In this article
Is Your Filtration Solution Hiding Horrors?
We all know that there are many hidden horrors in our factories and plants. They are often overlooked, undervalued and pushed aside when maintenance teams have to react. But can a simple health check save you money and precious time?
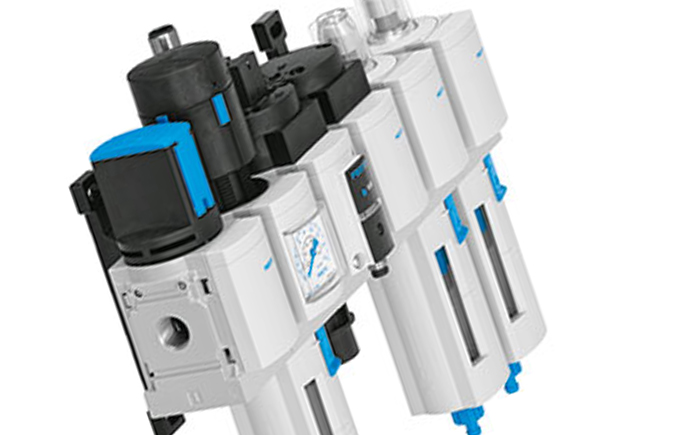
Recently ERIKS were asked to visit site and look at a “total” filtration solution for a radiator manufacturer who were experiencing several problems and issues on site. They included obsolescence on parts, some of which had not been used for over 10 years, and if a breakdown was to occur there would be an even longer delay in repair.
We conducted an initial survey to identify and create a working log the various units.
From the survey it became apparent that a number of issues had arisen from our findings, which included energy loss i.e. leaking auto drains and empty lubricators with no oil. There were also broken gauges on site which we were unable to take any substantial readings from, which left us unable to inform the customer if there were any pressure discrepancies, and whether his air lines were over or under pressure.
Overall the factory was suffering from a poor filtration quality on its current set up and carried a large number of unused spares, there was no standardisation of preferred brand/supplier which resulted in too many variations and stocking issues. To help correct this issue ERIKS documented all the filter regulator and lubricator sets, the sizes etc. which we found to have approximately 150 sets which ranged in size from ½” up to 1½” in port size.
Standardised for savings
First of all our priority was to try and standardise on one brand, reducing the number of spares carried. Secondly we introduced our supply partner Festo into the process. Festo were chosen as they could offer a suitable range of air saving units which met the customer’s needs, and were able to cross reference the existing parts over to the MS6 and MS9 range or air preparation sets. The air preparation units were of a modular design and offered varying connector plates to suit the different size pipe work, eliminating the need for much engineering re-work which could delay the process.
In addition to all the above there was an opportunity to reduce lower pressures at certain points in the operation delivering further savings to the customer. A report calculating the savings achievable by dropping the pressure from 7 bar (factory standard) to 6.5bar, 6 bar and 5bar over a 5 day period and based on a 16 hour shift showed a potential annual cost saving in the region of £68,000.
For more information on Fluid Power, Transfer and Control Solutions and to get in touch with one of our ERIKS Specialists, please contact your local ERIKS Service Centre, who will be happy to discuss your options.
#Festo #ERIKS #LetsMakeIndustryWorkBetter #Filtration #Solutions #Savings