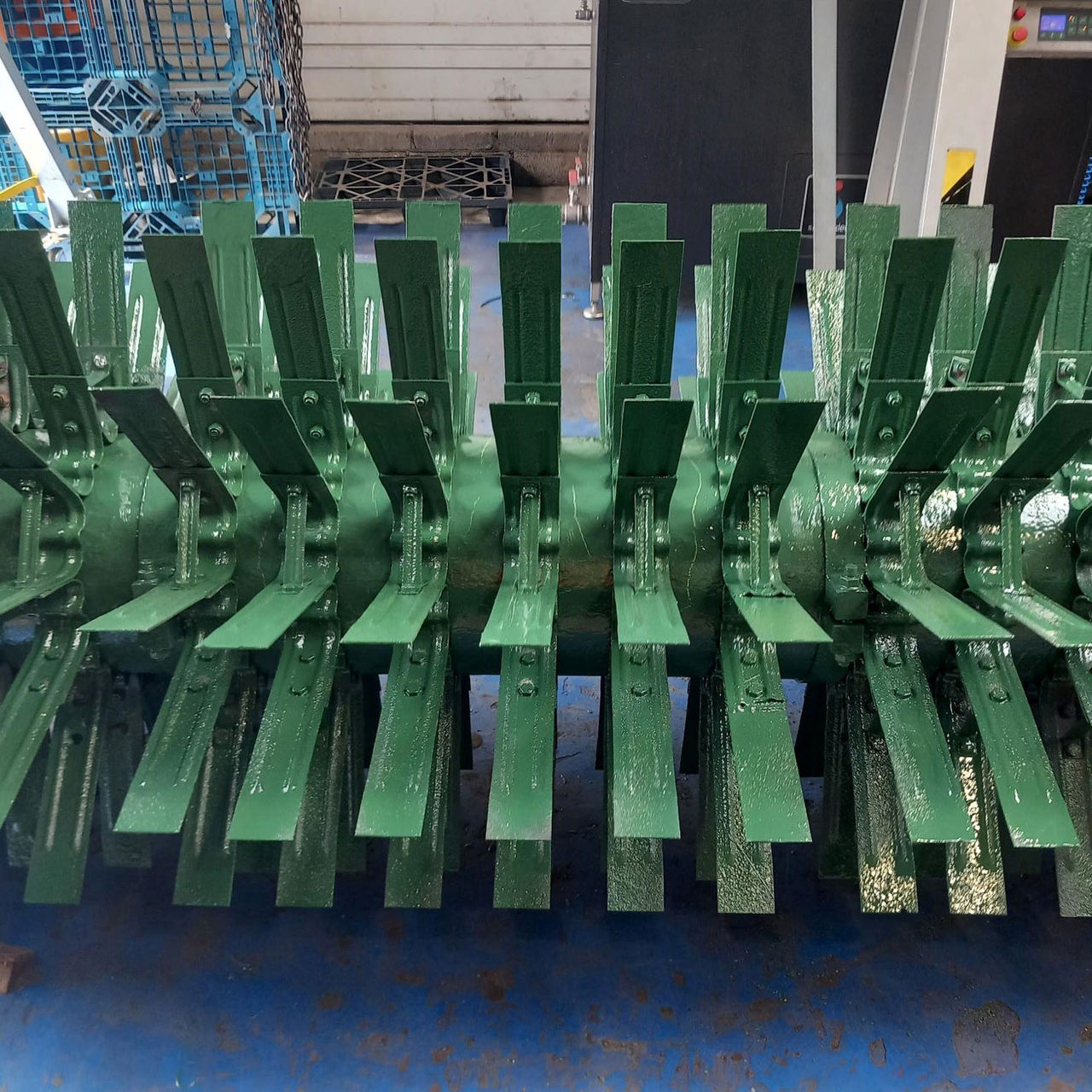
Repair more, stress less
LOCTITE protective coatings help you repair components for less than the cost of replacement, while still ensuring long-term protection.
That’s what a large water utility company discovered, when LOCTITE and ERIKS worked together to provide surface treatment and a protective coating for a water agitator.
The existing painted assembly was corroding and eroding in its harsh waste water environment. At ERIKS’ Cardiff workshop, the parts were cleaned and abraded to remove corrosion down to bare metal, then treated with LOCTITE SF 7515: a liquid surface treatment that gives 48-hour protection against flash rust on large surfaces.
After this pre-treatment, two coats of LOCTITE PC 7255 Green were applied and left to cure for 72 hours.
Thanks to LOCTITE and ERIKS, the surface treatment, coating, and training solution for the application saved the customer money, minimised waste, and maximised the part’s life expectancy. The sprayable protective coating also reduced the total repair time compared to the previous paint-on solution, which needed frequent maintenance.
So if you want to lengthen asset life, improve efficiency, and save costs, downtime and environmental impact, a LOCTITE coating is the answer. Just ask your usual ERIKS contact for more information.
For more information, contact your local ERIKS Service Centre, who will be happy to discuss your options.
#Henkel #Loctite #ERIKS #LetsMakeIndustryWorkBetter #AggressiveEnvironments #Maintenance