In this article
Roll-up, roll-up! (There’s more than that to hose management)
Managing your hoses means more than rolling them up at the end of the day. And not managing them can mean more than an untidy site. It can mean dangerous trip hazards, polluting leaks, and unnecessary maintenance and replacement costs.
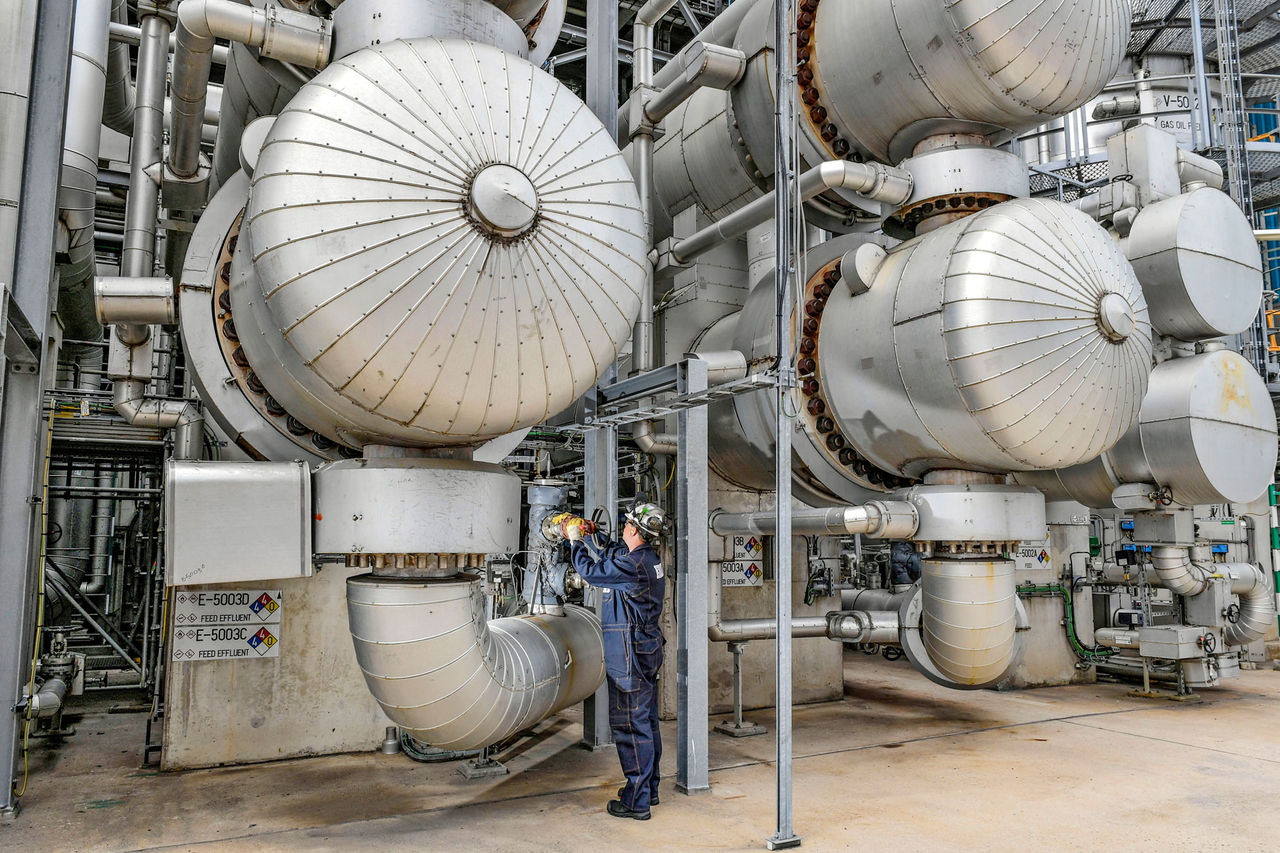
Like most people, you’re probably not a hose expert. As long as your hoses are transporting liquids from one place to another, why would you even think about them? But in reality, that’s not the end of your hose management.
If you want hoses you can count on to be safe, reliable and cost-effective, you need to start by identifying what hoses you have. An ERIKS Hose Management Survey will tell you that – and much more.
ERIKS’ hose specialist engineers have surveyed sites where more than 1 in 10 of the hoses in use were wrongly described on the customer’s SAP system. Which means that when the time comes to replace them, a less experienced supplier who replaces like-for-like will also be replacing wrong-for-wrong. And, depending on what the hose was being used for, that means continuing all the associated risks of leaks, premature failure, and potential pollution or injury.
Not knowing what hoses are on site and what applications they are being used for can also lead to unnecessary duplication of purchasing and inventory, and missed opportunities for cost savings.
Keeping tabs with tags
Once an ERIKS Hose Management Survey has identified the hoses, the results need to be recorded for future reference.
So ERIKS specialists attach tags to each hose, with a unique reference number and barcode. It’s then possible simply to use any smartphone to identify the hose and check its specification, function, age, and replacement due date.
This information is essential for satisfying Health & Safety inspectors and insurers, whether during an audit, premium quotation, or – in the worst case scenario – during an accident investigation.
A written report is also provided, which not only identifies the hoses, but also makes recommendations for replacing unsuitable hoses, for rationalising the hose inventory, for inspection and testing regimes, for a replacement timetable, and for hose housekeeping best practice.
Right hose, right place
In one survey of a customer’s hoses, ERIKS’ specialists identified 23 different types of hose in use at one site. Using their knowledge of hose types and applications, they were able to rationalise the types of hoses in use, and reduce the number to just 7-types – with no reduction in hose efficiency or safety.
