In this article
A true Gearbox story (to be taken with a pinch of salt)
Salt in the air. Salt crunching underfoot. Salt coating every surface. It’s probably what you would expect at a major salt processing plant. And if you’re there to investigate a repeated drive failure, it would be easy to assume the aggressive environment was the obvious cause of the problem. But it doesn’t pay to jump to conclusions, especially with a suspended gearbox and motor at great height...
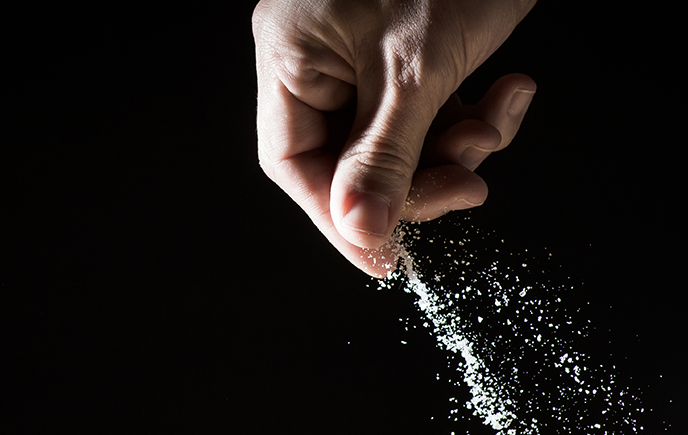
Too much salt is as bad for mechanical assets as it is for people. However, if you’re adding it to a massive plate of greasy chips with a battered Mars Bar, you need to look further than the salt to see what’s going to do the real damage. Similarly, although the operating conditions might be tough, are they really the cause of the drive failure?
This customer’s motor and gearbox are positioned around 70ft up in the air, at the top of a vertically-running bucket elevator. It’s a far from ideal location to be carrying out repairs or frequent replacements. Installing a new drive – weighing around 500kg – demands a crane for initial lifting, then a block and tackle for manoeuvring. And it means engineers working at height, with serious Health & Safety implications.
Add in the cost of a new gearbox and motor every twelve months, and it’s no surprise the customer’s Reliability and Improvement Manager wanted to get to the bottom of the problem at the top of the elevator.
One call – unlimited expertise
An ERIKS’ engineering workshop team from the Regional Hub at Haydock, St. Helens, had been involved in the most recent gearbox swap-out. So ERIKS were the natural choice to carry out further investigation. Haydock Service Centre Manager Mark Glover was the customer’s first point of contact, and Mark called for expert Technical Application Engineering support.
The drive operates a vertical bucket elevator which carries salt from a hopper on the ground to discharge into a silo for storage. The salt is extracted from brine, pumped over 20 miles from its extraction site to a holding reservoir prior to processing. Salt is present everywhere on site, and corrosion is inevitable. However, it wasn’t the leading cause of the drive failures.
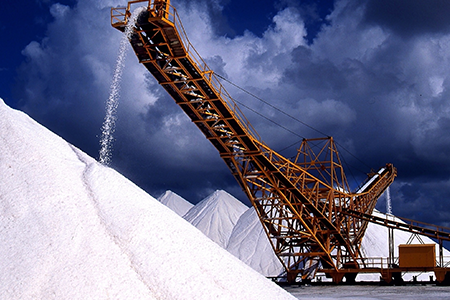
The application involved a 15kW motor driving a worm gearbox. A coupling then connects to a reduction chain drive at the headshaft of the bucket elevator. A first glance indicated, based on long experience, that the gearbox was almost certainly too small for the job it had to do. And collecting and assessing the application data proved the hunch to be correct.
For an elevator of this type, a gearbox service factor of 1½ is ideal. This one had a service factor of barely 1, even when new. Its capability for transmitting the necessary motor power was borderline. So it was constantly running under an excess load, leading inevitably to excess wear on the worm and wheel set, and premature gearbox failure.
Less stress all round
Discussions with the appropriate ERIKS Product Business Unit led to the proposal for a replacement geared motor. This would have the same operating characteristics, but importantly with a Service Factor of 2+ to reduce stress on the gearbox. At the same time an upgrade to the final reduction chain drive – from a 1” pitch duplex to triplex – was also recommended, to reduce bearing pressure on the chain and lengthen its service life.
The combined geared motor had a bedplate suitable for the existing mounting. Also simplifying matters, no guard modifications were required to accommodate the new motor unit or the triplex chain. So removal of the old unit and installation of the new took just one week during a scheduled shutdown, and was far easier than previous like-for-like swap-outs. Predicted service life is also far longer than the 12 months of the former gearbox and motor solution.
The customer had easy, stress-free access to ERIKS’ unparalleled resources, extensive experience and exceptional know-how, all through one initial contact. And ERIKS not only recommended, supplied and installed a solution, but also provided CAD documentation and complete traceability of all components for future reference.
Impressed by the comprehensive service, the customer has now briefed ERIKS to resolve an issue with short-lived bearings at the base of the same elevator. Whatever solution ERIKS’ engineers come up with, it’s sure to give the customer a lift.
For more information you can contact your local ERIKS Service Centre, who will be happy to discuss your options.
#ERIKS #LetsMakeIndustryWorkBetter #Gearbox #Motor #Reliability #Engineering #LiftingSafety