In this article
A brewer chills out over costs and reliability
When ageing equipment needs replacing, or a production line needs expanding, doing nothing is not an option. That doesn’t mean considerations of cost-effectiveness, reliability and total cost of ownership (TCO) can be put to one side. It’s actually the perfect opportunity to investigate new technologies, with a view to improving productivity and reducing costs – as Bürkert proved for one of the UK’s leading brewers.
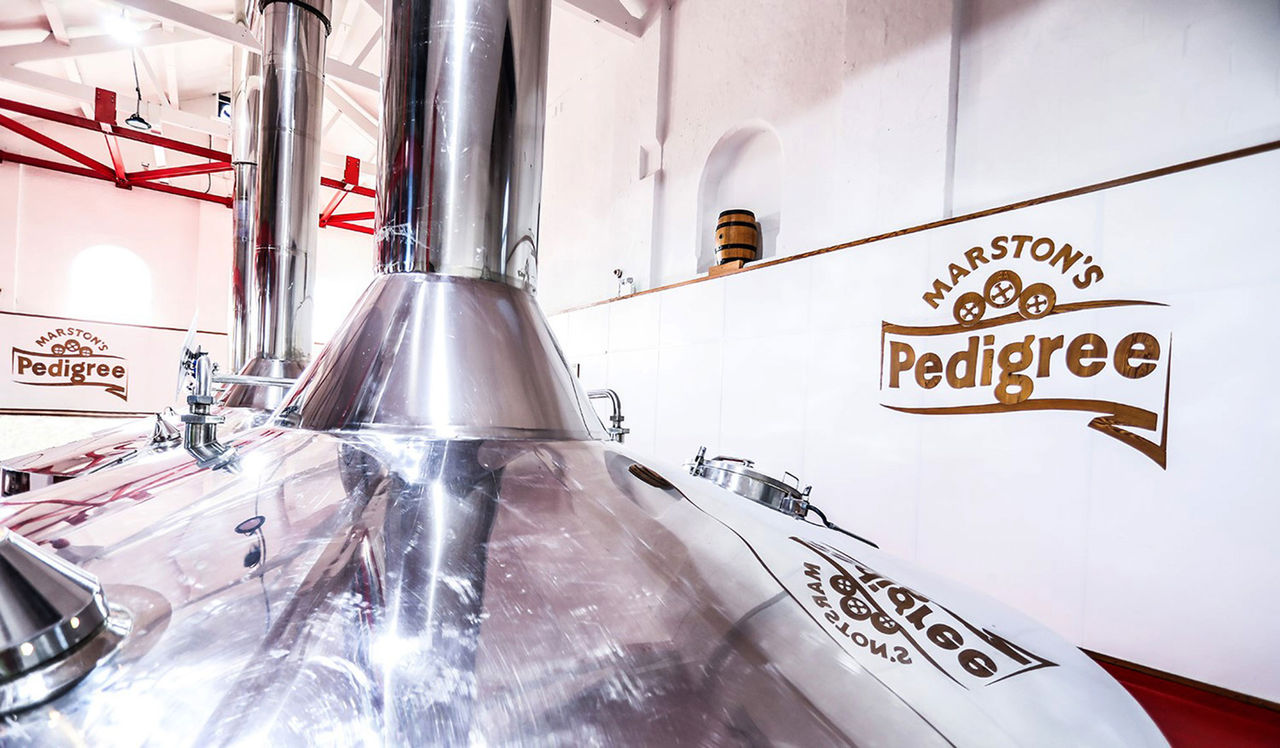
Increased demand for craft beers meant a brewery needed to install new chilled storage tanks, just as the pipework and control valves on its existing tanks were reaching the end of their service life. This left the production engineers with a requirement for no fewer than 84 control valves. Which initially threatened to leave them with a very large bill.
Having previously relied on electronically-actuated control valves, the engineers sought like-for-like quotes. But rather than simply quoting and sitting back, Bürkert arranged a site visit to assess the requirement at first hand.
Mixed messages
The valves are used to control a water/ glycol mix which cools the storage tanks. As they are part of a hygienic process, they need to be manufactured in stainless steel. And adding further to the cost is the size of the threaded connecting pipework, at 50mm/2ins diameter.
Although a premium price seemed unavoidable, Bürkert felt sure they could offer a more cost-effective solution.
The site visit revealed that the engineers had specified electrical actuation because of ‘the high cost of pneumatic controls.’ This perception was based on one recent quote from a different process control manufacturer. After reviewing and assessing the existing system, Bürkert’s engineers explained how all the aims of the process could actually be achieved using pneumatic valve islands and control valves.
