In this article
Festo help to make air that's good enough to eat!
Compressed air is an essential part of the diet of any production facility – and the food manufacturing sector is no exception. In fact this sector uses compressed air in three different ways, making it more important than ever to ensure the air is produced efficiently, and used effectively.
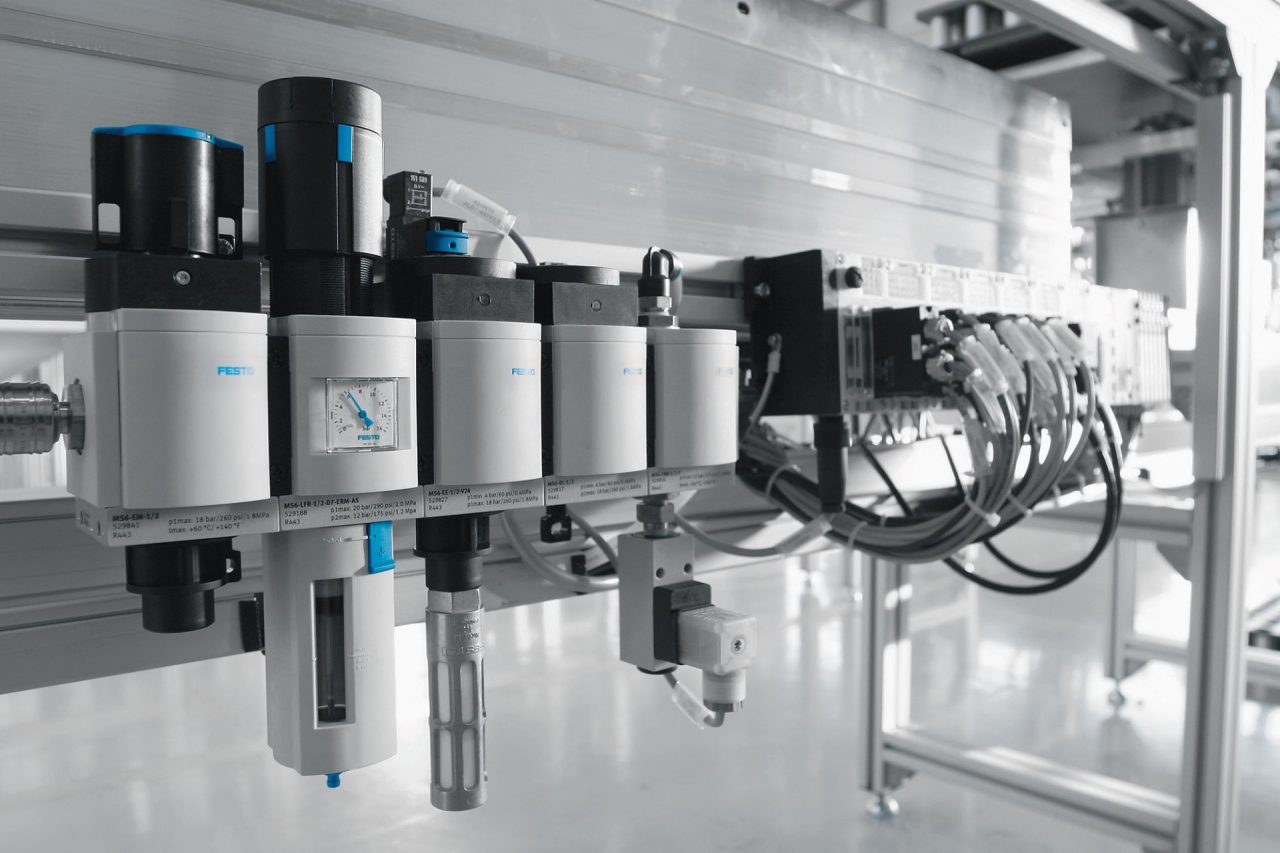
Like most other modern manufacturers the food industry firstly relies on compressed air for its pneumatic systems. Secondly, some processes within the industry involve compressed air coming into contact with food itself. And thirdly – where air cleanliness is most critical – some food manufacturing involves direct injection of compressed air into food (known as flocculation).
These three different uses demand three different levels of compressed air purity which, using their practical experience in the field, pneumatics manufacturer Festo has categorised [see box-out].
However, some compressed air users are incurring unnecessary costs by cleaning their air to the wrong level, in the wrong place, at the wrong time.
Cleanliness where it counts
One cubic metre of unprepared ambient air at 50°C contains up to 180 million dirt particles, up to 80g of water and up to 0.03mg of oil.
These can cause corrosion, friction, mechanical damage, blockages and long-term consequences such as higher maintenance costs, malfunctions, shorter service life and higher energy costs. In food production, if any of these contaminants find their way into end products, the consequences can be even more severe: from fines to reputational damage.
So if you use compressed air anywhere in your manufacturing process, you’ll be well aware of the need for it to be clean. But where and when should you clean it for the greatest cost-efficiency?
Make a clean start?
Many food manufacturers clean their compressed air in the compressor house, to food- contact levels of cleanliness. This not only means they’re having to use more energy to achieve the required flow rate through these upstream finer filters. It also means that when the air reaches point-of-use, its pressure could have dropped below the required operating pressure. And most worryingly, by the time the air has travelled through the system and comes into contact with food, it could have picked up all kinds of new contaminants.
To ensure optimum air cleanliness – with the most efficient use of energy, reduced energy costs and a smaller carbon footprint – Festo offers 5 Best Practice top tips.
