In this article
Sticking to food safety
Food and adhesives aren’t usually found together. At least, not on the same plate. But in the food and beverage industry, adhesive use is rapidly increasing, as manufacturers become aware of the benefits. However, like all products which may come into contact with food, adhesives in the sector are strictly regulated. Advice from Loctite on product selection can help ensure you don’t come unstuck.
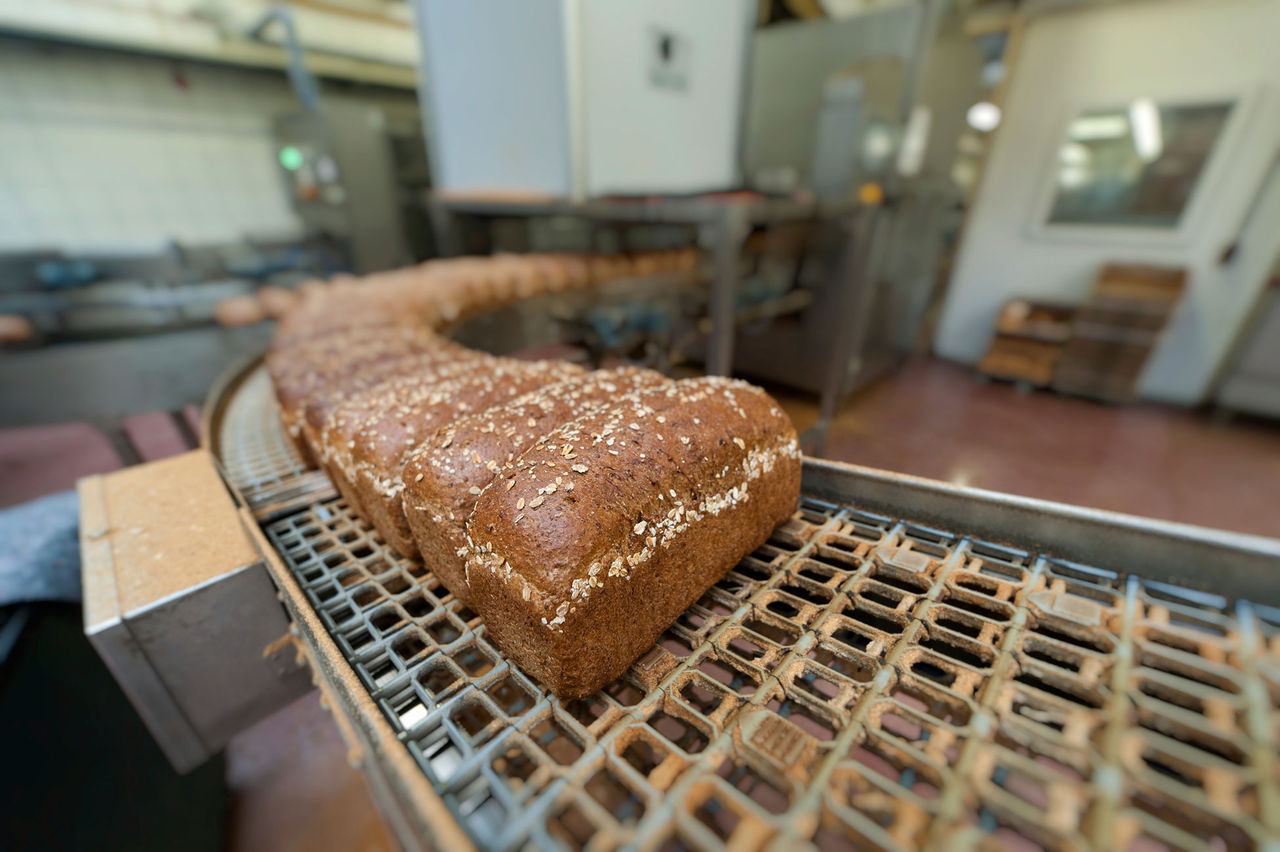
In the UK, the key regulating body for the use of adhesives is the Water Regulations Approval Scheme (WRAS). Internationally, the National Sanitation Foundation (NSF) and the Food & Drug Administration (FDA) are amongst the most important.
Avoid the wrath of WRAS
Acting as, effectively, the UK’s drinking water inspectorate, WRAS approval of adhesives and sealants certifies their safe use throughout the food and beverage industry. Using products that are not WRAS-approved can lead to serious consequences, including product contamination, costly compensation claims and damage to brand reputation.
Henkel currently has several ‘live’ WRAS approvals for its renowned LOCTITE® range available from ERIKS. These include thread sealants (LOCTITE 577, 542 and 5400), retaining compounds (LOCTITE 6300, 638 and 648), thread locking adhesives (LOCTITE 2700 and 2400), and gasket sealant (LOCTITE 5800).
WRAS-approved LOCTITE 2400 mediumstrength thread locking adhesive is ideal for applications such as food- and water-safe gearbox repair. The adhesive will prevent case bolts from loosening, seizure and corrosion, to help ensure reliable operation, long service life and minimal downtime. For gearboxes forming part of the power transmission for food and beverage processing, those can be crucial factors.
LOCTITE 2700 high-strength thread locker is also WRAS-approved, and suitable for mounting bolts in similar applications.
Safe choice
LOCTITE ‘white label’ products are another option suitable for the food sector.
