In this article
Does your PPE stand for ‘Pen and Paper Exercise’?
For EH&S Managers, PPE checks are an essential part of the job. But they’re also hugely time-consuming, and generate large amounts of paperwork. 3M Connected Safety could be the answer to saving time – without cutting corners on safety and compliance.
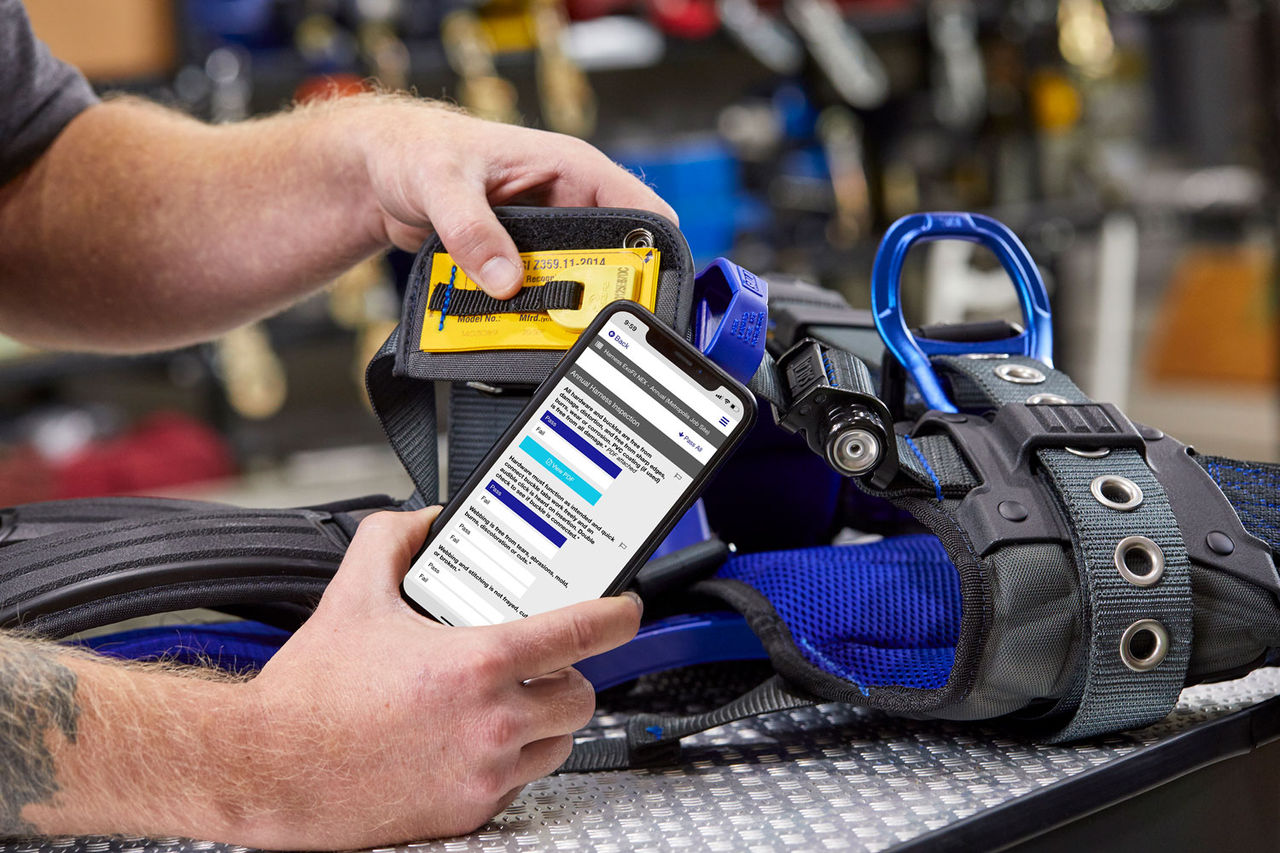
What does your usual PPE inspection regime look like? About 30% inspection and 70% paperwork?
Noting what’s present, what needs replenishing, and what’s due for maintenance. Writing-up the calibration checks and results on the spot. Recording with pen and paper what’s been checked and when. Taking all the notes back to your desk to enter into a spreadsheet on your PC. Plus printing-out all the latest documentation, and updating binders with hard copies for all the stakeholders involved.
Then if someone needs access to the information when they’re out on site, the only way they can get it is by having a hard copy with them, or by contacting you. And when an audit is due, you’ll need to spend yet more time gathering the information together in a suitable format ready for inspection.
There has to be a PPEasier way.
Write-off the pen and paper
3M Connected Safety lets you swap pen and paper for phone and software.
With the Connected Safety app loaded onto your mobile, instead of making a handwritten note of PPE location, condition, maintenance status and so on, all you have to do is scan any of the following: RFID chip, data on the item or simply enter the items ID number. This will identify the equipment, provide all the necessary details, and allow for quick and easy updating on the spot.
Data is instantly uploaded to the cloud for secure storage, but is also quickly accessible to anyone with the necessary authorisation. No more manually updating a spreadsheet back in the office. No more endless printing. No more hard copies and ring binders.
Everything anyone needs to know is instantly available, literally at their fingertips.
Be safe, be sure, be ready
Your regular PPE checks are as vital as the PPE itself. But pen and paper recording of the checks on the spot can lead to errors. And keyboard entry onto a spreadsheet is a chance for something to be mistyped or missed out.
