In this article
How to Prepare Your Air
You know the expression that genius is 1% inspiration and 99% perspiration? Well, compressed air is 100% preparation for 0% condensation. And 0% dirt, oil and chemical contaminants too. Festo has shared with us best practice tips for compressed air preparation.
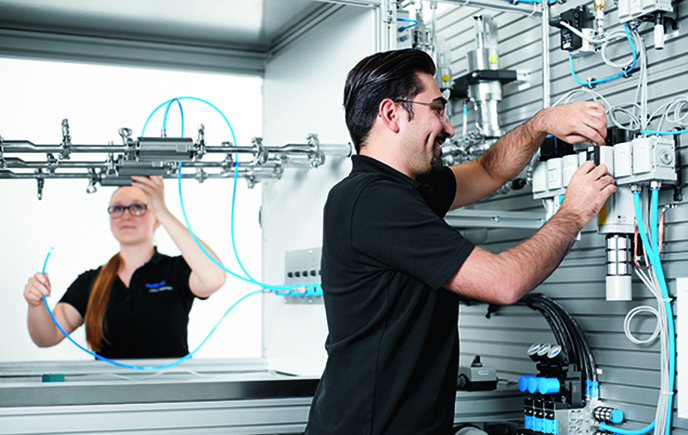
Only the best prepared, driest and cleanest compressed air can ensure the most efficient and cost-effective operation of your pneumatic systems. This will guarantee the longest service life for your pneumatically-operated machines.
So, with compressed air, the key to Best Practice is to start as you mean to go on.
Anything but fresh air
Compressed air is as essential to modern production equipment as fresh air is to humans. Versatile enough to be used across a huge range of applications, it combines speed, power, precision and safe handling.
But even though fresh air is good enough for us, in its natural state it’s not good enough for compressing, because it’s anything but fresh.
Just one cubic metre of unprepared ambient air contains up to 180 million dirt particles, 80g of water (at 50°C; amount depends on temperature), 0.03mg of oil, and various chemical contaminants. These can lead to mechanical friction within machines, corrosion, and blockages.
For systems in the food and beverage industries, the cleanliness of the compressed air used is even more important when the air is part of the process or comes into direct contact with the product.
However, in any industry sector where compressed air is used as a source of power, maintaining the efficiency of the compressed air system and optimising the operation and service life of equipment depends on removing impurities before the air enters the system.
Proper air preparation will pay for itself in increased process and product reliability, and increased system availability.
Prepare before…
Problems with compressed air systems tend to arise slowly and go almost unnoticed. If the air is not properly prepared and moisture or particles enter the system, the resulting corrosion, friction and reduced efficiency will take time to show themselves. Then all too often, even when they are evident, the response isn’t to resolve the cause but to tinker with the effect.
Instead of improving the air preparation upstream, operators may simply increase the compressed air pressure at the machine. The machine returns to its specified operating parameters, but at the expense of higher levels of compressed air usage and lower energy efficiency, all leading to an increase in energy costs. Most importantly, the effects of poor air preparation will not remain hidden for long and will re-appear as the same contamination and moisture is feed through your systems.
In fact, if heat energy and other losses in the system are unrecovered at the start, the energy efficiency of the compressed air process can be as low as 15%. That’s why it’s essential to utilise efficient processes upstream of your machines to prepare the air properly for use. Next, it’s important to consider the correct air preparation equipment at the machine level to allow you to fully realise the true benefits of pneumatics.
Maintain after…
If you were walking through your factory and saw oil or water leaking from a pipe, or saw sparks from a loose electricity cable, you wouldn’t ignore it. But if there’s a gentle hissing as you walk past an air line, most people would probably keep walking, if they even noticed the noise at all.
That’s why, no matter how well-prepared the compressed air may be upstream, it can still lose efficiency downstream through unresolved leaks or other causes. As the symptoms can be rectified by increasing the pressure at the machine, the problem may be left unattended for a long time.
It’s not only obvious leaks which can lead to inefficiency.
A poorly designed system, with excessively long lines, too many branches, or radii which are too small, can suffer reduced flow rates and require extra energy to deliver the required pressure. Old or damaged lines may not leak but could have rough internal surfaces or contamination which slow the flow. Cross sections and connections which are too small will also restrict the flow and reduce pressure.
Even a system which was well-designed to begin with can become inefficient if it’s extended or as more connection points or consuming devices (valves, filters, drying units) are added. It is vital to understand the function of the pneumatic circuit within your machine and adjust flow rates or operating pressures where needed.
So, it’s not only important to prepare the air properly before it enters the system. It’s also important to maintain the system, and even to overhaul its design if necessary, for optimum operational efficiency.
The new pneumatics
Even though compressed air is a long-standing, highly-developed and essential part of production operations, Festo are still making improvements and enhancements. For example, smart sensors are now being integrated into Festo pneumatic systems to improve monitoring of pressure and flow. Not only does this make your machine information easily accessible, it also allows actions to be implemented within your systems to actively start reducing your energy costs. Further advancements in pneumatic technology use intelligent components with integrated software control to allow for far greater control and flexibility within pneumatic systems.
Wherever energy efficiency and process reliability are important, the future of pneumatics looks promising. But for machine reliability and extended service life it’s more important to look backwards – to where the process begins with air preparation. Otherwise, if you fail to prepare, you can prepare to fail.
Air Preparation Tips
- Keep it Clean - Removal of particles, water, oil and other contaminants will increase equipment life and maintain optimum pressure.
- Think Three Choose your service unit based on compressed air purity, flow rate and correct pressure for your application.
- Dew The Right Thing - Ensure your pressure dew point is 10K below your lowest ambient temperature, to eliminate condensate and reduce corrosion.
- One Step At A Step - Air preparation involves several stages and therefore different modules: for switching on, building-up pressure, filtering, regulating, drying and oiling.
- Avoid the Random - Optimum performance arises from the ideal arrangement of service unit components. Consult a Festo pneumatics expert for advice.
For more information on Fluid Power, Transfer and Control Solutions and to get in touch with one of our ERIKS Specialists, please contact your local ERIKS Service Centre, who will be happy to discuss your options.
#Festo #ERIKS #LetsMakeIndustryWorkBetter #Filtration #Innovation #Air #Solutions #Maintenance