In this article
When you're in a hole, stop digging and start pumping
It’s a situation any engineer will relate to. A failed asset. A constantly evolving situation. The costs of downtime rapidly racking-up. You’re in it up to your neck. But imagine if what you’re in is seawater, and you’re in it up to 18m deep. That was the problem for an oil and gas producer at their newly-acquired offshore production site off the Humber Estuary.
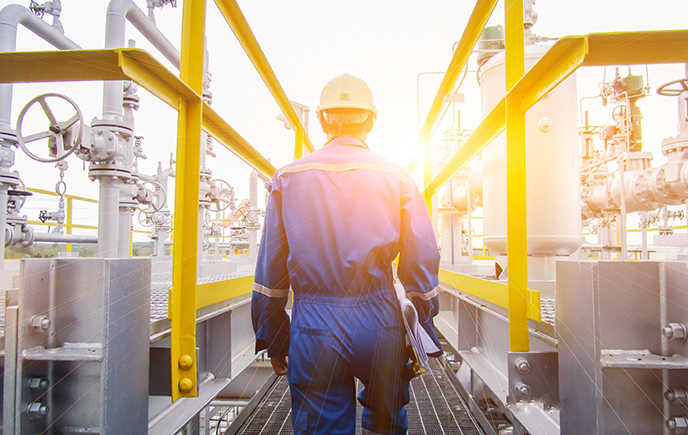
The site includes a 559mm diameter subsea caisson, measuring 37m from seabed to top, of which most is underwater. To keep it operational, seawater has to be continually pumped out, but after 20 years of duty the pump had finally failed.
Wanting to extract the maximum value and service life from the aging asset, the customer’s first instinct was to call on ERIKS’ MRO expertise, to effect a relatively short-term repair. However, the more ERIKS discovered about the complexity of the application, the more it became clear that a new pump to an upgraded spec., and a comprehensive rethink of the pumping operation, was the most cost-effective option.
As ERIKS pointed out to the customer, this wasn’t the kind of project for an MRO organisation to undertake. And a pump OEM would inevitably engineer a solution which shoehorned-in one of their own narrow choice of pumps – severely limiting the options.
So the most effective answer would be to use a complete engineering solutions provider, with extensive pump expertise, access to a broad range of pumps from a wide selection of OEMs, and with the necessary engineering know-how to handle every aspect of the application – including ancillary and peripheral equipment.
Who, the customer wondered, could that be?
A presentation from ERIKS provided the answer – and the answer was ERIKS’ Flow Equipment and Services business unit.
All at sea
When your site is in the North Sea, a site visit can be tricky to arrange. When there’s a global pandemic and a Work From Home instruction in place as well, your entire way of working has to change. ERIKS were more than up to the challenge.
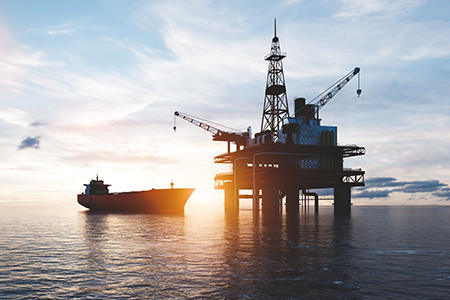
So began a steady stream of emails and video calls between ERIKS Business Development Manager John Dunkley, a member of the ERIKS pumping application engineering team and the customer, to thrash out the pumping solution.
ERIKS took on a project management role, advising on the optimum pump choice as well as on the associated hose, non-return valve, couplings and other associated components that the application demanded.
The result is an entirely bespoke solution. It includes a pump from ERIKS Accredited Pump Supplier, Tapflow of Southampton, designed for a flow rate of 80-100m3/hr. The impeller of the original pump – manufactured from standard stainless steel – had almost entirely corroded away. So the new pump incorporates a Super Duplex stainless steel impeller to cope with the corrosive operating environment.
An electrolytic copper/aluminium anti-fouling unit was also designed, engineered and supplied, together with a Super Duplex strainer to prevent blockage of the pump inlet.
Fast forward, not straightforward
Even a ‘straightforward’ MRO project to repair the original twenty year-old pump would normally be expected to take around three months to complete. And it would still be a twenty year-old pump, which could only be expected to have a limited service life.
The alternative – to engineer a replica pump to replace the original – would typically take at least one year, and possibly two. But with water levels rising as fast as the cost of downtime, ERIKS pulled out all the stops.
Expert engineers from ERIKS not only advised the customer on re-engineering the entire application, but also specified, sourced and replaced the pump – and project-managed the whole operation. The ERIKS solution incorporates a smaller, lighter and more efficient pump than the original, with a predicted service life when properly maintained of around ten years. And the entire project was completed in just three months from initial customer contact to delivery.
The speed is all the more impressive considering the solution was, as John Dunkley describes it, ‘engineered on the hoof’ as the customer’s requirements changed and developed throughout the design and engineering process.
ERIKS’ ability to get the customer out of a hole – even one that was underwater – has led to their being considered for two more of the customer’s projects. They clearly realise ERIKS is far more than an MRO provider – and the proof is in the pumping.
For more information on Flow Control solutions and to get in touch with one of our ERIKS Pumps Specialists or Valve/Flow Control Engineers, please contact your local ERIKS Service Centre, who will be happy to discuss your options.
#ERIKS #LetsMakeIndustryWorkBetter #Expertise #Engineering #RepairReplace #Solutions