In this article
Made just how you like it
If you’re a coffee drinker – and these days, who isn’t – you’ll be very particular about how your coffee is made. When you’re a coffee producer, the same principle applies to your production equipment.
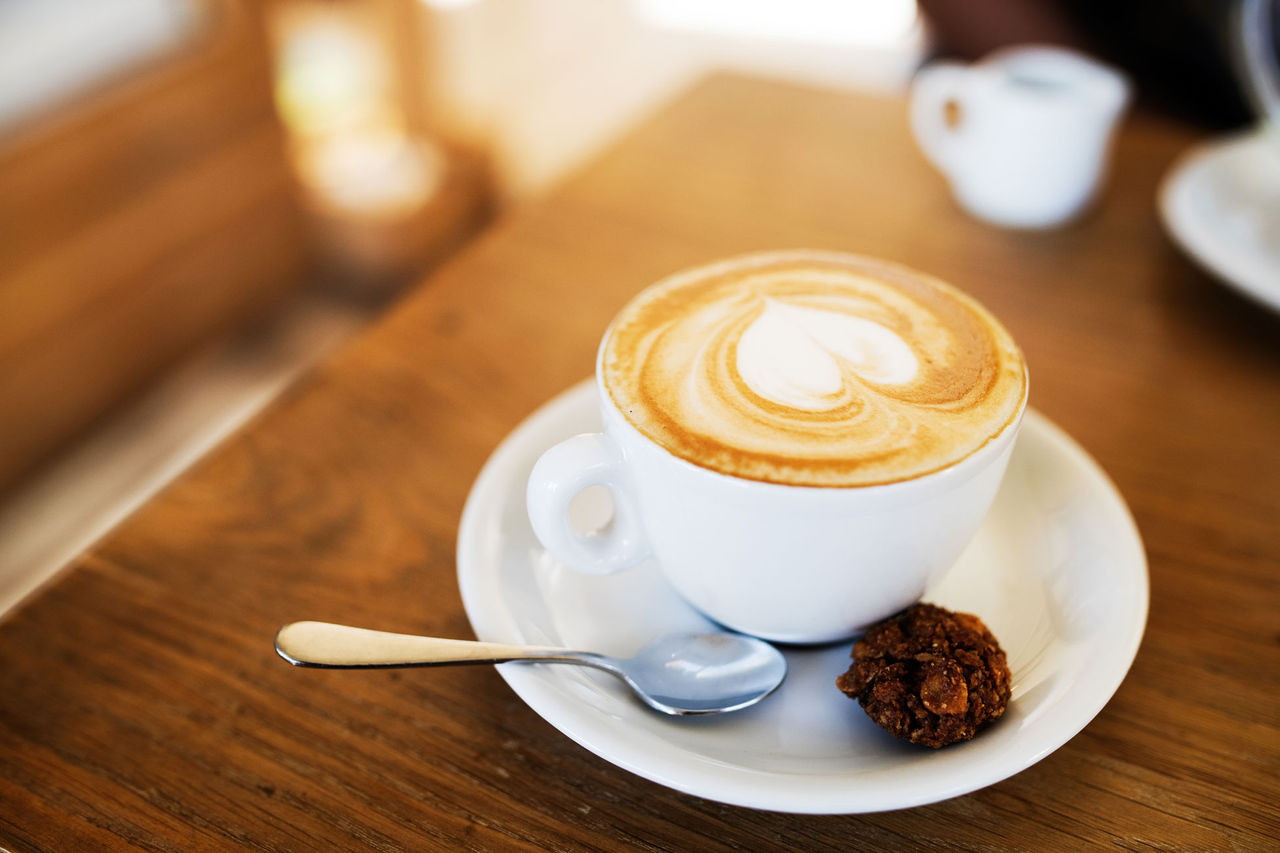
How do you like your coffee? Around 95 million cups of it are drunk every day in the UK alone, and though there won’t quite be that many different options, there will certainly be plenty of variety.
One of them is sure to be cappuccino, and many mugs of that will be made with coffee from one of the UK’s largest producers. So repeated downtime on their cappuccino line threatened not just their own productivity, but also the productivity of tens of thousands of bleary-eyed coffee drinkers nationwide.
When an off-the-shelf replacement part wouldn’t solve the problem, ERIKS’ engineers had to turn baristas, to design a bespoke solution that got the cappuccino flowing once more.
‘Coffee, the favourite drink of the civilized world’ – Thomas Jefferson
With so many coffee lovers to keep supplied, the customer’s cappuccino line is a tough, fast-moving operating environment for a valve.
The valve’s role is to control the flow of cappuccino powder – a highly abrasive and sticky substance, delivered at +90bar pressure at a temperature of 45°C. But around every three months on average, the build-up of powder on the ball of the high-pressure actuated ball valve is enough to cause it to stick in its open or closed position and bring the line to a halt.
When that happens, the valve has to be removed, taken to a workshop, stripped, inspected, fitted with new parts, and then taken back to the line for installation.
With a total of six valves on the process line, that’s a great deal of downtime, mounting maintenance costs and excessive lost production.