The customer was also able to simplify specifying and ordering, reduce the risk of using the wrong hose for the wrong application (also reducing the potential for leaks and bursts), and cut costs. And by identifying process critical hoses, and which hoses were used in the greatest numbers, ERIKS helped the customer to ensure they always had sufficient spares in stock.
In other cases, the ERIKS survey has helped customers to find more suitable hose solutions for specific applications.
For example, one customer had hoses which were dragged across the floor in daily use. To make this easier, the customer had specified lightweight hoses. But these tended to wear quickly due to their soft outer.
Rather than simply propose the obvious but unsatisfactory solution of a heavier-weight hose, ERIKS specified a hose with a polypropylene spring along its length. This reduced abrasion, the risk of leaks and the need for more frequent replacement, without significantly increasing the weight or cost of the hose.
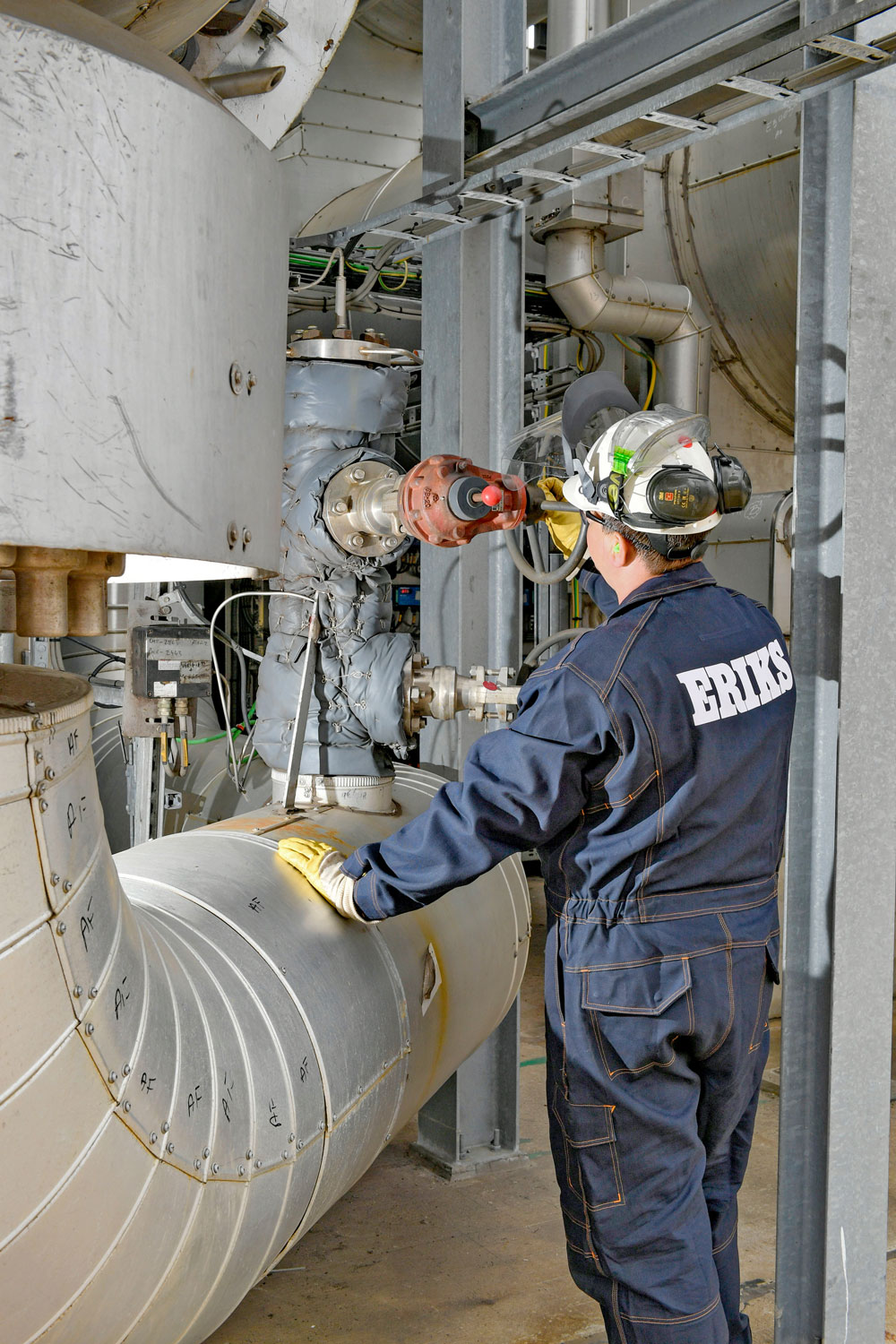
Easing the pressure
The risk of a hose leak or burst is always a concern. The more potentially polluting or toxic the liquid in the hose, or the greater the pressure it’s under, the greater the worry.
So rather than waiting until hoses fail, ERIKS’ scheduled hose testing provides proof and certification of their safety.
Pressure testing takes place on site, with water. ERIKS’ specialists take responsibility not only for certifying the hoses, but also for safe removal and disposal of the fluid originally in the hoses, and of the water used for testing – which may have become contaminated by the hose contents.
So whether you want to test, rationalise, or simply identify, an ERIKS Hose Management Survey will help you to get a grip of your hoses.
For more information on Flow Control solutions and a ERIKS Hose Management Survey, please contact your local ERIKS Service Centre, who will be happy to discuss your options.
#ERIKS #LetsMakeIndustryWorkBetter #IndustrialHose #HydraulicHose #HoseManagement #Survey