In this article
Don't get caught in the steam trap
The cost of producing steam, and steam's value to production processes, is well known. Yet too many industrial sites still have steam traps which are wrong for their application, faulty, incorrectly installed, leaking, or completely non-operational. An expert Steam Trap Survey can reveal the problems and offer solutions and cost-saving opportunities too.
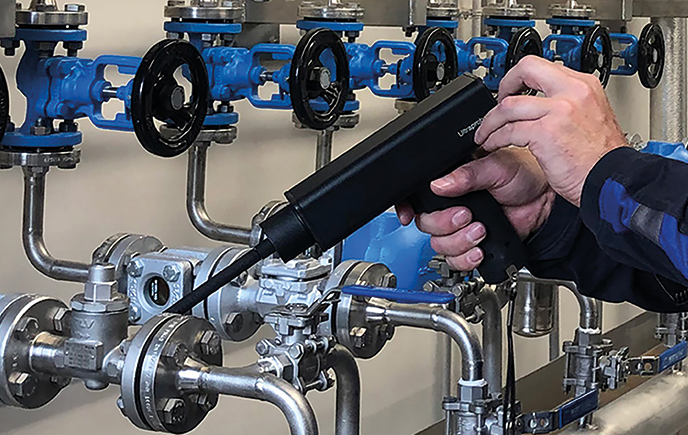
When steam traps are appropriate for the application and operating efficiently, you can expect to see anything from a 10-30% reduction in your fuel costs. For example, the ideal return temperature for a hotwell is 90°C. If your returned condensate is cooler than this, you're wasting energy and money to reheat it.
Every 6° your returned condensate rises in temperature will deliver a 1% energy saving. So an improvement from 70°C to 90°C will represent a 3.33% energy saving.
Taking a closer look
Inefficiencies in your steam systems are like steam itself: hard to see and impossible to pin down. Yet ERIKS' expert engineers have quantified partially leaking traps on some customers' sites as costing over £10,000 a year in wasted energy.
As well as increased costs and reduced manufacturing process efficiency, inefficient or ineffective steam traps can also lead to water hammer, which can cause serious damage to other equipment, and can even be a safety risk.
Water in the condensate return lines can also lead to a build up of corrosion. And steam leakage can increase pressure throughout the condensate network, making it harder for all of the steam traps to drain condensate, with knock-on effects on processes.
The sheer number of traps and their locations can make it challenging to carry out a survey. But the consequences of failing to do so means the need can't be ignored.
Trapping the measurements
Gathering and interpreting steam trap performance figures is a skilled task.
The most comprehensive, useful and accurate measurements will be obtained by specialist engineers with appropriate equipment, such as ultrasonic measurement transducers. The EX UE 2000, for example - as used by ERIKS' engineers - can produce vibration, sound and frequency readings.
Additional information can be provided by an infrared thermographic camera. This can build-up an image of the temperature gradient over a single component - such as a steam trap - or along a section of pipe.
Full steam ahead
A Steam Trap Survey by experienced ERIKS Condition Monitoring engineers not only reveals leaks or other inefficiencies in your steam system. It can also highlight opportunities for energy- and cost-savings, and efficiency improvements.
The Condition Monitoring team has an understanding of systems and components beyond the steam system alone. So as well as knowing the issues that arise with steam, they also understand the wider implications for your processes and systems, including pumps and valves. They can identify root causes of problems, and highlight potential changes to individual components or the wider system to increase efficiency, save energy or reduce costs. And they can propose system improvement projects with quantified paybacks. This service will be available in the Spring.
ERIKS has its own-brand EconⓇ range of flow control products, but also offers many other leading brands. Together with ERIKS' repair and replace capabilities, this means any proposals are solution-neutral and made with complete brand impartiality.
Once the survey is complete, ERIKS will produce a detailed and comprehensive report which the engineers will talk through with the customers. They'll highlight problems and risks, and identify opportunities that can help the customer to make more of steam, for less.
As well as reducing energy use and costs, condensate recovery with effective steam traps can:
- Reduce water use and costs
- Lower emissions. Less energy use means lower levels of CO2, NOx and SOx emitted into the atmosphere
- Reduce safety risks. Fewer vapour clouds leads to less build-up of water on the ground, which can be a slip hazard
- Reduce blowdown. This in turn reduces water and energy wastage
- Prevent corrosion - as a result of improved feedwater qaulity. This can improve efficiency and lengthen component life throughout the whole system, not just in the boiler itself.
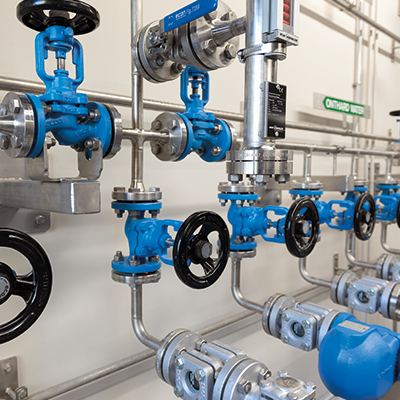
Cheese factory in a pickle
Until ERIKS carried out a Steam Trap Survey, a cheese factory in the Midlands was unaware of the sizeable emissions it was producing and the substantial losses it was incurring from its steam systems:
- Co2 emissions - 32 tons p.a.
- Energy loss - 121MW p.a.a
- Steam loss - 180 tones p.a.
Total cost of steam loss over £6,700 p.a.
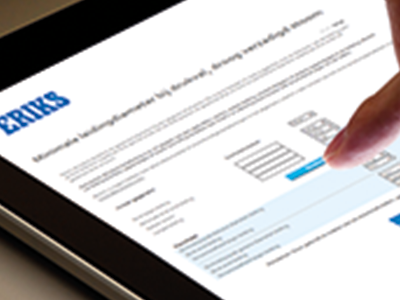
For more information to get in touch with one of our ERIKS Fluid Power, Transfer and Control Specialists please contact your local ERIKS Service Centre, who will be happy to discuss your options.
#ERIKS #LetsMakeIndustryWorkBetter #Steam #Valves #Maintenance #Specialism #AssetManagement