In this article
How to save thousands of pounds before breakfast
Suppose one of your production line assets had a maintenance schedule that declined from every two months to every two weeks. Would you wake up and smell the coffee? Or, as one ERIKS’ customer did, would you wake up and smell the porridge?
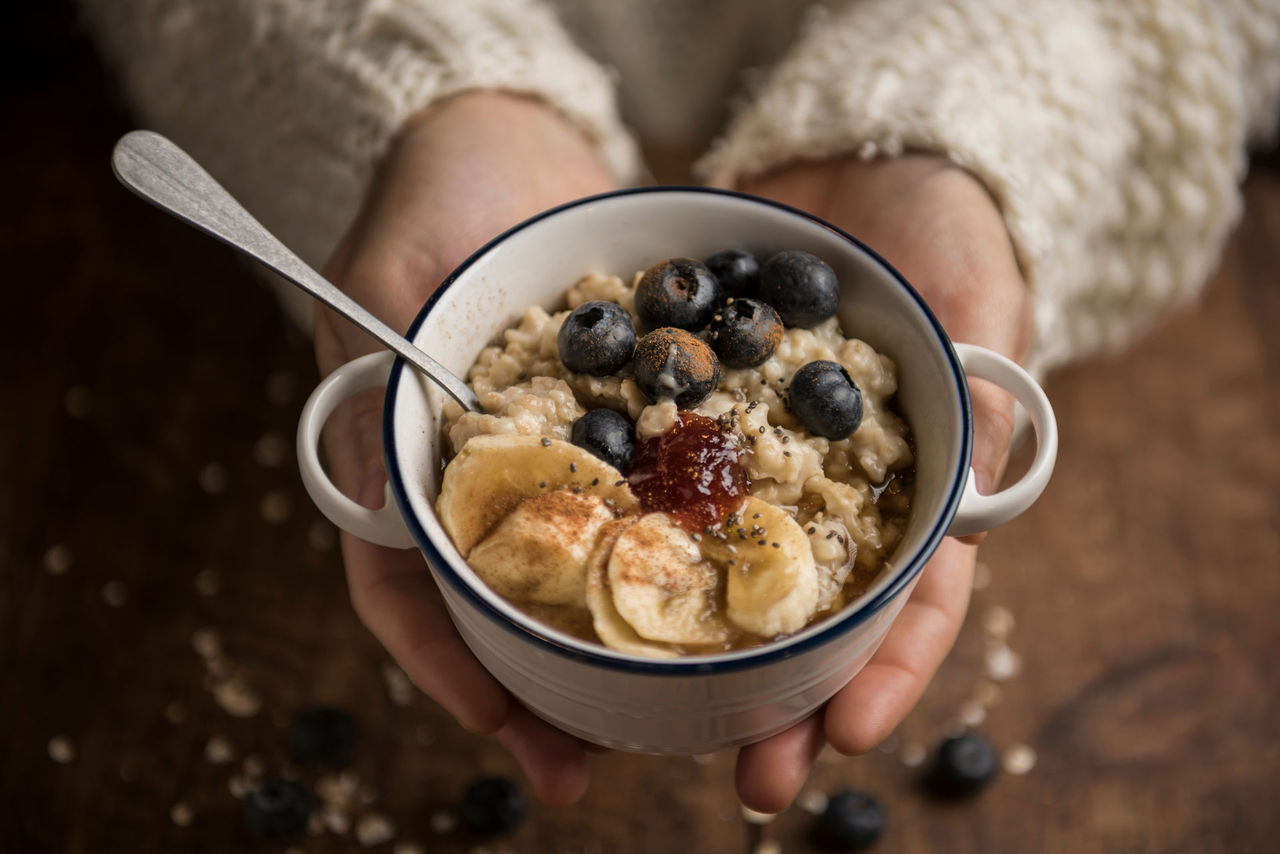
Whether you prefer breakfast porridge with sugar, salt, honey or syrup, one of the most convenient ways of making it is from a sachet. And the popularity of these sachets is why one porridge oats manufacturer has a high-speed production line which operates at 1,200 sachets per minute.
