In this article
If you joined all your hoses end to end...
…the chances are you’d find numerous leaks, many old hoses overdue for replacement, and several corroding connections. Or to put it another way: countless accidents waiting to happen. Fortunately the ERIKS Hose Management System can help you keep tabs on your static and dynamic hoses – to keep your employees safe, your processes efficient, and your site on the right side of the HSE.
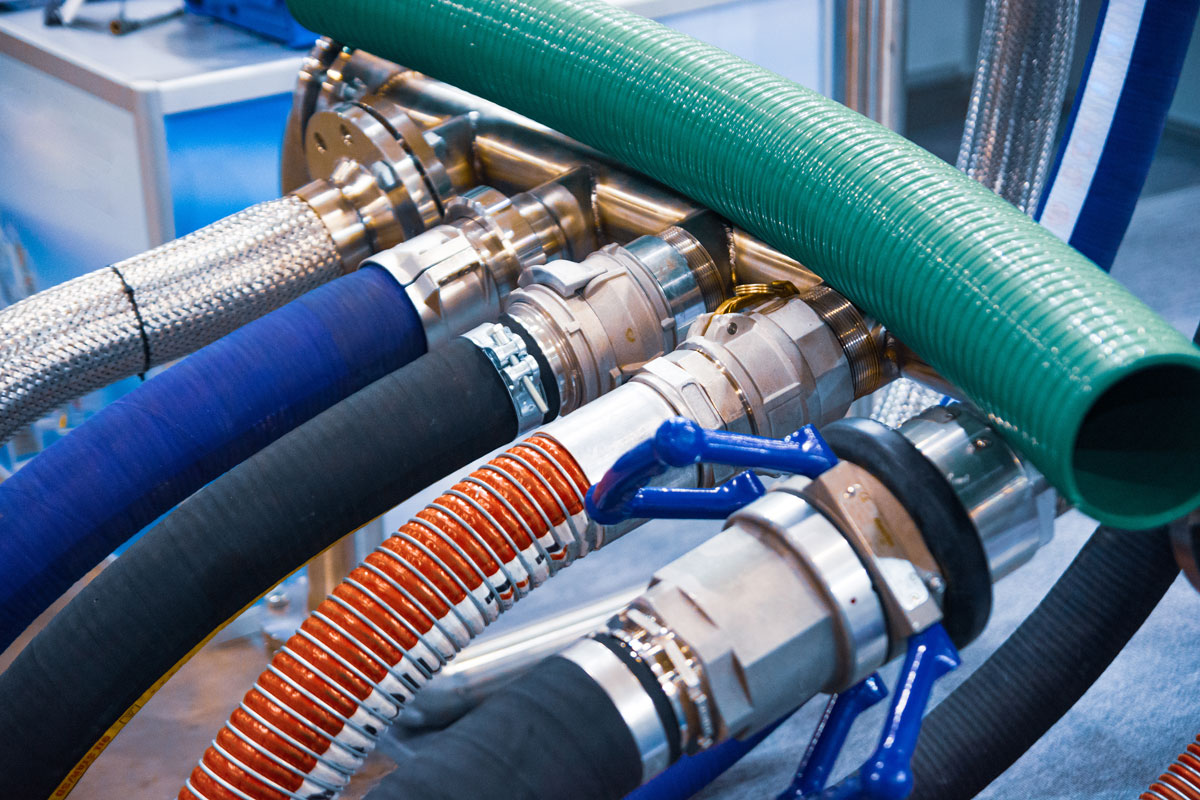
Your engineers have a lot on their plate. On any list of planned maintenance tasks, or maintenance inspections, hoses will come pretty close to the bottom. In fact, despite British Fluid Power Association (BFPA) guidelines stating that hoses should be swapped out every five years, they often won’t be replaced until they actually fail. Yet hoses are as critical as the vessels they feed into, the tankers they are used to discharge, and the pipework systems they connect to.
At an ATEX or COMAH regulated site, properly maintained hoses can also make the difference between incident-free operation and explosions or major accidents.
