In this article
Small gearbox. Big issue.
Twas the week before Christmas 2022, and all through the site the engineers were wondering if the gearbox on their critical asset would see out the year. Then a strip down and inspection revealed that it almost certainly wouldn’t.
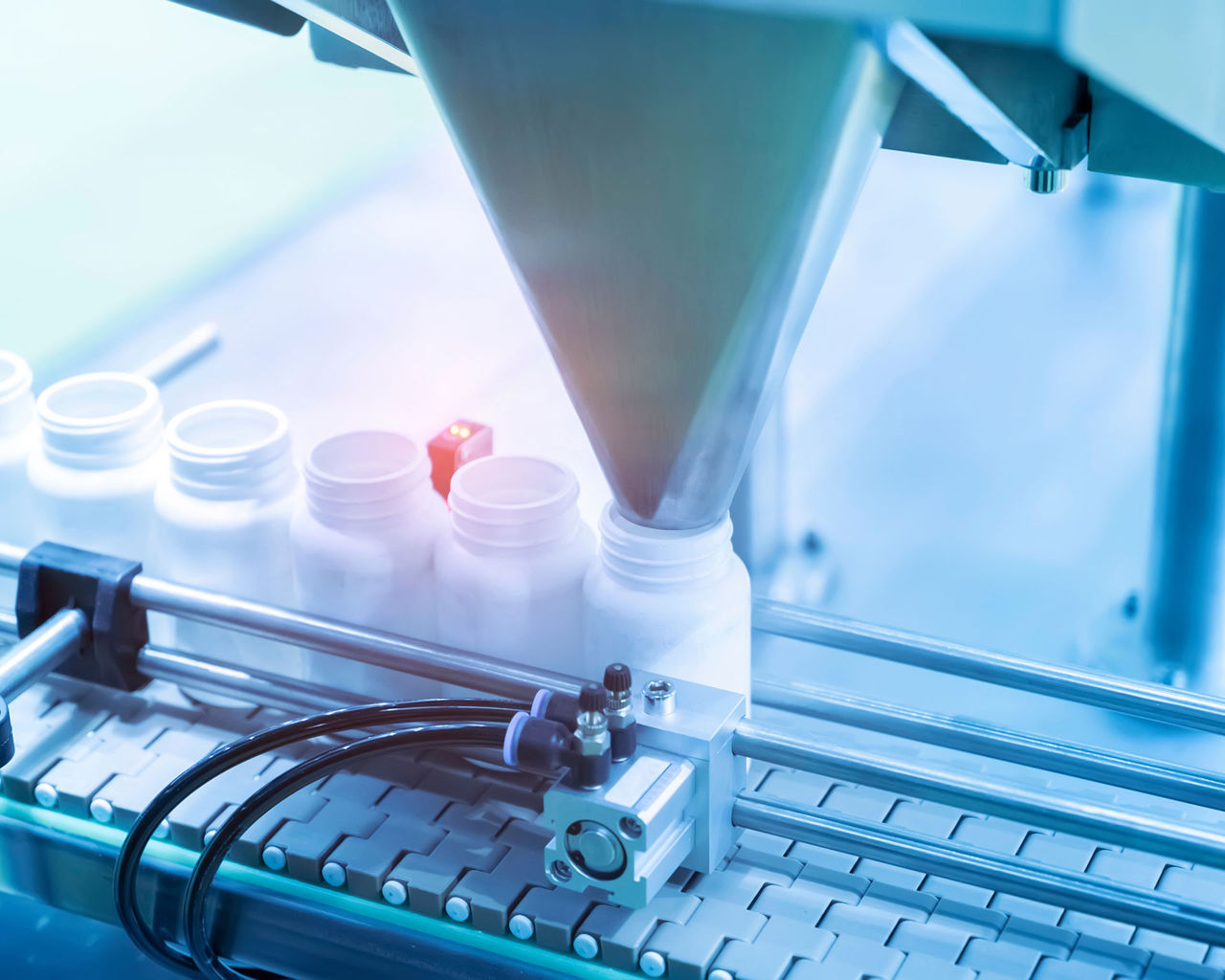
It’s often not the size of the asset which piles on the pressure. It’s the criticality. In this case the gearbox in question is small, but the part it plays in a pharmaceutical product labelling machine makes it crucial to maintaining production. So much so, that every day of gearbox downtime costs the customer close to £8,000.
That’s not the kind of Christmas present anyone would wish for.
The customer had no spare gearbox ready to drop in. A replacement had been ordered from the OEM, but expected delivery was four months away. The only options left were a letter to Santa, or a word with the ERIKS OnSite Services team at the customer’s facility.
Even without a sleigh or reindeer, ERIKS were confident they could deliver, and called in the experts from the Drives and Rotating Equipment Product Business Unit.
