In this article
Wiping the steam clean? How Gaskets can seal the deal
Have you ever been driving along, and your car windows begin to steam up? Well the first thing you would do is switch on your air condition system and the problem is resolved. Leave it and your vision is seriously impaired and danger is imminent. It’s the same principle in a manufacturing environment, the more steam, the more your vision will be challenged.
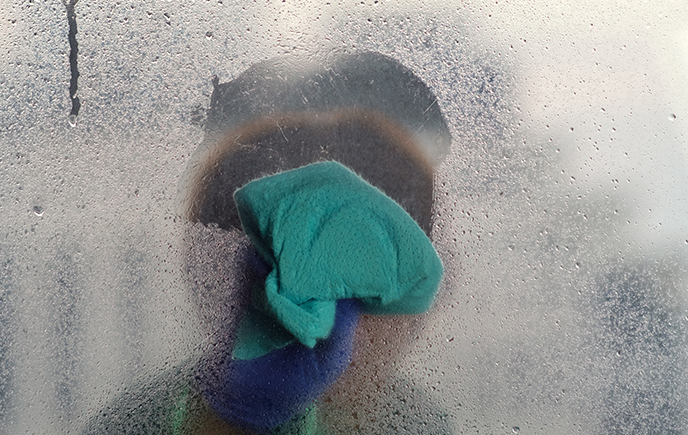
So, when a renowned steel manufacturer was experiencing issues with condensate blurring their blast furnace inspection windows, ERIKS Sealing Technology specialists were on hand to deliver not only a solution to the recurring problem, but one that was far more suitable, and far more superior.
In the past, the condensation caused by the steam from the blast furnace posed the customer no problems, as the windows used for inspection and could easily be manually wiped clear when required. However, with technology taking significant strides forward, the customer made the decision to introduce a more accurate and automated Tuyere camera system for its inspection process.
The newly installed Tuyere camera system remotely controls 30 cameras strategically positioned around the base of the furnace, that are constantly checking for any signs of abnormalities in the furnace environment, whilst sending back accurate data to regulate optimum operating conditions.
Right from the get-go, the problems became apparent.
Running into steam
Condensation caused by the escape of steam via leak paths in perished gaskets was obstructing the cameras vision, resulting in the remotely controlled camera being rendered completely useless.
The only solution was for an engineer to manually change the relevant gaskets on the corresponding windows, an occurrence which needed repeating 3-5 times a month per camera, requiring valuable engineering time and a reliance on holding an increased stock of replacement gaskets. In short, defeating the object of investment in more modern technology.
Originally, the site had specified an extreme high-temperature Vermiculite-based gasket material for the blast furnace in question, believing that this was the best option. But in reality, this type of gasket does not see the higher temperatures within the furnace and a far more suitable gasket could have been utilised.
Understanding the conditions
Upon investigation as to why the windows were having condensation problems, it was found that, although a Mica-based material was suitable for extreme heat, the Vermiculite-based Mica being used was not suitable for the constantly changing temperatures of such an aggressive environment, conditions that caused the gaskets to expand and contract.
As the gasket relaxes, the bonding material fillers which are used to layer the thinner heat resistant Vermiculite mineral begin to degrade due to heat. This then results in a weight deficiency to the overall gasket from which the steam can find a problematic escape route.
Trial initiated
With the root cause of the escaping steam identified and analysed, the ERIKS Application Engineer suggested changing the current style of gasket in operation and, aided by the use of the ERIKS Engineered Gaskets Brochure, was able to suggest various options that would solve this recurring issue.
Taking ERIKS’ suggestions on board, the customers engineering team decided to trial the Leader Egraflex grade of tanged graphite. Although unable to withstand the same temperature range as Mica-based gaskets, it was realised that these properties weren’t essential due to the location of the camera windows not being exposed to the same heat intensity of elsewhere in the furnace.
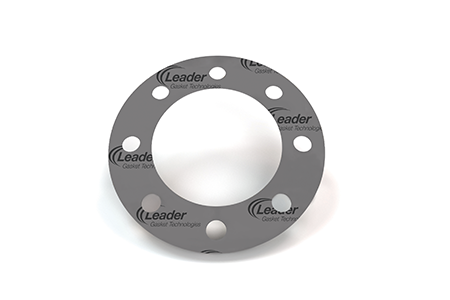
The key characteristics of graphite-based gaskets are that they have the capabilities to work well within steam pressurised systems and also don’t require the filler materials which were the original downfall within the Vermiculite-based Mica gaskets when fluctuations in temperature arose.
Trial success leads to complete process change
Following the initial trial period undertaken on two furnace camera windows, the site reported back to ERIKS, expressing their delight at the vastly improved results of the proposed gaskets, and are currently completing a fully documented engineering management change process that will facilitate the installation of a full change of gaskets on all of the blast furnaces equipment within the Tuyere Camera system.
This change of direction, utilising ERIKS know-how aided by extensive materials and behavioural knowledge, provided the customer with a simple solution to a very irritating and time-consuming problem. Not only has the condensation issue been resolved, but the visibility of the camera investment has also been significantly improved.

In addition, the customers overheads have been reduced due to less stock holding, thanks to the versatile properties and longer lifecycles of the newly installed gaskets, while plant and engineer safety has also been increased dramatically.
Finally, and arguably the most the most important factor, onsite engineers are now able to focus their valuable time and efforts elsewhere across the site, improving the customer efficiency and productivity.
It just goes to show, that with the right advice and expert knowledge, making even the simplest of changes to your production can offer the greatest benefits. The material datasheets and gasket info contained within the Engineered Gaskets brochure is a great source of reference for Engineers and is ready for download today.
#LetsMakeIndustryWorkBetter #ERIKS #Safety #Inspection #Steam #Visual #ProblemSolving #Gaskets #seals