In this article
Rolling back the years
While some people were busy founding Pizza Hut, Elvis Presley was joining the U.S. Army. The EEC (as it was called then) was just starting, and so was the Campaign for Nuclear Disarmament (CND). Meanwhile, in that same busy year (can you guess which one?*, A sugar manufacturer was pressing the start button on their new rotary louvre granulator. Now, in 2022, it was time for ERIKS to step in.
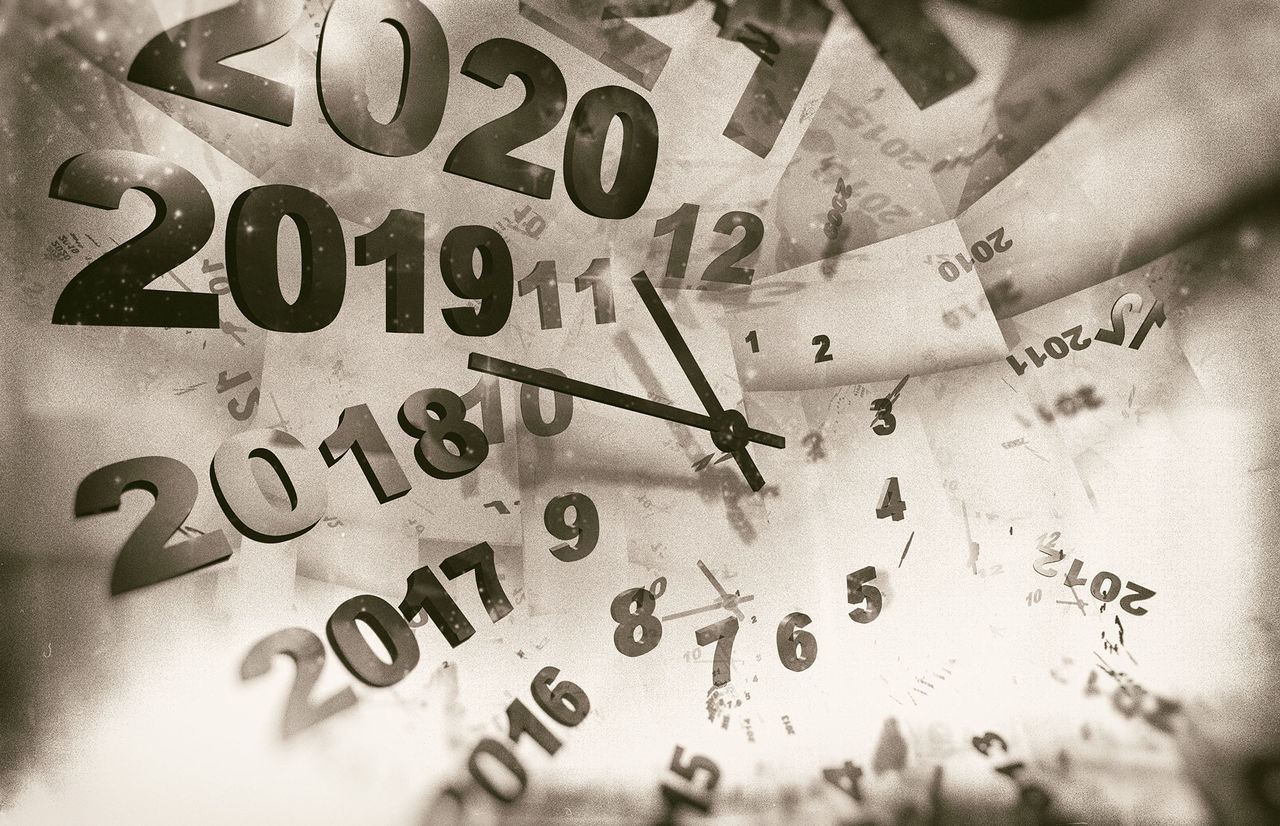
Testing, testing…
Designing, engineering, and manufacturing the new component was only the start of the job. Before it could be installed in the asset, ERIKS – and the customer – had to know for sure that it would perform as effectively and safely as possible.
That’s when Non-Destructive Testing came into play.