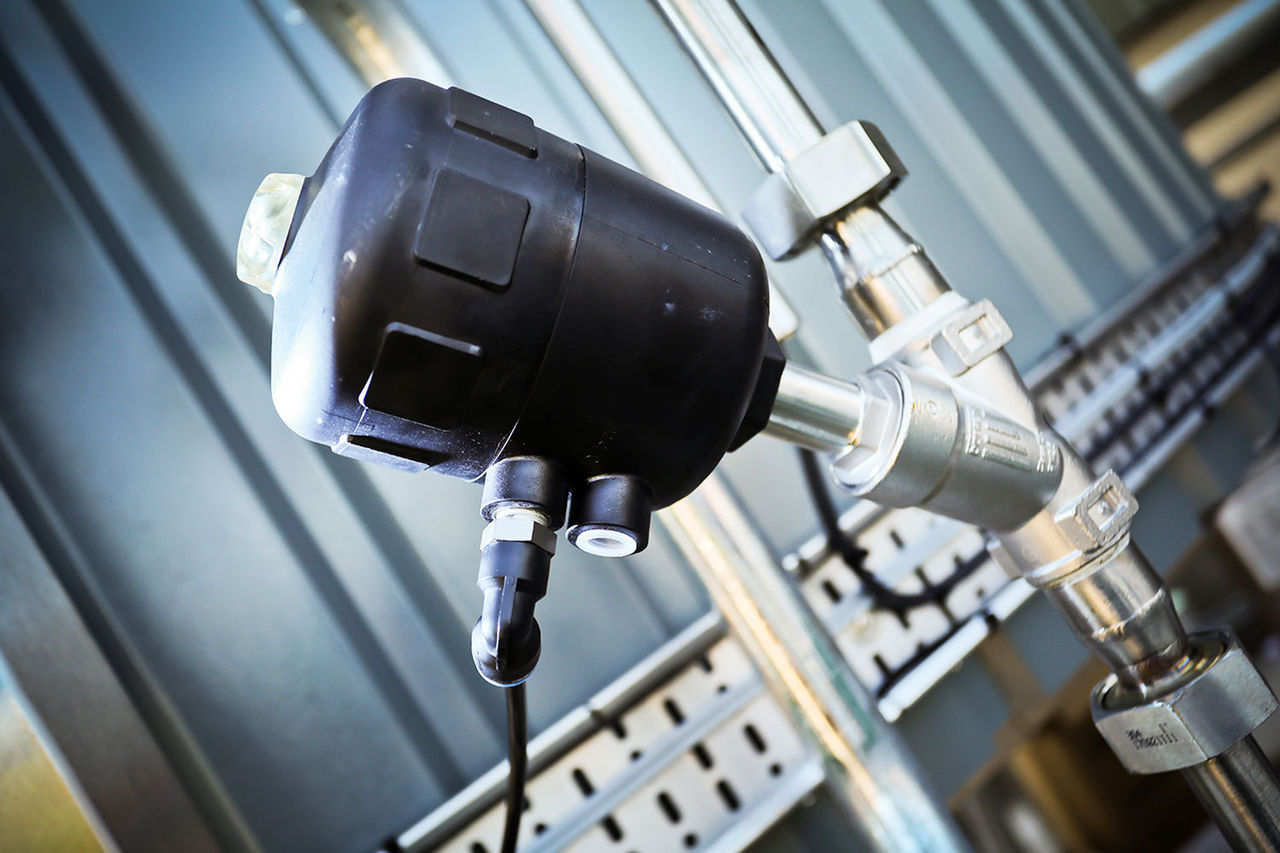
And at a significant saving over an electrically-actuated system.
Forward thinking
Bürkert’s proposed solution wasn’t designed to deliver just short-term benefits, but also long-term TCO and reliability advantages.
The company’s latest valve island – the Type 8652 – built into a European Hygienic Engineering and Design Group panel, could be positioned close to the process, to reduce installation complexity and cost.
While the compact size of the valve island has space-saving benefits, in this case the customer wanted a larger panel, to future-proof against expansion of the system and allow for their own input/output systems. So Bürkert populated all the valve island control modules, leaving the unused ones to easily be connected as and when the application expands.
