In this article
The no seal of approval
A confectionery manufacturer was losing almost as much of a key ingredient onto their factory floor as made it into their product. Tired of having to continually mop the floor, empty buckets, and replace failed and leaking pump seals, the manufacturer spoke to their usual ERIKS contact, who called in an ERIKS pump expert.
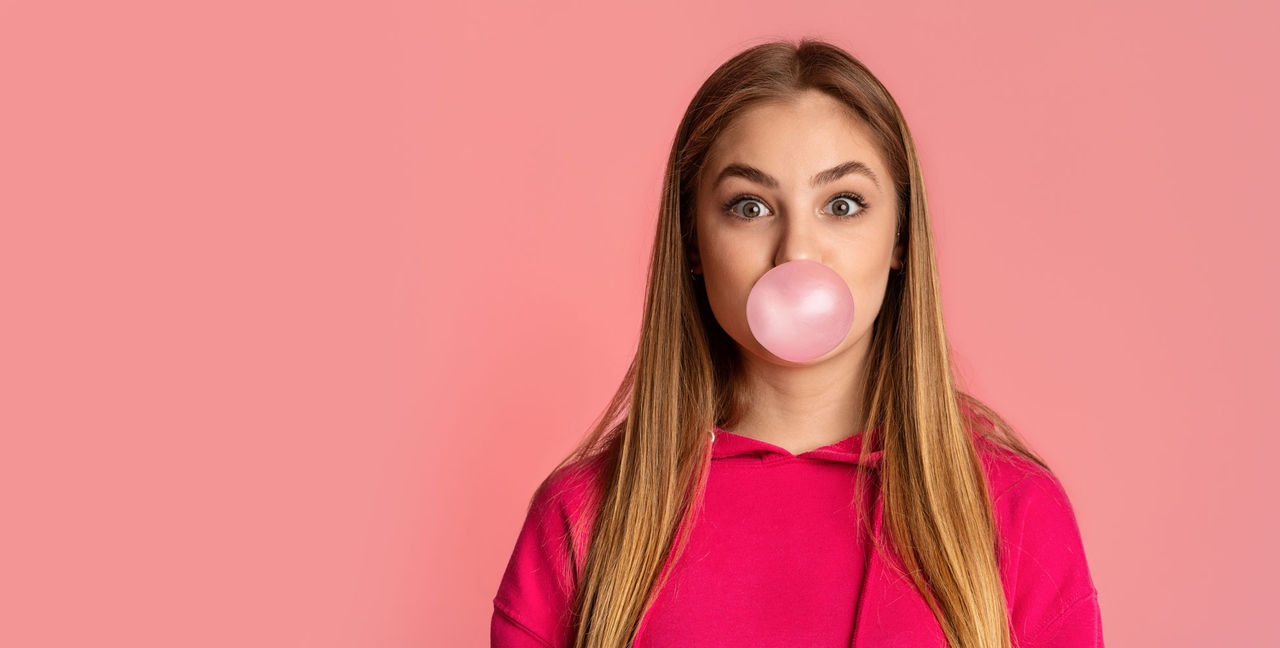
The cause of the problem was easy enough to identify. Corn syrup – the ingredient being pumped – is highly abrasive, and doesn’t take long to abrade seals enough for them to leak. Two or three seal replacements a year wasn’t unusual for the customer, and each one meant around half a day’s lost production, on top of the cost of the replacement parts and labour, and however many bucketsful of corn syrup had leaked in the meantime.
Add to this the health and safety and food hygiene risk of a syrup-coated floor, and it was clearly several accidents waiting to happen.
Meanwhile, the customers’ rotary lobe pumps were at least thirty years old and getting older by the day. So obsolescence was a growing problem and parts were increasingly hard – and costly – to come by.
Despite this, no-one had proposed an alternative solution. At least, not until ERIKS got stuck into the syrupy challenge.