It was clear to the customer that this couldn’t continue, and that a standard part was never going to be the answer. So ERIKS were briefed to create a bespoke design that would last a minimum of six months between failures.
Fortunately, they had specialist expertise to call on.
‘No work would be possible without coffee’ – Henning Mankell
To design a specialist actuated valve, it makes sense to work with actuated valve manufacturer – and ERIKS-owned AMGPesch/ABK Valves GmbH are exactly that.
Experts at designing and engineering valves for challenging or unusual applications, their capability – combined with ERIKS know-how – led to several prototypes for consideration. The most promising design included several features to help overcome the issues and extend the service life of the component:
- Firstly, it was designed with no dead space where the cappuccino powder could accumulate. This immediately reduces the amount of powder at risk of sticking to the ball.
- Secondly, the ball itself was protected with an FDA approved special coating to help prevent the powder from adhering.
- Thirdly, a special sealing system was included in the design, to remove any powder which did somehow manage to stick to the ball.
- And lastly, an automated system intermittently blasts the valve with nitrogen to blow off any powder that remains where it shouldn’t.
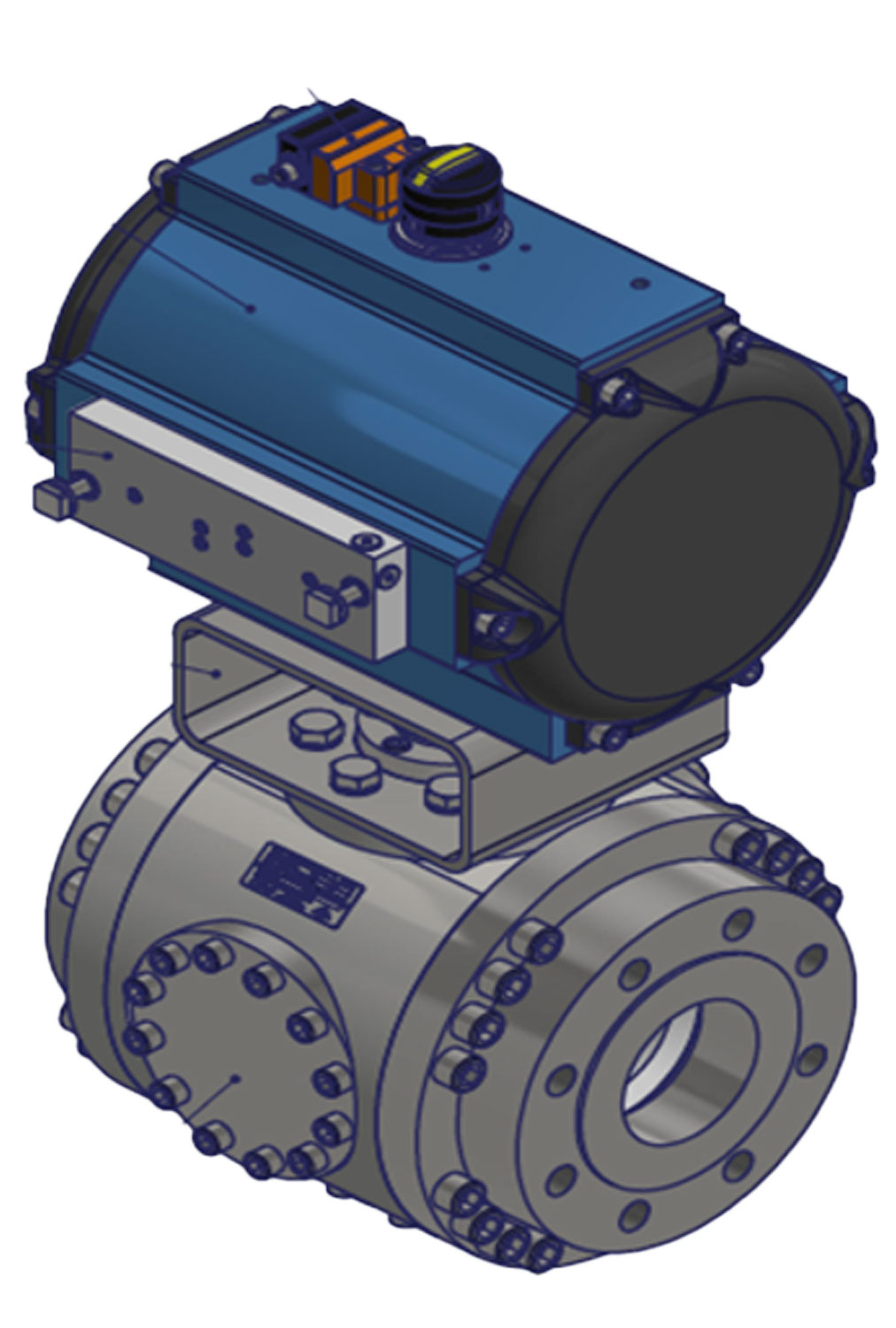
‘What goes best with a cup of coffee? Another cup’ – Henry Rollins
After a period of continuous development, the ERIKS / AMG-Pesch team achieved the ultimate prototype. Now it was time to install it for a live trial on the production line.
