In this article
Top 5 Tips for Healthy Motors
It might be an obvious statement, but healthy motors are pivotal to the successful operation of any production plant. Not only will a healthy set of motors ensure a smooth production line, but regular maintenance will significantly reduce your Total Cost of Ownership (TCO), improve reliability and increase productivity. Sound like music to your ears?
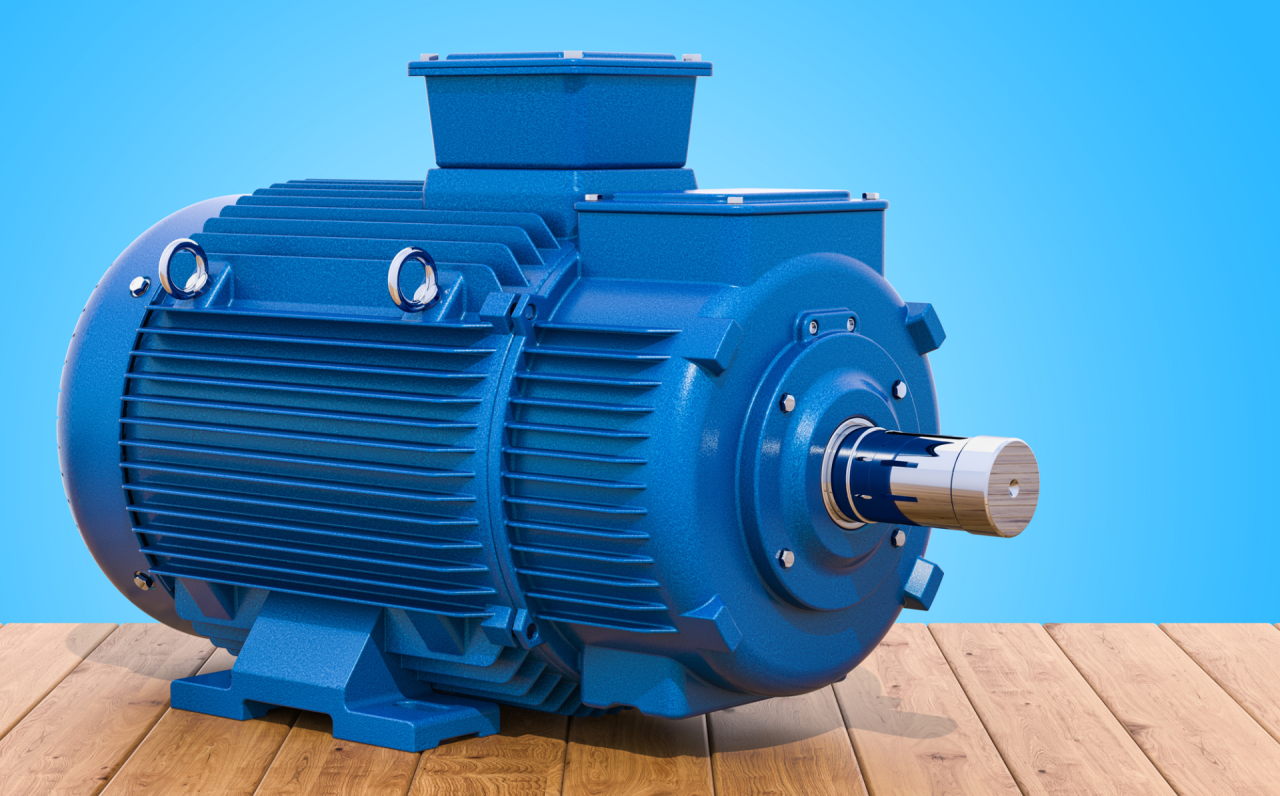
To assist you in maintaining healthy motors, ERIKS Product Manager for Power Transmissions Mark Prior, shares his top 5 tips to ensure your core motor assets remain in tip-top condition.
1. Use the most efficient motors for your requirements.
With rapidly increasing energy costs, it is now more important than ever to optimize your operation to ensure energy requirements are managed in the most efficient way to keep running costs to a minimum.
ERIKS have an easy-to-use TCO motor calculator to allows a quick and easy decision-making process when replacing or upgrading old, lower efficiency motors, along with a comprehensive stock of IE3 and IE4 motors allowing for a quick turnaround.
2. Protect your critical equipment
Utilise a Smart Asset Management system to keep an eye on your critical motors. Monitoring KPI’s such as vibration and temperature allow problems to be identified and planned for before and unexpected failure occurs, preventing expensive downtime and hassle.