Or at least it did when it wasn’t offline for maintenance, as it increasingly was.
Cutting production
The critical asset causing the problems was the knife tower of six flexible blades on a minor hub set and twelve fixed blades on a major hub set. These were driven by two gears at a ratio of 1:2, and work together like scissors to cut the bandolier of filled pouches into individual sachets.
A registration mark on each sachet is read by sensors, which send a signal to the knife tower servomotor. This then slows down or speeds up the process as appropriate, to ensure the bandolier is cut at the correct place to create the sachet.
As the knife tower’s reliability declined, knife blades were being replaced every two weeks, rather than every two months as originally. In addition the drive gears, once replaced every twelve months as part of a preventative maintenance programme, were running to failure as often as every three months.
Changing the blades alone took up to six hours, and replacements were expensive. So costs and productivity were both being badly affected.
Time for ERIKS to take a look.
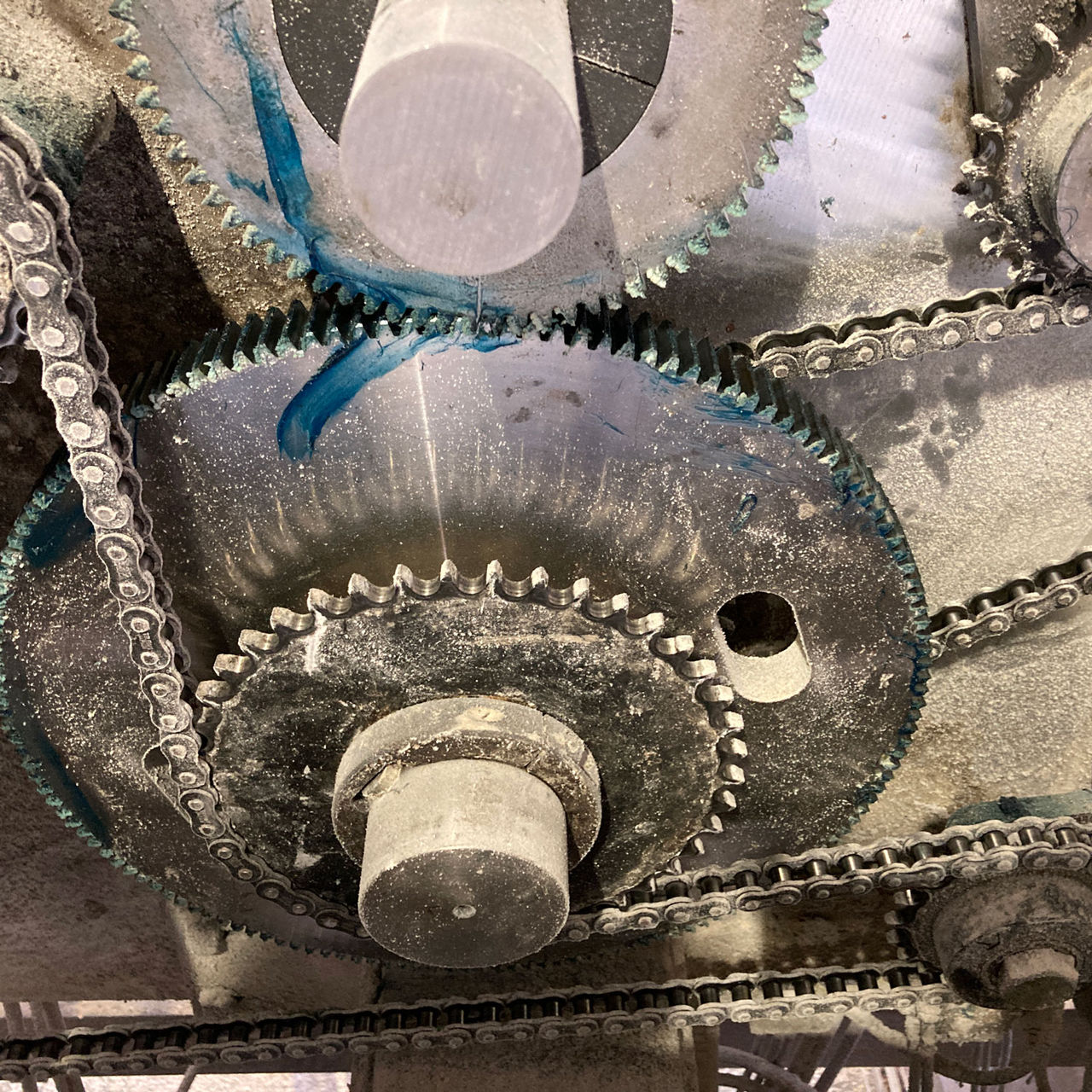
Repair, replace – or rethink?
