In this article
Hiss! Boo!
Hear that hissing noise? Boo! It’s bad news for your energy bill. Can’t hear it? Boo! That’s even worse news. Air leaks from your compressed air systems are obviously invisible, sometimes inaudible, but always an avoidable waste of compressed air, energy and money. A recent Air Leak Survey carried out by ERIKS for Procter & Gamble revealed leaks which were wasting significant amounts of compressed air, and the energy required to generate it. So the survey enabled repairs that saved tens of thousands of pounds.
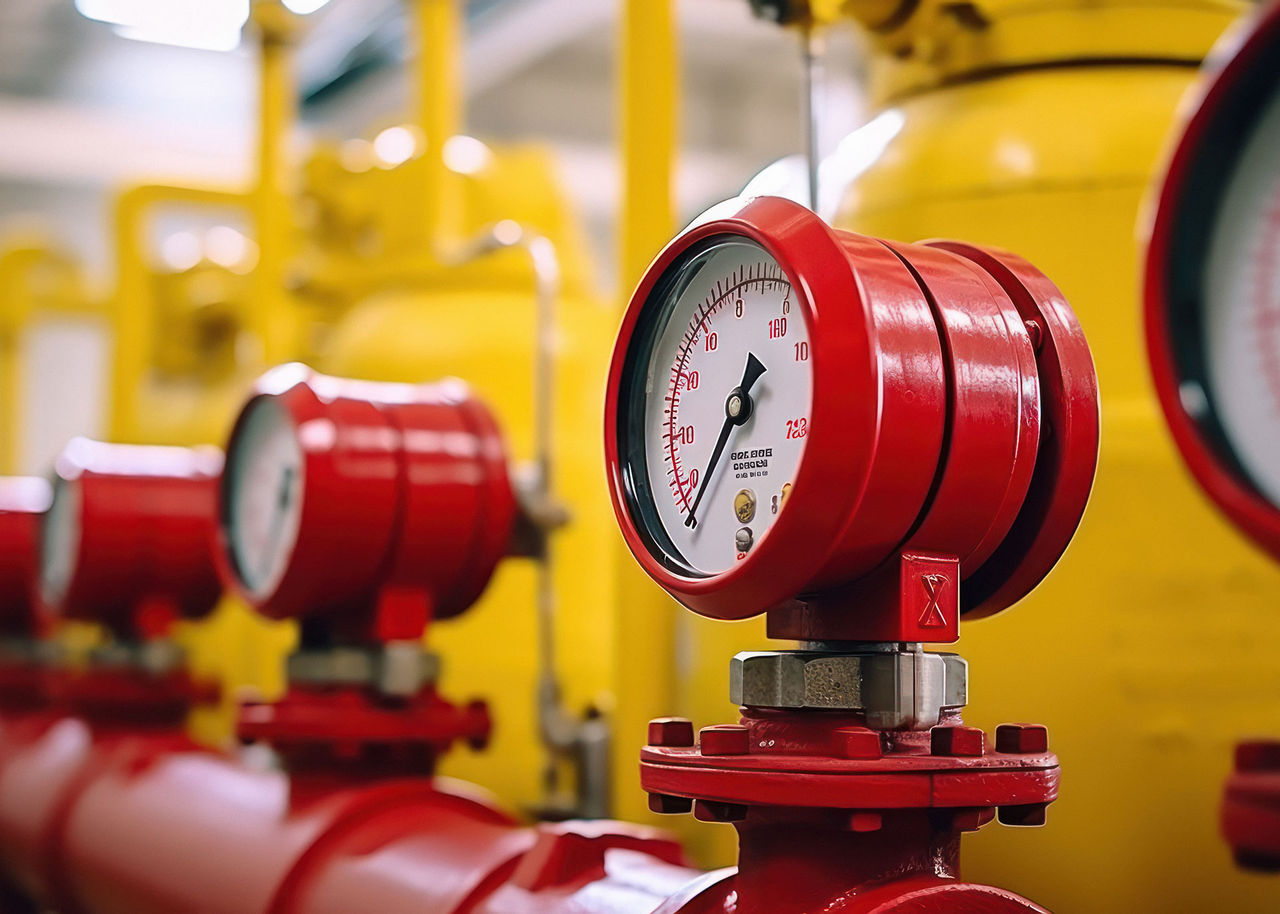
Compressed air is such an integral part of so many manufacturing and production processes, it’s easy to forget about. It’s just there. And even when something goes wrong, it’s still there. It may be leaking, but you can’t tell. It may be costing more to generate because so much is being wasted, but you don’t notice. It may even be reducing the efficiency of your production process – but so gradually you’ve got used to it.
