In this article
Don't Burn Through Efficiency: Why Best Efficiency Point (BEP) Matters in EfW Pump Systems
In the Energy from Waste game, efficiency isn’t a buzzword — it’s your bottom line. Whether it’s feeding fluid to a thermal process or keeping the flue gas system moving, your pumps are doing some serious heavy lifting. But here’s the kicker: if they’re not operating near their Best Efficiency Point (BEP), they’re quietly draining energy, shortening maintenance intervals, and racking up avoidable costs.
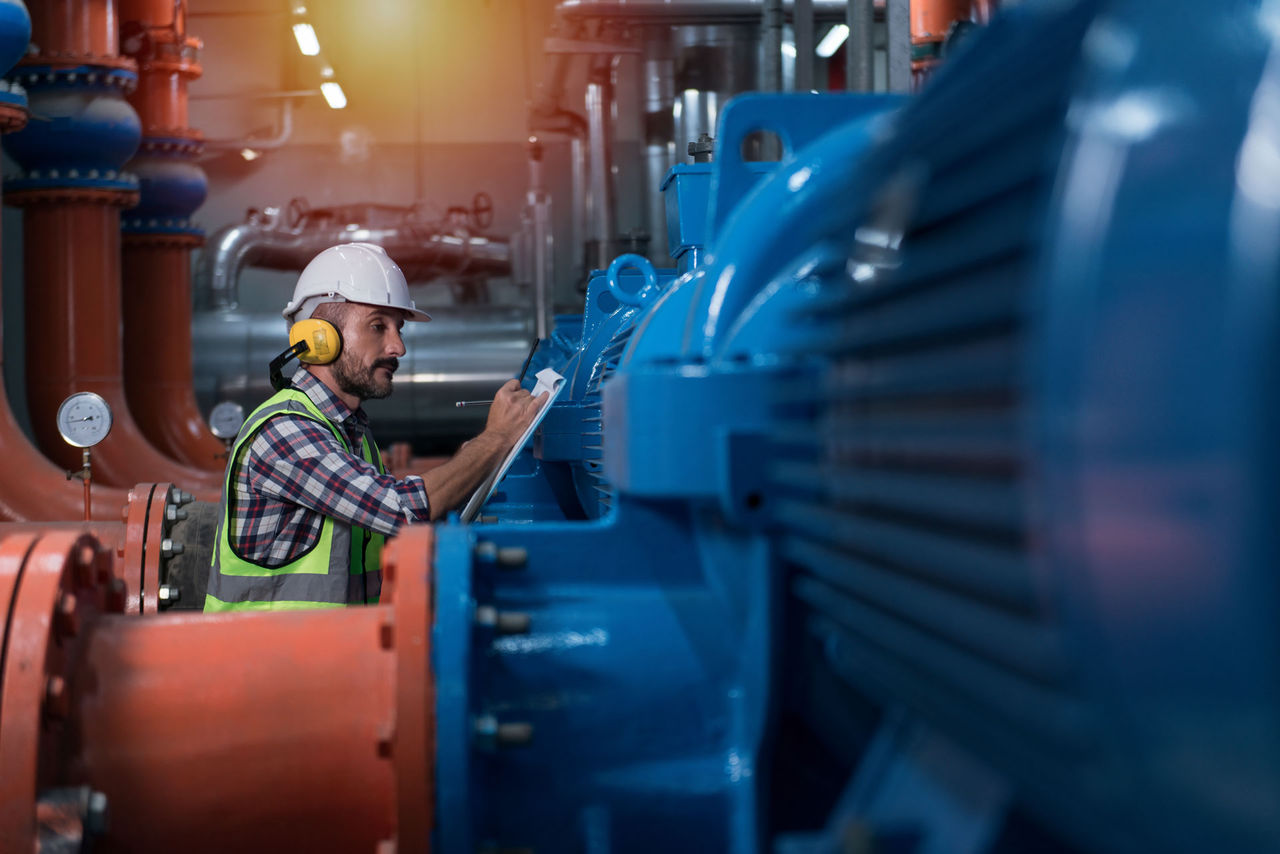
At ERIKS, we’ve worked with EfW plants across the UK, and the same patterns crop up: oversized pumps throttled to fit, variable duty points, and poor visibility into system curve behaviour. You wouldn’t run a turbine blind — your pumps deserve the same respect.
