In this article
Are you letting off too much steam?
When looking to reduce energy consumption, identifying inefficiencies across your production line should be the first step in your action plan. In many of your production processes, diagnosing and resolving issues can be done quickly, but in the case of steam systems, it’s far more difficult.
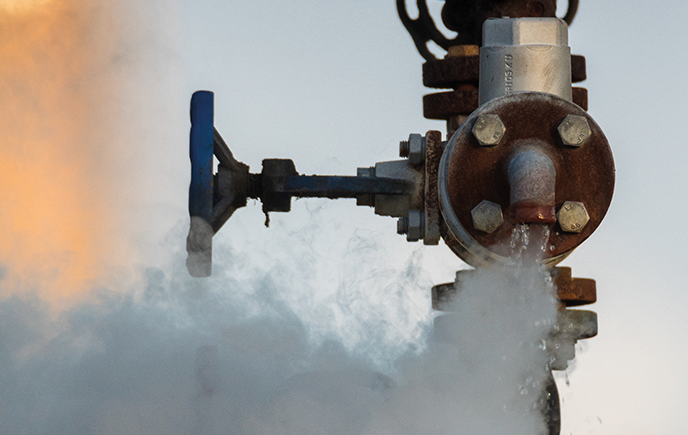
Due to slower rates of efficiency deterioration and reduced levels of performance, inefficiencies in your steam systems are not so obvious. In fact, previous research has suggested that steam systems which haven’t been surveyed for more than five years could have up to 30% of their steam traps leaking or blocked.
The good news is, an expert Steam Trap Survey from ERIKS can help identify any high-risk areas. And with inefficiencies at an all-time high, and costs significantly rising, one large steel manufacturer took the opportunity to discuss the ways in which ERIKS Flow Control could support their steam operations.
Not good reading
Initial conversations got underway in September 2019 and a steam trap survey was performed across certain parts of the steam line. A report was produced, and it wasn’t great reading for the customer. The report summary highlighted the following:
- 140 steam traps identified as not working
- 3,701,031kg of steam lost p.a.
- 604,305kg of CO2 emissions
- £55,516 financial loss p.a. caused by failing steam traps
At first examination of the report, it was easy to see that the biggest problem was in the amount of non-operational steam traps. 248 steam traps were tested, and a staggering 140 were identified as not working. That total’s a 57% failure rate. Extremely high compared to normal failure rates which lie somewhere between 10 and 20%.
And to make the statistics even worse, only approximately 20% of the site had been surveyed, so these figures didn’t reflect the overall efficiencies – or inefficiencies – of the very old site.
Problem after problem
Beyond the obvious financial implications, steam loss comes with a variety of concerns. Leaking steam pipes are hazardous and can endanger the safety of employees. Steam leaks tend to be invisible and only detectable by a whistling sound, but in a loud production environment your hearing is impaired, therefore making them extremely difficult to identify.
The implications of steam-related injuries can be catastrophic. At minimum, a steam leak will cause severe burns, cauterizing the skin, which as you can appreciate would be very painful. But worst-case scenario can be death.
Steam leaks also produce condensate, which can cause pools of water. This creates slip and trip hazards with slippery surfaces, whilst also increasing the negative effects on groundwater and drainage systems. The prior accounting for millions in compensation globally.
Finally, we have the severe impacts steam loss has on our environment. This is an issue that has become an even more pressing concern over the years, and companies are now pushed to take a more active approach to eliminating these effects and responsibility to ensure the environment is better safeguarded.
Out with the old. In with the new
With the high-risk areas identified and an action plan agreed, ERIKS teamed up with a partner supplier, widely respected in the area of steam systems, to devise a solution that would offer significant improvements.
As with all projects, quick turn-around was required, as major disruptions would have catastrophic consequences for the customer. The solution was to provide complete steam trap assemblies, ready-to-install that could be retro-fitted into the current pipework system.
The new steam trap assembly package included PN40 piston valves with carbon steel constructions that could operate to a maximum working pressure of 25 bar; ¾” 20mm ‘Y’ Type carbon steel strainer; and ¾” 20mm PN40 stainless steel traps, suitable for superheated steam.
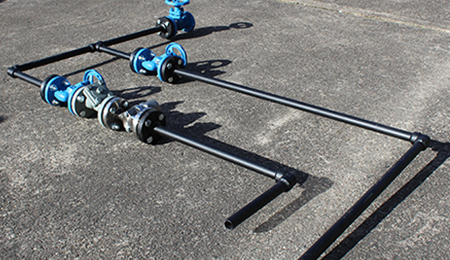
All products were prefabricated, assembled, tagged, tested and certified prior to the installation. The assemblies were compliant with all current health and safety Pressure Equipment Directive (PED) and Pressure Systems Safety Regulations (PSSR) 2000.
The new assembly also provides double proven isolation, allowing maintenance of the strainer and trap without engineers having to shut down the steam system.
To date, ERIKS have already received orders for 36 assemblies for superheated steam and saturated steam requirements, with another 20 assemblies to be ordered shortly after.
Increasing understanding
The success of the new steam trap assemblies has secured savings of over £50,000 for the customer. And that’s just on steam loss alone.
With the long-term now a focus, the customer is looking to achieve even more energy savings, by utilising ERIKS’ knowledge of steam, and how to better understand steam traps, their usage, how to effectively maintain high efficiency, and what effects poor steam traps pose.
There seems to be a real underlying issue with lack of knowledge and confidence on the subject of steam, with opportunities not claimed due to lack of understanding. Luckily, for customers who operate with steam systems, ERIKS wants to raise awareness on steam and address these issues by offering training, and simply getting people to talk about steam.
For more information on ERIKS Steam Traps or Steam Services offering, please give us a call on 0121 508 6000 and one of our technical experts will be on-hand to discuss your options.
#ERIKS #LetsMakeIndustryWorkBetter #Solutions #SteamTraps #SteamSystems