As recent inspections by ERIKS hose experts at customer sites have proved, a Hose Management System not only takes a load off your engineers’ shoulders. It can take a weight off your mind too.
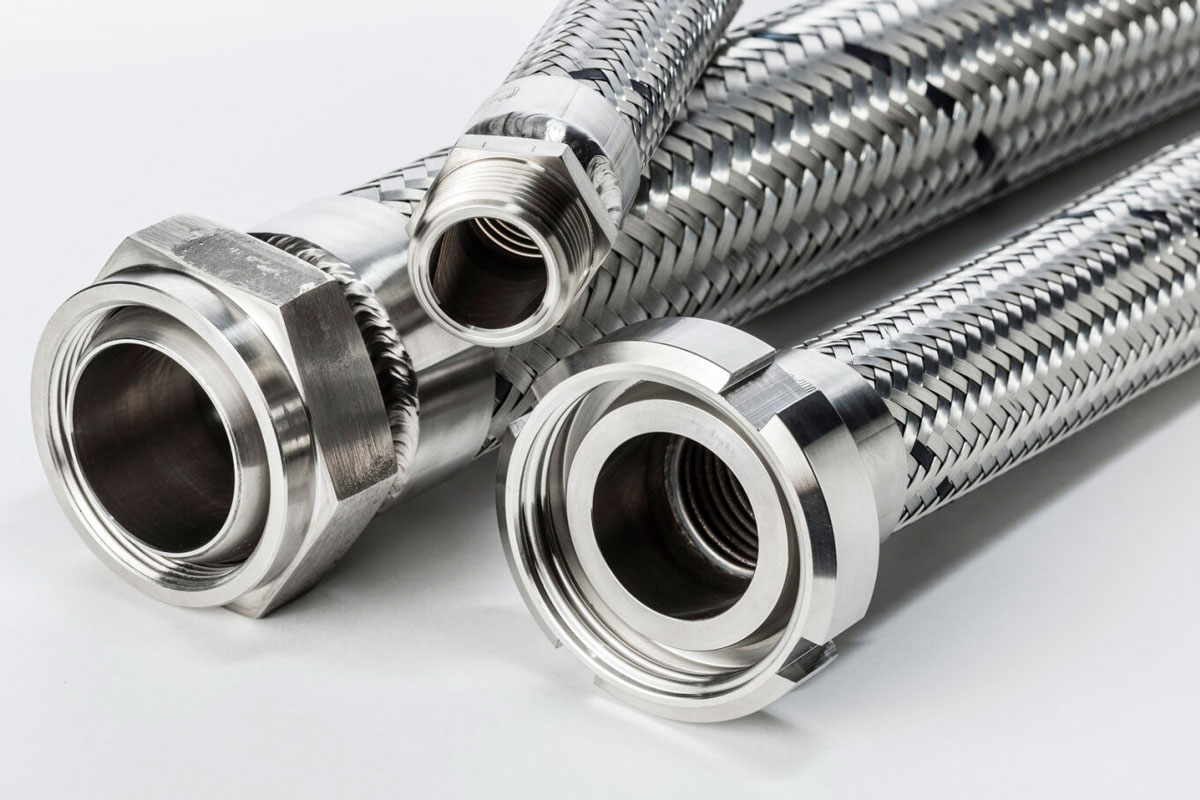
Hose safety lows
A recent visual inspection of hoses at a customer’s large ATEX- and COMAH Tier 1-rated site produced some surprising, and frightening, statistics.
The inspection – which looked for leaking or corroded hoses or connections, and signs of age – assessed 825 hoses. These included high-end PTFE hoses, general industrial hoses, and specialist hoses for the transportation of various chemicals. The failure rate, indicating hoses which were leaking, overdue for replacement, or otherwise at risk of failure, was a staggering 15%.
That’s just under 130 hoses which had the potential to cause a process breakdown or stoppage, a health and safety incident, or even a major or catastrophic accident.
A survey at another customer’s site, which covered a total of 262 hoses, revealed a 50% failure rate. Whilst a survey at a chemicals company discovered almost 125 hoses in need of replacement.
