In this article
Have You Overlooked Your Industrial Hose?
Whatever the industry, it’s impossible to eliminate all risks. COMAH regulators know that’s the case, but they still want you to do everything you can to reduce the risk to as low as reasonably practicable. So, if you’ve overlooked or underestimated the potential hazard of static build-up and sparking from your hoses, then you’re falling short.
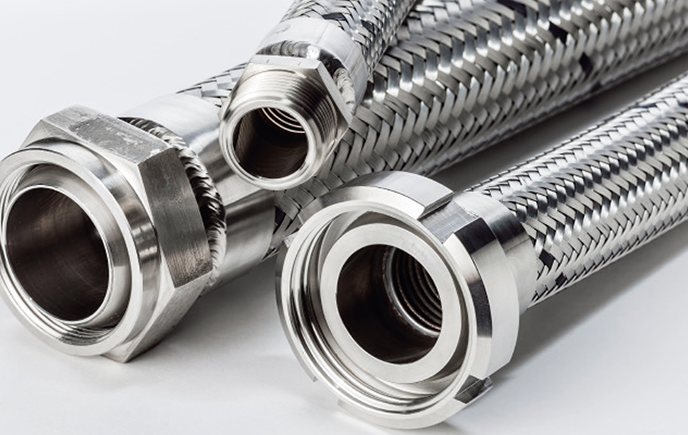
One spark is all it takes
Where flammable chemicals are concerned, all it takes is one spark to turn a working day into an accident. You’ll be taking all the usual precautions in all the obvious places, but have you overlooked your hoses?
Few people think of hoses as critical to applications, and even those who do may not have thought beyond process hoses. Yet any hose – whether it’s a process hose with chemicals flowing through it or a commodity hose for air, water or steam – will be a potential source of static charge build-up, with the potential to cause a spark on discharge.
So, all your hoses need to be able to conduct that charge away, to prevent sparking.
Goodall Conductive Hoses were the first to be designed to do this for a broad spectrum of chemicals. Almost 50 years later, the latest Goodall Kemflex hose is the benchmark for construction and safety.
Conductivity at the core
At the core of the Kemflex hose lies a compound incorporating highly-conductive carbon black particles. These create a pathway for the safe dissipation of any static charge, reducing the risk of a spark.
The Ultra High Molecular Weight Polyethylene (UHMWPE) central tube is surrounded by high tensile braids. These offer more resilience than a spiral construction, while enabling flexibility and providing kink resistance. Around this central tube is an EPDM outer cover, resistant to abrasion, chemicals and ozone.
Exceeding the European norm EN 12115, Kemflex is long-lasting – helping to reduce your Total Cost of Ownership. But above all, it meets the demands of COMAH and your requirement to take “all measures necessary” for safety.
Single pass, or fail
Another important safety consideration for hoses is the avoidance of leaks. In their Metal Visor hoses, Goodall has developed an innovative manufacturing technique to reduce risk.
Most metal hoses are welded once for crimping then again for fitting the attachment. Each time the hose is heated for welding, microfractures and impurities are introduced – each a potential source of leakage. Additionally, every heating event extracts chromium from the stainless-steel, reducing its corrosion resistance. When the chromium content falls below 12%, there’s a risk of oxidation and corrosion, leading to leakage.
Goodall Metal Visor hose overcomes these problems by using a single-pass welding technique, which reduces the amount of heating, as well as avoiding gaps and burrs between the hose end and fitting.
Perfect fit for purpose
Leak-free fitting and complete compatibility between hose and accessories is standard because Goodall manufactures not just the hoses but the ferrules and fittings too.
Goodall service also includes expert advice on matching the fitting to the hose, for leak-free performance whatever your application.
Read the Complete Article: Know+How Magazine Issue 37 Aggressive Environments
For more information on Hose solutions and to get in touch with one of our ERIKS Fluid Power, Transfer and Control Specialists please contact your local ERIKS Service Centre, who will be happy to discuss your options.
#Goodall #ERIKS #LetsMakeIndustryWorkBetter #IndustrialHose #Chemical #Safety