Faced with steadily decreasing efficiency and steadily rising energy bills, anyone would be quick to act. But when it’s ‘just’ compressed air, it can easily slip to the bottom of the to-do list.
However, as more manufacturers set energy-saving KPIs, detecting and resolving compressed air leaks can be a highly effective way to meet – or even exceed – targets. That’s why ERIKS proposed an Air Leak Survey at Procter & Gamble’s washing powder production plant.
More than two ears required
Because most air leaks are inaudible, being a good listener isn’t good enough. It also takes extensive experience of pneumatic air systems, an effective ultrasonic device, and system engineering know-how.
Experience means the surveyor knows the most likely places for air leaks to occur, so knows where to look for them. The ultrasonic detector means they can be quickly and easily detected. And engineering know-how means being able not just to find the leak, but to understand the reason for it – and how to resolve it.
For Procter & Gamble, the survey took just two working days and detected over 100 leaks.
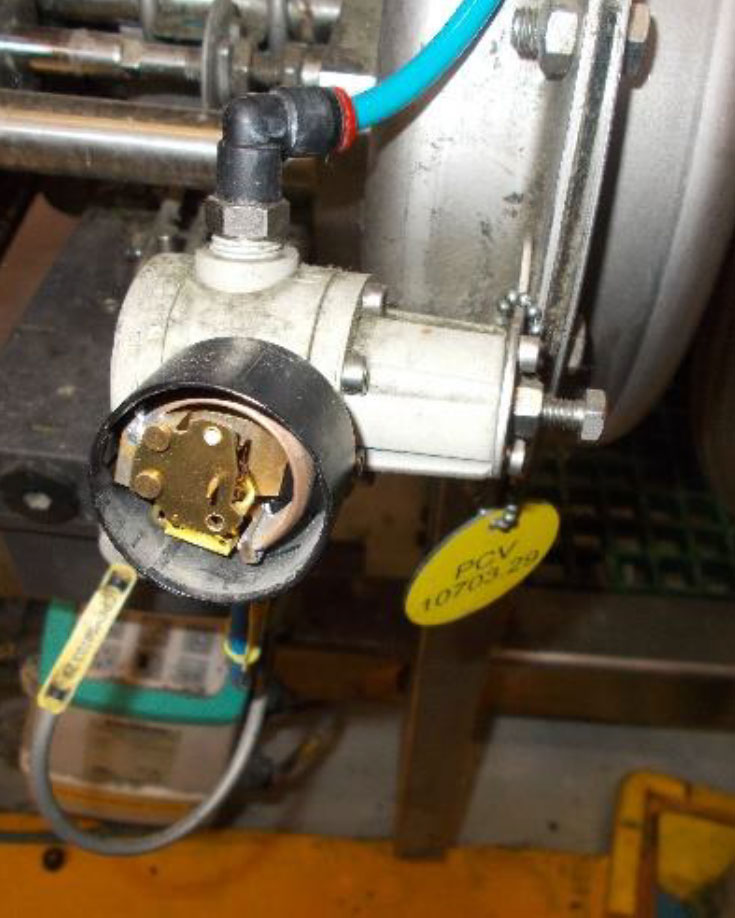
Clearing the air
Sometimes customers find it hard to believe the extent and scale of air leaks in their plant. Or they’re tempted to dismiss them as a minor consideration amongst other, more obvious energy wastage. So the ERIKS Air Leak Survey provides a comprehensive written report of the results, to help clear the air.
The report records the location of each leak, together with a photograph. It also identifies the cause of the leak (for example, poor or incorrect fitting of joints, or poor quality or damaged tubing) and the level of air loss.
Last but not least, it translates each leak into financial terms – because air leaks may be invisible, but their effect on the bottom line isn’t.
Take a deep breath
In Procter & Gamble’s case, the 100-plus leaks detected were allowing a staggering total of £250,000 worth of energy to escape into thin air every 12 months.
However, fixing every leak at once would have been too great a strain on the available in-house maintenance and repair resources, as well as representing a sizeable investment in parts.
So using the detailed information in the ERIKS’ report, Procter & Gamble prioritised the leaks in terms of the potential energy savings generated and their criticality for production efficiency. Their own engineers were then tasked with tackling the leaks which would deliver the most immediate benefits.
