In this article
Can Pressure Be Good for Your Motors?
One of the weakest points of a motor in an aggressive environment is the winding. Once contamination gains ingress it creates a tracking path through the winding which allows a leak to earth and a motor trip. The same can happen in damp conditions even without contamination.
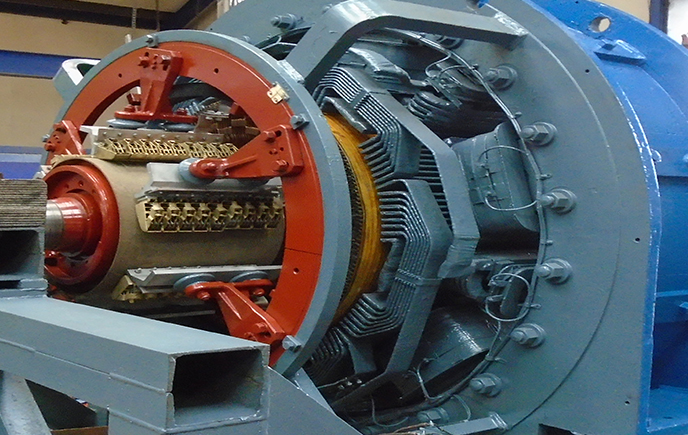
The challenge is to find a way to resist contaminant and moisture ingress, to ensure the insulation resistance of the motors is maintained.
VPI – VIP treatment for windings
There are usually two ways motors are treated to resist moisture. One is dipping the winding in a polyester or epoxy resin, to creates a moisture-resistant coating. The other – more effective method – is Vacuum Pressure Impregnation (VPI) of the winding.
The advantage of VPI over dipping is that moisture resistance is integrated into the winding structure, rather than being just an outer coating. The resin is forced right into the depths of the winding under vacuum pressure, filling air pockets in the winding. This also binds together any loose lamination in the core: not only helping to keep out moisture but also enhancing the winding’s mechanical strength and heat dissipation properties.
VPI has been available for many years, but many treatments use resins optimised for low- cost processing rather than performance. Leading suppliers such as ERIKS use a more effective 100% solid epoxy resin, optimised for performance and protection.
The scale of equipment required for VPI means the treatment is only available from a limited number of suppliers. ERIKS VPI plant is designed to process stators from the smallest DC coil wire wound, up to larger 6,600 volt windings.
However, it takes more than just equipment to make VPI effective in protecting motors and increasing their reliability. It takes know-how too.
Going further. Lasting longer
ERIKS’ engineers have the expertise to determine whether VPI will solve the problem, or whether additional measures – such as a complete rewind – are required.
If the motor winding is in good condition apart from its porosity and moisture absorption, then VPI alone has the potential to increase its service life by several years. If, on the other hand, the winding has deteriorated too far, ERIKS will recommend a complete rewind utilising highly absorbent VPI-compatible material, followed by the VPI process. The compatible material will increase the uptake of the epoxy resin and help to form a solid, homogenous mass providing maximum moisture resistance.
Their know-how also allows ERIKS’ engineers to look beyond the motor winding to the bigger picture.
Back on the rails
When traction motors on Channel Tunnel freight trains were proving unreliable, some suppliers may simply have recommended VPI. After all, the damp and dirty operating conditions in the Channel Tunnel suggested that contaminant and moisture ingress to the motor were the main problems.
However, in addition to very low insulation resistance readings, ERIKS’ wider investigations determined the failure mode as a breakdown between phases on the stator winding connections.
Realising that VPI would only partly solve the problem, ERIKS’ engineers not only stripped the connection rings and reinsulated them using VPI, but also redesigned them. The original high-temperature silicone insulation system within the coils was retained, to provide higher-temperature protection where it’s most needed. Meanwhile the redesigned rings were sealed with Class H 180°C epoxy VPI, providing greater protection against the environmental conditions.
The result was a complete elimination of the motor failure mode, and an ongoing programme to modify all the customer’s other traction motors in the same way.
As the chart [Fig. 1] and graph [Fig. 2] show, when VPI alone is the answer, the results can be dramatic. But if a broader solution is required, ERIKS have the know-how to see it through – and to take the pressure off you.
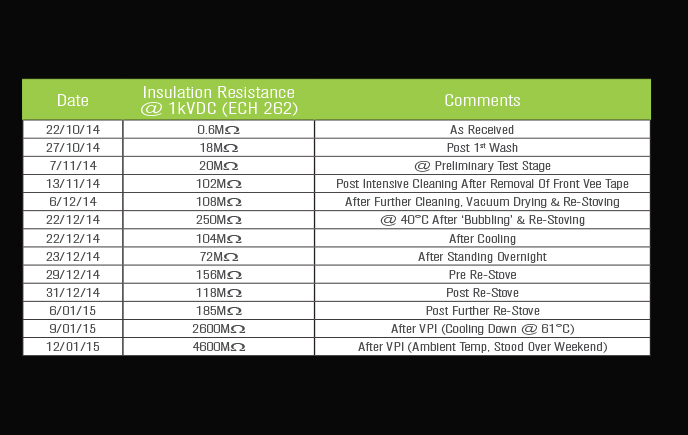
Fig 1: Cleaning and VPI of Motor Winding
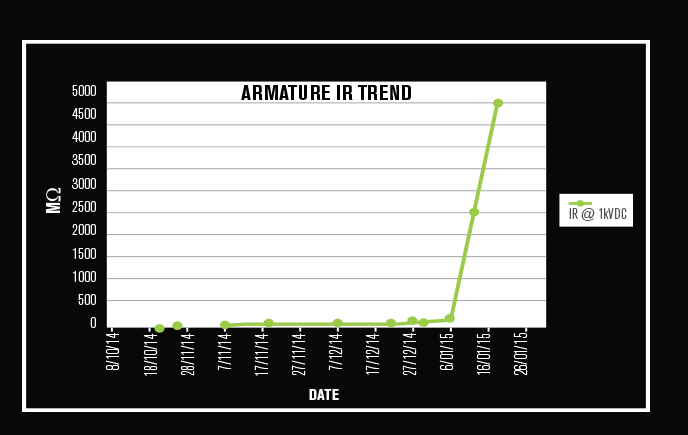
Fig 2: Insulation Resistance trend of armature, before, during and after cleaning and VPI
For more information on Power Transmission solutions and to get in touch with one of our ERIKS Power Transmission Specialists, please contact your local ERIKS Service Centre, who will be happy to discuss your options.
#ERIKS #LetsMakeIndustryWorkBetter #PowerTransmission #Motors #Winding