The least attractive option to keep the porridge pouring would have been to repair – at a cost of £5,000 for a new pair of gears every three months.
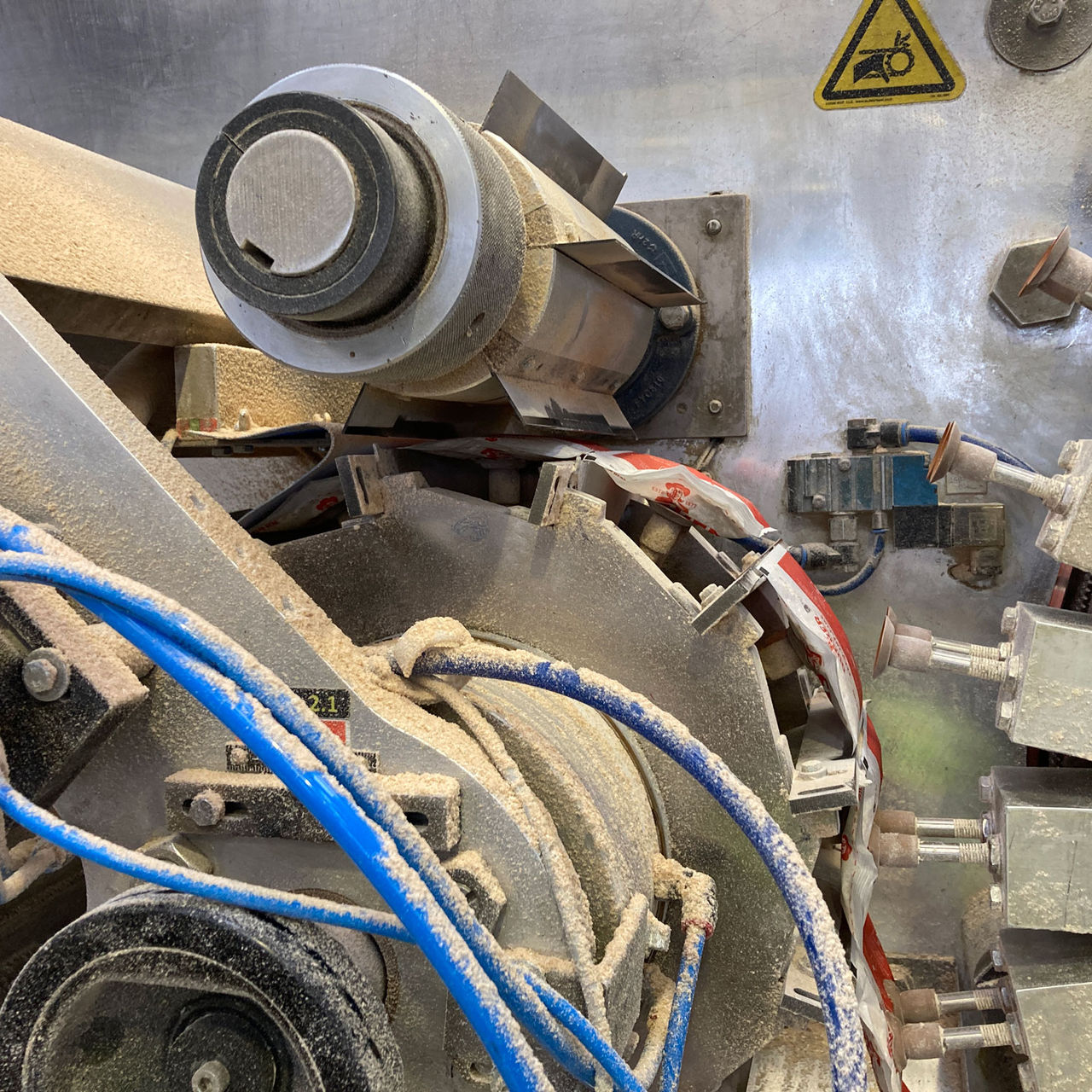
Another option would have been to carry out a complete asset replacement – at a cost of several thousand pounds – hoping it would run at full speed and capacity for a while before the problems began to reoccur.
ERIKS’ approach was different. Not to repair. Not to replace. But to go back to the drawing board and rethink. And not just to ask why the asset was failing, but also if there was a way of making it perform more reliably. ERIKS know-how provided the answers.
Changing gears
An assessment of the asset and its failure modes showed that the gears were the weak link in the set-up. So ERIKS’ engineers designed an entirely new layout which maintained the performance but eliminated the gears – and the problems that went along with them.
By replacing the gears with belts and pulleys, gear wear through friction is eradicated. The noise level is reduced. And only the drive belt and bearings – inexpensive, off-the-shelf items – will need to be replaced over time.