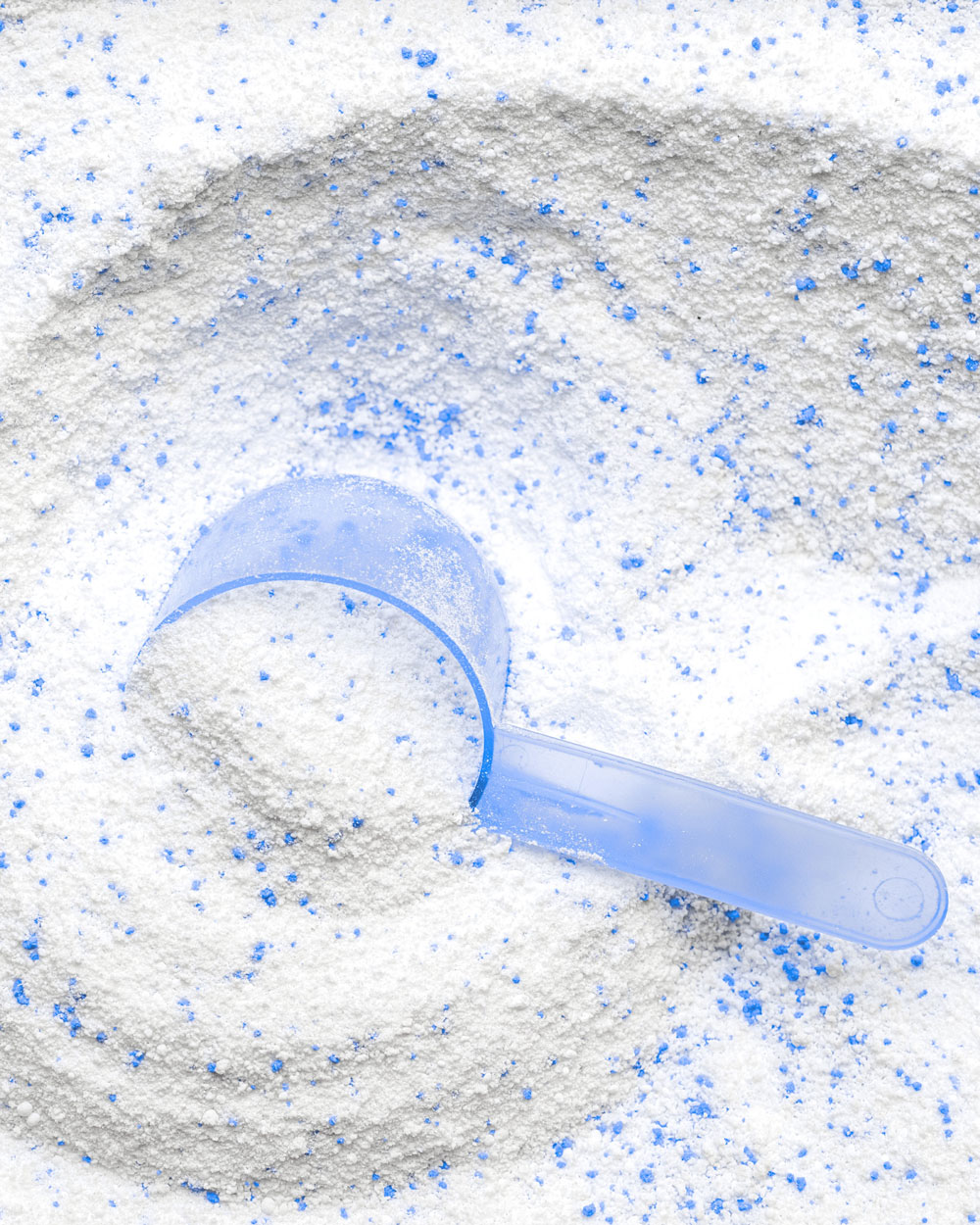
The result has been an initial cost saving of £60,000. And that’s a saving which will not only be repeated year after year, but will increase year-on-year as leaks lower down the list are fixed in turn.
Procter & Gamble spoke highly of the ERIKS Air Leak Survey, describing it as ‘a major step towards [our] energy optimisation goals. It helped shine a light on an area often overlooked, but [which] cost the company and department a lot of money each year.’
But they know that actions speak louder than words. So a survey of another department has already been commissioned and completed – resulting in an additional £50,000 of energy savings per annum – and there are two more booked for next year.
More savings are definitely in the air.
For more information on Fluid Power, Transfer and Control Solutions and to get in touch with one of our ERIKS Specialists, please contact your local ERIKS Service Centre, who will be happy to discuss your options.
#ERIKS #LetsMakeIndustryWorkBetter #AirLeakSurvey #CompressedAir