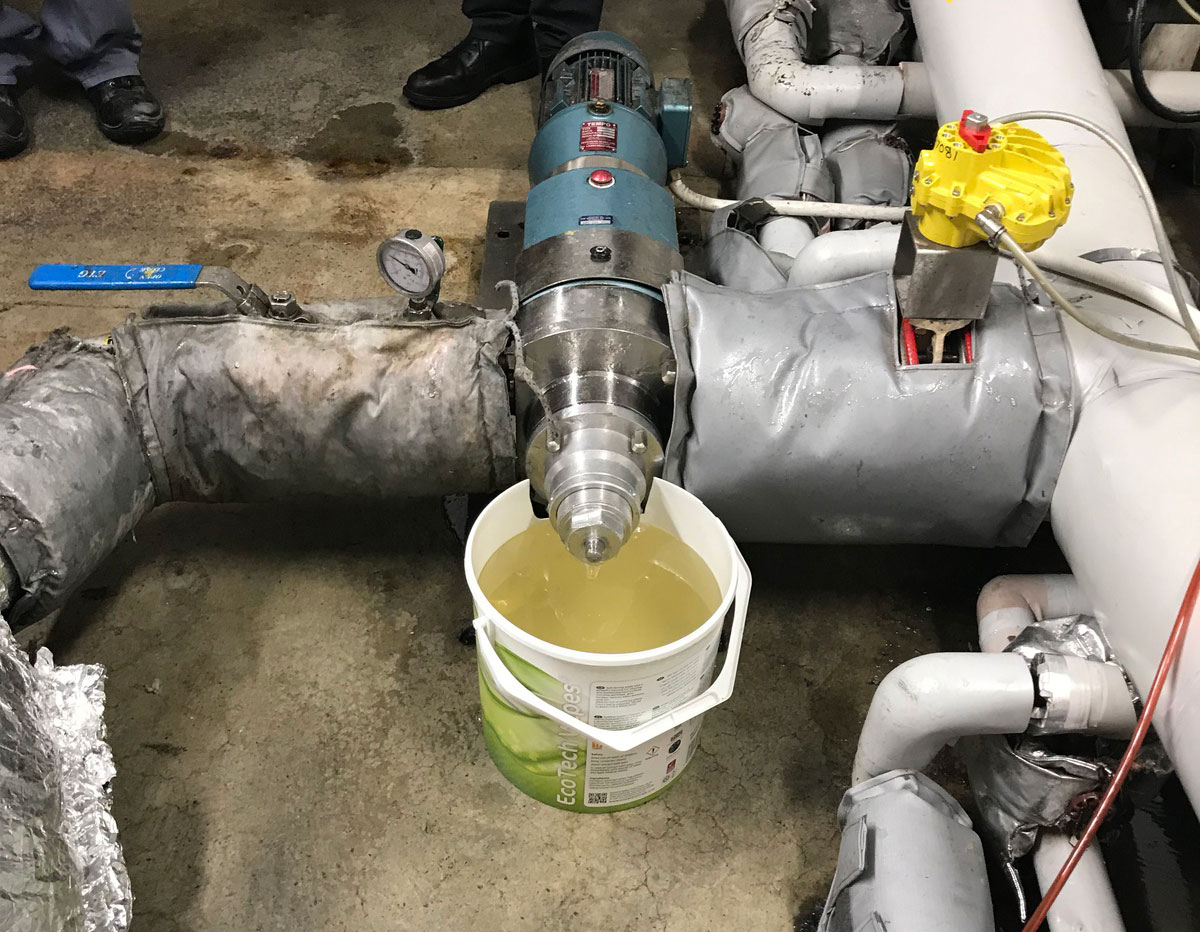
No special treatment
The usual solution would be two-fold. Firstly, eliminate the problem of obsolescence by installing a new rotary lobe pump. Secondly, reduce abrasion and protect the seals by utilising a warm water (Flush)wash to remove the abrasive substance from the seals.
However, the waste water produced by this process would have to be treated before it could be discharged into a watercourse, and the manufacturing site has no effluent treatment plant. ERIKS needed to find another option.
With hindsight the answer sounds obvious, but ERIKS’ were the first to propose it: to avoid the issue of seals which leak, use a pump with no seals
An eccentric answer
With an extensive knowledge of the latest in pump design and technology, ERIKS’ pump expert was well aware of the unique seal-less design of the Mouvex® SLS Series Eccentric Disc Pump.
Unavailable when the original pumps were installed, the design features double stainless steel bellows for durability, safety and product containment. A cylinder and pumping element are mounted on an eccentric shaft which rotates, allowing the pumping element to form chambers inside the cylinder. These increase in size at the intake port to draw the pumped medium into the chamber.
The fluid is then transported to the discharge port, where the pumping chamber size deceases to squeeze the fluid – in this case, the corn syrup – into the discharge piping.
The high suction and discharge pressures allow the pump to self-prime and fully strip lines, which in turn enables recovery of up to 80% of ingredients. Not to mention the percentage no longer leaking onto the factory floor.
Rigging the results
A Mouvex® SLS Series pump is not a small investment. So instead of expecting the customer to spend a large sum on a solution untried in their application, ERIKS offered a risk-free alternative.
