In this article
Are you looking for fast, accurate, repeatable blending or mixing?
Whatever recipe you are blending, mixing or formulating - food, beverage or pharmaceutical - there's one ingredient that can put the whole process at risk. A human. So introducing an automated in-line or batch blending system to the mix will increase efficiency, productivity and repeatability of your process. And if it's an ERIKS system, it can do even more.
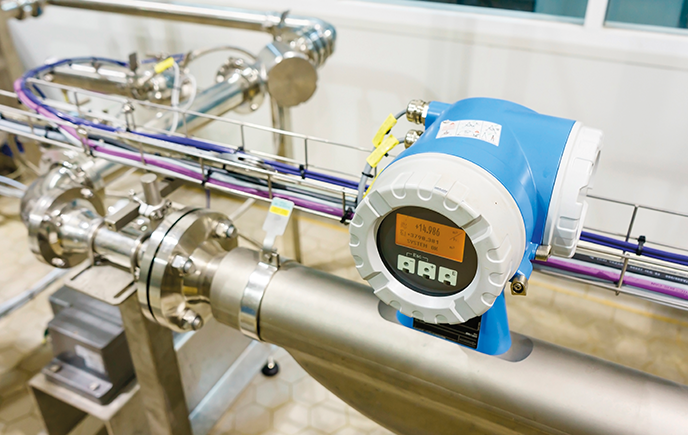
Humans are fallible, inaccurate and slow. In production processes which demand repeatability, accuracy and speed, that makes them a liability.
The solution is an automated batch or in-line blending or mixing system, for fast, accurate dosing, time after time. All at a speed that significantly accelerates productivity.
From a single production line upwards, ERIKS Flow Control can design, install and maintain a cost-effective system for your application. And because ERIKS is a major purchaser of high-quality brand-name system components, it will be built-to-order, but at a close to off-the-shelf price.
A whole batch of problems
Moving from a batch production process to an in-line system delivers a wide range of benefits. That's because manually-operated batch blending and mixing systems have an inherent set of problems.
ERIKS is currently undertaking design and installation of a new in-line system for a manufacturer of flavoured and infused oils. A number of issues with their current batch system should be resolved as a result.
The customer produces small runs of speciality oils, currently hand-blended to the required ratios and specifications, in 1000kg batches stored in intermediate bulk containers (IBCs). Product demand is high, and there is a large number of flavour variants, so the customer processes approximately 2,500 IBCs annaually - each one taking around an hour to blend.
Once an IBC has been blended, it has to be moved manually from the bulk oils dispatch point to the filler point on the production line. This involves manual handling on a trolley, over a distance of around 150m.
Moving IBCs is a tipping and manual handling safety risk, and in the confined space around the production line poses the additional risk of machinery damage. The operation also takes the depalletiser operator away from his machine for at least 10 minutes at every IBC change. Since one of the lines involved can process a full IBC every 90 minutes, this is a significant amount of the operator's time which could be better used.
One final inefficiency is the 12 litres of oil lost from production at every oil change.
A tasty mix of benefits
As part of the Project Definition presented to the customer, ERIKS itemised the main benefits the in-line system would achieve, together with the associated cost savings.
These include a reduction in:
- Blending requirements for the bulk oils department - saving 37.5 man hours per week, and £20,088p.a.
- Lost oil, from 12L to 4L per oil change. With 10 flavoured oil changes required every four weeks, at an average price of £6.25 per litre, that amounts to a saving of £6,500p.a.
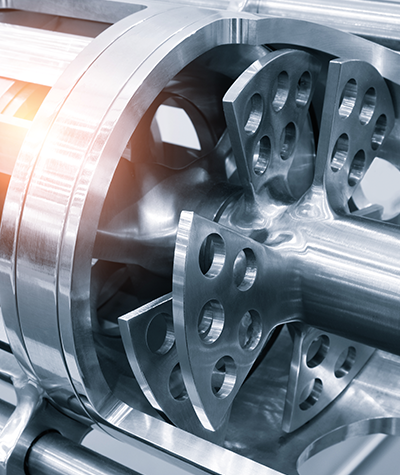
- Stock-holding of semi-finished goods, by approximately £110,000 - saving £3,000 interest
- Palecon changes, from 514p.a. to 128p.a. - resulting in a downtime reduction from 37hrs. to 9hrs. and a labour cost saving of £798p.a.
- Waste handling, by 50%, resulting in a £3,000p.a. saving
Quality ingredients
It doesn't matter how unusual or complex your mixing or blending requirement is, ERIKS can make it more efficient, accurate and cost-effective.
The specialist knowledge to design and build an effective in-line or batch system is only the start. To ensure reliability, the system will be engineered with quality components from well-known manufacturers. These include Xylem for pumps and Prominent for dosing systems, WEG for electric motors, Econ for valves and proportional valves, and Fenner for control systems.
And ERIKS' comprehensive Flow Control systems know-how, together with expertise in pumps, valves, flow meters, mixing vessels and weighing and dosing equipment, means you can source a complete system from one supplier. A supplier who also has the buying power to keep component costs down.
This all-in-one offering extends to the system itself: fully assembled and mounted on a compact stainless steel framework skid - together with the control panel, pipework, wiring, and inlet and outlet pipework connections - ready for delivery and "plug and play" installation.
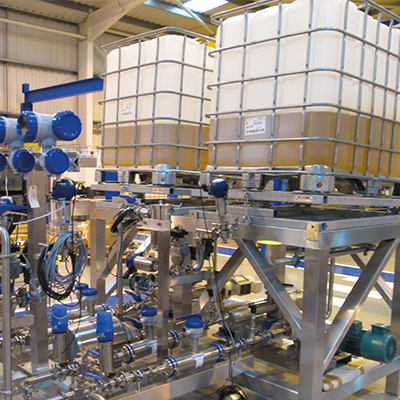
ERIKS Flow Control engineers can also return regularly to check the system is operating within your required parameters, and to recalibrate, service and maintain as necessary.
In fact, with whole-life support from ERIKS' dedicated Flow Control Technology Centre, the service and maintenance can be just as fast, effective, repeatable and reliable as your blending and mixing itself.
Complete solution, complete service, complete range
The complete range of flow control solutions available at ERIKS Flow Technology Centre comprises:
- In-line blendling, recipe/formulating systems
- Batch blending, recipe/formulating systems
- Automated dosing systems
- In-line dilution acids/alkalis
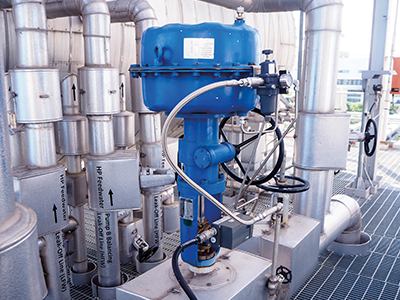
- Batching sytems
- Filtration system
- Clean-In-Place (CIP) systems
- Filling systems (fulling automatic and semi-automatic gravimetric, for 20-1,000L IBC containers)
For more information on Flow Control solutions and to get in touch with one of our ERIKS Pumps Specialists or Valve/Flow Control Engineers, please contact your local ERIKS Service Centre, who will be happy to discuss your options.
#ERIKS #LetsMakeIndustryWorkBetter #Pumps #FlowTechnologyCentre