One problem; three solutions
It wasn’t just the timing around Christmas that made a sticky problem even stickier. It was also the non-standard gearbox specification. Instead of the usual two shafts – one input and one output – this particular box includes a second input shaft to drive a tachometer.
With the condition of the gears suggesting catastrophic failure was imminent, speed of response was critical. So ERIKS arrived on site, inspected the gearbox, and presented the customer with three options – any of which could be initiated the very next day.
The first was to modify the input shaft to handle the tachometer connection. The second was to manufacture an entirely new double worm output shaft. And the third was to reposition the tachometer onto the non-drive end of the motor.
After careful consideration the customer chose option one, but with a tricky Christmas caveat: they needed the job to be completed over the holiday period.
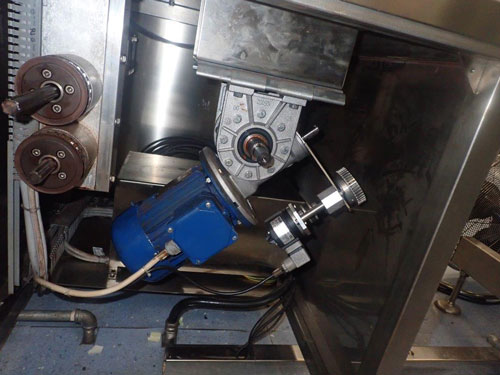
Christmas is cancelled
Apart from Santa and a few other special cases, most people expect a few days off over Christmas. But not ERIKS; not this time. Christmas may only come once a year, but the customer always comes first.
Putting festive plans on hold, ERIKS’ engineers started work on designing and manufacturing the gearbox the customer needed.
The first step was to reduce the time required for manufacture, by starting not from scratch but from a standard gearbox. The next step was to adapt this to the double input that the customer required.
That wasn’t as simple as it sounds.
There were complicated calculations to carry out, to ensure the modifications to the shaft would not affect transmission of the correct amount of torque. The risk of unacceptable torsional stresses and shearing of the shaft had to be avoided at all costs.
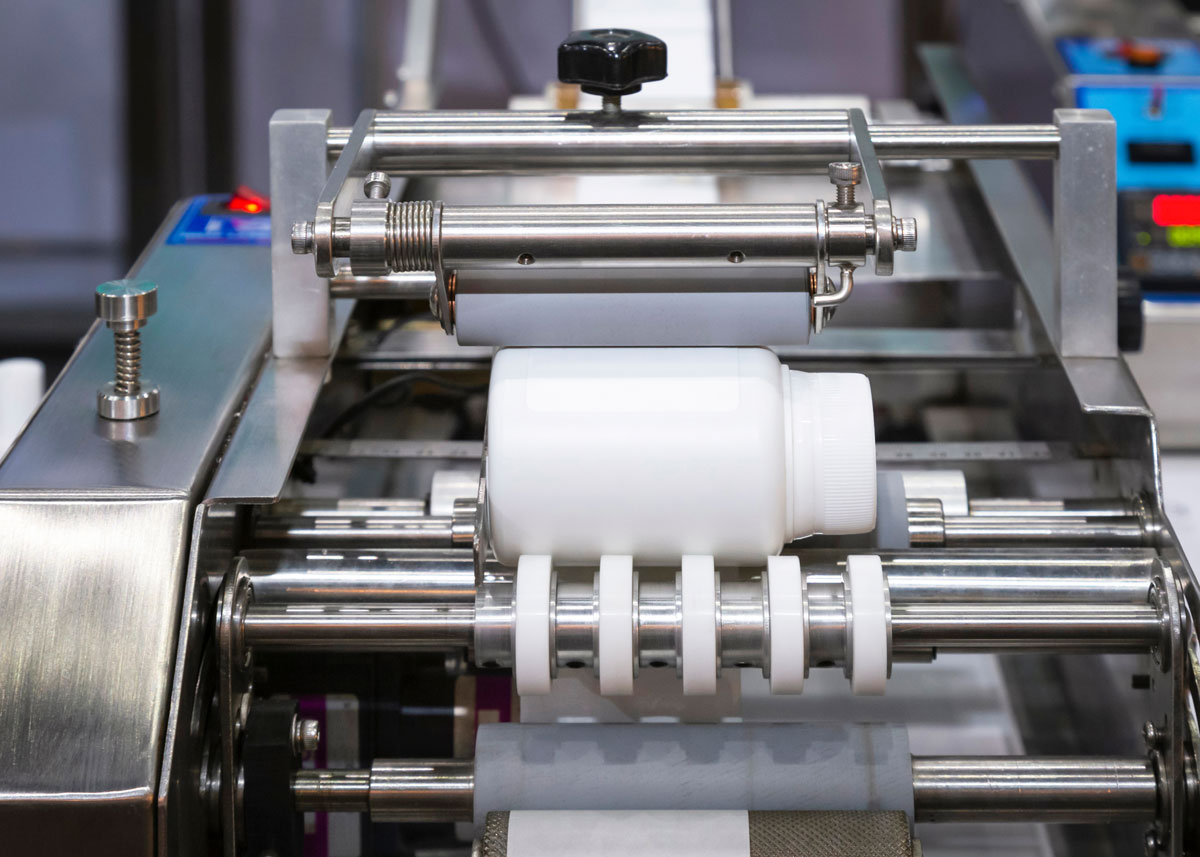
Happy New Year!
