In this article
Cereal Winners!
Weetabix operates at an immense scale, producing a staggering number of cereal products at its Burton Latimer and Corby sites. With 12 production lines, the company churns out 864 biscuits per minute per line, amounting to nearly 15 million biscuits daily!
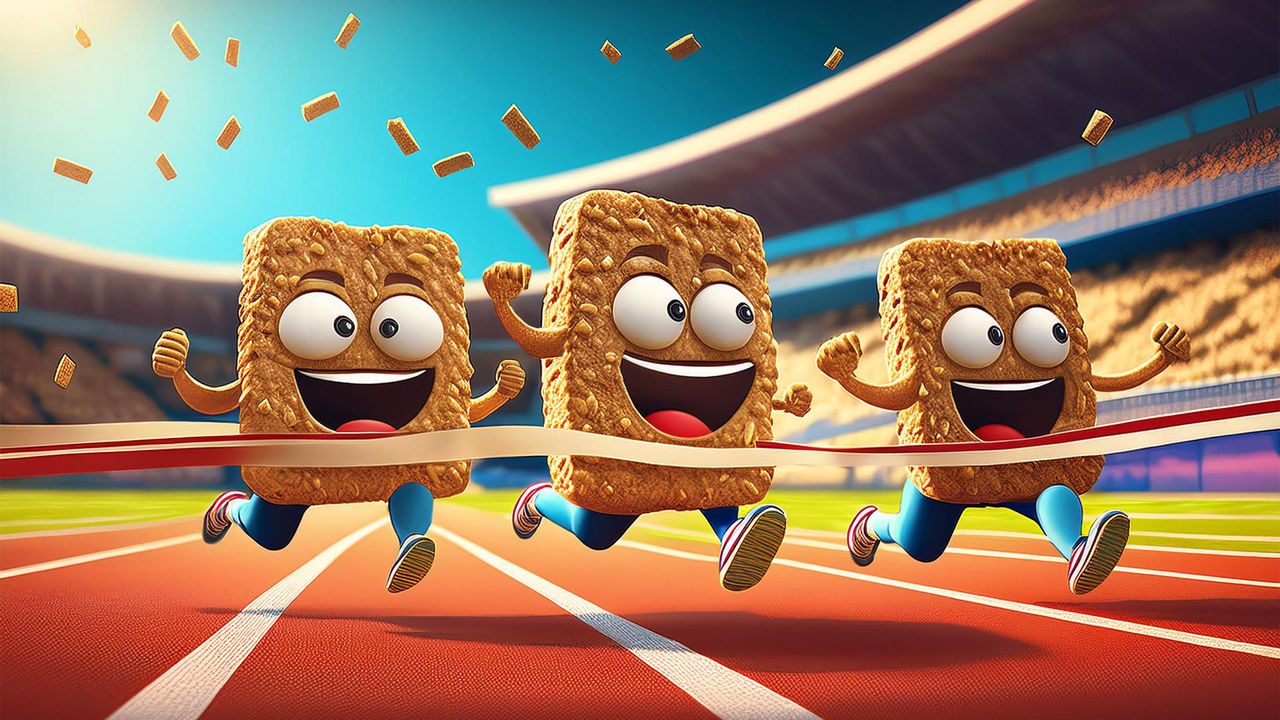
In addition to the classic Weetabix biscuit, the sites also manufacture other products like Alpen, Ready Brek, Weetos, and Alpen bars, as well as Weetabix ‘on the go’ drinks. To support this massive operation, the Weetabix engineering and maintenance team comprises 150 members, along with 40 contractors and 12 ERIKS OnSite staff, who handle purchasing and engineering product spend through dedicated Maintenance Repair and Operations (MRO) stores at both sites.
ERIKS has a long-standing relationship with Weetabix, having managed the MRO stores for over 20 years. Despite competitive tender processes, ERIKS has successfully secured the OnSite contract for Weetabix on nearly every occasion. When the most recent contract renewal approached its end, it prompted both parties to revisit their partnership and explore innovative ways to work together.