The cost to the customer of the new design was just £2,200 – or less than half the price of the previous set-up. When the belt does eventually need replacing, the downtime will be much reduced. And the belt itself will cost just a few hundred pounds rather than £5,000 for a new pair of gears every three months.
With the new ERIKS-designed belt-driven system in place, the customer undertook a test run which operated successfully at full speed for six weeks before the blades broke. This was three times the life of the previous asset.
After minor adjustments the line was restarted and this time the blades lasted sixteen weeks: eight times longer than the gear-driven version. The true efficiency of the line has been calculated to have increased from an average of 62% to 78% – reflecting the greatly increased reliability of the new gear-free design.
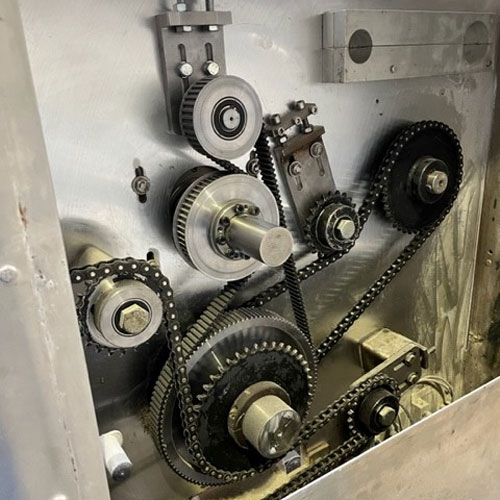
Pleased with the cost-savings and productivity improvements, the customer has now placed an order to swap gears for belts and pulleys on a second knife tower. So if you like your porridge in cost-effectively produced sachets, relax. A second helping is on its way.
For more information on Power Transmission and to get in touch with one of our ERIKS Specialists, please contact your local ERIKS Service Centre, who will be happy to discuss your options.
#ERIKS #LetsMakeIndustryWorkBetter #GearedDrives #Belts #Pulleys #FoodAndBeverage