3. Ensure your motors are correctly aligned
Geometric inaccuracies during installation can lead to accelerated wear of the bearings that provide critical support to the internal components of an electric motor.
Tell-tale signs usually include vibration, audible noise, and overheating. These symptoms should be promptly investigated and remedied to ensure no sudden surprises like catastrophic failure, and the associated downtime that ensues.
4. Keep it cool
Most electric motors keep cool by using a fan to force air along a series of cooling fins on the motor body. It is imperative that these cooling channels are kept free of debris. This allows for an undisturbed flow of air which provides maximum cooling.
It is also important to ensure motors are correctly rated for the ambient temperature of the application. This will help ensure a long and productive life cycle.
5. Use the right motor for the job
Significant energy savings can be unlocked in certain applications by using a variable speed drive, but it is important to use motors that are correctly specified for the application.
When using variable speed drives, it is common to slow the motor down, which also slows the cooling fan down which may lead to issues with overheating. Measures can be taken to keep things running smoothly, such as using an oversized motor for heavy load applications to better cope with the heat at lower speeds or using a force ventilation cooling system to provide the same level of cooling at all speeds.
It is also recommended to use a PTC-thermistor or Thermostat, and correctly wire these into the control system to prevent the motor from overheating.
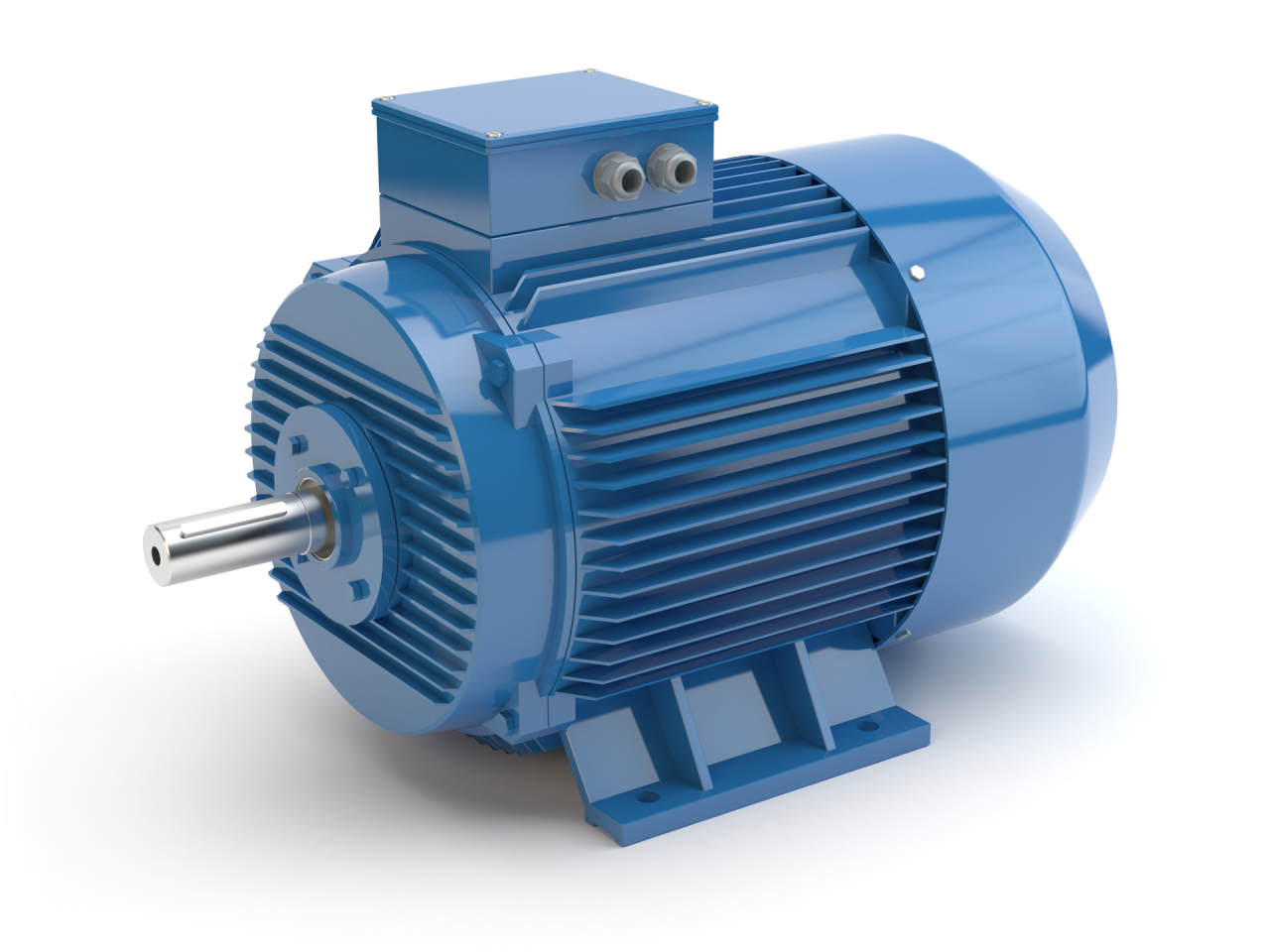
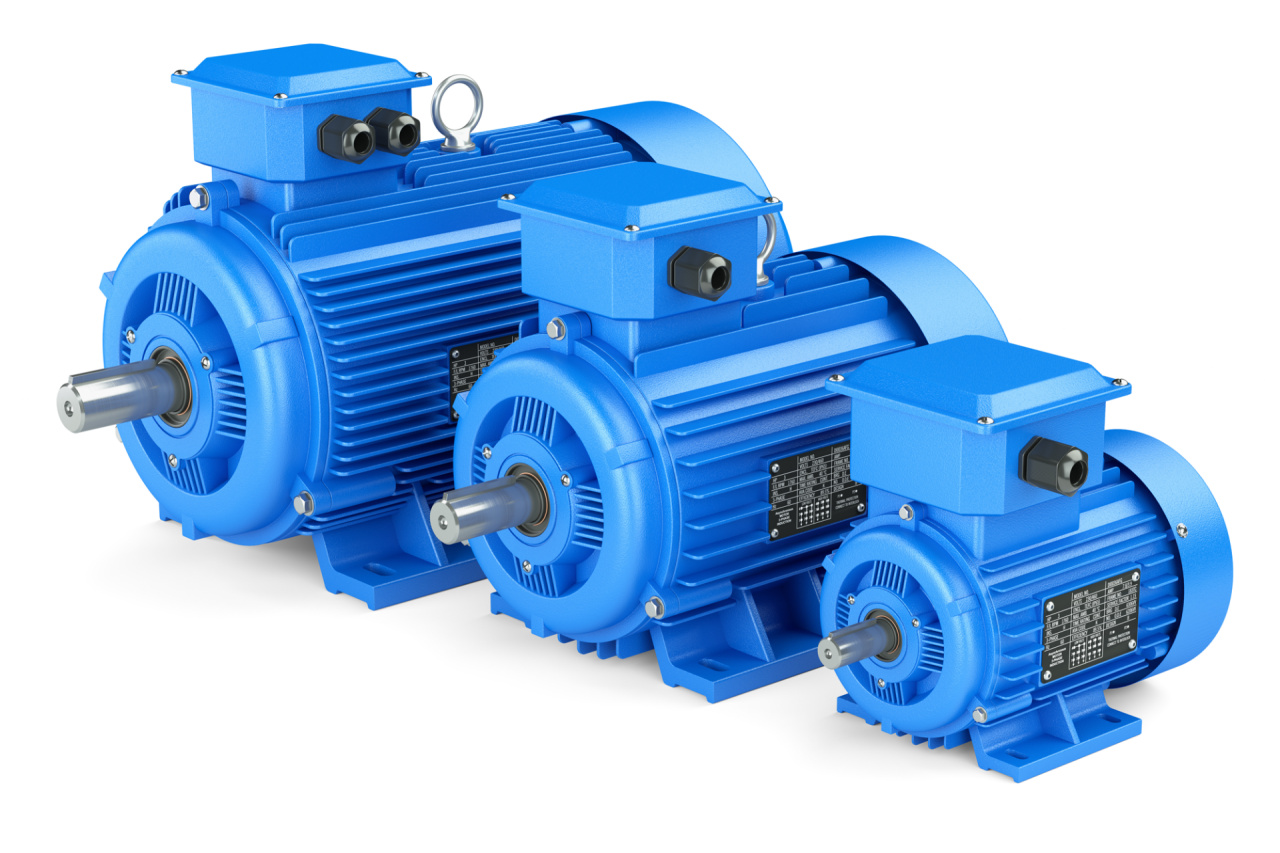
For more information on Power Transmission solutions and to get in touch with one of our ERIKS Motor Specialists or Power Transmission Engineers, please contact your local ERIKS Service Centre, who will be happy to discuss your options.
#Motor #Motors #MotorLegislation #Legislation #Engineering #ERIKS #LetsMakeIndustryWorkBetter