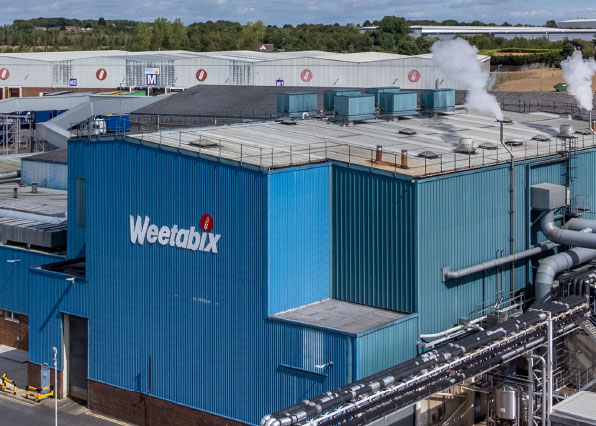
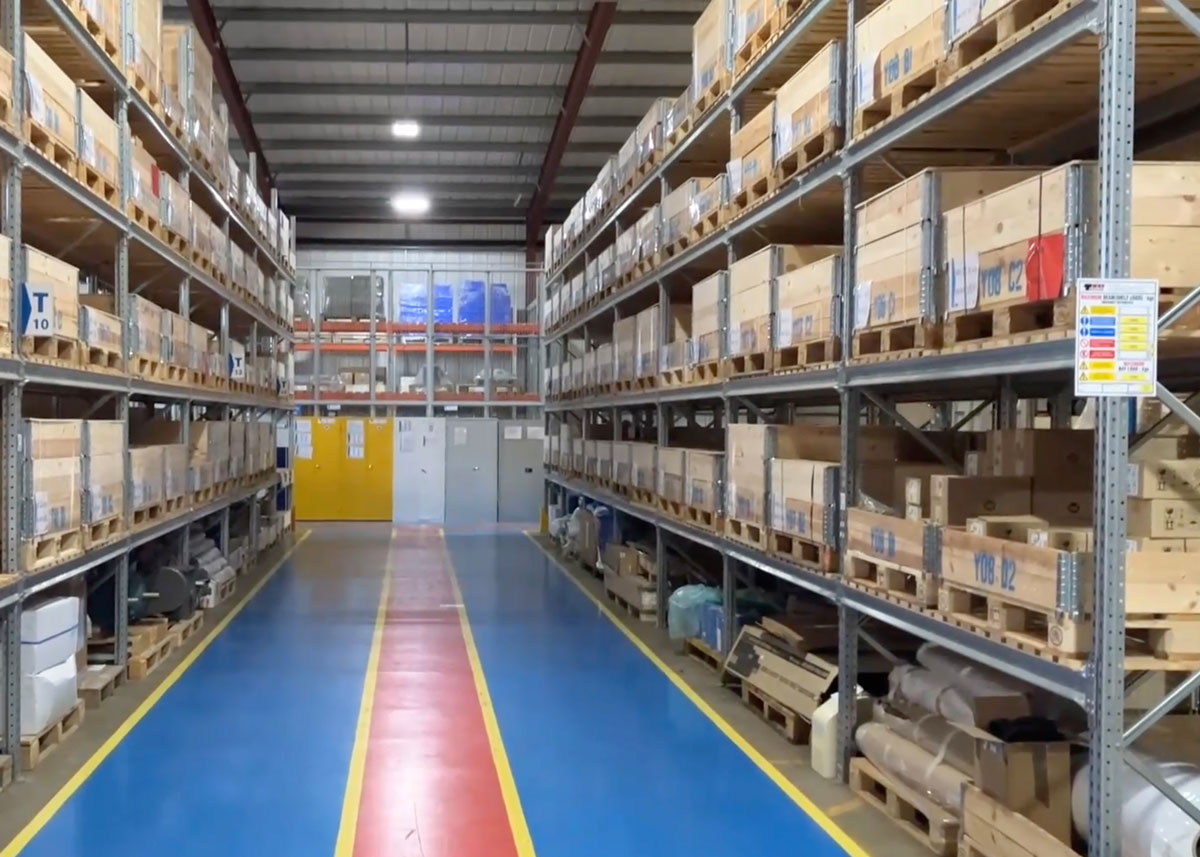
Shared goals and forward planning are essential
In preparation for the contract renewal, ERIKS and Weetabix took significant steps to align their business strategies. Adrian De-Gare Pitt, ERIKS’ Regional Operations Manager, and Sava Mirkovic, Weetabix’s Facilities Manager, collaborated closely to ensure ERIKS’s services would meet the evolving needs of Weetabix. This alignment focused on shared goals and forward planning to effectively support Weetabix’s production demands.