With the help of long-term supplier partner, ERIKS arranged for the construction of a custom-built trial rig for the customer.
This mobile pump rig was delivered to the customer’s factory, where it could be tested in the line without the need to remove or completely decommission the existing pump.
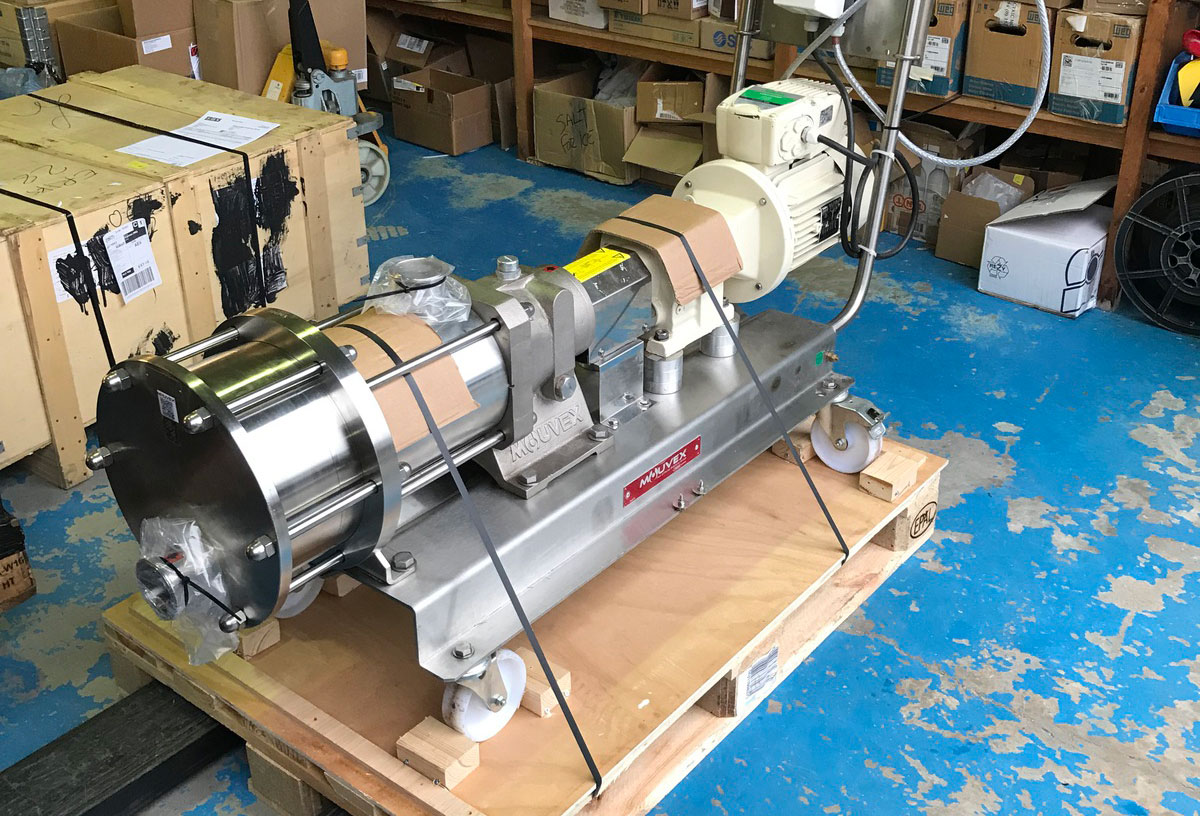
The customer was able to try out the new seal-less option over a period of weeks, before deciding whether or not to buy.
When they saw the results, buy was exactly what they did.
When seal-less is more
It wasn’t only the elimination of leaks which convinced the customer.
With no mechanical seals or timing gears to maintain or replace, their maintenance and lost production costs were greatly reduced. The eccentric disc design of the pump also allows for consistent product flow and improved energy savings. If shear-sensitive products are being pumped, the extremely gently, pulse-free flow protects their integrity, and the pump is both Clean-in-place and Sterilise-in-place, making it easy and convenient to maintain cleanliness to food hygiene standards.
So thanks to exceptional pumps know-how, and strong industry relationships, ERIKS got yet another customer out of a sticky situation.
For more information on Flow Control solutions and to get in touch with one of our ERIKS Pumps Specialists or Valve/Flow Control Engineers, please contact your local ERIKS Service Centre, who will be happy to discuss your options.
#ERIKS #LetsMakeIndustryWorkBetter #Pumps #Seals #FoodSafety