So even if the PPE is correct, the documentation may not be. Or, potentially more dangerous, the PPE may be unsafe – in need of maintenance, for example – or may have been missed on a check, but the documentation says its okay.
With the 3M Connected Safety app, that can’t happen. The software includes a Task List which colour codes actions green if an item is due for checking in the near future, and red if the check is overdue. It also provides an alert if something is missed.
And because the system helps keep everything up-to-date, and keeps all records securely in the cloud, when the time comes for an audit there’s no last-minute panic to get equipment and documentation ready.
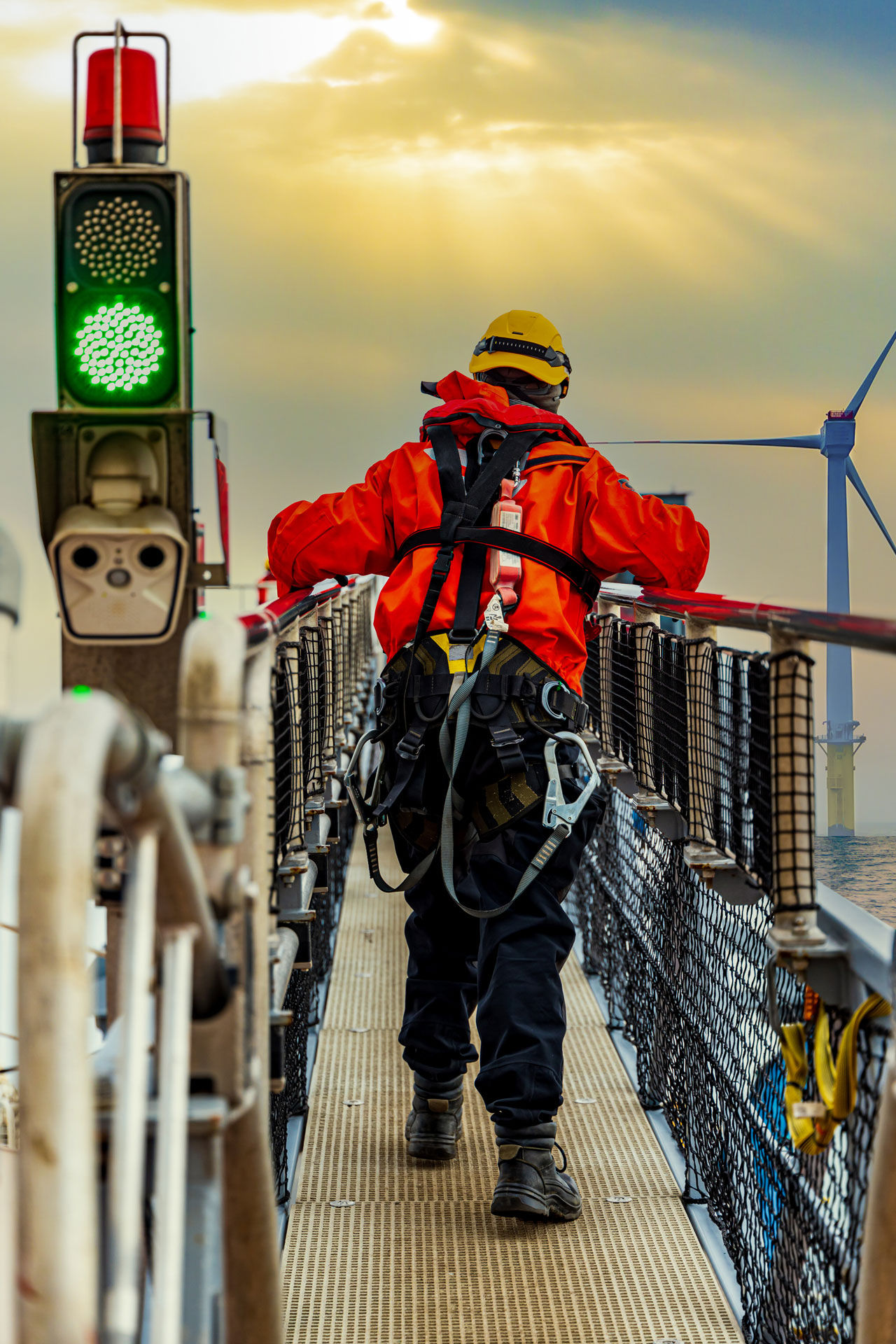
The system ensures all equipment is checked on schedule with nothing overlooked, and that all necessary documentation to prove it is in perfect order, available from the cloud in seconds.
Paper cuts and safety
A leading cable manufacturer opted to cut out their pen-and-paper system in favour of the 3M Connected Safety system and digital app.
By removing the need for manual recording on site, manual data entry back in the office, and printing of multiple hard copies, the result was a staggering 70% time saving for their EH&S team, and a huge saving of paper. But all without compromising safety.
Whether that sounds impressive or hard to believe, there is a Return On Investment calculator tool which you can use to identify how much time you can save in your own organisation by using the 3M Connected Safety system.
ERIKS is one of the first 3M partners to have the 3M Connected Safety system available now. So it’s time to make PPE stand for ‘Please Phone ERIKS.’
For more information, contact your local ERIKS Service Centre, who will be happy to discuss your options.
#3M #ERIKS #LetsMakeIndustryWorkBetter #PPE #ConnectedSafety #TimeSaving