What Is BEP, and Why Should You Care?
The BEP is the point on the pump curve where efficiency peaks. At that sweet spot, your pump moves fluid using the least amount of energy, with minimal vibration and wear. Anywhere else? You’re adding strain — not just to the pump, but to your budget.
EfW environments are tough: aggressive fluids, abrasive particles, temperature extremes, non-stop operation. Running pumps outside BEP in these conditions accelerates fatigue. Bearings wear faster, seals fail, and shafts start flexing. And when a pump goes down in a plant that runs 24/7, it’s not just inconvenient — it’s a potential process bottleneck.
Understanding the Curve: It’s More Than a Line on a Chart
The pump curve maps flow rate against head and overlays key data like power, efficiency, and NPSHr (Net Positive Suction Head required). BEP is right at the top of the efficiency curve — the Goldilocks zone.
But here’s the thing: EfW processes don’t always behave nicely. Fluctuating ash content, variable waste moisture levels, system pressure swings — they all mess with flow conditions. Many pumps are specified with “safe margin” in mind, leading to oversizing and throttling, which pushes operation away from BEP.
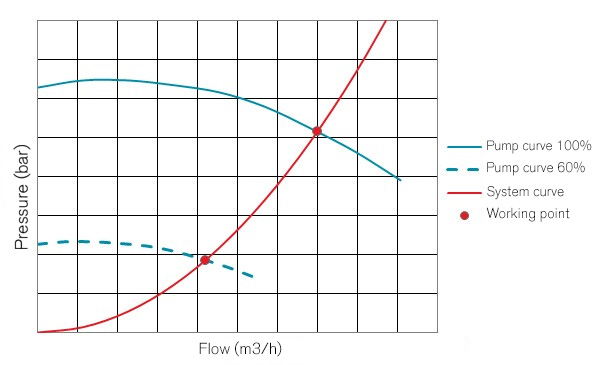
At ERIKS, we dig into the data:
- What’s your real-world duty point?
- How variable is demand across the day?
- Are you matching system resistance to the pump curve, or fighting it?
Only by aligning the pump curve with your actual system curve can you consistently hit BEP and stay there.
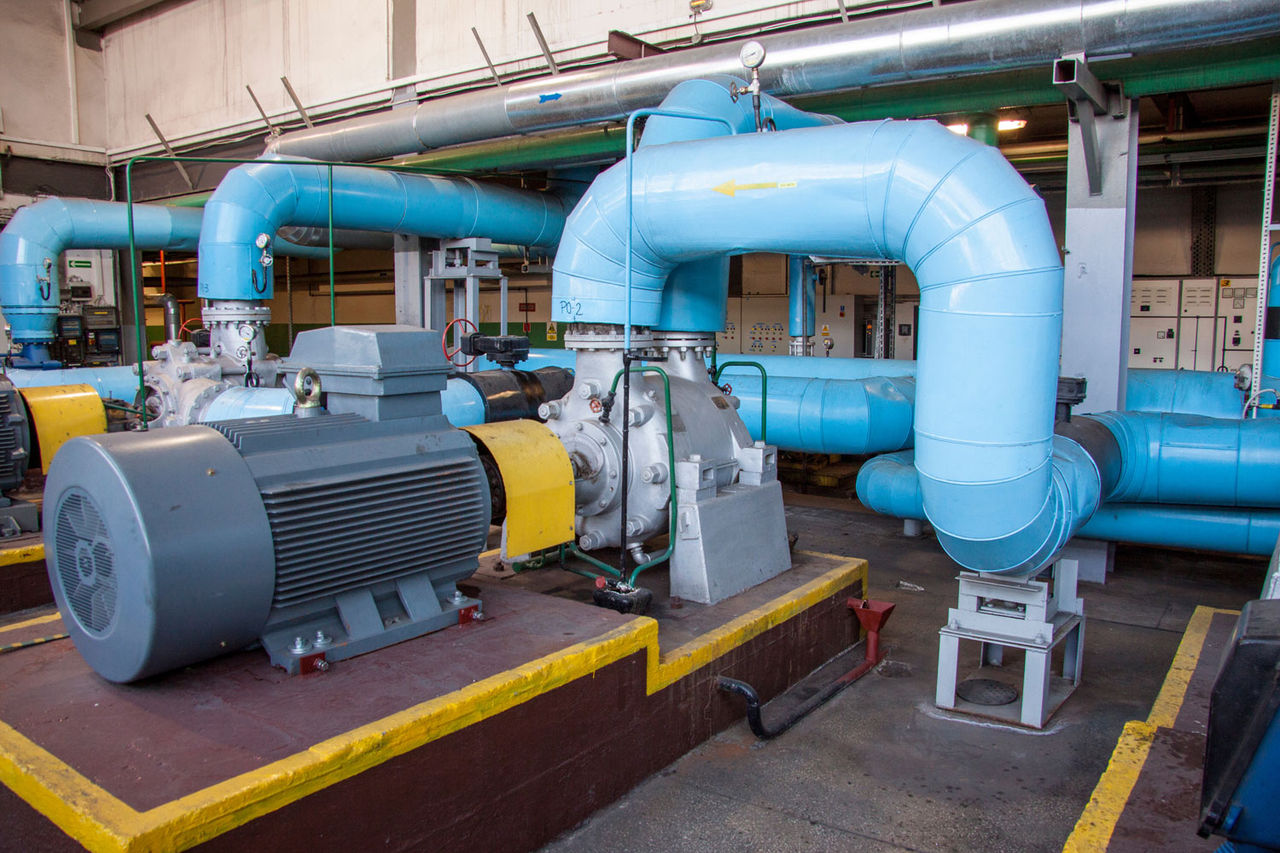
Off-BEP = Off the Mark