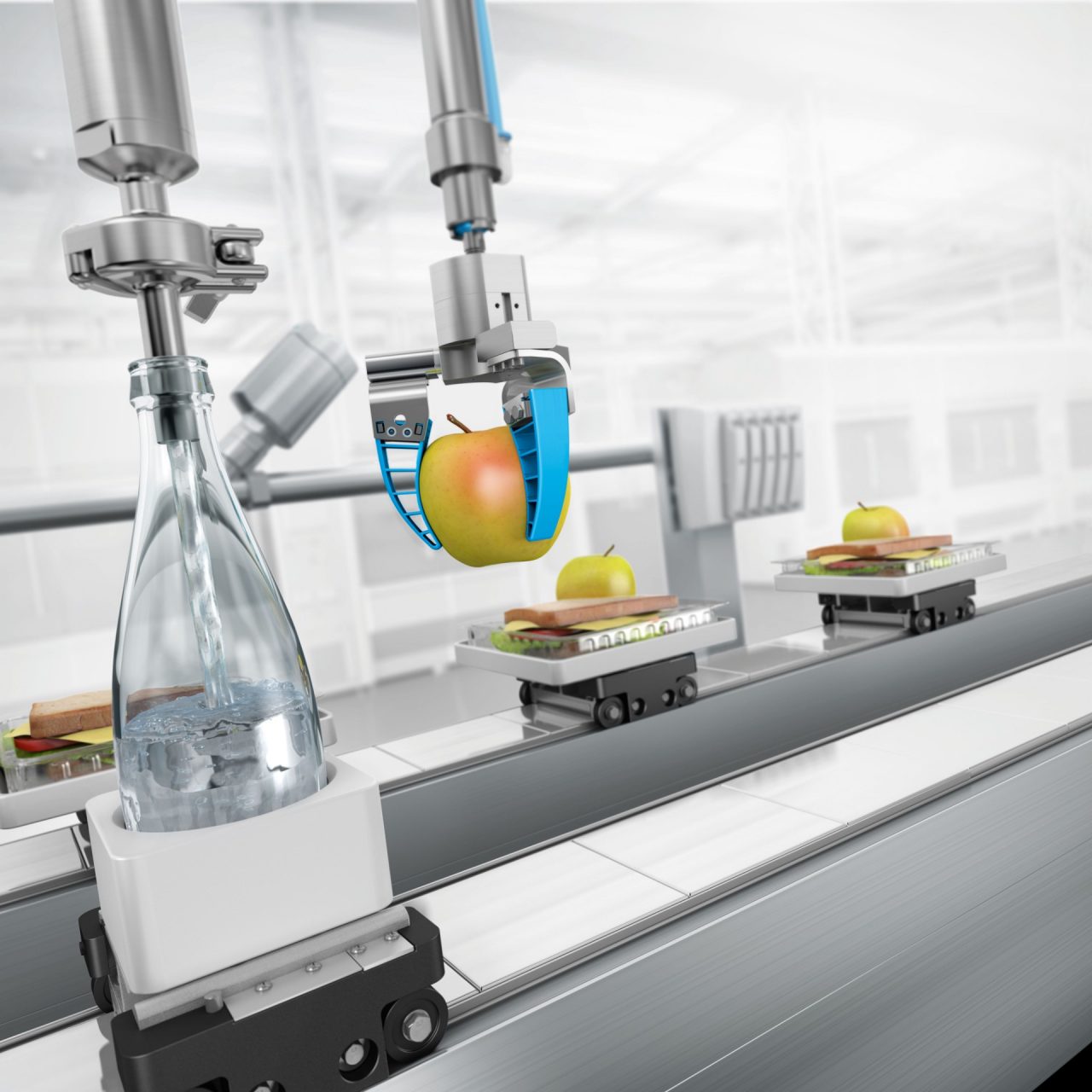
Tip 1 Size and position air preparation units carefully
Filter bowls oversized for the flow rate required by the air preparation unit impair filtration performance and waste money. Using smaller units with coarser filters upstream, and finer filters downstream at point of use, can ensure cost-effective clean air where you really need it.
Tip 2 Drain condensate effectively
Mounting condensate drains within or below filter units will prevent carry-over of extracted liquid into the downstream air flow. This will reduce contamination and corrosion.
Tip 3 Set pressures accurately
Machine pressure is often set by the requirements of only one or two components. Introducing individually regulated pressure zones, or a pressure booster, can allow for reduced pressure and reduced energy use and costs.
Tip 4 Monitor pressures frequently
Gauges with pre-set operating zones enable fast setting and checking of operating pressures, even by unskilled technicians. When over- or under-pressure is easy to see it can also be quick to adjust. Pressure monitoring also makes it easy to see when filters need changing.
Tip 5 Change filters appropriately
Clogged filter elements reduce airflow rates by up to 50%, and fail to remove particulates. Monitoring pressures (see above) and using flow meters will help to identify when it is appropriate to change a filter element. This is a low-cost, simple maintenance task that will optimise performance, minimise pressure drop and reduce energy use.
Or to encapsulate all these tips into one simple, basic rule: clean your compressed air in the right place, with the right filter, to the right level of cleanliness.
For more information on Fluid Power, Transfer and Control Solutions and to get in touch with one of our ERIKS Specialists, please contact your local ERIKS Service Centre, who will be happy to discuss your options.
#Festo #ERIKS #LetsMakeIndustryWorkBetter #Filtration #Innovation #Air #Solutions #Maintenance