In this article
Top 10 tips for selecting the right gasket
Get the most from your gaskets with the top 10 selection tips from ERIKS...
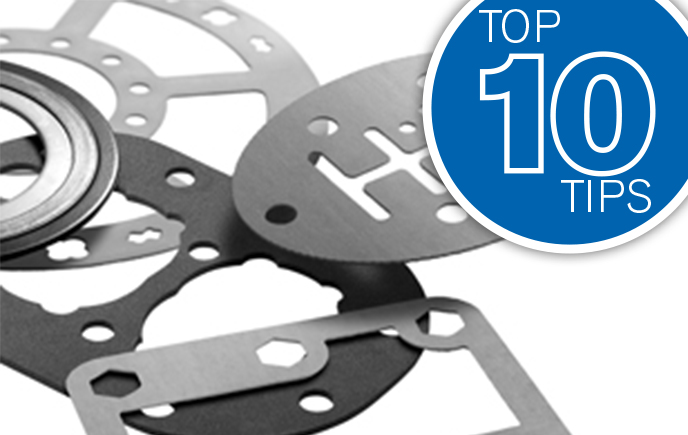
1. Value your gaskets
Gaskets are often the forgotten heroes in manufacturing and process operations, providing a vital interface and seal between mating surfaces.
2. Establish the correct specification.
In many instances, failure arises because gasket material, shape or thickness has been incorrectly specified - often because basic criteria such as chemical, temperature or mechanical compatibility have been overlooked.
3. Consider the temperature of the application.
A typical cause or premature failure is a lack of attention to the issue of temperature during the specification process. Gaskets become brittle at low temperature, leading to lack of flexibility in the seal and, ultimately, the ingress of contamination.
4. In high temperature applications, consider graphite.
As the process temperature rises, the number of suitable gaskets available for specification reduces but graphite gaskets offer robust resistance to high temperatures. Above this we could offer mica/vermiculite based materials for sustained very high temperatures (>550°C) especially in an oxidising atmosphere.
5. In hygiene-critical applications, consider PTFE.
The issue of chemical contact is especially critical within the food and pharmaceutical industries, where process substances can rapidly degrade gasket materials that are not compatible with the application. However, a range of chemical-resistant gaskets are now available using materials such as PTFE , which can be used to manufacture exceptionally resilient gaskets.
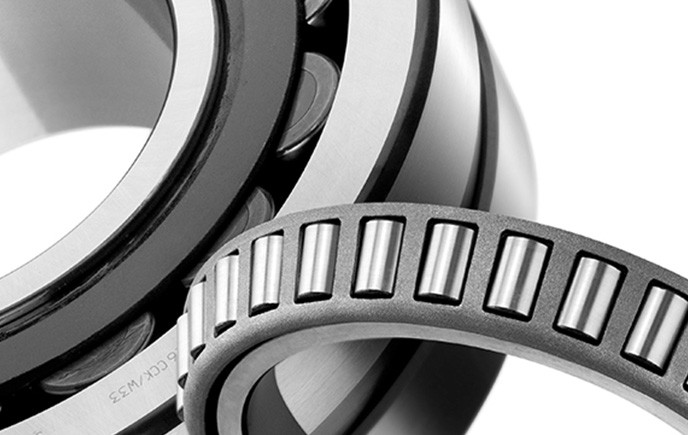
6. Get custom-cut gaskets fast with CAD/CAM services.
Today's state-of-the-art cutting systems use CAD /CAM to deliver fast results to a range of specifications and can cut custom-sized components without transferring contaminants to the gasket. ERIKS UK operates a dedicated gasket cutting operation that has increased wider gasket availability and reduced unnecessary downtime in machinery overhauls.
7. Gaskets can be over-specified as well as under-specified.
The best gasket is not necessarily the most expensive one. Sometimes a simple gasket is more cost-effective because it is perfectly adequate for the application, which is good news when the plant requires the cutting of thousands of gaskets.
8. Consult an expert supplier.
The points made above illustrate why it is so important to consult with an expert supplier from ERIKS Gasket Technology, who can establish, for example, whether the performance requirements of your application are well met by a simple, inexpensive gasket.
9. Make cost savings by rolling out new specifications plant-wide.
If you establish that current components have been over-specified, the result of consultation with an expert supplier from ERIKS Gasket Technology may be that your production plans incorporate a planned reduction of gasket quality to avoid any unnecessary expense.