In this article
Compressed Air Treatment – A Guide to Filtration and Drying
Compressed air produced by a compressor is hot, wet and dirty. It contains water and hydrocarbon/oil vapour, liquid (aerosols) and solid particles. Professional Compressed Air Treatment is the best way to achieve Clean Compressed Air.
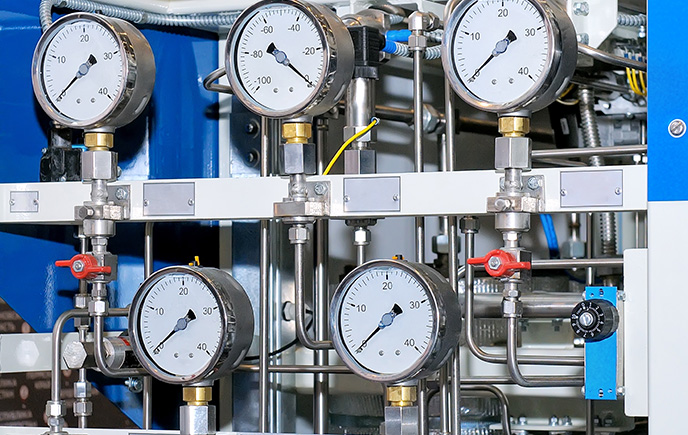
The first step is to understand the sources of compressed air contamination and the types of contaminants which must be reduced or eliminated. This is a key factor in planning an efficient compressed air system.
Water Liquid and Vapour
Water in the compressed air system enters through the compressor intake as a gas (water vapour from the environment).
The ability of air to hold water vapour is dependent upon its pressure and temperature. The higher the temperature, the more water vapour that can be held by the air, the higher the pressure, a greater amount of water vapour is dropped out in liquid form (condensate).
When ambient air is compressed, the gas volume is reduced which causes a reduction of water vapour by condensation. On the other hand, water vapour content per given volume is increasing with increasing temperature. This is the reason that hot compressed air in most cases contains more water vapour per volume than ambient air and is generally “saturated” with water vapour. Air at a constant temperature has a maximum capacity for water vapour for a given volume whether at atmospheric pressure or in a compressed state. As the compressed air cools down, water vapour gradually condenses to liquid water that has to be removed from the compressed air system.
Solid Particles Contaminants
Like water, solid particles exist in all compressed air systems regardless of the type of compressor. These can arise from four principle sources.
- Atmospheric dirt entering the compressor intake
- Corrosion products due to the action of water and weak acids formed by the interaction of water and gases such as sulphur dioxide inhaled by the compressor
- Carbon products formed by the action of the heat of compression on the lubricating oil or the normal wear of the carbon piston rings used in some types of oil free compressors
- Particles of debris originating from the mechanical fixing of the metal pipework and components into the air distribution system
The size of solid dirt particles covers a very wide range from below 1 micron to several hundred and the level of filtration required to remove them depends upon the degree of cleanliness required for the application.
Oil In The Compressor
Oil in a compressed air system can exist in three forms, oil/water emulsions, aerosols/mists (small liquid particles suspended in the air) and oil vapours.
The principle source of oil contamination within a compressed air system is from the compressor lubricant. Oil lubricated compressors may introduce as much as 8 litres per year of oil in to a system.
Oil Contamination
Atmospheric air also contains oil in a gaseous form (hydrocarbon oil vapour) which can be drawn into the compressor intake. The location of the compressor intake may also have an effect and should be carefully positioned away from any sources of pollution such as vehicle and generator exhausts. When the oil vapour enters the distribution system it will cool and condense into a liquid and may combine with liquid water to form an oil emulsion. Oil vapour can taint manufactured products it comes into contact with and when exhausted from the application can make plant operators feel unwell. It is especially hazardous when it is found in compressed air used for breathing air.
Compressed Air Contaminants - A Solution For Every Contaminant
By taking all of these sources of compressed air contaminants into consideration, it is vital that proper and genuine compressed air treatment products/systems are installed to ensure clean compressed air at a quality level as required by the application.
Liquid Oil & Water Removal
General purpose filters (also known as water separators) are used in a compressed air system to remove bulk condensate (water and liquid oil) contamination therefore protecting the downstream particulate and coalescing filters.
General purpose filters will only remove liquids and will not remove water or oil in either aerosol or vapour phase. The filters are designed to remove the water by centrifugal action which optimises the separation efficiency and reduces running costs.
Solid Particle Removal
General purpose filters also contain elements to remove solid particle contamination that originates from the atmosphere and possibly from compressor wear as well as the compressed air pipework and air receiver. They utilise a replacement filter element with a micron rating adequate to remove the solid particles and also act as a pre filter to the high efficiency coalescing filters downstream.
Oil Aerosol Removal
Coalescing filters are used in a compressed air system to remove small and submicron particles, water mists and oil mist aerosols. They are usually installed in pre-filter and after filter combinations and each has its own automatic drain to discharge liquid emulsions to a condensate management system. The filter media efficiently employs the three main mechanisms of filtration: diffusion, inertial impaction and direct interception. IMI Norgren coalescing filters utilise a unique design and construction of filter housings with replacement filter elements that have high dirt holding capacity, low pressure drop and long life with a sub-micron filter rating.
Water Vapour Removal
Clean and dry compressed air is easily achieved with the IMI Norgren HYDRA-D range of desiccant dryers.
Our desiccant air dryers are used for high purity applications where pressure dewpoints of -70,-40 and -20°C are required according to ISO8573.1 humidity classes 1, 2 and 3 respectively.
- High efficiency moisture removal
- Integral inlet and outlet filtration
- Reliable PLC control
- Energy saving option - dew point sensing for lowest possible purge air use
- Replacement desiccant cartridges for quick and easy servicing
- ISO 8573-1 (2010) class 2: -40°C PDP for water and class 1:1 micron particulate
- Alternative dew point settings
Designed for use in the compressor room, at the point of application or integrated into your original equipment, Hydra-D dryers are an effective solution to the problems caused by contaminated compressed air.
For more information on Fluid Power, Transfer and Control Solutions and to get in touch with one of our ERIKS Specialists, please contact your local ERIKS Service Centre, who will be happy to discuss your options.
#ERIKS #LetsMakeIndustryWorkBetter #CompressedAir #Contaminants #Solutions