One of the key improvements ERIKS introduced was the identification of ‘Priority 1’ requests, which are crucial for preventing production line stoppages. This proactive approach involved direct communication with suppliers to expedite the delivery of essential parts, ensuring that Weetabix’s operations ran smoothly. As Mirkovic noted, “Shared goals and forward planning are essential.”
Safety and operational efficiency are critical
Safety has always been a top priority for Weetabix, and the partnership with ERIKS has seen a renewed focus on managing critical safety spares. Together, they have implemented visual controls to manage these essential safety components, enhancing both safety and operational efficiency.
The introduction of new Key Performance Indicators (KPIs) has also played a crucial role in improving transparency and efficiency. By closely monitoring monthly expenditures, Weetabix has successfully reduced costs with external suppliers, as engineers now rely more on ERIKS for their needs. This has resulted in more efficient operations, with a clear focus on critical needs. Mirkovic emphasized, “ERIKS is integral in moving our business forward.”
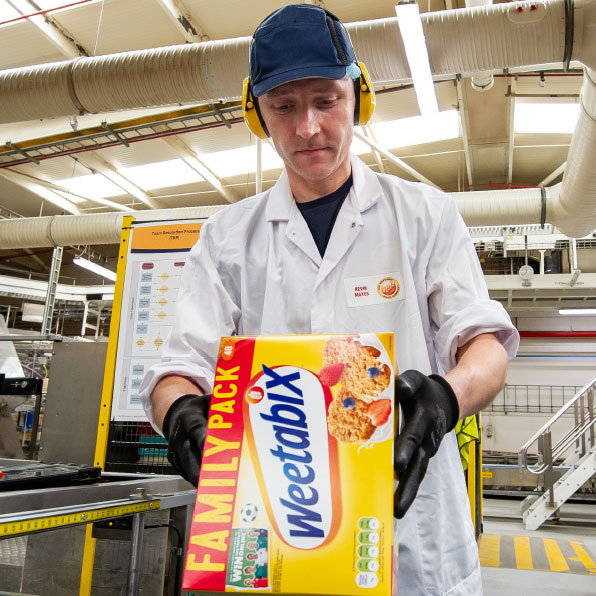
Another key aspect of the renewed partnership is improved communication. This has fostered a more collaborative and proactive relationship, allowing ERIKS to better understand and address the needs of Weetabix’s engineering teams. Additionally, Alison Blakey, ERIKS’ Customer Operations Manager, now regularly attends Weetabix’s engineering team meetings, providing tailored support that strengthens the partnership.
The renewed contract between ERIKS and Weetabix marks a new chapter in their long-standing relationship. Both parties are committed to continuous improvement and innovation, with a strong focus on achieving common goals and enhancing operational efficiency.
For more information on ERIKS OnSite Solutions, contact your local ERIKS Service Centre, who will be happy to discuss your options.
#ERIKS #LetsMakeIndustryWorkBetter #MRO #OnSiteSolutions #OperationalEfficiency