In this article
To upgrade your motors, upgrade your experts
A major pet food manufacturer carries out continual process evaluations and efficiency, emissions and productivity assessments. That’s what helped them recently to identify the need for an upgrade of their motors. However, their engineers realised that to achieve the best solution, they would need expert advice and support. So before they looked at motors, they looked at suppliers.
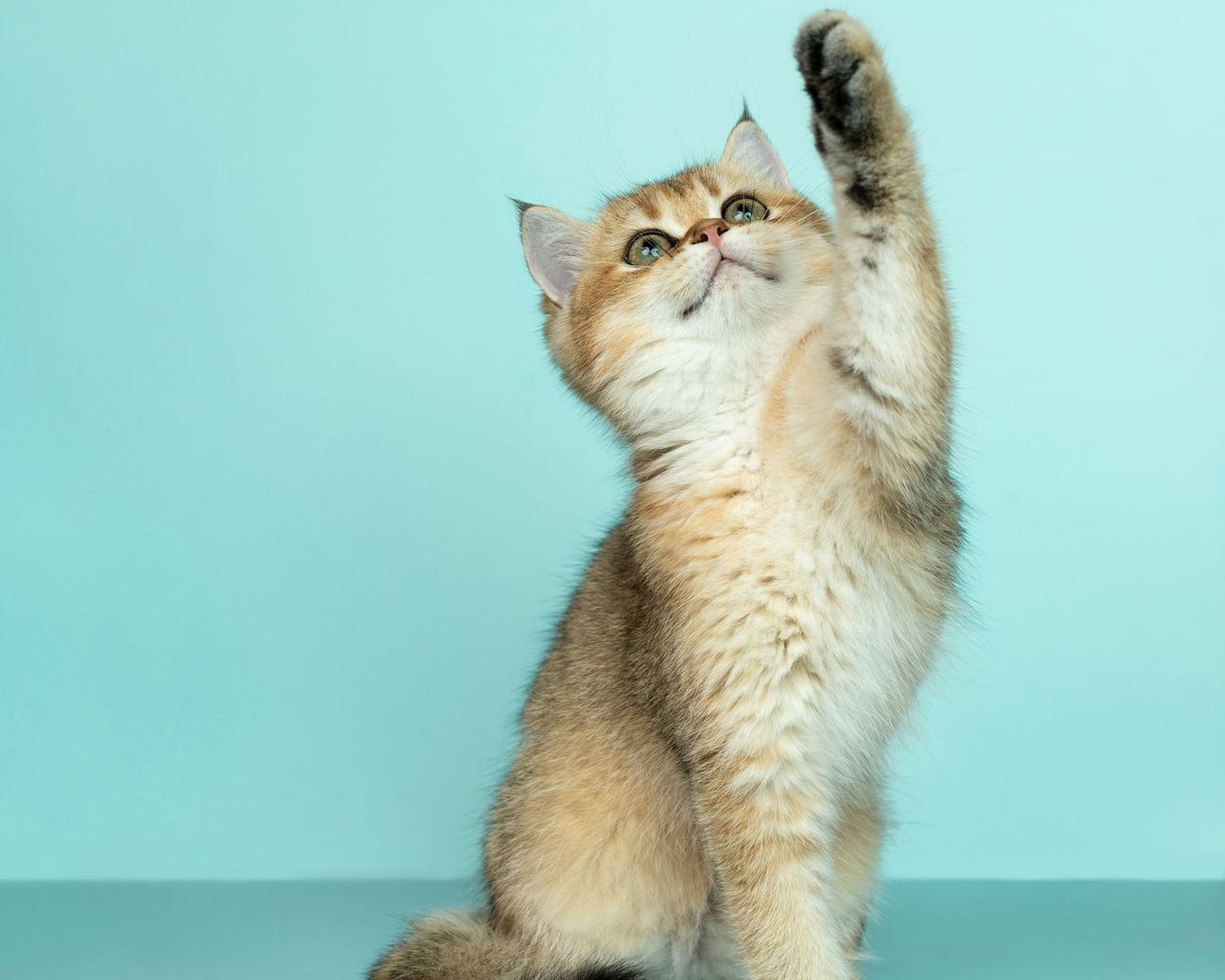
In the first instance, the customer contacted WEG and a competitive motor OEM. As ERIKS’ motors partner, when WEG got the call they contacted ERIKS to arrange a joint site visit. After all, why offer a customer only energy-saving motors technology expertise, when you can combine it with unparalleled application know-how?
Room for improvement
The customer’s engineers had recognised that the 250kW IE2 motors powering one particular application were a weak point in their energy-efficiency efforts. As IE2 is the second-lowest energy efficiency rating for electric motors, replacing IE2-rated motors with more energy-efficient options gives plenty of room for improvement in energy consumption and emissions reductions.