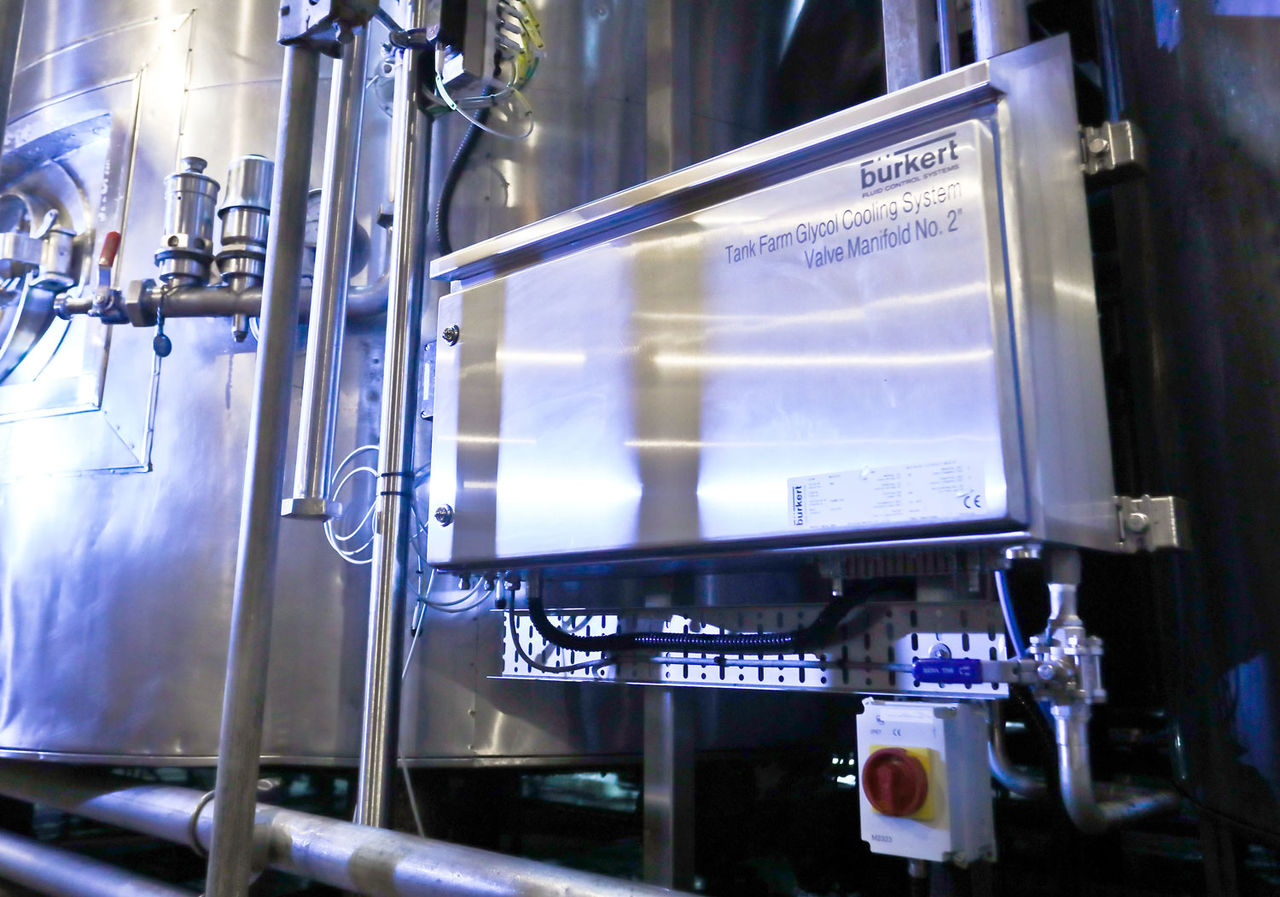
The control panel was custom-built by Bürkert, and designed to accommodate the installation of the Type 8652 AirLINE, which is optimised for installation at the bottom of the panel.
The choice of positions for the air supply port on the valve island meant the air preparation unit (filter and regulator) could also be included within the panel, with no need for additional connection points. Placing this unit outside the panel is the more conventional option, but Bürkert’s solution provided protection against water ingress during washdowns.
The last pieces in the system jigsaw were the Type 2000 valves, in stainless steel with threaded connections. These were each fitted with a CLASSIC actuator. Although the customer opted for hardwiring rather than gateway connectivity direct to the Rockwell PLC, the amount of wiring – and therefore its cost – was still significantly reduced over the electrical solenoid valve option.
