In this article
Having Your Cake and Eating It
Food and beverage manufacturers want to have the best of all possible worlds: optimum cost-efficiency, combined with consistently high standards of hygiene, and exceptional flexibility for product, packaging and pack size variation. When you not only want to make your cake, but have it and eat it too, process and factory automation technology solutions from Festo can help.
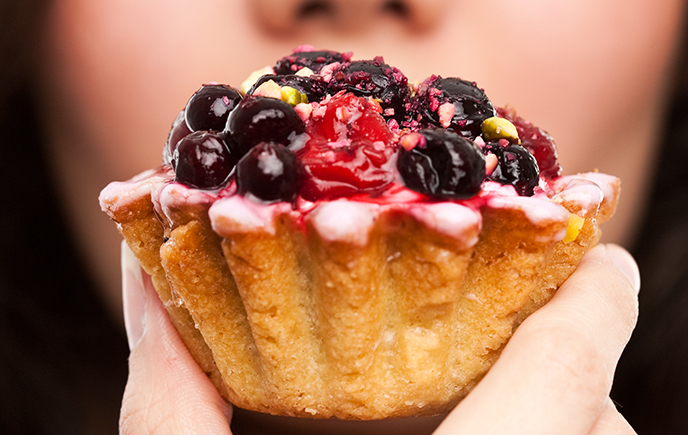
Continuous production processes need to be reliable as well as efficient. The most effective way of ensuring both is through automation – of mixing and stirring, sterilisation, pasteurisation, homogenisation, filtration, dosing, weighing, filling and storage.
Semi-rotary actuators and linear drives, powered by high-quality air prepared to ISO standards, can open and close process valves throughout the plant. The air quality also plays an important part in ensuring hygiene, and in optimising the reliability and life of the control system.
Keep it clean
Automation equipment in food processing splash zones is subject to water splashes, cleaning agents and dripping food – all demanding corrosion-proof drives, valve terminals, proximity sensors and fittings.
If the installation utilises decentralised control, then Festo splash-resistant, clean-design valve terminals (CDVI) and individual valves (CDSV) should be considered, because they can be installed close to the drives without a protective control cabinet.
Clean-design (CDC) cylinders are also suitable for these areas, as they lack the sharp edges and corners where dirt residues or germs can hide. If process installations need additional guidance, guided cylinders (DGRF) are also available.
Of course washing is essential to remove dirt and debris. But it can also remove grease – which is usually the death knell for an actuator. However, a dry-running seal option prolongs the life of actuators even when the factory-installed grease is completely washed away. The lubrication and seals have FDA certification, and all accessories – such as proximity sensors – are optimised for the environment, and resistant to cleaning agents, heat and mould.
All-round performer
The Festo star performer in food zones is the stainless steel round line ISO cylinder (CRDSNU).
Its gently rounded profile makes it easy to clean, and its unique, self-adjusting PPS end position cushioning saves huge amounts of time during set-up and maintenance.
Put to the test in the extreme environment of a salmon sorting machine, these cylinders more than proved their worth. Continually subjected to humidity, salty sea water and fish extracts, and cleaned daily with strong chemicals, a standard actuator would fail in just a few weeks. However the Festo CRDSNU has been proven to provide long, reliable, lifetime performance.
Signed, sealed, delivered
One seal doesn’t fit all environments. So the Festo modular seal toolbox offers a choice of drive seals to suit different harsh environments.
Options include:
- FDA-compliant seals for food use with standard cleaning regimes
- Seals for unlubricated and intensive cleaning
- FKM seals for elevated temperatures up to 120°C and acidic environments
- Hard scrapers for temperatures down to -40°C and for a variety of harsh applications – including sugar crystals, honeycomb and icy fish scales.
Expertly handled
Festo provide a wide variety of handling solutions for the non-food zone, with drives to suit applications in packaging, labelling, testing and monitoring.
With more than 30,000 standard Festo products to choose from, and servo-pneumatic, electric and pneumatic technology options available, there’s no handling application which can’t be satisfactorily and efficiently automated.
Systems are delivered ready-to-install, meaning less work, reduced system design costs, simplified procurement and lower process costs.
“Fit-and-forget is our objective,” explains Andrew MacPherson, Industry Segment Manager for the UK food and beverage industry. “No two handling systems are the same – ranging from simple pick-and-place systems to linear, cantilever or 3D gantries, and dual rod, kinematic Tripod robotic systems. But all our customers have to do is describe their handling task and we’ll eliminate complex commissioning by delivering a plug-and-work solution directly to their installation cell.
Nothing half-baked
With waste and energy reduction being high priorities for most manufacturers, it’s increasingly important to take a comprehensive overview of production, maintenance, condition monitoring and energy-saving, throughout the production process.
Less machine downtime, and detecting and eliminating leaks in compressed air systems, are both crucial ways to save.
Choosing state-of-the-art Festo automation technology is one way food and beverage manufacturers can optimise productivity, cost- and energy-efficiency, hygiene and food safety.
And the result for profitability? A bigger slice of the cake!
For more information on Pneumatic solutions and to get in touch with one of our ERIKS Pneumatics Specialists, please contact your local ERIKS Service Centre, who will be happy to discuss your options.
#FESTO #ERIKS #LetsMakeIndustryWorkBetter #Pneumatics #Automation #FoodAndBeverage