In this article
You Only Need One Tool for the Job - The Right One
Apologies to engineers across the country. But depending where you work, you’ll know that a Birmingham, Glasgow or Manchester screwdriver is another name for a hammer. Though sometimes, using the wrong tool is not a joke, but a deadly risk.
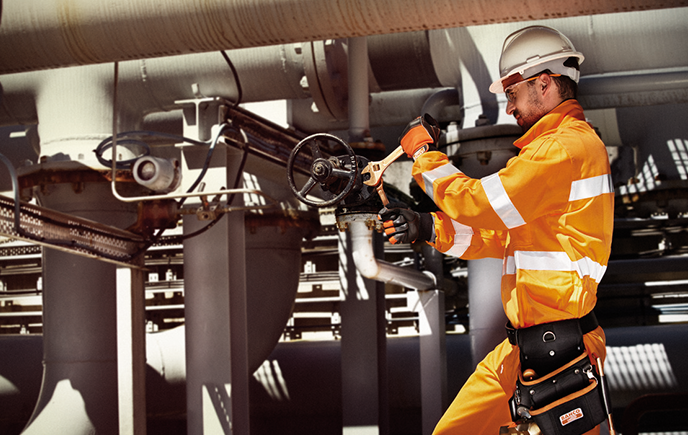
When working in an ATEX zone it goes without saying there are strict safety requirements. Electrical and mechanical equipment must be ATEX-approved and the correct PPE should be used, but were you aware you could just be holding an explosion-risk in your hands?
Hand tools are not within the scope of ATEX regulations. Yet in the right – or should that be wrong? – atmosphere, they could cause the spark that ignites the explosion that leads to minor damage or even major fatalities.
In a sector like the chemical industry, choosing the right tool for the job is a serious business.
One spark is enough
When flammable gases, mists or vapours –or combustible dusts – are present, if enough mixes with air, one spark could ignite an explosion. And that spark could come from a hand tool.
Knock a traditional steel alloy spanner against the nut you’re loosening, drop a wrench onto metal flooring, or let your screwdriver slip as you’re tightening a screw with a standard ‘steel’ hand tool, and that could be the last thing you do.
Fortunately, there is a solution that’s easy to get your hands on: non-sparking tools.
Usually made from Copper-Beryllium Alloy or Aluminum Bronze Alloy non-sparking tools greatly reduce the risk of a spark. However, selecting the right tool is very important but non-sparking tools should never be the only preventative measure in a hazardous environment.
Create a better atmosphere
Sparks are only a danger if the atmosphere is explosive. Preventing that atmosphere from developing is the most effective step you can take.
This means taking isolation, ventilation and purging measures to prevent build-up of flammable vapour-air mixtures, and organic dust clouds such as flour or coal dust. Combine those practices with the use of non-sparking tools, and you reduce the risk of explosion to a minimum.
It’s also important to use and care for non-sparking tools in the right way, to enable them to provide the most effective protection.
They need to be kept clean, free from ferrous and other contaminants which could compromise their non-sparking properties.
And they need more frequent redressing than ordinary tools, as they’re made from softer materials.
Staying stainless
Unlike a dangerous spark, contact corrosion is not a health and safety risk. But with the increasing use of stainless steel in construction and many other sectors, it’s a growing potential problem that can also be resolved with the right tool.
In this case, the right tool for stainless steel is a tool made from stainless steel.
When friction occurs – when tightening a nut, for example – even the hardest steel tool will leave small steel particles behind on the surface it’s in contact with. If that’s a stainless steel nut, this residue is a foot in the door for corrosion to start.
The stainless steel begins to corrode, lose it’s “looks”, and negate the value of its extra cost.
Use a stainless steel tool, on the other hand, and contact corrosion is prevented, the stainless steel items remain corrosion-free, and the additional cost for a better appearance and longer life is fully justified.
So whether you’re working in Birmingham, Glasgow, Manchester, or anywhere else, it’s well worth thinking carefully about your tool choices.
Pick the right tool for the job and – whether or not it’s a hammer – you’ll hit the nail on the head.
#ERIKS #LetsMakeIndustryWorkBetter #Tools #Safety #StainlessSteel