In this article
Don't get caught in the steam trap
If you’ve never worried too much before about the cost of producing steam for your processes, here are some scary steam statistics to get you thinking.
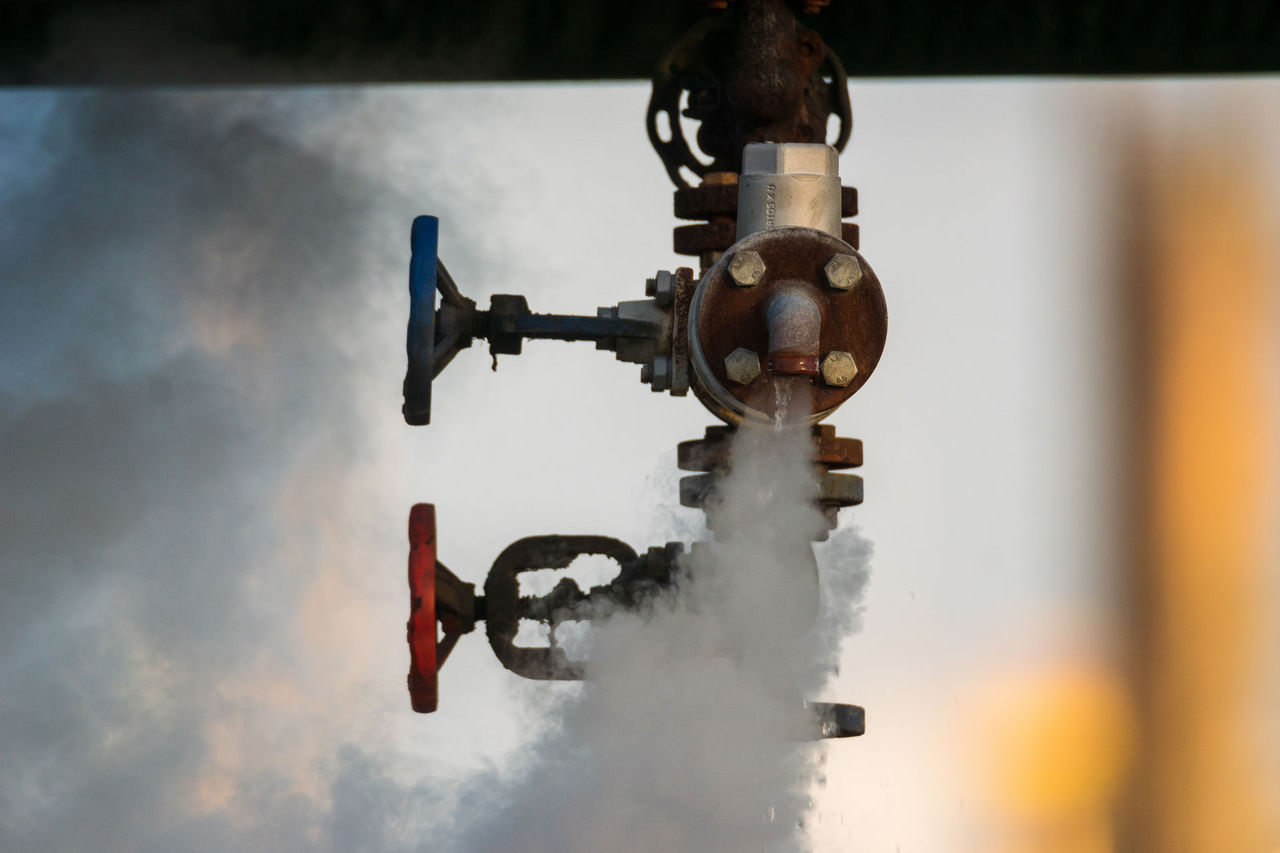
- The rising price of energy has increased the cost of generating a tonne of steam, from around £20/tonne twelve months ago, to £40 - 50 today.
- On average, 15 - 20% of steam traps in a steam system will be in failure mode at any one time. They may be jammed open, closed, or leaking steam.
- One failed steam trap will waste up to £2,000 worth of steam per year.
- A 1mm hole in a steam line will waste £500 of steam per year.
- A leaking 2” isolation valve will lose steam to the value of £750/year.
- ERIKS Flow Control specialists identified a steam trap failure rate of 57% on one steam system surveyed.
So, it looks like steam is more than just a lot of hot water. And talk about the cost is not just a lot of hot air. With energy prices rising – and energy use directly reflected in the size of your carbon footprint – all businesses want to save energy, save money and be more sustainable.
Which means now is the time to find ways to produce steam more cost-effectively, use it more efficiently and shrink the size of your next energy bill.