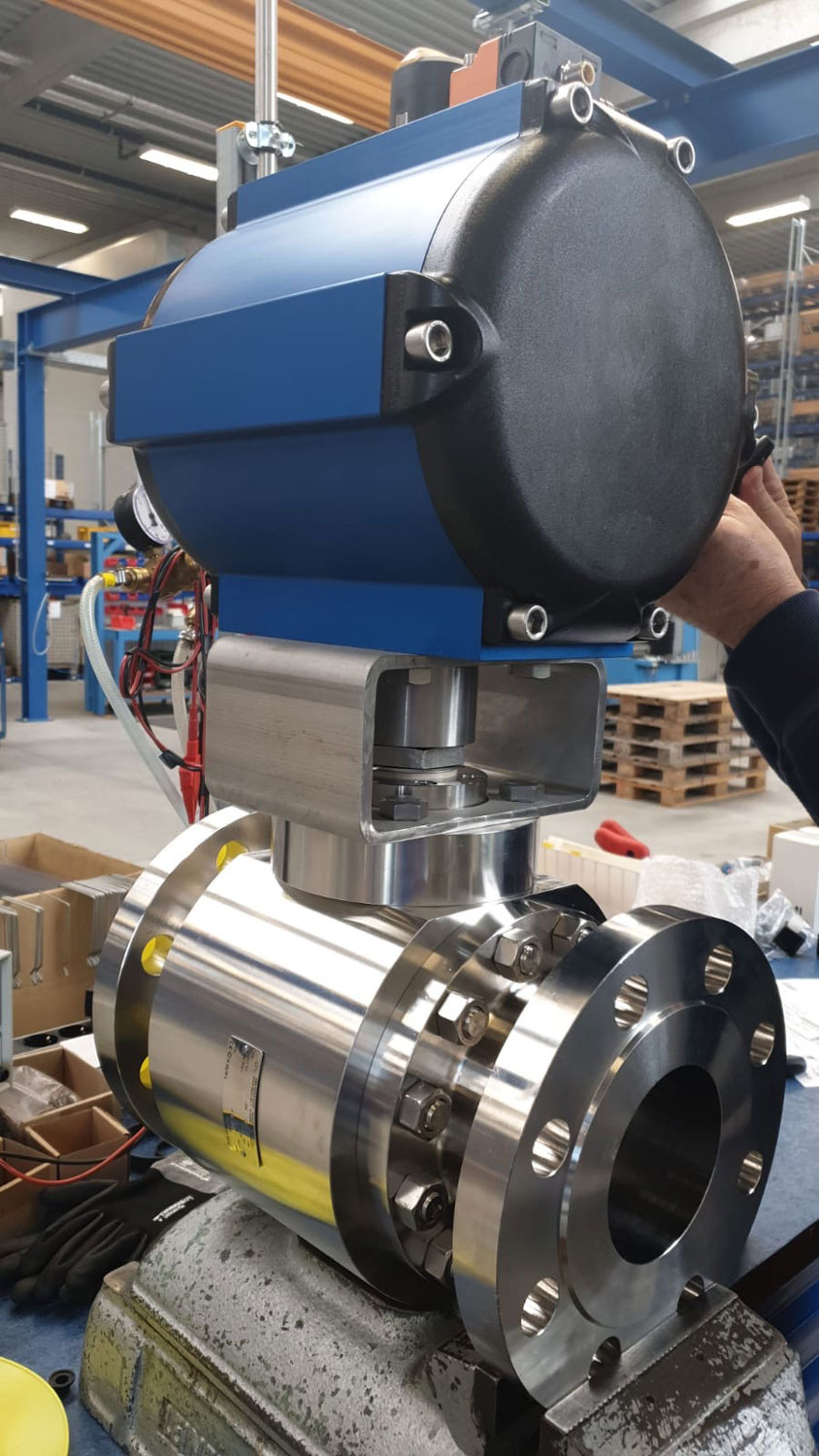
The original actuated ball valve lasted an average of three months before failure. The customer had asked for a new design which would operate trouble-free for at least six months: giving them double the reliability.
What ERIKS gave them was a prototype which completed not just three months, not even six months, but an unbroken nine-months in the production line’s most aggressive operating conditions. No wonder the customer decided they had seen enough… and placed an initial order for 28 of the new valve design.
These will be installed on the cappuccino line process and replace the competitors similarly failing valves at the UK site. In addition, work has already begun on slight modifications to the original design, to satisfy an order for 12 more units at the same customer’s around the globe, resulting in a orders of over 1m in total.
All of which calls for a celebratory drink. Anyone for coffee?
For more information on Flow Control solutions and to get in touch with one of our ERIKS Valve/Flow Control Engineers, please contact your local ERIKS Service Centre, who will be happy to discuss your options.
#ERIKS #LetsMakeIndustryWorkBetter #ActuatedValves #FlowControl #Manufacturing #BespokeSolutions