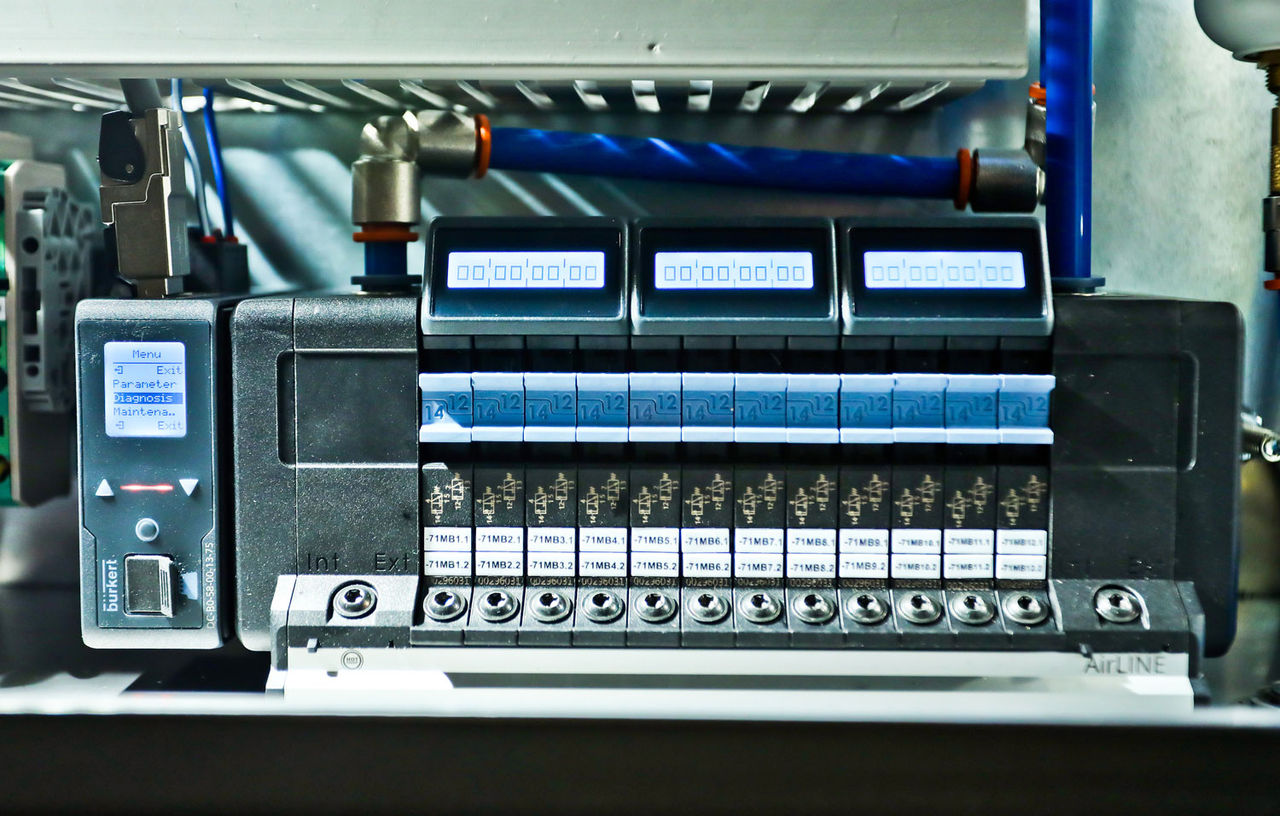
Status symbol
Along with the lower cost of the pneumatic package, the Bürkert system helps reduce the TCO with a handy status monitoring feature.
A back-lit LCD screen integrated into the valve island displays pilot valve status, process valve switching status, a switching cycle counter and a diagnostic report. This instant status information for remote components and connections accelerates and simplifies fault diagnosis – making it easier to maintain performance, optimise efficiency, and manage operational maintenance.
With the system fully operational, the customer’s Project Manager reported that ‘the increased functionality means we can reduce the amount of cooling and have greater control over the whole process. We have also made some very significant savings in terms of installation time and overall plant running costs.’
Not surprisingly, the brewery then decided it was time to get another round in - of 20 more Type 2000 valves and an additional valve island.
For more information on Flow Control solutions and to get in touch with one of our ERIKS Pumps Specialists or Valve/Flow Control Engineers, please contact your local ERIKS Service Centre, who will be happy to discuss your options.
#Burkert #ERIKS #LetsMakeIndustryWorkBetter #Brewery #Valves #CostSavings #TCO #Sustainability