Survey, safety, and savings
Steam is not only expensive. It can also be dangerous. So, Health and Safety considerations come before cost, but the two go hand-in-hand.
Leaking pipes or jammed valves – which waste energy and money – can also allow scalding hot steam to escape, and risk injuring anyone in the vicinity.
To comply with Health and Safety regulations, every system containing steam at pressure must be regularly inspected. An ERIKS Steam Trap Survey will not only identify issues which are a safety risk, but also those which are reducing efficiency and increasing costs.
Returns on return
With your steam system surveyed and any maintenance issues resolved, ERIKS Flow Control specialists can also help you identify more ways to save money. One of the simplest is to ensure the system returns condensate to the boiler.
Raising cold water above 100°C to produce steam consumes a large amount of expensive energy.
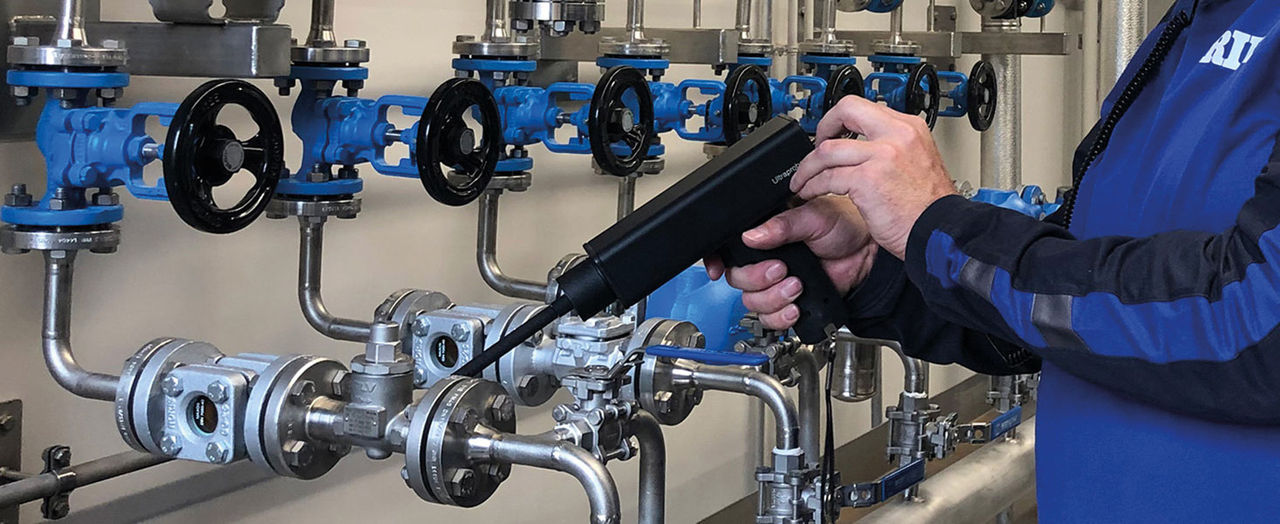
In fact, to raise a tonne of cold water to the required steam temperature costs around £4-6. But if condensate is captured and returned to the boiler, the water temperature will be maintained at a higher level, so it takes less time and energy to achieve the required steam temperature for steam production once again.
Recovering flash steam is another way to recoup the cost of steam generation. When condensate is discharged via steam traps, from high to low pressure, some of the condensate (typically 10-15%) evaporates into flash steam. This contains heat energy which will be wasted unless recovered.
Incorporating flash steam recovery into a steam system can provide a return on investment within as little as 6 months.
Taking back control
Once you have done everything you can to avoid wasting steam that’s already been produced, there’s still more you can do to produce the steam more efficiently in the first place.
Simple on/off control of the gas or oil burners heating the boiler is crude and costly. But modulated burner controls allow far greater flexibility and enable far more efficiency.
Variable speed pumps are also more costeffective than those which are either on or off. They can modulate their operation to match the amount of boiler feedwater required, saving energy, and eliminating the need for boiler feedwater control valves.
And variable speed controls on cooling fans can also help ensure the most efficient use of energy.
Hot stuff
Steam is to hot water what flow control is to daily engineering maintenance. In other words, more complex and specialist than you may imagine.
That’s why you need Flow Control specialists like ERIKS to regularly inspect your pressurised steam system for Health & Safety compliance, to provide scheduled maintenance, and to identify and implement effective cost-saving measures.
Because losing steam from your system doesn’t only mean lost steam. It means lost energy, lost money and lost production.
For more information on Flow Control solutions or contact your local ERIKS Service Centre, who will be happy to discuss your options.
#ERIKS #LetsMakeIndustryWorkBetter #SteamTraps #FlowControl #Specialism #Sustainability