An NDT Inspection assesses a component’s safety, consistency, reliability and other essential factors, without damaging the item during the testing process. NDT can also detect any defects which may have occurred during the manufacturing process. This was especially critical in this case, as ERIKS was engineering a component from scratch using a new grade of material.
The impressive asset comprises a metal drum 41ft long by 10ft diameter (approx. 12.5m x 3m). The drum is supported on 4 rollers, each weighing 1½ tonnes and operating in pairs. When fully loaded with white sugar crystals, the drum and contents weigh 50 tons (approx. 45 tonnes metric).
Gently tumbling the sugar to remove moisture, the granulator rotates on the rollers at a stately 12 rpm. It’s the kind of enormous and unusual engineering asset which might once have featured on Blue Peter (the children’s TV programme that launched in the same year). It’s big. It’s heavy. And it’s clearly wellengineered – because although they didn’t know it at the time, it was to prove to have a service life of more than six decades.
For much of that time, maintenance of the asset’s taper roller bearings has been carried out by ERIKS. This has included frequent machining of the rollers to maintain their smoothness, as the drum gradually wears them away.
However, over half a century after the initial installation, it has become clear that – due to parts obsolescence – a more comprehensive solution is required.
A metric make-over
The older the asset has become, the harder it gets to source spare parts – not least because the originals were manufactured to imperial measurements. Even when they can be sourced, the delivery lead time on replacement parts can be as long as 14 weeks.
Eventually, on ERIKS’ advice, the customer realised it was time to rethink rather than simply repair.
However, replacing the original components with new, metric versions wasn’t just a matter of converting the measurements.
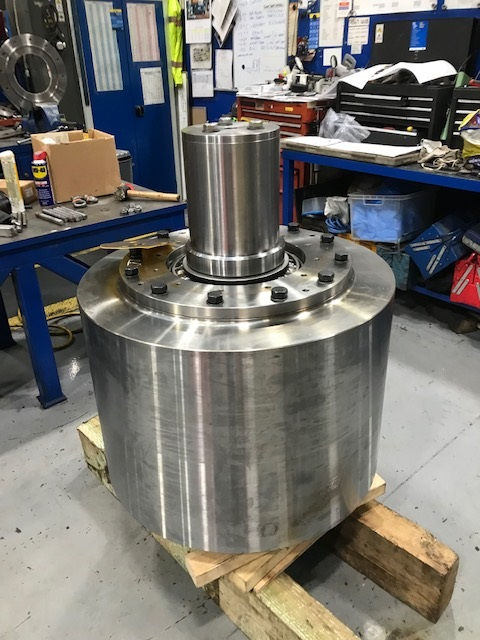
Sixty-four years on, the original manufacturing material – BS1760 Grade A – was no longer available. But matching its specification was essential. Too soft, and the rollers would wear too quickly. Too hard and, instead of solving maintenance issues, it would create new ones. Rather than the drum causing wear to the rollers, the rollers would wear the drum. Which would then also need replacing.
While the ERIKS project team assessed the original engineering drawings from the Fifties, converted the measurements to metric and created new manufacturing drawings, a specialist analysed the original materials used, to identify a suitable similar grade.
Find, test, deliver
Maintaining the ratings of the bearings while updating the material required extensive investigation and analysis. Even when a potential alternative material for casting had been identified, it had to be checked for its suitability through nondestructive testing (NDT), to ensure it would meet all necessary mechanical and chemical certification [see box-out above].
ERIKS’ know-how ultimately identified BS3100 Grade AW2 as a suitable material. So, with the drawings completed, the manufacturing could proceed. However, even this wasn’t straightforward. The new rollers had to be cast, not forged. This gave ERIKS the challenge of finding a supplier with the necessary skills to produce the pattern, and then to manufacture the roller to the updated and upgraded specification.
Now, thanks to ERIKS’ comprehensive capabilities, the new taper roller bearings are installed and operational, and the customer can look forward to – potentially – another 64 years of smooth operation.
*The year in questions was 1958
For more information on Power Transmission solutions and to get in touch with one of our ERIKS Power Transmission Specialists, please contact your local ERIKS Service Centre, who will be happy to discuss your options.
#ERIKS #LetsMakeIndustryWorkBetter #PowerTransmission #Rollers #Sugar #Food #Specialism #Innovation #KnowledgeTransfer