Excellence, not Excel
Although many sites may have a system of sorts for recording hose assets, it’s often nothing more sophisticated than an Excel spreadsheet. And without regular inspections of the assets, it’s little more than an inventory.
The ERIKS Hose Management System goes much further: recording detailed information about every hose surveyed [see box-out below] and tracking their age, so that they can be replaced in a timely manner. All the asset and tracking information is displayed on a digital dashboard, making it easy to access and understand.
A full written report is also provided after the initial hose inspection. This includes not only information on hose condition, but also recommendations for hose upgrades and proposals for particular applications, such as different fittings and other enhancements.
Alongside the ongoing monitoring via the dashboard, the ERIKS Hose Management Service also offers monthly meetings and annual hose inspections.
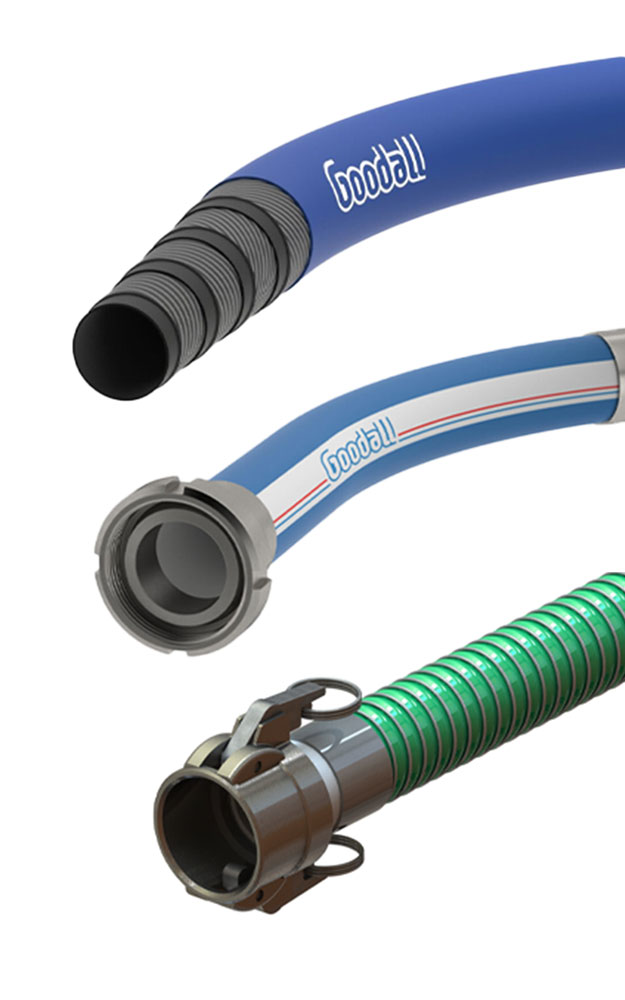
To help keep your site compliant with HSE, ATEX or COMAH regulations, contact your usual ERIKS Service Centre to ask for an initial hose survey.
Keeping tabs - and tags - on hoses
Once a hose has been inspected by ERIKS’ engineers, it is physically tagged with a unique number and a barcode or QR code. This makes it easy to check all its details on subsequent inspections, via the Hose Management System dashboard. This dashboard is populated initially by ERIKS, then jointly managed with the customer.
Information on the dashboard comprises:
- Tag number
- Bar code / QR code
- Hose type
- Size (diameter, length)
- Availability (on-site or to order)
- Dates of manufacture and modification
- Certificates of conformity
- Inspection dates
- OEM technical drawings
In addition, the management system software will monitor the age of each hose, and provide a ‘Valid’, ‘Almost Expired’ and ‘Failed’ warning based on the BFPA 5-yearly replacement guideline.
3 months’ warning of expiry allows sufficient time to organise a replacement hose and schedule an engineer to swap out the old hose.
For more information on Industrial Hose Solutions or Fluid Power, Transfer and Control Solutions and to get in touch with one of our ERIKS Specialists, please contact your local ERIKS Service Centre, who will be happy to discuss your options.
#ERIKS #LetsMakeIndustryWorkBetter #HoseManagementSystem #Hose #Safety