There are five of the motors on the site, all used to power an essential part of the manufacturing process. The customer decided initially to replace just one as a test case.
However a handful of additional challenges and requirements meant the solution wouldn’t necessarily be as simple as just swapping out one motor for another. A little more thought was needed.
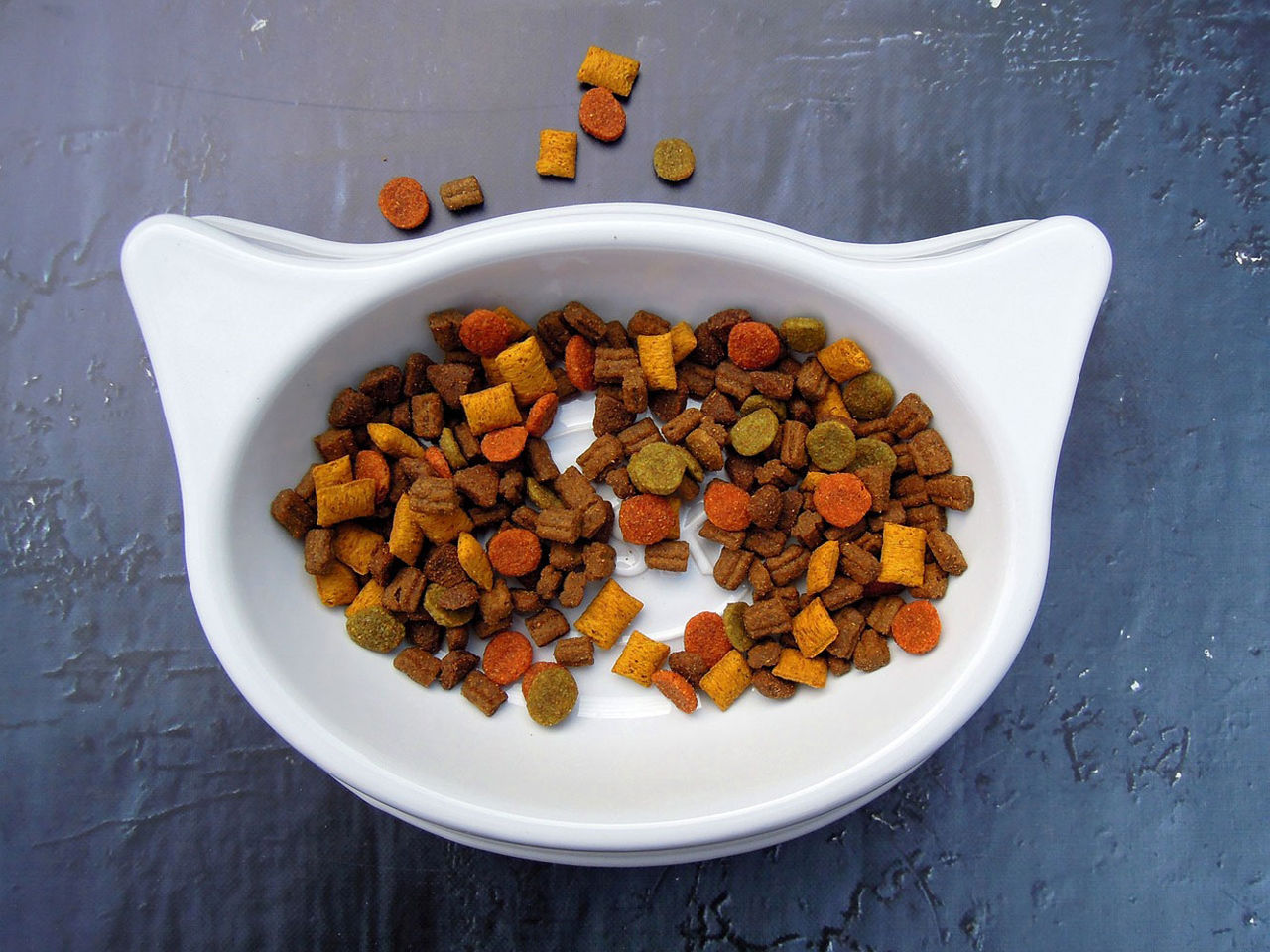
Cost-saving drive
The first challenge was the customer’s existing standardisation of drives throughout the site. This meant there was little to be gained – and a great deal to be lost – by choosing a motor which required a different drive. So any new motor proposed had to be fully compatible with the existing drive.
The competitive tenderer for the new motor proposed a model which would have required a change of drive. This would have created extra unnecessary complications for the installation, as well as increasing installation costs and – potentially – maintenance costs too.