This range of structural and flexible adhesives and sealants, instant adhesives, thread lockers, retainers, and liquid gaskets comes with a ‘white’ material safety data sheet. This means that users can be confident the products are fully tested, and contain no hazardous ingredients requiring COSHH assessments or hazard labelling.
They’re a quick and effective solution for many applications where food safety is the prime consideration.
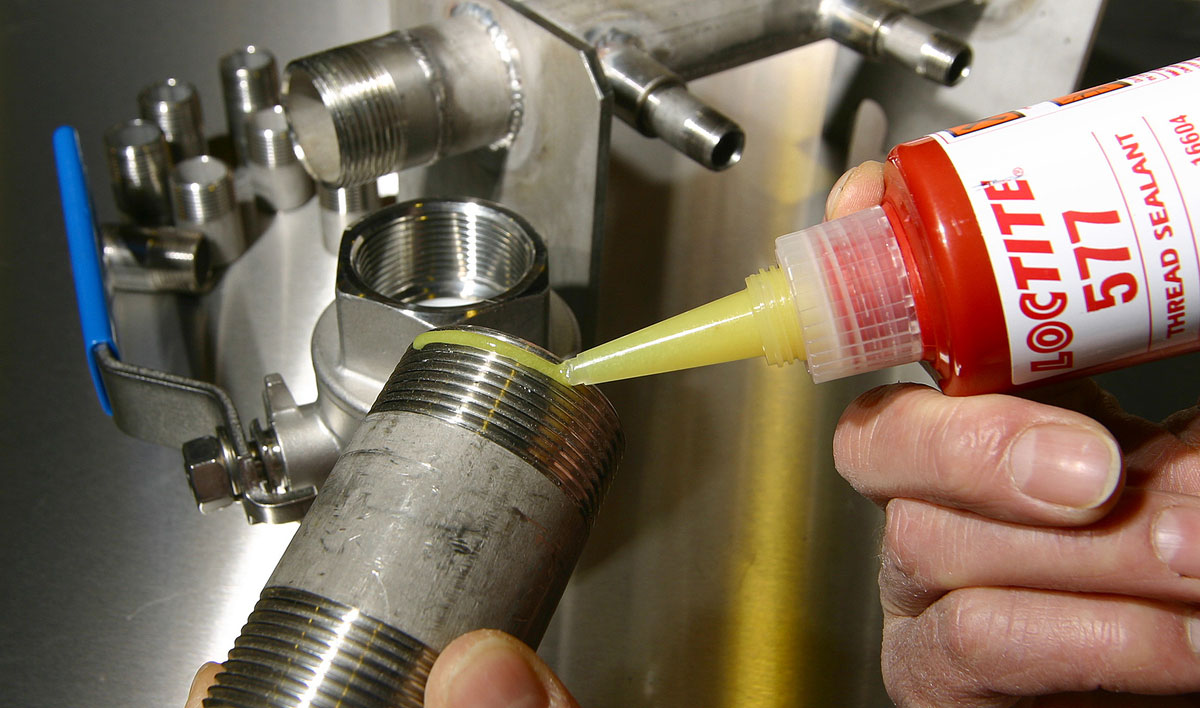
Multiple benefits
Every LOCTITE product for the food and beverage industry offers a multitude of advantages.
With the freedom and flexibility to use LOCTITE adhesives and sealants throughout the sector, food equipment manufacturers and maintenance engineers can work faster and more cost-effectively. For instance, it’s possible to make joints more quickly, and lock and seal them more reliably to prevent any ingress of foreign matter.
Where, for example, fast cure and medium strength are prerequisites – such as anaerobic pipe sealant applications involving coarse metal threads – LOCTITE 577 is ideal.
And when using LOCTITE adhesives and sealants, there’s no danger of nuts and bolts working loose through vibration, of hydraulic parts leaking, gaskets seeping or bearings fretting. So there’s less likelihood of process disruption.
Henkel’s expertise in the food and beverage sector extends far beyond product development. Working together to conduct a free and detailed process and sub-process line survey and audit, Henkel and ERIKS can help identify potential cost savings and improvements.
Matched to the machine
In partnership with ERIKS, Henkel can tailor solutions for any machine in the line: from conveyors to depositors, and mixers to slicers and packagers.
Requirements might include adhesives and sealants for the assembly and sealing of machinery covers, inspection windows and fasteners; bonding of small parts and rubber seals; creating chemical- and airtight assemblies; or carrying out repairs on indexers, rollers, shafts, gears or bearings.
LOCTITE products backed by Henkel expertise and ERIKS know-how can help food and beverage industry customers to find simple, cost-effective solutions for all these applications – and to avoid sticky moments with the regulators.
Case Study
A liquid waste vacuum tanker manufacturer using a competitor product was experiencing leaks in several threads. The stainless steel threads are part of metal-to-metal fittings that come into contact with potable water.
The manufacturer approached ERIKS and Henkel to find a better way to secure and seal the threads. The challenge was to find a sealant suitable for stainless steel, that also carried WRAS approval. In addition it had to be long-lasting, and capable of application by maintenance personnel.
The answer was LOCTITE 5400 thread sealant in conjunction with LOCTITE SF 7063 activator.
The products were a simple, cost-effective solution to a significant and costly problem.
For more information, contact your local ERIKS Service Centre, who will be happy to discuss your options.
#Henkel #Loctite #ERIKS #LetsMakeIndustryWorkBetter #Adhesives #Food #FoodSafety