If your pump is chugging along 15–30% away from BEP, you’re not just losing efficiency — you’re compounding wear. That means shorter life cycles, increased maintenance, and rising energy bills. In an EfW plant, that hits twice: in lost throughput and higher carbon intensity per kWh generated.
The carbon cost of inefficiency is no small thing. If your plant’s being measured against net-zero targets or pushing for R1 classification, every kilowatt saved counts.
What Can You Do?
Here’s what our ERIKS pump team recommends for EfW operators:
- Audit your actual operating conditions – flows, pressures, and fluid properties often diverge from design assumptions.
- Re-check pump sizing – overspecification is a silent killer of BEP performance.
- Install or optimise VSDs – they’re a game-changer when configured properly for varying load demands.
- Monitor pump health – especially in high-temp or abrasive duties; real-time data is gold.
- Work with a specialist partner – ERIKS offers pump curve analysis, condition monitoring, and tailored upgrades that target BEP as standard.
Let ERIKS help you eliminate quiet inefficiencies
EfW plants demand reliability. And pumps, when neglected, quietly become one of the most expensive inefficiencies in the system. Staying close to BEP isn’t just good practice — it’s good economics, good engineering, and frankly, good sense.
If you need help finding your BEP — or are wondering if your current setup is quietly sabotaging your uptime? We’ll bring the data, the diagnostics, and the fix.
For more information on Renewables, or get in touch with your local ERIKS Service Centre who will be happy to discuss your options.
#ERIKS #LetsMakeIndustryWorkBetter #Renewables #EnergyFromWaste #EfW #BestEfficiencyPoint #Pumps