The ERIKS and WEG solution, on the other hand, integrated seamlessly: saving installation time, reducing disruption and costs, and maintaining the customer’s site-wide standardisation.
Fit for purpose
In addition to integrating with the existing drive, the customer wanted the new motor to retain the 250kW rating of the old one. This would enable it to fit the same frame size and footprint. Again, the aim was to minimise extra work, costs and disruption.
ERIKS and WEG proposed two alternative motors, and ultimately the customer opted for the WEG 260kW IE5 permanent magnet 6-pole motor, operating at 75Hz. This not only met the customer’s criteria, but with its permanent magnet technology also has the added benefit of not having the need to replace the existing drive configuration.
The asset’s operating environment places additional demands on the motor, which WEG technology and ERIKS know-how helped to resolve.
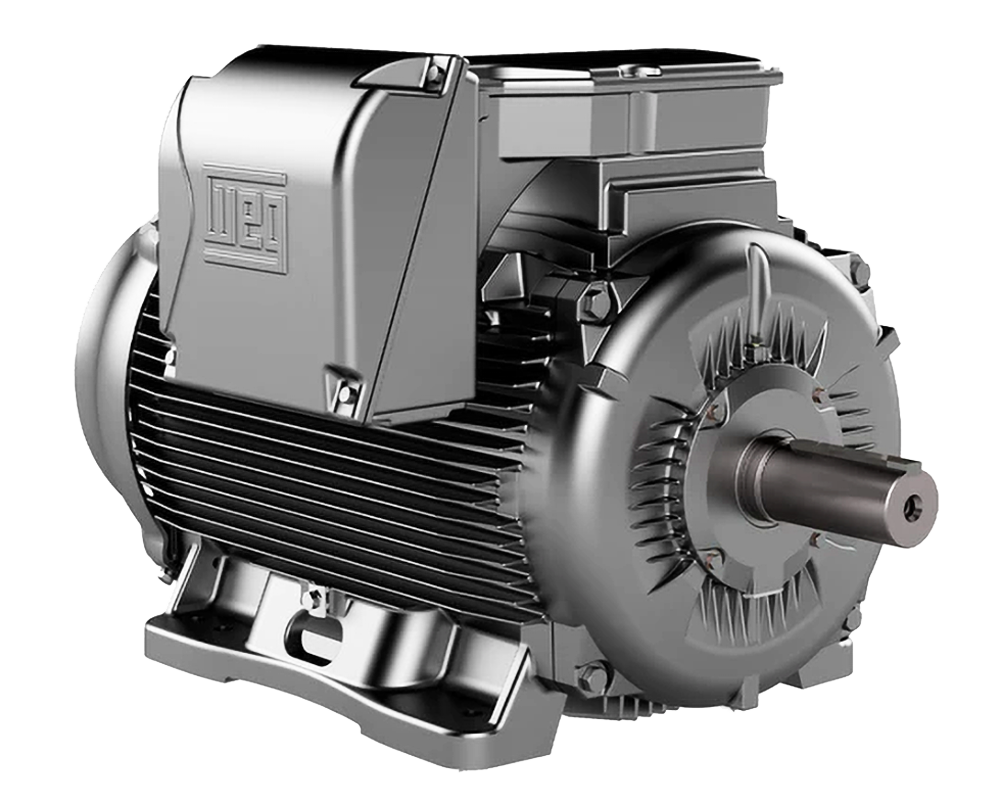
The potential for heat transference from the asset to the motor raises the possibility of lubricant failure. WEG’s solution was to fill the motor bearings with high-temperature grease. And the frequent high-pressure cleaning which takes place around the asset, using aggressive chemicals, meant that the motor casing had to be treated with a specially resistant and hard-wearing paint finish.
The power of two
By upgrading to a more energy-efficient motor, the customer had been targeting a 5% energy-saving with a 5-year payback period.
In fact, thanks to expert support and advice from two leaders in motors, industrial applications and energy-efficiency, they have achieved energy savings of 8-9%. That means energy cost savings, calculated by the customer, of £12,492 p.a. with a payback period of just 2 years.
With four more IE2 motors powering the same application on this site alone, and 80 more worldwide, there is enormous potential to make even more significant savings and carbon footprint improvements, by upgrading them all to a higher energy-efficiency rating.
Five energy-efficient motors are better than one. And when it comes to energy-saving advice, two heads are clearly better than one.
For more information on Power Transmission and to get in touch with one of our ERIKS Specialists, please contact your local ERIKS Service Centre, who will be happy to discuss your options.
#WEG #ERIKS #LetsMakeIndustryWorkBetter #Motors #IE5 #TCO #EnergyEfficiency