With more dedication to customer service than even Santa’s elves, the ERIKS team got down to work. They were well aware that failure to deliver the new gearbox before the existing one failed would result in devastating downtime, and a loss of production amounting to 318,000 packs per week.
Calculations completed, manufacturing and adaptation could begin. This involved stripping down the standard gearbox, and modifying not only the shafts but also the gearbox casing.
Thanks to ERIKS’ engineering know-how, the customer’s worst-case scenario was avoided, and the replacement gearbox was delivered on 30th December for a local installer to fit in a day.
Based on the OEM’s lead time for a new non-standard gearbox, the customer has calculated that ERIKS’ quick response and Christmas holiday working delivered a saving of £165,000 in potential lost production.
And despite the high-speed turnaround, the customer’s own engineers have described the new gearbox as ‘running better than it ever has been’ – perhaps due to ERIKS’ attention to detail in modifying the standard box.
With the asset still running smoothly twelve months on, ERIKS also won the business to manufacture an additional spare gearbox. So, the customer’s Christmas was saved, and everyone had a happy new year.
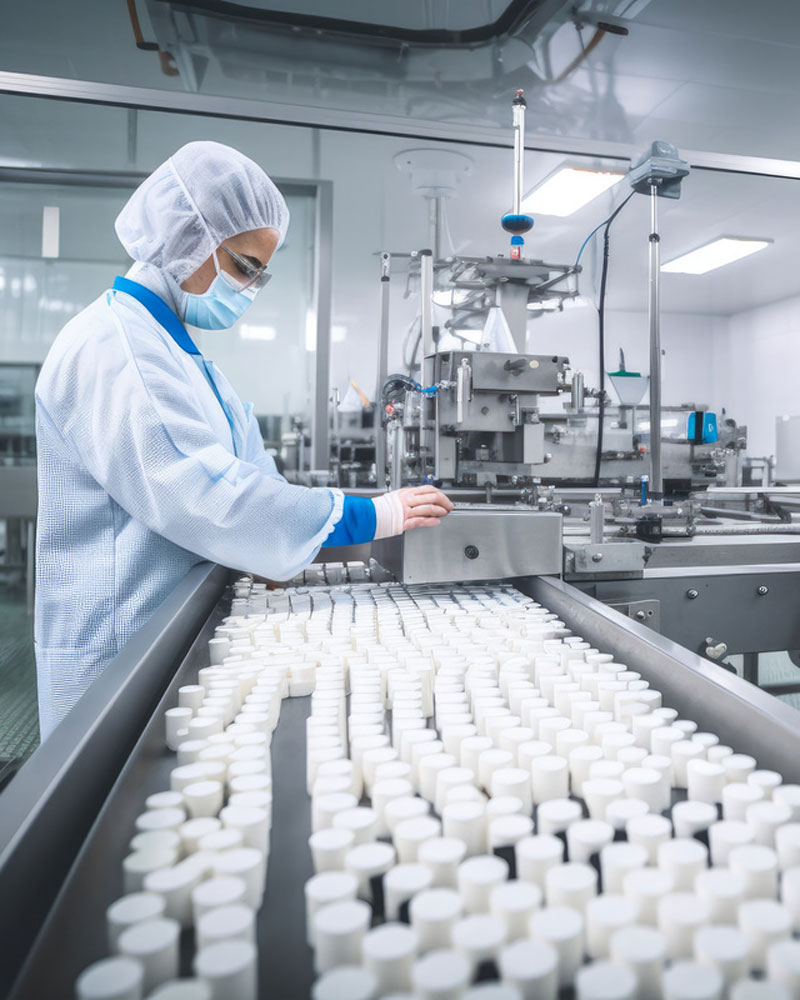
For more information on Repair or Replace or to get in touch with one of our Engineering Specialists please contact your local ERIKS Service Centre, who will be happy to discuss your options.
#ERIKS #LetsMakeIndustryWorkBetter #Gearbox #RepairReplace #Pharmaceutical